Erschwerte Druckluftaufbereitung in der Zementproduktion
Branche: | Baustoffe |
Kunde/Ort/Jahr: | Ghacem, Takoradi (Ghana), 2016 |
Anwendung der Druckluft: | Förderluft, Prozessluft |
Installierte Produkte: | DRYPOINT RA, CLEARPOINT, ÖWAMAT |
Zement und Wasser sind eine ähnliche brisante Paarung wie Öl und Feuer – zumindest dann, wenn man beide Komponenten unkontrolliert in Verbindung bringt. Das zu verhindern, ist gerade bei der Zementherstellung eine enorme Herausforderung. Vor allem, wenn die Produktion in unmittelbarer Meeresnähe erfolgt – und damit die Druckluftaufbereitung für die Herstellungsprozesse mit schwierigen Klimabedingungen konfrontiert ist.
Ghana ist ein tropisches Land, kennt also keine Jahreszeiten, sondern einen Wechsel zwischen Regen- und Trockenzeit. Nahezu gleich lange Tage und Nächte bestimmen das Leben. Grob lässt sich das Klima in den trockeneren Norden mit seiner Baum-, Strauch- und Grassavanne sowie den feuchten Süden mit seinen immergrünen Regenwaldgebieten und der Atlantikküste unterscheiden.
An der Küste, in Takoradi, der drittgrößten Stadt des Landes und wichtigem Wirtschaftszentrum, findet sich auch der größte Zementproduzent Ghanas: die Ghacem Ltd., sie gehört zum weltweiten Verbund der HeidelbergCement AG. Die AG betreibt in Afrika ein Netzwerk von zwölf Produktionsstandorten in neun Ländern und leistet damit einen entscheidenden Beitrag zur wirtschaftlichen Entwicklung dieser Länder.
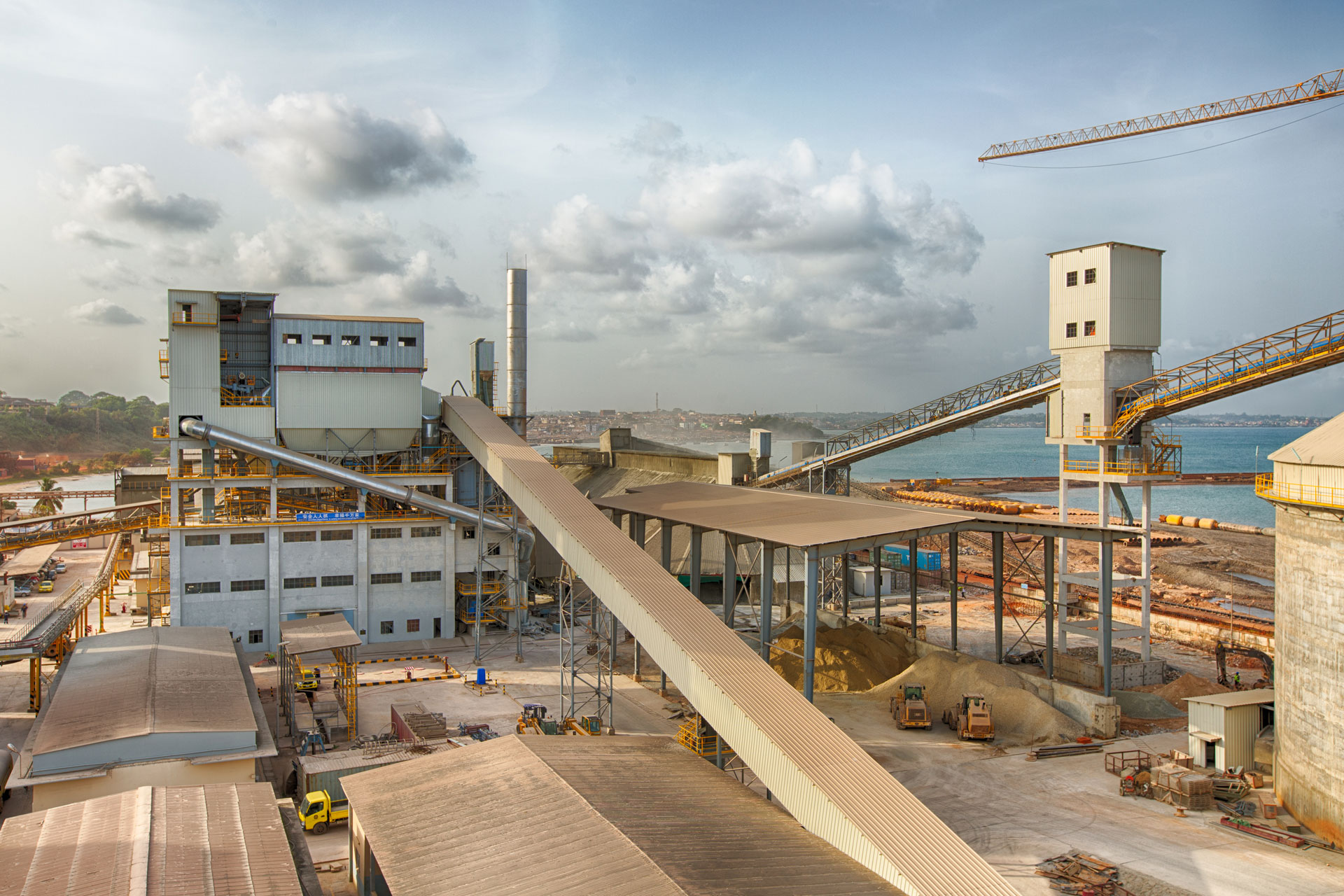
Wie die die meisten afrikanischen Staaten südlich der Sahara profitiert auch Ghana von der aufstrebenden Rohstoffindustrie und verzeichnet eine robuste Wirtschaftsentwicklung und lebhafte Bauaktivitäten. Solides Wirtschaftswachstum, steigende Bevölkerungszahlen, Urbanisierung und Infrastrukturmaßnahmen sorgen seit Jahren für einen Anstieg der Bautätigkeit und Zementnachfrage.
