Drucklufttechnik in der Verpackungsindustrie
Branche: | Verpackung, Papier |
Kunde/Ort/Jahr: | Delkeskamp, Nortrup, 2008 |
Anwendung der Druckluft: | Steuerluft, Prozessluft, Kondensattechnik |
Installierte Produkte: | EVERDRY, BEKOSPLIT |
Dieser Industriezweig ist nicht von Pappe: Mehr als 100 darauf spezialisierte Fabriken mit rund 19 000 Mitarbeitern stellen in Deutschland Wellpappe her und verarbeiten sie. Druckluft und ihre Aufbereitung spielen eine zentrale Rolle im Produktionsprozess. Vor allem Feuchtigkeit in der Druckluft hätte fatale Folgen für Anlagen, Rohmaterialien und Fertigprodukte.
Mit einer Jahresproduktion von annähernd neun Milliarden Quadratmeter Wellpappe liegt Deutschland in Europa auf dem ersten Platz und im internationalen Vergleich hinter den USA, China und Japan auf Platz 4. Nahezu drei Viertel aller transportierten Waren in Deutschland sind inzwischen in Wellpappe unterwegs – und fast 30 Prozent aller gefüllten Wellpappenverpackungen überqueren die Landesgrenzen auf ihrem Weg zum Verbraucher. Ein großes Geschäft also, das Kreise zieht und damit für die gesamte deutsche Volkswirtschaft von entsprechender Bedeutung ist.
Einer der Pioniere, Schrittmacher und Leistungsträger dieses Industriezweiges ist die Delkeskamp Verpackungswerke GmbH im niedersächsischen Nortrup. Bereits 1896 als Kartonagenfabrik gegründet, produziert sie außer im Stammwerk Nortrup heute in weiteren Fertigungsstätten in Hannover sowie im tschechischen Odry. Hergestellt werden Papier, Wellpappe und Schaumstoff für Verpackungen vielfältiger Couleur.
Geschlossener Produktionskreislauf
Das Ausgangsmaterial für die Wellpappenherstellung ist das Wellpappenrohpapier. Die Delkeskamp GmbH stellt den weitaus größten Teil des von ihr benötigten Rohpapiers im Werk Nortrup selbst her. Insofern ist dieser Standort das erste Glied eines geschlossenen Produktionskreislaufs – und somit für die Funktionsfähigkeit und Wirtschaftlichkeit der gesamten Delkeskamp-Fertigungsstruktur von entscheidender Bedeutung. Denn neben rein fertigungstechnischen Vorteilen sichert die Eigenerzeugung des Wellpappenrohpapiers dem Unternehmen auch eine maximale Unabhängigkeit vom Beschaffungsmarkt.
Überhaupt steht man bei Delkeskamp gern auf eigenen Beinen. So wird in Nortrup sogar der für die Produktion von Papier benötigte Dampf in einem eigenen Kraftwerk mittels moderner Gasturbinen erzeugt. In diesem Prozess entsteht Elektrizität in einer Menge, die den Eigenbedarf deutlich übersteigt – und dem öffentlichen Netz zugeführt wird. Damit ist man nicht nur Eigenversorger, sondern darüber hinaus anerkannter Energieversorger in Niedersachsen.
Neben der unbedingten Prozesssicherheit in der eigenen Fertigung besteht für das Unternehmen also auch noch eine gewisse Verantwortung für die Menschen der Region. Erwartungen, denen man gerecht werden muss. Einer der Eckpfeiler dafür ist die stabile und qualitativ hochwertige Versorgung des Werkes mit Druckluft – einem für die Produktion in vielfacher Hinsicht entscheidenden Energieträger.
Druckluft ist entscheidender Energieträger
In Nortrup werden drei – eigentlich vier – Betriebszweige mit Druckluft versorgt. Das sind in der Hauptsache die Papierfabrik, die Wellpappe-Produktion und das Schaumstoffwerk. Ein weiterer, wenn auch weitaus geringerer Bedarf entfällt auf das hauseigene Kraftwerk.
