Drucklufttrocknung in der Gipsaufbereitung
Branche: | Baustoffe |
Kunde/Ort/Jahr: | Remondis, Lünen, 2010 |
Anwendung der Druckluft: | In der Produktion |
Installierte Produkte: | EVERDRY |
Feuchtigkeit ist der größte Feind der 432 Gewebefilterschläuche im Wirbelschicht-Ofen 7 der Remondis Production GmbH am Lippewerk im westfälischen Lünen. Er dient dem Kalzinieren von Gips – einem naturgemäß äußerst hydrophilen Material. Mit einem warmregenerierenden Adsorptionstrockner für die Reinigungsdruckluft der Tuchfilter unterbindet man nun die unselige Verbindung von Wasser und Gipsstaub im Filtergewebe. Dabei dachte man zunächst an eine ganz andere Lösung.
Remondis ist eines der weltweit größten Unternehmen der Wasser- und Kreislaufwirtschaft mit über 500 Standorten in 26 Ländern auf drei Kontinenten. Kernkompetenzen des Konzerns sind die Wasserversorgung und Wasseraufbereitung, das Gewinnen von Rohstoffen aus Abfällen, das Entwickeln von Recyclingprodukten und das Bereitstellen alternativer Energieträger. In einem weiteren Geschäftsfeld erfolgt das Aufbereiten von Gipsen aus der Rauchgasreinigung und industriellen Prozessen zu hochwertigen Gipsbindemitteln.
Dafür bewegt Remondis riesige Stoffmengen, die als Sekundärrohstoffe wieder in den Wirtschaftskreislauf zurückgeführt werden können. Allein 1200 Mitarbeiter findet man am Remondis-Standort in Lünen. Mit einer Fläche von 230 Hektar ist es das größte Zentrum für industrielle Kreislaufwirtschaft in Europa. Im Mittelpunkt stehen hier die Rohstoffgewinnung, die Herstellung von Grundstoffen, Spezialprodukten und Industriegütern sowie die Energieerzeugung.
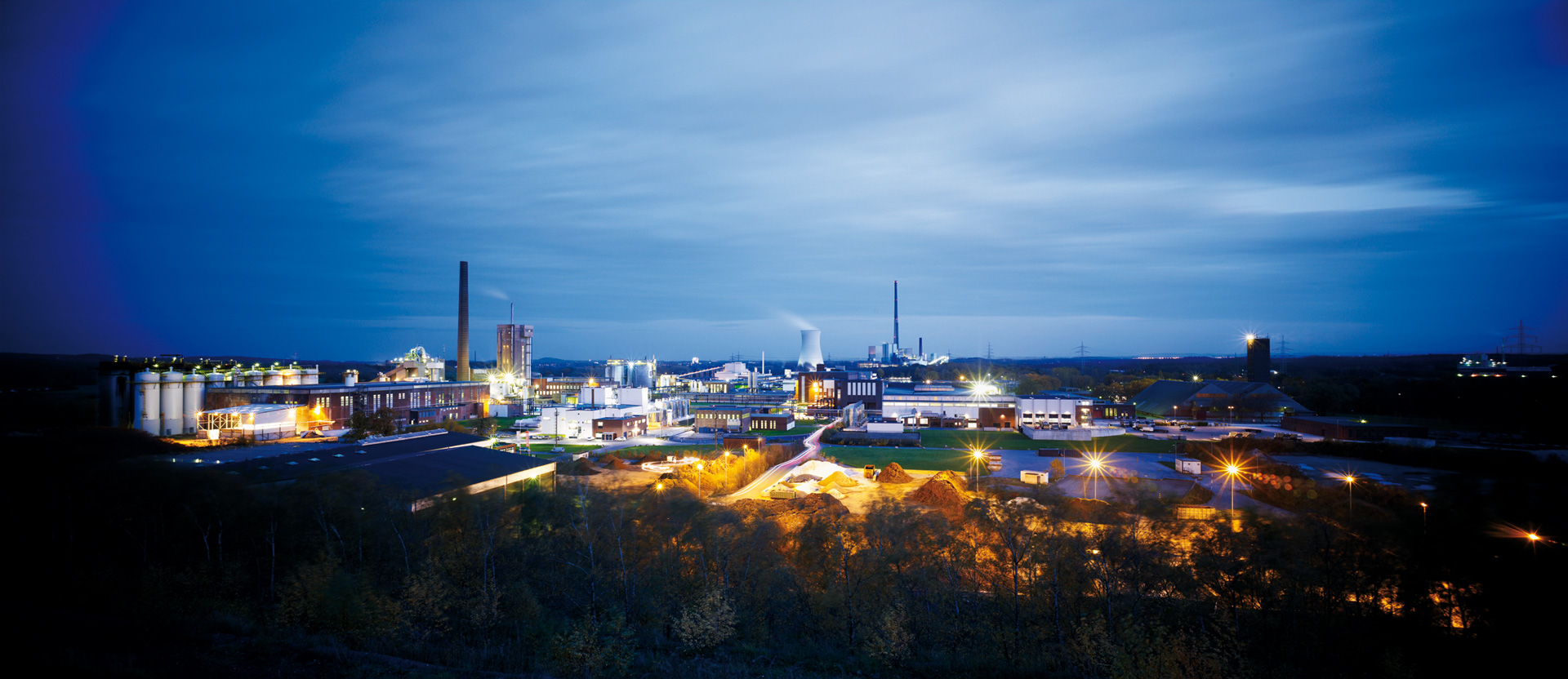
Eine der großen Aufgaben ist das Aufbereiten von jährlich rund 280 000 Tonnen Gips, die in Kohlekraftwerken der näheren Umgebung als Nebenprodukte anfallen. Sie entstehen in den Rauchgasentschwefelungsanlagen (REA) von Kraftwerken, die mit fossilen Brennstoffen befeuert werden.
In Lünen wandelt Remondis diese REA-Gipse in hochwertige Additive und Bindemittel um, die wiederum – unter dem Handelsnamen RADDiBIN – der Gipsindustrie als Rohstoffe für verschiedene Anwendungen zugeleitet werden. Aus ihnen entstehen beispielsweise Fließestriche, Porenbeton, Düngemittel, Zement oder Werkstoffe für die Zahnmedizin.
