Chlazení laserových řezacích strojů stlačeným vzduchem
Odvětví: | laserová technologie |
Zákazník/místo/rok: | Horstmann, Verl (Germany), 2008 |
Použití stlačeného vzduchu: | procesní vzduch |
Nainstalované produkty: | BEKOKAT |
Laserové řezání patří k tepelným způsobům dělení. Teplo není cítit jen v ohniskovém bodě, tam kde laserový paprsek narazí na řezaný materiál. Horko je i v předcházející dráze paprsku. Zde je žádoucí ochlazení. Nejlépe a nejhospodárněji pomocí stlačeného vzduchu. Ten však musí být absolutně bezolejový.
U společnosti Horstmann GmbH & Co. KG se sídlem ve Verlu u Güterslohu se věnují vysoce kvalitnímu a náročnému kovoobrábění pro významné zákazníky z nejrůznějších hospodářských odvětví, mimo jiné automobilového průmyslu, výrobců lodí, strojů, zařízení a nástrojů.
Laserové řezačky, které u společnosti Horstmann neúnavně pracují, by nanejvýš alergicky reagovaly i na minimální zanesení olejem způsobené stlačeným vzduchem. A sice výrazným snížením výkonu a kvality. Jejich superostrý laserový paprsek by totiž doslova degradoval na mdle plápolající „olejový plamínek“. Oproti tomu, co by se člověk mohl domnívat, se stlačený vzduch na laserových řezačkách u společnosti Horstmann totiž nepoužívá pro pneumatický systém, ale výhradně k chlazení dráhy laserového paprsku.
V principu se řezací zařízení s laserem CO2 skládá ze zdroje laserového paprsku a pohyblivé zaostřovací optiky, většinou dutého zrcadla nebo spojné čočky. Od zdroje se laserový paprsek vede přes odrazné zrcadlo k obráběcí optice. Tam se zaostřuje a vytvoří se tak výkonová hustota potřebná pro řezání. U společnosti Horstmann, kde se řežou především plechy z nerezové oceli, je to výkon paprsku až šest kW. To je mimochodem dost na to, aby paprsek bez námahy zcela pronikl lidským tělem.
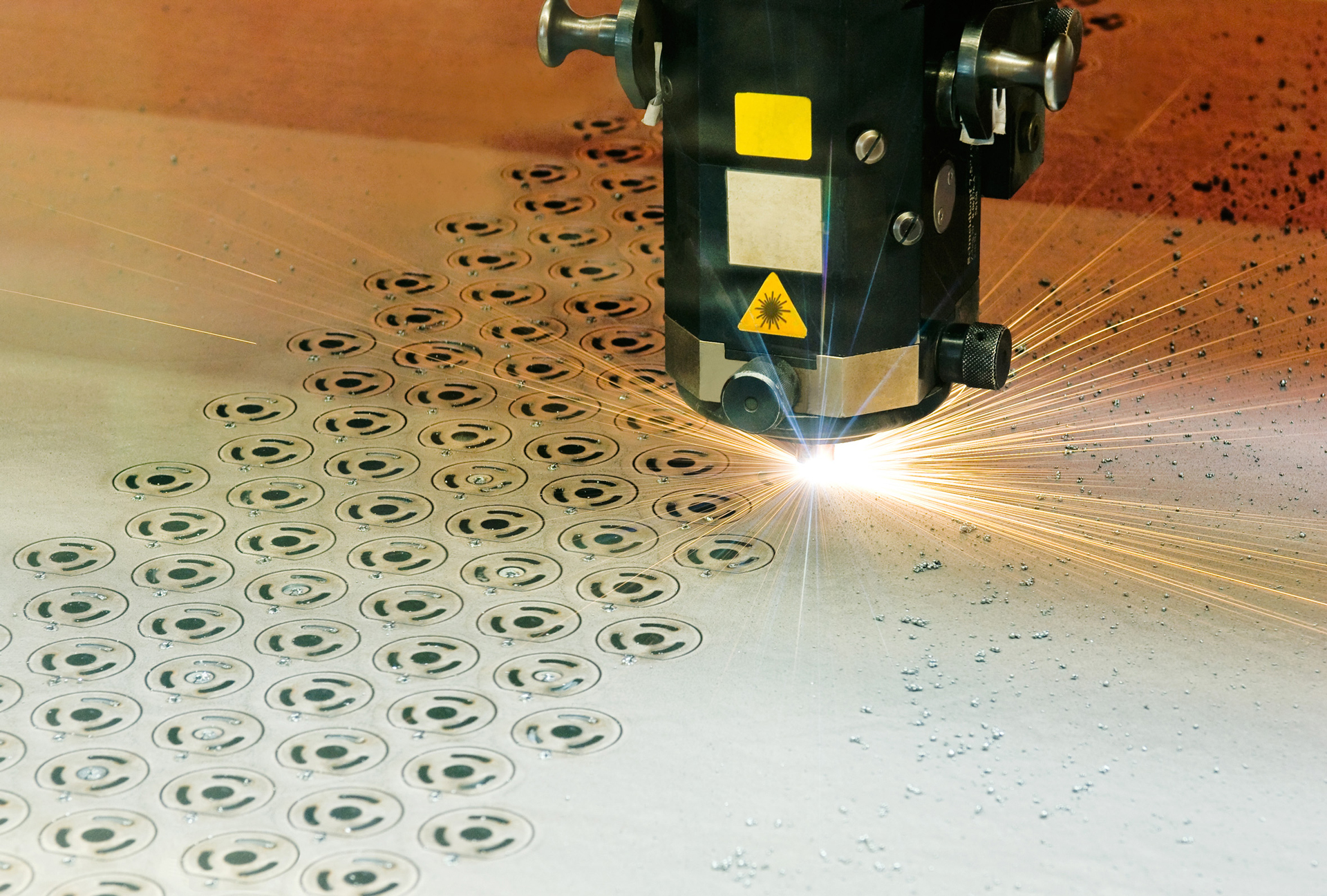