Ohne Druckluft würde sich bei Delkeskamp praktisch nichts bewegen. Um das zu verstehen, braucht man sich lediglich die grob skizzierten Fertigungsabläufe in den drei Produktionsbereichen vorzustellen: Das im ersten Schritt in riesigen, hochmodernen Produktionsanlagen aus Altpapier hergestellte Wellpappenrohpapier wird in der ersten Stufe der Pappenfertigung erwärmt und befeuchtet. So erreicht es die erforderliche Elastizität, um geformt zu werden. Im folgenden Schritt wird das Papier unter Druck und Hitzeeinwirkung zwischen zwei zahnradartig ineinandergreifende Riffelwalzen hindurchgeführt. Dann wird das gewellte Papier zunächst mit der Papierinnenbahn von oben und danach mit der Papieraußenbahn von unten verklebt – dadurch kann die Wellpappe ihre optimale Schutzwirkung entfalten.
In vollautomatisierten Arbeitsgängen werden aus den Wellpappenformaten dann Faltkisten, Stanzverpackungen, polsternde Innenverpackungen und Displays hergestellt. Das alles wird über unzählige pneumatische Anlagen und auch durch Druckluft betätigte Regler und Schieber bewegt beziehungsweise gesteuert. Wenn es irgendwo in dieser fein aufeinander abgestimmten Fertigungsabfolge hakt, hat das sofortige Auswirkungen auf die Produktionsquote und vor allem die Fertigungsqualität.
Das Wichtigste: trockene Druckluft
Was Delkeskamp vor allem braucht, neben der Kontinuität der Versorgung, ist trockene Druckluft. Feuchteeintrag in der Druckluft ist pures Gift für die pneumatischen Anlagen und für die Produkte.
Dabei ist feuchte Druckluft längst nicht nur für Papier und Wellpappe ein Risiko. Auch im dritten Produktionsbereich von Delkeskamp, der Schaumstofffertigung, ist Trockenheit ein Muss. Hier werden individuell für unterschiedliche Verpackungen entworfene Formteile aus expandierendem Polystyrol (EPS) hergestellt. Was landläufig unter dem Begriff Styropor bekannt ist, heißt bei Delkeskamp Denopor und ergänzt das nahtlose Verpackungskonzept des Herstellers.
Druckluft wird in diesem Betriebsteil unter anderem für die Arbeit der Formteilautomaten, das Bewegen von Stellzylindern und die Funktion von Ventilen benötigt. Hinzu kommt das Ausblasen der fertigen Formteile aus den Maschinen. Da die fertigen, per Druckluft aus der Formmaschine ausgeblasenen Denopor-Teile in einer ungeheizten Halle gelagert werden, müssen sie absolut trocken sein. Denn bei aller sonstigen Belastbarkeit reagiert dieses Material sehr empfindlich auf frostige Temperaturen. Feuchtigkeit erhöht diese Sensibilität naturgemäß noch.
Trockenheit steht für die Delkeskamp Verpackungswerke GmbH also ganz oben auf der Prioritätenliste der Druckluftversorgung. So auch bei der notwendig gewordenen Erweiterung der Druckluftanlage im Stammwerk Nortrup. Seit 2007 expandiert und investiert man hier in erheblichem Umfang in die Vergrößerung und Modernisierung der Fertigung.
Höherer Druckluftbedarf nach Werkserweiterung
Die bisherige Druckluftstation im so genannten „Kompressorenkeller“ konnte mit diesem Wachstum leistungsmäßig nicht Schritt halten. Die dort untergebrachten fünf Kompressoren plus nachgeschaltetem Adsorptionstrockner brauchten dringend Verstärkung. Und ein schon länger bestehender „Wackelkandidat“ sollte endlich aufs Altenteil geschickt werden: der statische Öl-Wasser-Trenner, der längst nicht immer so funktionierte, wie man es sich bei Delkeskamp wünschte.
Die Suche nach der modernsten Lösung für dieses Problem führte Delkeskamp nach intensiver Marktanalyse zu einem für ihn völlig neuen Ansprechpartner: zum deutschen Druckluft-Systemanbieter BEKO TECHNOLOGIES GmbH.