Im Lippewerk gehen derzeit zwei Produkttypen aus den aufbereiteten REA-Gipsen hervor. Zum einen ALPHA Halbhydrat, das nach Zugabe von Wasser eine besonders hohe Festigkeit aufweist. Und zum anderen Anhydrit. Es wird bei sehr hohen Temperaturen gebrannt und eignet sich besonders für die Herstellung von Estrichmörteln.
Bei der Anhydrit-Produktion läuft nichts ohne Ofen 7. Dieses über 50 Meter hohe „Ungetüm“ ist im wörtlichen Sinne der Brennpunkt des Geschehens. In ihm erleben täglich rund 1000 Tonnen REA-Gipse bei einer Temperatur über 800 Grad Celsius ihre Metamorphose zum wertvollen Rohstoff.
Viel Wirbel um die Qualität
Der so genannte Kalzinierofen arbeitet nach dem Prinzip der zirkulierenden Wirbelschicht. Ursprünglich für die Kalzinierung von Aluminiumhydroxid gebaut, wurde er bei der Umstrukturierung des Lippewerks im Jahre 1989 umgerüstet, um fortan das Kalzinieren von Gips zu übernehmen.
Bei der Kalzinierung in der Wirbelschicht wird feinkörniges Material in einem Heißgas mit hohen Geschwindigkeiten transportiert und gleichzeitig durch die Energie der Heißgase zu Anhydrit entwässert. Dieser Vorgang wird durch die einzigartige Anlagentechnik so gesteuert, dass alle Partikel der gleichen Verweilzeit und den gleichen Prozesstemperaturen ausgesetzt sind. Dadurch gelingt es, im großtechnischen Maßstab eine Qualität zu realisieren, die den Eigenschaften einer Laborqualität im Kleinstmaßstab entspricht.
Für Ofen 7 sind Qualitätsschwankungen kein Thema. Schließlich hat er verfahrenstechnisch alles in trockene Tücher gebracht. Und das darf man wörtlich nehmen. Denn einer der neuralgischen Punkte des feurigen Riesen sind seine Gewebefilter. Werden sie zu feucht, steht schnell auch der Produktivität und Qualität „der kalte Schweiß auf der Stirn“.
Feuchtigkeit treibt Schweiß auf die Stirn
Das Risiko eines Feuchtigkeitseintrags in das Gewebe liegt vor allem in der Reinigung der Gewebefilter mit Druckluft. Dabei werden die Tücher mit starken Druckstößen angeblasen, um anhaftenden Gips auszutreiben. Ist die dazu verwendete Druckluft nicht absolut trocken, wird mit den Druckimpulsen auch Feuchtigkeit in das Gewebe geblasen. Der Luftdruckstoß führt zudem schlagartig zu einer Abkühlung mit gleichzeitiger Taupunktunterschreitung.