Protože se pojízdná, „létací“ optika pohybuje nad obráběnými plechy, mění se neustále její vzdálenost od pevně stojícího laserového zdroje. Avšak vytvořený laserový paprsek nemá potřebnou paralelitu, která by jej přenesla přes částečně velké a proměnlivé vzdálenosti. Z tohoto důvodu a také proto, aby se snížilo tepelné zatížení odrazného zrcadla, je zčásti rozšířen pomocí zrcadlového teleskopu.
Vlastní vedení paprsku mezi laserovým zdrojem a zaostřovací optikou probíhá přes zrcadla s vrstvou zlata a molybdenu, která jsou většinou vyrobena buď z čisté mědi, nebo z monokrystalického křemíku. Navíc reagují nanejvýš citlivě na olej, respektive aerosoly, které se na nich usazují a způsobují předčasnou, velmi nákladnou výměnu.
V celé dráze paprsku laseru se přirozeně vytváří vysoká teplota. Bez chlazení by materiály, které jsou zde použité, například odrazné zrcadlo a ještě rychleji měch pohyblivé optické jednotky, utrpěly značnou škodu.
Tuto životně důležitou funkci chlazení přebírá stlačený vzduch, vyfoukávaný do dráhy paprsku. Ten musí být absolutně bez obsahu částic a oleje a rovněž suchý, aby „nerozptýlil“ laserový paprsek poletujícími částicemi ani aby neznečistil odrazné zrcadlo usazeninami. Už ten nejmenší podíl oleje a aerosolů ve stlačeném vzduchu by měl rychle fatální následky na procesní bezpečnost a hospodárnost řezacího zařízení.
Oba faktory jsou však – spolu s absolutní kvalitou produktu – podstatnými složkami přetrvávajícího obchodního úspěchu společnosti Heinrich Horstmann GmbH & Co. KG. Proto zde také věnují tématu úpravy stlačeného vzduchu enormní pozornost.
Dosud se u společnosti Horstmann pokoušeli – tak jako ostatně u téměř všech uživatelů stlačeného vzduchu s podobnými nároky – vyrábět bezolejový stlačený vzduch pomocí relativně náročných, často dokonce navzájem spojených kompresních, filtračních a vysoušecích technologií. Často se to však dařilo jen s větší či menší spolehlivostí.