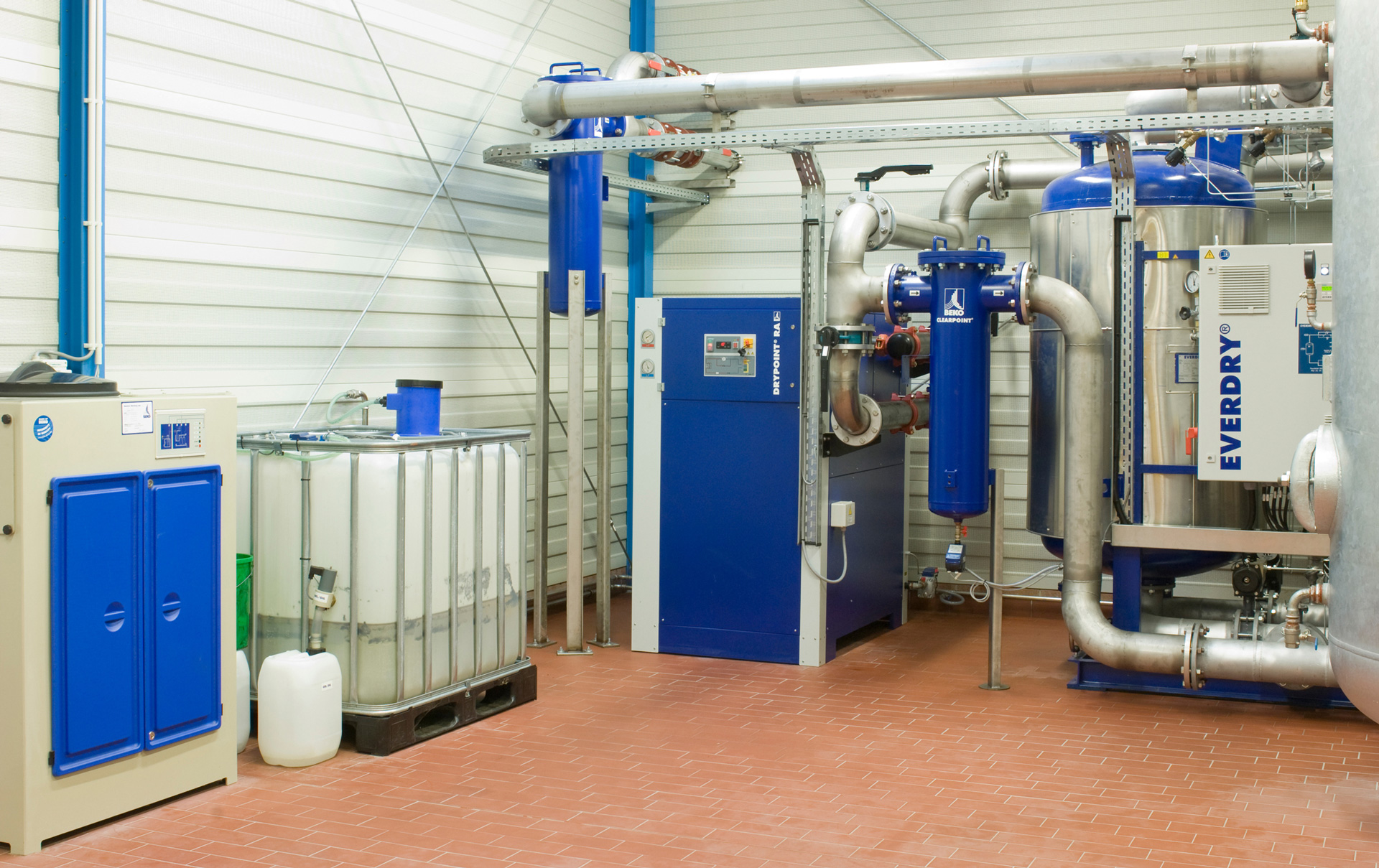
Das im rheinischen Neuss ansässige und weltweit aktive Unternehmen hat eine Technologie zur Trennung von Öl-Wasser-Emulsionen im Programm: BEKOSPLIT. Diese Spaltanlagen reinigen emulgierte Kondensate, wie sie unter ungünstigen Ausgangsbedingungen oder bestimmten Schmierstoff—Verdichter-Kombinationen vorkommen. Neben Druckluftkondensat können auch andere ölhaltige Industrieabwässer aufbereitet werden. Wasserunlösliche organische Verschmutzungen – etwa Öle, pflanzliche oder tierische Fette – sowie eine Vielzahl von Feststoffverunreinigungen werden aus dem Wasser entfernt. Darüber hinaus werden eventuell vorhandene Schwermetalle, Schmutz und Farbpartikel zuverlässig adsorbiert.
