Druckluftaufbereitung als Prozessketten-Konzept
Branche: | Antriebstechnik |
Kunde/Ort/Jahr: | Flender, Mussum, 2009 |
Anwendung der Druckluft: | Prozessluft, Sperrluft, Kondensattechnik |
Installierte Produkte: | BEKOSPLIT, CLEARPOINT, DRYPOINT RA |
Wo vielfältige Anforderungen zu erfüllen sind, führen Einzellösungen selten zu befriedigenden Ergebnissen. Die A. Friedr. Flender AG, einer der weltweit führenden Anbieter mechanischer und elektrischer Antriebstechnik, setzt deshalb auf ein formschlüssiges Prozessketten-Konzept. Unter anderem bei der Druckluftaufbereitung, bei der sowohl technische als auch qualitative und umweltschutzbezogene Herausforderungen zu meistern sind.
In der Flender-Fertigungsstätte Mussum, dem weltweit größten Produktionswerk für Industriekupplungen im Drehmomentbereich von 10 bis 10.000.000 Nm, entstehen im Dreischichtbetrieb an 365 Tagen im Jahr elastische und hochelastische Kupplungen, drehsteife Kupplungen – also Zahnkupplungen und Ganzstahllamellenkupplungen – sowie Spezialkupplungen für Windturbinen und Bahnantriebe. Ein wahrhaft beeindruckendes Portfolio, dem sich hier rund 350 Mitarbeiter – von weltweit 6.300 in der gesamten Flender-Firmengruppe – widmen.
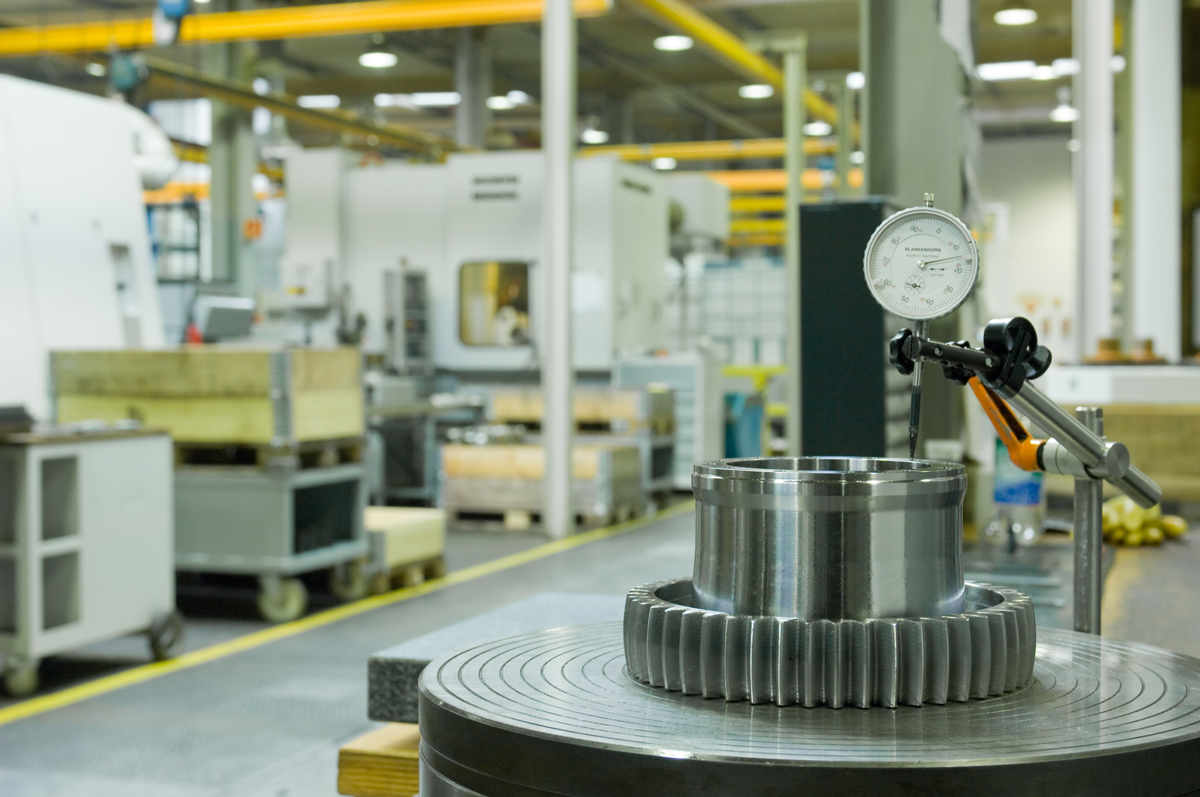
Aufgabenteilung und Gesamtverantwortung
Mussum repräsentiert als Kupplungswerk praktisch ein Modul des formschlüssigen Flender-Antriebsstrangs, die Aktivitäten sind eng verzahnt mit denen des Stammwerks in Bocholt sowie des Getriebemontagewerkes in Voerde-Friedrichsfeld. Die Werke arbeiten nach einem stimmigen Gesamtkonzept, das alle Konzernbereiche und -aktivitäten berücksichtigt und zielorientiert zusammenführt. Und zwar äußerst erfolgreich, wie die lange Unternehmensgeschichte beweist. Nicht von ungefähr hat im Jahre 2005 die Siemens AG die Flender Holding AG übernommen und damit ihr Geschäft in der industriellen Antriebstechnik abgerundet.
