Technika stlačeného vzduchu v obalovém průmyslu
Odvětví: | výroba obalů, papírenství |
Zákazník/místo/rok: | Delkeskamp, Nortrup (Germany), 2008 |
Použití stlačeného vzduchu: | ovládací vzduch, procesní vzduch, kondenzační technika |
Nainstalované produkty: | EVERDRY, BEKOSPLIT |
Toto průmyslové odvětví nelze podceňovat: Více než 100 specializovaných továren s přibližně 19 000 zaměstnanci v Německu vyrábí a zpracovává vlnitou lepenku. Stlačený vzduch a jeho úprava hraje při výrobním procesu centrální roli. Především vlhkost ve stlačeném vzduchu má fatální následky pro zařízení, suroviny i hotové výrobky.
S roční produkcí přibližně devět miliard metrů čtverečných vlnité lepenky je Německo na prvním místě v Evropě a v mezinárodním srovnání na 4. místě za USA, Čínou a Japonskem. Téměř tři čtvrtiny veškerého přepravovaného zboží v Německu cestují zabalené do vlnité lepenky – a téměř 30 procent všech naplněných obalů z vlnité lepenky překročí na své cestě ke spotřebiteli hranice země. Jde tedy o velký byznys, který má velký vliv, a tedy odpovídající význam pro celou německou ekonomiku.
Jedním z průkopníků a předních výrobců tohoto průmyslového odvětví je společnost Delkeskamp Verpackungswerke GmbH v dolnosaském Nortrupu. Byla založena jako továrna na výrobu kartonových obalů již v roce 1896 a kromě kmenového závodu v Nortrupu dnes vyrábí v dalších výrobních závodech v Hannoveru a v českých Odrách. Vyrábí se papír, vlnitá lepenka a pěnová hmota pro obaly z nejrůznějších kulérů.
Uzavřený výrobní okruh
Výchozím materiálem pro výrobu vlnité lepenky je surový papír na vlnitou lepenku. Společnost Delkeskamp GmbH si největší část potřebného surového papíru sama vyrábí v závodu Nortrup. Tento závod je tedy prvním článkem uzavřeného výrobního okruhu, a má tak rozhodující význam pro funkčnost a hospodárnost celé výrobní struktury Delkeskamp. Kromě čistě výrobně-technických výhod zajišťuje totiž vlastní výroba surového papíru společnosti také maximální nezávislost na nákupním trhu.
U společnosti Delkeskamp vůbec rádi stojí na vlastních nohou. V Nortrupu se tak dokonce vyrábí ve vlastní elektrárně prostřednictvím moderních plynových turbín i pára potřebná k výrobě papíru. Při tomto procesu vzniká elektřina v množství, které výrazně překračuje vlastní spotřebu a odvádí se do veřejné sítě. Společnost je tak nejen samozásobitelem, ale kromě toho také uznávaným dodavatelem energie v Dolním Sasku.
Kromě bezpodmínečné procesní bezpečnosti ve vlastní výrobě tak nese i určitou odpovědnost za obyvatele regionu. Očekávání, která je nutno naplnit. Jedním z pilířů je přitom stabilní a vysoce kvalitní zásobování závodu stlačeným vzduchem – jedním z nosičů energie, které jsou pro výrobu z různých hledisek rozhodující.
Stlačený vzduch je rozhodující nosič energie
V Nortrupu se stlačeným vzduchem zásobují tři – vlastně čtyři – podnikové pobočky. Jsou to zejména papírenská továrna, výrobna vlnité lepenky a závod na pěnové hmoty. Další, i když mnohem nižší spotřeba, připadá na vlastní elektrárnu.