Dabei arbeitet das BEKOSPLIT-Prinzip effektiver als eine Ultrafiltration: Es werden keine aggressiven Reinigungsmittel benötigt und weniger Energie gebraucht. Der Investitionsbedarf ist äußerst überschaubar und längere Wartungsintervalle fördern die Wirtschaftlichkeit zusätzlich.
Ein System bewährt sich
Doch es sollte mehr aus diesem Kontakt zum Druckluftspezialisten BEKO TECHNOLOGIES werden. Schnell erkannte man bei Delkeskamp, dass man mit BEKO TECHNOLOGIES einen Partner gefunden hatte, der ähnlich „tickte“ wie man selbst. Der übergreifend dachte und schlüssige Gesamtkonzepte entwickelte. Die Sache begann spannend zu werden.
Vor allem, als man bei BEKO TECHNOLOGIES begann, das für Delkeskamp so sensible Thema der Drucklufttrocknung doch auch einmal zu überdenken. Zum Beispiel, was die Wirtschaftlichkeit betraf. Als man sogar so weit ging, die Aufbereitung von den bislang ausschließlich eingesetzten Adsorptionstrocknern zu einem guten Stück auch auf Kältetrockner zu übertragen, fielen die Türen allerdings zunächst wieder ins Schloss.
Für Delkeskamp kam dieser Vorschlag zunächst einmal einer Palastrevolution gleich, vertrauten sie doch einzig auf das Prinzip und die Sicherheit der Adsorptionstrocknung für die Anlagenauslegung. Man hatte da bislang keinerlei Probleme und wollte sich keine unnötigen Risiken ins Haus holen. Andererseits war der Kältetrockner-Gedanke enorm reizvoll, wenn man sich die weitaus günstigere Energiebilanz dieses Verfahrens im Vergleich zum Adsorptionstrockner anschaut. Wenn man also beides kombinieren könnte…
Genau die richtige Herausforderung für den Systemanbieter BEKO TECHNOLOGIES. Innerhalb weniger Tage entwickelte er für Delkeskamp ein schlüssiges Konzept für ein redundant aufgebautes Kombinationssystem aus Adsorptions- und Kältetrockner. Das ist seit Mai 2008 Realität.
Dieses System erlaubt dem Verpackungshersteller, je nach Anforderung und Umfeldbedingung – zum Beispiel saisonal – die jeweils sowohl sicherste als auch kostengünstigste Trocknerkonstellation zu fahren. Entweder als flexible Kombination beider Verfahren oder ausschließlich über Adsorptions- beziehungsweise Kältetrocknung.
Da die Rohrleitungen der Druckluftanlage innerhalb des Werksgeländes über Rohrbrücken weitgehend im Außenbereich verlaufen, sind sie naturgemäß saisonal großen Temperaturschwankungen unterworfen. So muss zum Beispiel zum Schutz vor Nachkondensation und Einfrierungen im Winter ein Drucktaupunkt von besser als minus 40 °C gegeben sein. Um hier höchste Prozesssicherheit zu erzielen, sind die installierten EVERDRY-Adsorptionstrockner von BEKO TECHNOLOGIES mit entsprechender Taupunktmessung und Steuereinheiten ausgestattet. Bislang funktioniert das perfekt. Die Trocknerleistung ist absolut stabil und die Energiebilanz hat sich spürbar verbessert.
Inzwischen setzt man bei Delkeskamp in der modernisierten Druckluftaufbereitung ausschließlich auf BEKO TECHNOLOGIES-Geräte. Neben den BEKOSPLIT-Spaltanlagen, EVERDRY-Adsorptionstrocknern sowie dem DRYPOINT-Kältetrockner verrichten auch CLEARPOINT-Filter ihren Dienst.
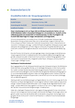