Die Feuchtigkeit reagiert mit den Gipsrückständen im Gewebe und bindet den Gipsstaub ab. In der Folge verhärten die Tücher und brechen schließlich. Ein schleichender Prozess, der jedoch die Gewebealterung immens beschleunigt. Hier sah Remondis ein erhebliches Sparpotenzial bei den Betriebskosten. Grundlage einer deutlich erhöhten Wirtschaftlichkeit sollte die Ergänzung der Druckluftaufbereitung um eine leistungsstarke Drucklufttrocknung sein.
Die Standzeit der mit ungetrockneter Druckluft gereinigten Tuchfilter im Ofen 7 lag bis dato bei etwa zwei Jahren. Würde man stattdessen eine Trocknung vornehmen, ließe sich die Lebensdauer der Gewebe auf etwa drei Jahre verlängern, so die Berechnungen. Bei 432 installierten Tüchern zu einem Stückpreis von rund 100 Euro also eine enorme Kostenersparnis.
Nach eingehenden Planungen schrieb Remondis Anfang 2009 die Installation eines kaltregenerierenden Adsorptionstrockners in der Druckluftanlage des Ofens aus.
Mit wärmsten Empfehlungen
Entgegen der Ausschreibung und konträr zu allen anderen Anbietern schlug BEKO TECHNOLOGIES GmbH ein warmregenerierenden Drucklufttrockner vor. Für größere Volumenströme ist die Adsorptionstrocknung fraglos das einzige industriell gängige Verfahren zur Trocknung von Druckluft auf Taupunkte von minus 20 Grad Celsius und tiefer. Die im Anwendungsfall konkrete Größe – bei Remondis bis zu 1 500 Kubikmeter pro Stunde – führte dann letztlich zur wirtschaftlich wirklich sinnvollsten Entscheidung zwischen kaltregenerierenden und warmregenerierenden Geräten.
Kaltregenerierende Adsorptionstrockner
Kaltregenerierende Adsorptionstrockner arbeiten mit kurzen Beladungszyklen. Durch die geringe Beladung des Trockenmittels erfolgt die Regeneration ohne zusätzlichen Eintrag von Wärmeenergie. Die Feuchtigkeit wird durch einen auf den atmosphärischen Druck entspannten Trockenluftteilstrom ausgetragen.
Elektrische Energie wird beim kaltregenerierenden Adsorptionstrockner lediglich für die Steuerung und das Umschalten der Ventile benötigt. Die dafür erforderliche elektrische Leistungsaufnahme ist somit vernachlässigbar klein. Aber: Den geringen bis mittleren Investitionskosten stehen die Kosten für den Verbrauch von etwa 15 Prozent der bereits aufbereiteten Druckluft gegenüber, bezogen auf Volllastbedingungen bei 7 bar.
Die Kosten durch die Spülluftverluste summieren sich schnell auf inakzeptable Beträge. Das war für Remondis das überzeugende Argument, sich für ein warmregenerierendes Gerät zu entscheiden.
Warmregenerierende Adsorptionstrockner
Bei Anlagen mit Gebläseluftdesorption gibt es unterschiedliche Bauformen. Allen Verfahren gemeinsam ist, dass zum Entfernen der adsorbierten Feuchtigkeit keine aufbereitete Systemluft, sondern erhitzte Umgebungsluft zum Einsatz kommt. Unterschiede gibt es dann jedoch bei den Methoden zur Kühlung des Trockenmittels.
Bei der klassischen Ausführung wird zum Kühlen des Trockenmittels schlicht ein entspannter Teilstrom aufbereiteter Druckluft herangezogen. Natürlich entsteht hier wieder ein zweckentfremdeter Anteil wertvoller Druckluft. Auch wenn dieser sich durchschnittlich auf nur zwei bis drei Prozent beläuft, bleibt doch eine Beeinträchtigung der Wirtschaftlichkeit.
Die ökonomischere Alternative sind „Zero Purge“-Adsorptionstrockner, die ohne jeglichen Verbrauch aufbereiteter Druckluft arbeiten. Bei ihnen erfolgt die Desorption wie beim klassischen Verfahren durch erhitzte Umgebungsluft, die ein Gebläse durch das Adsorptionsmittel führt. Die anschließende Kühlung des erhitzten Trockenmittels geschieht hier ebenfalls durch Umgebungsluft.