Bez stlačeného vzduchu by se u společnosti Delkeskamp nehnulo prakticky nic. Abychom to pochopili, stačí si pouze představit nahrubo narýsované výrobní postupy ve třech výrobních oblastech. V prvním kroku se v obrovských, vysoce moderních výrobních zařízeních vyrobí ze starého papíru surový papír na výrobu vlnité lepenky a v prvním stupni výroby lepenky se zahřeje a zvlhčí. Dosáhne se tak potřebné elasticity k tvarování. V následujícím kroku se papír pod tlakem a působením žáru provede mezi dvěma rýhovanými válci, které do sebe zoubkovitě zapadají. Vlnitý papír se pak nejprve slepí s vnitřním pásem papíru shora a poté s vnějším pásem papíru zespoda – vlnitá lepenka tak může rozvinout svůj optimální ochranný účinek.
V plně automatizovaných pracovních cyklech se pak z formátů vlnité lepenky vyrábějí skládací bedny, ražené obaly, vypodložené vnitřní obaly a vystavovací obaly. To vše se pohybuje a řídí přes nesčetné pneumatické systémy a také přes regulátory a posuvné součásti ovládané stlačeným vzduchem. Pokud se něco někde v tomto jemně navzájem sladěném výrobním postupu zadrhne, má to okamžité následky na výrobní kvótu a především na kvalitu výroby
To nejdůležitější: suchý stlačený vzduch
To, co společnost Delkeskamp především potřebuje, kromě kontinuálního zásobování, je suchý stlačený vzduch. Zanesení stlačeného vzduchu vlhkostí je pro pneumatické systémy a pro produkty čistým jedem.
Vlhký stlačený vzduch přitom zdaleka není rizikem jen pro papír a vlnitou lepenku. Suchost stlačeného vzduchu je nezbytná i ve třetím výrobním odvětví společnosti Delkeskamp, výrobě pěnové hmoty. Zde se z pěnového polystyrenu vyrábějí tvarované díly, navržené individuálně pro různé obaly. Materiál, známý běžně pod názvem polystyren, se u společnosti Delkeskamp nazývá Denopor a doplňuje kompletní obalovou koncepci výrobce.
Stlačený vzduch je v této části provozu potřebný mimo jiné pro práci automatických tvářecích strojů, pohyb stavěcích válců a funkci ventilů. K tomu se přidává vyfukování hotových tvarovaných dílů ze strojů. Protože hotové Denoporové díly, vyfouknuté z tvářecího stroje pomocí stlačeného vzduchu, se skladují v nevytápěné hale, musí být absolutně suché. Při jakémkoli jiném zatížení totiž tento materiál reaguje velmi citlivě na teploty pod bodem mrazu. Vlhkost tuto citlivost přirozeně ještě zvyšuje.
Suchost je proto pro společnost Delkeskamp Verpackungswerke GmbH v seznamu priorit pro zásobování stlačeným vzduchem na prvním místě. Je tomu tak i u potřebného rozšíření zařízení stlačeného vzduchu ve kmenovém závodě Nortrup. Od roku 2007 se zde významnou měrou rozšiřuje a investuje do zvětšení a modernizace výroby.
Vyšší potřeba stlačeného vzduchu po rozšíření závodu
Dosavadní stanice stlačeného vzduchu v takzvaném „kompresorovém sklepě“ nemohla co do výkonnosti držet s tímto růstem krok. Pět kompresorů, které zde byly umístěny a následná adsorpční sušička potřebovaly nutně posílení. A jeden již po delší dobu „viklavý“ zub bylo už potřeba vytrhnout – statický separátor voda-olej, který už dávno nefungoval tak, jak by si to u společnosti Delkeskamp přáli.
Hledání nejmodernějšího řešení tohoto problému dovedlo společnost Delkeskamp po intenzivní analýze trhu k partnerovi, který byl pro ni zcela nový: německému dodavateli systémů stlačeného vzduchu BEKO TECHNOLOGIES GmbH.