Ani u společnosti Horstmann nikdy nenalezli skutečně uspokojivé řešení, především nikoli po pořízení nových, ještě výkonnějších řezacích zařízení. Na začátku roku 2008 narazili na katalytický postup pro výrobu absolutně bezolejového stlačeného vzduchu, vyvinutý německou firmou specializovanou na stlačený vzduch BEKO TECHNOLOGIES GmbH. Přístroj nazvaný BEKOKAT otevírá cestu k absolutně bezolejovému stlačenému vzduchu pomocí naprosto jiného technologického základu než všechna dosavadní řešení: katalýzy
Totální oxidace uhlovodíků
V zásadě provádí systém BEKOKAT totální oxidaci uhlovodíků a vyrábí tak absolutně bezolejový stlačený vzduch. A sice v jednom koncentrovaném, obsáhlém procesním kroku po kompresi. Kompletní odolejování stlačeného vzduchu se tak provádí v jedné jediné komponentě zařízení. Ta pracuje nezávisle na okolních podmínkách, vstupní koncentraci oleje a relativní vlhkosti stlačeného vzduchu.
BEKOKAT se věnuje veškerým nečistotám stlačeného vzduchu přiváděného od kompresoru. Jsou to maziva, oleje, oxid siřičitý, oxid uhelnatý, nitrogenní plyny atd., které se vyskytují jak v plynné formě, tak jako pára a aerosoly. Pomocí zařízení BEKOKAT se tyto látky obsažené ve vzduchu přemění zcela na oxid uhličitý a vodu.
Tu lze pak bez obav přímo a bez dalších ekologických opatření odvádět do sítě odpadních vod. Dokonce i kondenzát vznikající při ochlazení stlačeného vzduchu je díky katalytickému postupu absolutně bezolejový a může rovněž bez úpravy odtékat do kanalizace. Tuto totální oxidaci a naprosto bezezbytkový pracovní postup nezajišťuje aktuálně žádný jiný postup.
Jako katalyzátor slouží v zařízení BEKOKAT granulát, který se pomocí topných článků zahřeje na provozní teplotu asi 150 stupňů Celsia. V katalyzátoru se molekuly oleje rozbíjejí tak dlouho, dokud nezůstane jen jeden atom uhlíku. V konečné fázi katalýzy zoxidují molekuly oleje až na H2O a CO2.
Důležité je, aby uhlovodíkové řetězce, tedy olejové molekuly, mohly být „krakovány“ na libovolném místě. Jsou rozbíjeny tak dlouho, dokud nezbude jen oxid uhličitý a vodík. Různě dlouhé uhlovodíkové řetězce z bezolejových a olejem mazaných kompresorů nepředstavují tedy pro BEKOKAT žádný problém.
Ne vždy je také známo, že jinak často využívané filtry s aktivním uhlím nedokáží adsorbovat polární sloučeniny, jako jsou olefíny, alkoholy, glykoly nebo ketony. Systém BEKOKAT oproti tomu ze stlačeného vzduchu zcela odstraní i tyto látky. V dalším průběhu procesu BEKOKAT se vyčištěný stlačený vzduch ochladí ve výměníku tepla na teplotu o 10 až 15 stupňů Celsia vyšší než je na vstupu a je k dispozici pro příslušné použití.
Pomocí BEKOKATu je poprvé možné dosáhnout absolutně bezolejového stlačeného vzduchu s maximálním obsahem zbytkového oleje téměř neměřitelných 0,003 miligramu na metr krychlový. Tedy kvality, která je potřeba v maximálně náročných oblastech lékařství a farmacie a rovněž ve zpracování a balení potravin.
Hospodárně nanejvýš výhodná je také enormní životnost speciálního granulátu BEKOKAT, který je nutno vyměnit nejdříve po 20 000 provozních hodin. Ve srovnání s tím je životnost filtru s aktivním uhlím i za dokonalých pracovních podmínek vyčerpána již asi po 500 provozních hodin.
Od časného léta 2008 se systém BEKOKAT používá u zpracovatele kovů společnosti Horstmann, po dvacet čtyři hodin denně bez poruchy. Společnost Horstmann GmbH & Co. KG má navíc i dobré svědomí ohledně ekologie, protože od začátku používání zařízení BEKOKAT lze kondenzát ze systému stlačeného vzduchu bez problémů a bez drahé úpravy odvádět přímo do odpadní kanalizace.