Bei der Siemens AG und bei der Flender Holding AG wird in zusammenhängenden Prozessketten geplant und agiert. Da ist nicht nur wichtig, was hinten rauskommt, sondern ebenso, was davor passiert und wie es passiert. Ist es effizient, ist es folgerichtig, ist es zielführend? Und vor allem: Ist es zu verantworten? Zu verantworten im Sinne qualitätsbezogener Aspekte, wirtschaftlicher Überlegungen und selbstverständlich rechtlich-ethischer Belange – zum Beispiel in Sachen Umweltschutz und Schonung natürlicher Ressourcen.
Gute Vorsätze und konkrete Ergebnisse
Auch das sind offensichtlich alles andere als Prospektsprüche, wie konkrete Beispiele an den deutschen Produktionsstandorten der Flender AG zeigen. Ein äußerst anschauliches Beispiel ist die Druckluftaufbereitung im Kupplungswerk in Mussum.
Der größte Teil der Druckluft wird dort für das Beaufschlagen der Koordinatenmessgeräte an den Produktionsmaschinen mit Sperrluft benötigt. Unmittelbar gefolgt vom Beschicken der Direktantriebsmotoren in den Maschinen, die damit gegen das Eindringen von Feuchtigkeit gesperrt werden. Weiterer erheblicher Druckluftbedarf besteht für den Einsatz von Entgratmaschinen, an Reinigungsanlagen für das Abblasen von Werkstücken sowie an Farbspritzsystemen in der Lackiererei und automatischen Naglern im Versandbereich.
Selbst die Infrastruktur des Kupplungswerks setzt auf den Energieträger Druckluft. Zum Beispiel für das Stellen von Lichtkuppeln und Lüftungsklappen sowie für das Steuern von Belüftungssystemen. Während einige dieser Anwendungen keine besonderen Ansprüche an die Qualität der Druckluft stellen, sind andere hoch sensibel – besonders die Messgeräte und die Lackiereinrichtungen. Während erstere vor allem kein Restöl in der Druckluft mögen, reagiert man in der Lackiererei allergisch auf mitgeführte Feuchtigkeit. Sie würde hier zu winzigen Bläschen im Farbauftrag der Kupplungsgehäuse führen – ein „Schönheitsfehler“, den auch Käufer robuster Industrietechnik nicht gern sehen.
Vielschichtige Anforderungen an die Druckluftqualität
Gebraucht wird also sowohl weitgehend ölfreie als auch absolut trockene Druckluft, um die hohen Qualitätsmaßstäbe in der Kupplungsfertigung zu erfüllen. Doch damit nicht genug. Bei Flender hat man weitergehende „interne“ Ziele beziehungsweise selbst auferlegte Pflichten. Dabei orientiert man sich am Mutterkonzern Siemens, der bereits nach der neuen Umweltmanagement-Norm ISO 14001 zertifiziert ist. Dazu gehört auch die bestmögliche Entsorgung des bei der Druckluftaufbereitung anfallenden Kondensats.