Mehr als 30 Millionen Tonnen Zement
Seit 1967 hat Ghacem mehr als 30 Millionen Tonnen Zement hergestellt. Ein Produktionserfolg, der unter den herausfordernden klimatischen Bedingungen nicht hoch genug bewertet werden kann. Denn im nur einen Steinwurf vom Atlantikstrand entfernten Ghacem-Werk in Takoradi meint man nicht nur die Brandung zu hören, sondern fast schon die Gischt auf der Haut zu spüren. Feuchtigkeit ist also ein Thema – und bei der Zementherstellung immer ein besonders brisantes.
Die im Steinbruch gewonnen Rohstoffe für Zement werden zunächst in einer Brecheranlage zerkleinert und von dort über Förderbänder oder mit Seil- und Schienenbahnen in die Schotterhalle des Zementwerks gebracht. Hier werden sie in einem Mischbettsilo eingelagert und homogenisiert und im nächsten Prozessschritt zu Rohmehl gemahlen sowie entsäuert. Es folgt das Brennen des Rohmehls im etwa 1 450 Grad heißen Drehofen zu Zementklinker, der anschließend gekühlt und auf Korngrößen von bis zu 50 Millimetern gemahlen wird.
Nach dem Mahlen wird der Klinker in Silos oder geschlossenen Hallen gelagert, um Emissionen von Klinkerstaub möglichst zu vermeiden. Zur Herstellung von Zement wird der Klinker allein oder mit weiteren Hauptbestandteilen – zum Beispiel Hüttensand oder Flugasche – gemeinsam feingemahlen. Dabei wird dem Mahlgut zur Regelung des Erstarrens ein Sulfatträger zugesetzt. Dazu verwendet man zur Schonung natürlicher Ressourcen Gips oder Anhydrit aus natürlichen Vorkommen.