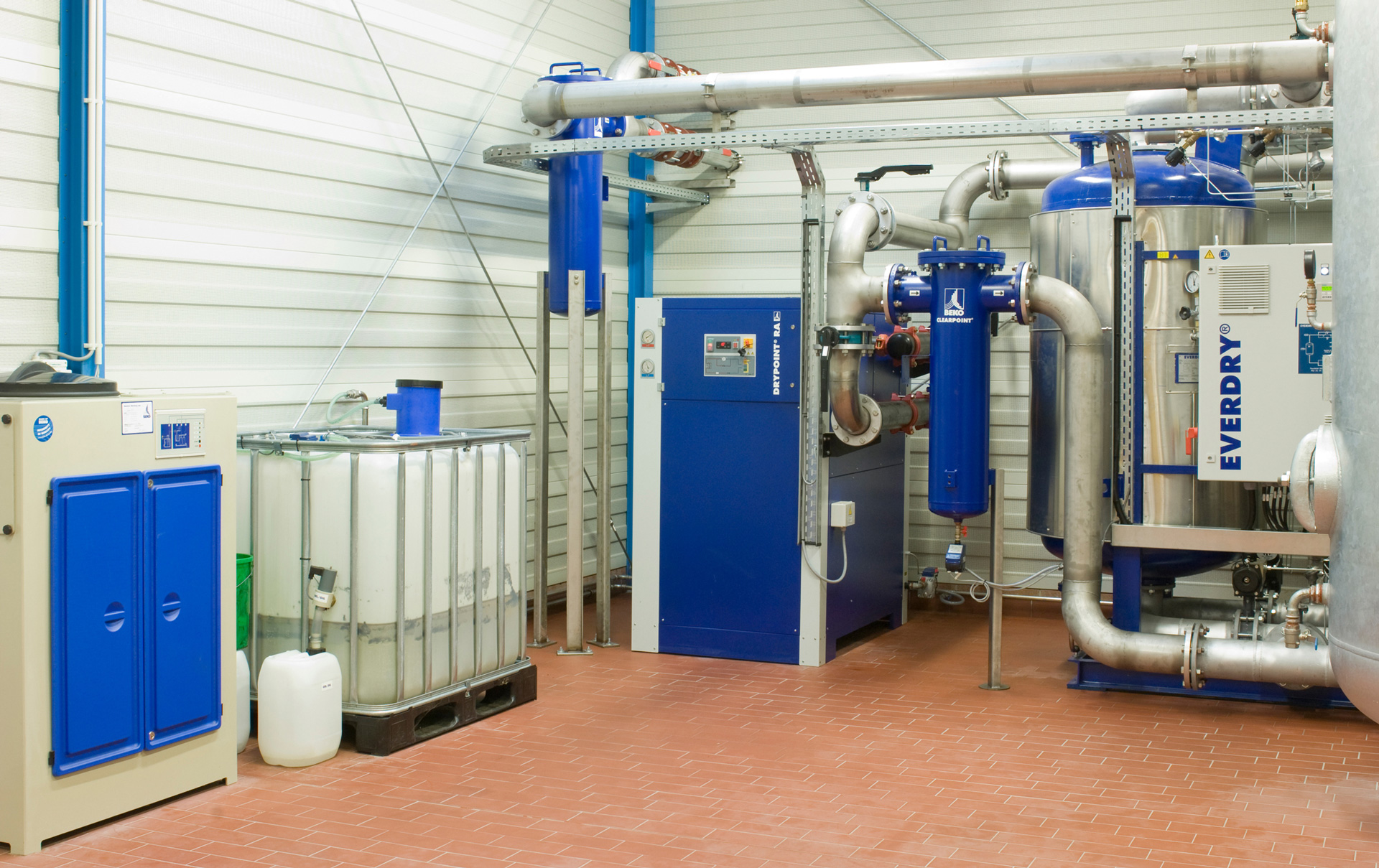
Tato společnost se sídlem v rýnském Neussu a s aktivitami po celém světě má v programu technologii pro separaci olejovo-vodnatých emulzí: BEKOSPLIT. Tato štěpicí zařízení čistí emulgované kondenzáty, k jejichž vzniku dochází za nepříznivých výchozích podmínek nebo u určitých kombinací maziv a kompresorů. Kromě kondenzátu ze stlačeného vzduchu lze upravovat i jiné průmyslové odpadní vody obsahující olej. Z vody se odstraňují organické nečistoty nerozpustné ve vodě – například oleje, rostlinné nebo živočišné tuky – i celá řada pevných nečistot. Kromě toho se spolehlivě adsorbují případně obsažené těžké kovy, nečistoty a částice barviv.