Die Wirtschaftlichkeit hinter dem Ofen hervorgelockt
Nach eingehender Analyse der Umgebungs- und Betriebsbedingungen am Ofen 7 fokussierten sich die Aufbereitungs- und Systemspezialisten von BEKO TECHNOLOGIES auf den warmgenerierenden Adsorptionstrockner vom Typ EVERDRY FRA-V aus dem breiten Produktprogramm des Hauses. Die Anlagen der Baureihe FRA-V benötigen weder für den Desorptionsprozess noch für die anschließende Kühlung des erhitzten Trockenmittels Druckluft (Zero Purge).
In der Desorptionsphase arbeitet das Regenerationsgebläse im Druckbetrieb. Während in einem Adsorptionsbehälter die Trocknung der Druckluft stattfindet, wird der zuvor mit Feuchtigkeit gesättigte Adsorptionsbehälter regeneriert. Vor Regenerationsbeginn wird hier eine sanfte Druckentlastung auf Atmosphärendruck vorgenommen. Das Regenerationsgebläse fördert Umgebungsluft zum nachgeschalteten Erhitzer. Dort erfolgt die Erwärmung auf die erforderliche Desorptionstemperatur.
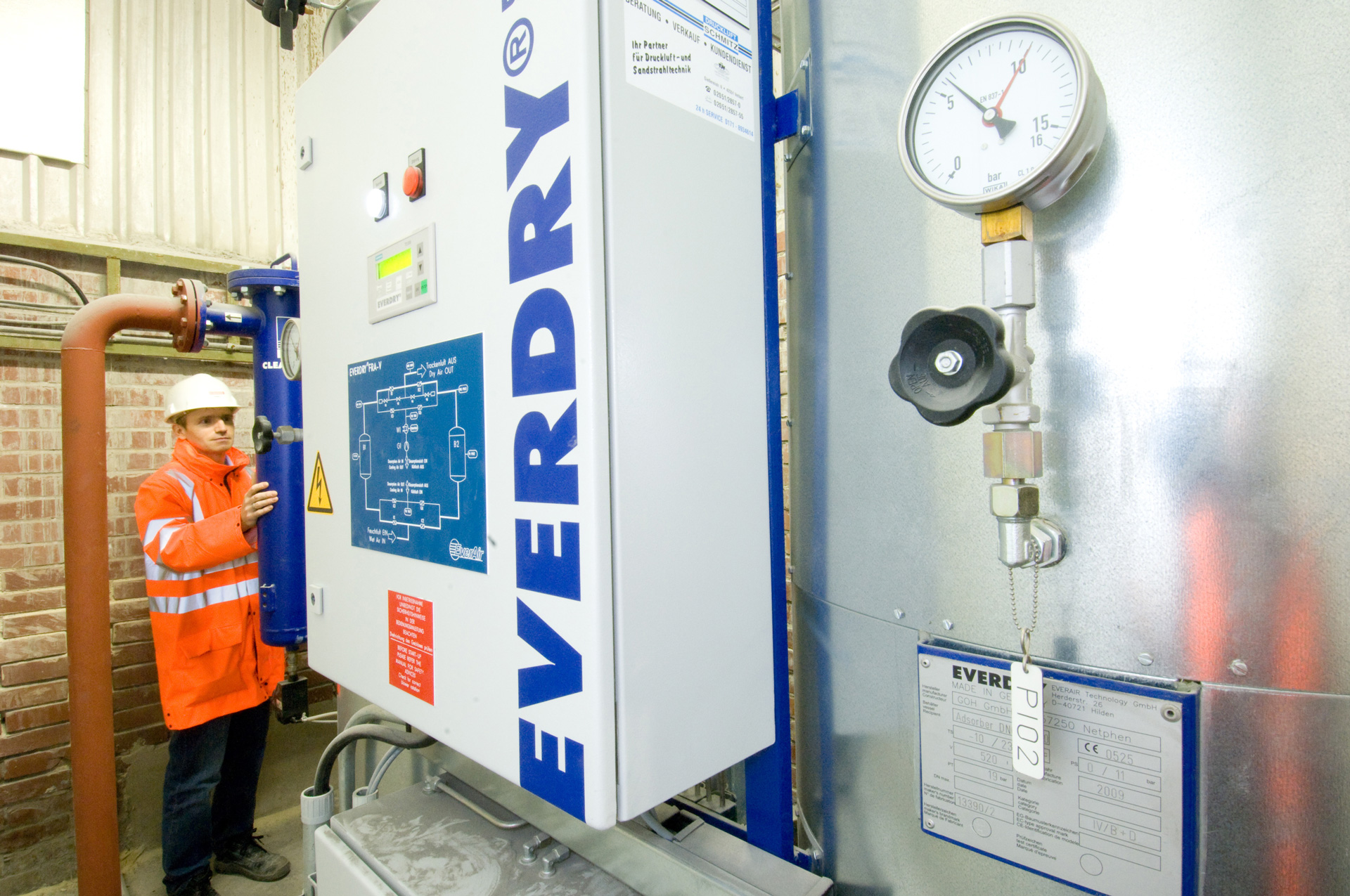
Durch den Druckbetrieb des Regenerationsgebläses entsteht ein Temperaturzugewinn, der sich positiv auf den Leistungsbedarf des Erhitzers auswirkt. Der Gebläseluftstrom verdampft die im Trockenmittel aufgenommene Feuchtigkeit und wird anschließend mit dem Luftstrom in die Atmosphäre geleitet. Die Desorption läuft energetisch optimiert im Gegenstromverfahren ab.