Druckluft: zentrales Medium in allen Prozessschritten
In nahezu all diesen Prozessschritten spielt Druckluft eine zentrale Rolle. In den Zementmühlen des Ghacem-Standorts in Takoradi übernimmt sie eine Vielzahl von Aufgaben: Förderluft für den Zementtransport von den Mühlen in die Silos; Steuerluft für die Funktionselemente von Pumpen und Kontrollsystemen; Reinigungsluft zum Ausblasen von Filtern. Ausnahmslos Einsatzgebiete, die in höchstem Maße allergisch auf den Eintrag von Feuchtigkeit reagieren – mit Funktionsausfällen, Produktionsunterbrechungen sowie erhöhtem Wartungs- und Reparaturaufwand. Ursachen dafür sind Verklebungen von Zement und Zusatzstoffen, Materialanbackungen und Korrosion der Anlagenkomponenten. Störungen und Ereignisse, die man in derart produktiv getakteten Anlagen wie denen in Takoradi unter allen Umständen vermeiden muss. Was in der Vergangenheit allerdings unter besonderen klimatischen Belastungen nur bedingt gelang.
Grund dafür war die bisherige konzeptionelle Auslegung der Drucklufttrocknung im Ghacem-Werk Takoradi, die nur zwei zentrale Trockner für das gesamte Werk vorgesehen hatte. Konnte diese Auslegung vor Jahren noch den Erfordernissen genügen, drohte sie auf die erhöhten Anforderungen der Gegenwart jedoch zunehmend mit mangelnder Trocknungsleistung oder gar signifikanten „Wassereinbrüchen“ ins Druckluftsystem zu reagieren. Ein für die QS-Verantwortlichen bei Ghacem unbedingt zu vermeidendes Szenario.
Feuchtigkeit: Schachmatt in drei Zügen
Auf Ingenieurswissen und Systemtechnik aus dem Heimatland der Konzernmutter HeidelbergCement vertrauend, wandte man sich bei Ghacem an die den lokalen Partner des deutschen Druckluftspezialisten BEKO TECHNOLOGIES GmbH. Der Systemanbieter aus dem rheinischen Neuss entwickelte für Ghacem eine unabhängige dreizügige Druckluftaufbereitung. Sie versorgt nun jede der drei Zementmühlen vom eigenen Kompressor bis zu den individuellen Verbrauchsstellen separat mit absolut trockener Druckluft.
Herzstück der Druckluftaufbereitung für die Mühlen sind drei DRYPOINT RA 5400 TAC-Kältetrockner mit jeweils einer CLEARPOINT L080-Vorfiltration und einer ÖWAMAT 16 Öl-Wasser-Aufbereitung von BEKO TECHNOLOGIES. Ergänzt werden sie von einem weiteren DRYPOINT RA 8800 TAC-Kältetrockner, der die ebenfalls separierte Druckluftaufbereitung für die Verpackungsmaschinen absichert.
Die ausgewählten DRYPOINT RA Kältetrockner sind mit ihrer Auslegung die beste Antwort auf die besonderen klimatischen Bedingungen vor Ort in Ghana. Um den extremen Herausforderungen an der afrikanischen Atlantikküste zu begegnen und einen bestmöglichen Drucktaupunkt von 3 Grad Celsius sicherzustellen, wurden die Trockner für Ghacem bewusst um ein Vielfaches überdimensioniert. Außerdem verfügen alle vier Trockner über eine spezielle TAC-Anti-Korrosionsbeschichtung (Anti Corrosion Treatment) auf allen wichtigen Komponenten sowie dem gesamten Gehäuse. Damit sind sie auch gegen die besonders aggressive salzhaltige Meerluft dauerhaft gewappnet.
In den DRYPOINT RA-Trocknern von BEKO TECHNOLOGIES erfolgt die Drucklufttrocknung über einen optimalen Wärmeaustausch durch Gegenstromverfahren über die gesamte Strecke. Die Luft strömt in einer abwärts gerichteten Bewegung ohne ungünstige Umleitungen. Dieser großzügig dimensionierte Counter-Flow-Wärmetauscher, der sich unter anderem aus einem Luft-Luft- und einem Luft-Kältemittel-Wärmetauscher zusammensetzt, kühlt die Druckluft bis auf eine Temperatur von plus zwei Grad Celsius herunter, wobei die Baugröße des Wärmetauschers nicht nur eine besonders effektive Abkühlung begünstigt, sondern auch den Strömungswiderstand auf ein absolutes Minimum senkt.