Princip zařízení BEKOSPLIT přitom pracuje efektivněji než ultrafiltrace. Není třeba žádných agresívních čisticích prostředků a spotřebuje se méně energie. Potřeba investice je nanejvýš přehledná a hospodárnost navíc podporují delší intervaly údržby.
Systém se osvědčuje
U tohoto kontaktu se specializovanou firmou na stlačený vzduch BEKO TECHNOLOGIES to však neskončilo. U společnosti Delkeskamp rychle zjistili, že v BEKO TECHNOLOGIES nalezli partnera, který „to má podobně“ jako oni. Který přemýšlí komplexně a vyvíjí logické celkové koncepce. Záležitost začala být zajímavá.
Především, když u BEKO TECHNOLOGIES začali ještě jednou promýšlet téma vysoušení stlačeného vzduchu, tolik citlivé pro společnost Delkeskamp. Například ohledně hospodárnosti. Když to zašlo dokonce tak daleko, že se úprava stlačeného vzduchu přenesla z velké části z dosud výhradně používaných adsorpčních sušiček také na Konenzační sušičky, dveře se nejprve opět zavřely.
Pro společnost Delkeskamp se tento návrh zprvu rovnal palácové revoluci, pro uspořádání svého systému totiž spoléhala jedině na princip a bezpečnost adsorpčního vysoušení. Nebyly s ním dosud žádné problémy a společnost si nechtěla zadělávat na zbytečná rizika. Na druhé straně byla myšlenka kondenzačních sušiček velmi lákavá, pokud se člověk podíval na mnohem příznivější energetickou bilanci ve srovnání s adsorpčními sušičkami. Kdyby se tedy dalo zkombinovat obojí...
Přesně ta pravá výzva pro dodavatele systémů BEKO TECHNOLOGIES. Během několika dnů vyvinula tato firma pro společnost Delkeskamp logickou koncepci pro redundantně zkonstruovaný kombinovaný systém z adsorpční sušičky a kondenzační sušičky. Od května 2008 je to realita.
Tento systém umožňuje výrobci obalů v závislosti na požadavcích a okolních podmínkách – například sezónně – provozovat vždy jak nejbezpečnější tak nákladově nejúspornější konstelaci sušiček. Buď jako flexibilní kombinaci obou postupů nebo výhradně jako adsorpční vysoušení, respektive kondenzační vysoušení.
Protože potrubní vedení systému stlačeného vzduchu v rámci areálu závodu probíhají přes potrubní mosty z velké části ve venkovním prostoru, jsou samozřejmě v závislosti na ročním období vystavena velkým teplotním výkyvům. V zimě například musí být zajištěn tlakový rosný bod lepší než minus 40 °C, aby byla zaručena ochrana před následnou kondenzací a zamrznutím. Aby se zde docílilo maximální procesní bezpečnosti, jsou nainstalované adsorpční sušičky EVERDRY od BEKO TECHNOLOGIES vybaveny odpovídajícími jednotkami pro měření rosného bodu a řízení. Zatím to funguje perfektně. Vysoušecí výkon je absolutně stabilní a energetická bilance se výrazně zlepšila.
U společnosti Delkeskamp se v modernizovaném systému úpravy stlačeného vzduchu používají nyní výhradně zařízení BEKO TECHNOLOGIES. Kromě štěpicích zařízení BEKOSPLIT, adsorpčních sušiček EVERDRY a kondenzačních sušiček DRYPOINT zde své služby poskytují i filtry CLEARPOINT.
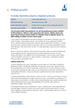