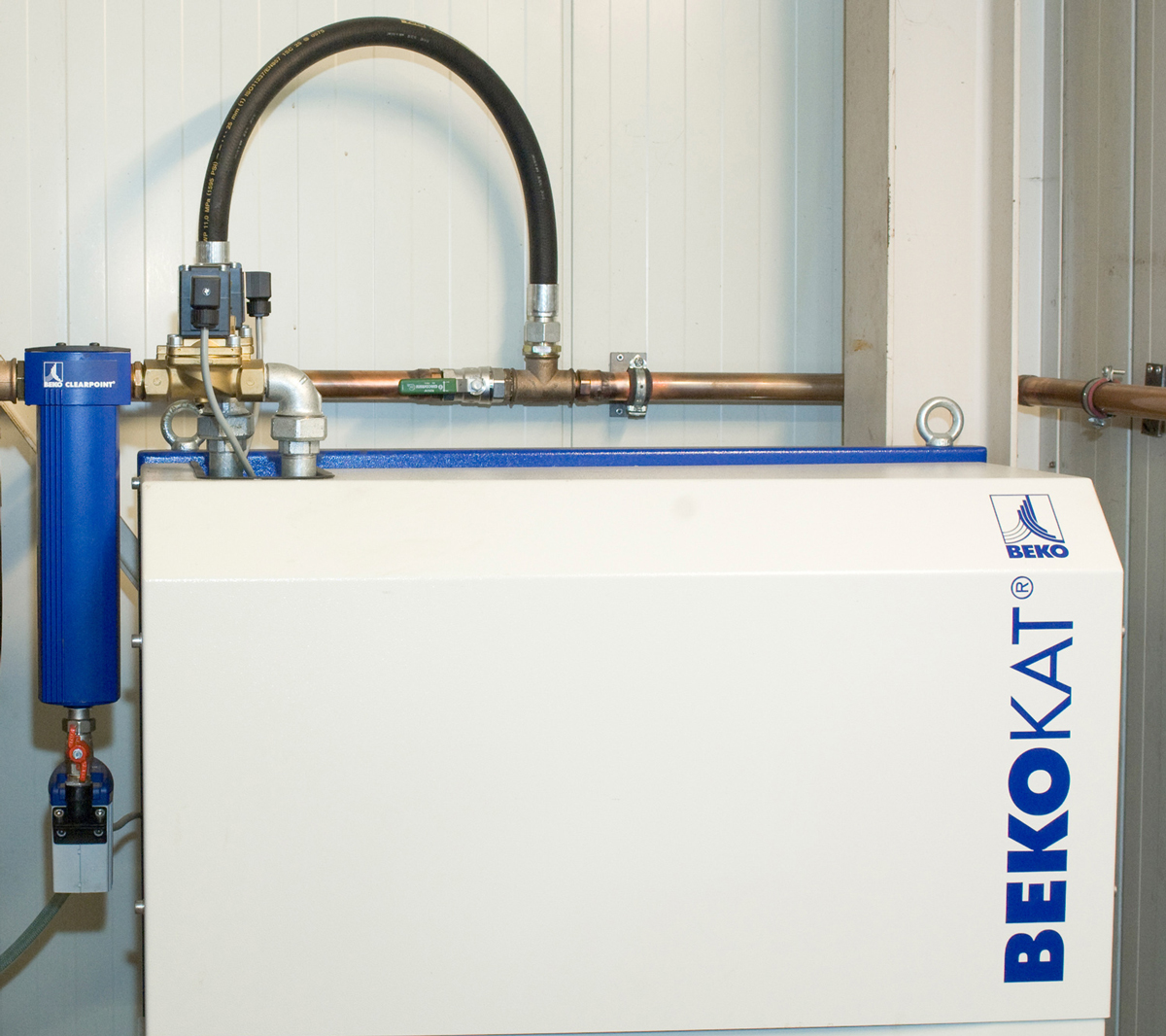
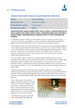