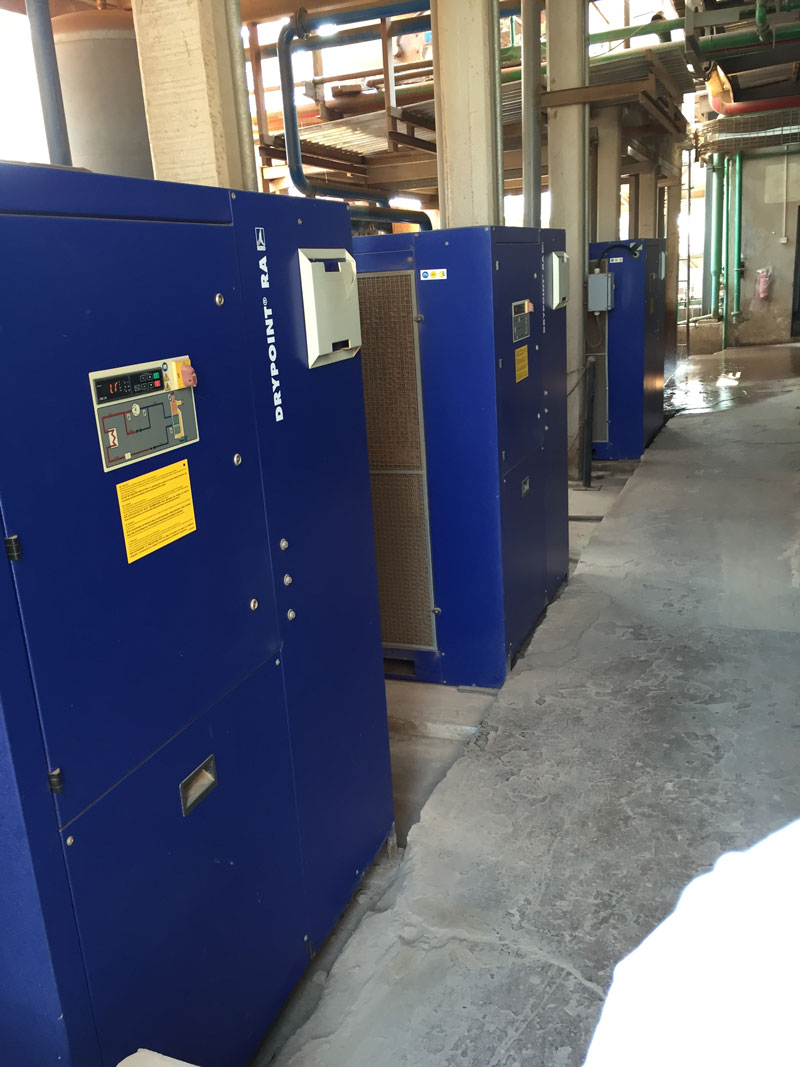
99 Prozent Tröpfchenabscheidung
Wesentliche Konstruktionsmerkmale der DRYPOINT RA Kältetrockner sind der vertikale Aufbau des Wärmetauschers, der einen Kondensatfluss von oben nach unten ermöglicht, ein Demister zur sicheren Abscheidung und ein großvolumiger Beruhigungsraum, der ein Mitreißen des Kondensats vermeidet. Besonders wirtschaftlich ist das Gerät unter anderem durch das Vermeiden strömungsungünstiger Druckluftumlenkungen und unnötiger Strömungswiderstände. Ein konstant niedriger Drucktaupunkt, nahezu 99 Prozent Tröpfchenabscheidung, kaum Druckluftverluste, geringer Wartungsaufwand und niedrige Betriebskosten sind weitere Pluspunkte.
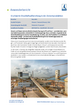