Was man benötigte, war ein formschlüssiges Gesamtkonzept, das sich aller Herausforderungen annimmt und sie übergreifend löst - mit Systemkompetenz. Nach einem intensivem Bewertungs- und Auswahlverfahren entschied man sich bei Flender für einen Systemanbieter, der bereits im Vorfeld mit seinen Produkten und Lösungen in Mussum hatte punkten können: den deutschen Druckluft-Spezialisten BEKO TECHNOLOGIES aus Neuss am Rhein.
Gemeinsam mit einem lokalen, auf die Kompressorentechnik spezialisierten Partner legten die BEKO TECHNOLOGIES Spezialisten ein überzeugendes Gesamtkonzept vor. Von der Verdichtung über die Trocknung, Filterung und Kondensataufbereitung bis hin zur Restölüberwachung und dem Rohrleitungsbau wurden dabei sämtliche Aspekte der Druckluftaufbereitung nahtlos verflochten.
Emulsions-Spaltanlage schont die Umwelt
„Schmuckstück“ der Konstellation und gleichzeitig Beleg für die Ernsthaftigkeit der Flender AG in Sachen Umweltschutz ist die Emulsions-Spaltanlage BEKOSPLIT. Mit ihr erfüllt man mühelos selbst die extrem hohen Anforderungen der neuen Umweltmanagement-Norm ISO 14001.
Diese in Deutschland meistverkaufte Spaltanlage für Druckluftkondensate kommt da zum Einsatz, wo kleinste Ölpartikel feinstverteilt in der Wasserphase vorliegen, sodass eine rein physikalische Schwerkrafttrennung, zum Beispiel durch Leichtflüssigkeitsabscheider oder Koaleszenzabscheider, nicht ausreicht. Das BEKOSPLIT-System bietet dagegen bei emulgierten ölhaltigen Industrieabwässern eine zuverlässige Aufbereitungstechnik, indem es wasserunlösliche organische Verschmutzungen, etwa Öle, und Feststoffverunreinigungen durch Zugabe eines natürlichen Tonerdeminerals aus dem Abwasser entfernt. Gleichzeitig werden vorhandene Schwermetalle und andere Schmutzpartikel zuverlässig adsorbiert. Das verbleibende, gereinigte Abwasser kann ohne Probleme in die Kanalisation eingeleitet werden.
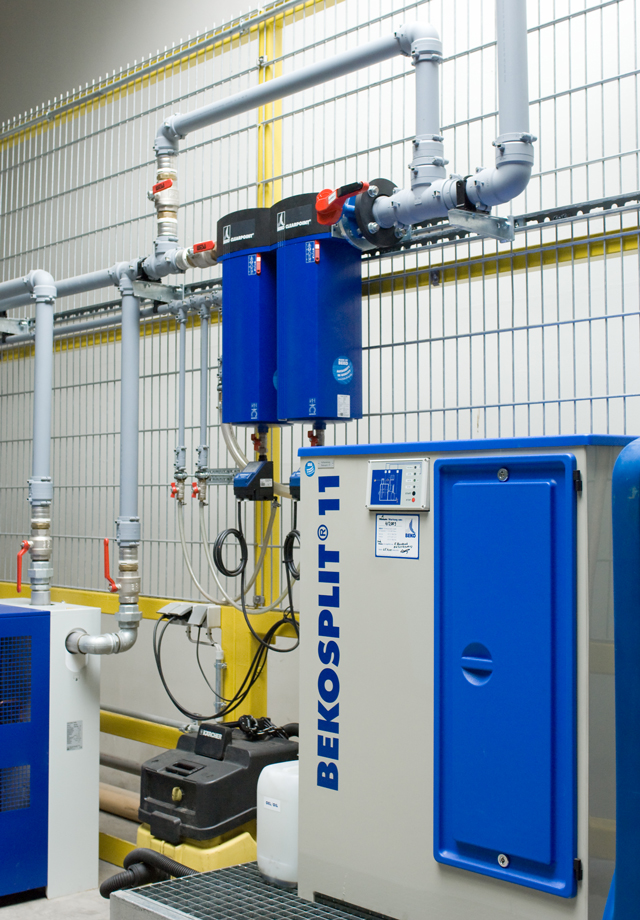
Vom Start weg mit System kombiniert
Während das BEKOSPLIT -Verfahren für drucklufttechnische Spitzenleistung am „Entsorgungsende“ der Systemkette steht, agieren am „Versorgungsstart“ gleich mehrere Komponenten Hand in Hand. Die verdichtete Luft wird zunächst über einen 3.000-Liter-Kessel geleitet, in dem bereits ein Teil der mitgeführten Feuchtigkeit abgeschieden wird.