Die Kühlphase erfolgt im Vakuumbetrieb. Temperatur- und Taupunktspitzen nach der Umschaltung werden vermieden, indem die nach der Desorptionsphase im Trockenmittel gespeicherte Wärme mit dem kühlen Gebläseluftstrom abgeführt wird. In der Kühlphase schaltet das Gebläse auf Saugbetrieb, wodurch die Umgebungsluft unmittelbar in den zu kühlenden Adsorptionsbehälter strömt. Der beim Saugbetrieb erzeugte Unterdruck bewirkt eine Veränderung der physikalischen Waage im Trockenmittel. Durch den Unterdruck sinkt die Desorptionstemperatur, wodurch während der Kühlphase eine Nachdesorption einsetzt. Durch diese Nachdesorption stellt sich im Trockenmittel nach Ende der Regenerationsphase (Heizen und Kühlen) eine geringere Restbeladung ein. Die Restbeladung im Trockenmittel beeinflusst maßgeblich die Qualität der Trocknungsphase.
Allein durch den energieeffizienten Betrieb des warmregenerierenden Adsorptionstrockners im Vergleich zu einem kaltregenerienden durfte man bei Remondis von einer Amortisation der Investitionskosten in weniger als einem Jahr rechnen. Doch nicht nur diese Perspektive veranlasste Remondis, sich für die Lösung der BEKO TECHNOLOGIES GmbH zu entscheiden. Wichtig war uns auch die Flexibilität und das übergreifende Denken in der Planungs- und Realisierungsphase. Da waren Remondis natürlich mit einem Systemanbieter wie BEKO TECHNOLOGIES bestens bedient. Dass der schönen Theorie denn auch erfolgreiche Praxis folgt, beweist der seit Herbst 2009 hocheffiziente Einsatz des Trockners am Ofen 7 im Lippewerk Lünen.
Übrigens bringt der EVERDRY-Adsorptionstrockner dort nicht nur die Filterreinigung in trockene Tücher. Deutlich verbessert hat sich die Prozesssicherheit auch in einem weiteren Einsatzfeld der Druckluftanwendung am Ofen 7: dem Betrieb der Messsysteme an der Brenneranlage. Und auch Probleme mit Feuchtigkeit und Öl an den Brennerdüsen des Ofens sind seit Installation des Trockners Vergangenheit.
Adsorptionstrocknung mit System
Die Produktreihe EVERDRY von BEKO TECHNOLOGIES bietet zahlreiche Variationsmöglichkeiten. Die standardisierte Baureihe ist für Volumenströme bis 20 000 m³/h verfügbar. Sonderlösungen über 20 000 m³/h gehören ebenfalls zum Leistungsportfolio. Die Anlagen der Baureihe FRA-V stellen als Zero-Purge-Adsorptionstrockner auf hohem technischem Niveau das wirtschaftliche Fundament für vielfältige Anwendungen.
Auch für den Einsatz bei hohen Eintrittstemperaturen in warmen und feuchten Klimazonen bietet die EVERDRY-Produktpalette geeignete Lösungen mit intelligentem Kosten-Nutzen-Gefüge. Der EVERDRY FRL als „closed-loop“-Adsorptionstrockner eignet sich mit seiner Kühlführung im geschlossenen Kreislauf sogar für den Einsatz unter tropischen Klimabedingungen.
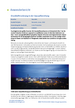