Ihm folgen gleich drei parallel geschaltete DRYPOINT RA-Kältetrockner von BEKO TECHNOLOGIES. Sie stellen praktisch eine 3 x-50%-Lösung dar: Jedes der drei Geräte ist für sich allein in der Lage, die Hälfte der in der Flender-Anlage geforderte Trocknerleistung zu erbringen. Durch die parallele Schaltung aller drei Kältetrockner wird also eine 150-prozentige Leistung erbracht. Das hat den Vorteil, dass jederzeit ein komplettes Gerät – etwa für die Wartung – aus dem System genommen werden kann, ohne die erforderliche Trocknerleistung zu beeinträchtigen. Selbst der Totalausfall eines Trockners bliebe ohne Folgen für die Druckluftqualität.
Das in den Trocknern entstehende Kondensat wird unter Vermeidung von Druckluftverlusten durch niveauregulierte BEKOMAT-Kondensatableiter abgeschieden und der beschriebenen Emulsionsspaltanlage BEKOSPLIT zugeleitet.
Die getrocknete Druckluft wird im weiteren Verlauf durch strömungsoptimierte CLEARPOINT-Druckluftfilter geführt. Mit ihnen hat BEKO TECHNOLOGIES besonders energieeffiziente und damit betriebskostenfreundliche Filtertechnik in das Druckluftsystem implementiert. Letzter Checkpoint für die Druckluft vor Verlassen der Kompressorenhalle ist ein ebenfalls von BEKO TECHNOLOGIES gestelltes Restölüberwachungssystem.
Alles in allem hat Flender an der Produktionsstätte in Mussum eine nahtlose, perfekt aufeinander abgestimmte Prozesskette in der Druckluftaufbereitung.
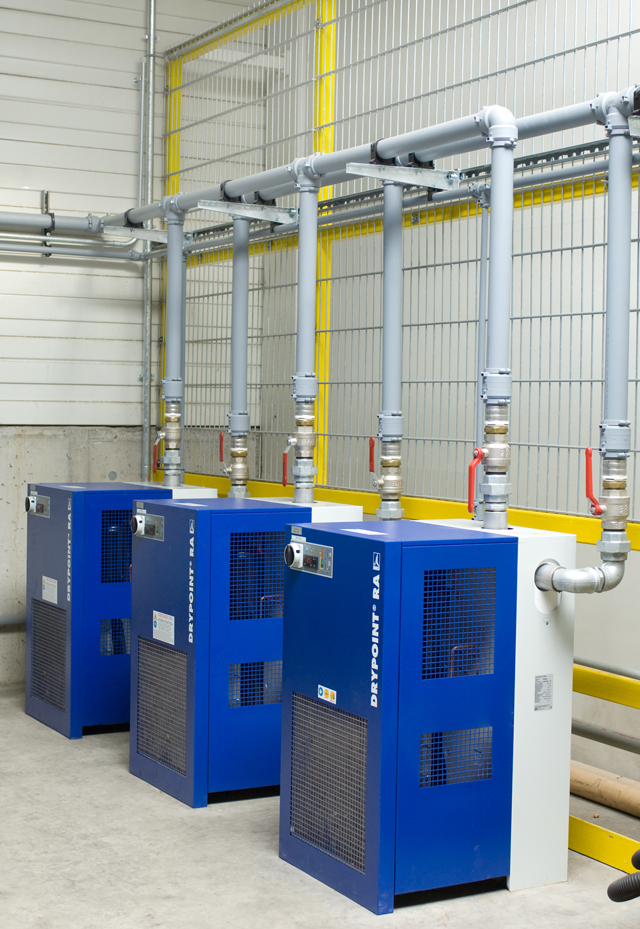
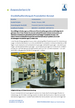