Clean compressed air for laser beams
Industry: | Applied medical research |
Customer/Location/Year: | Laser research centre CALA, Munich (Germany), 2017 |
Use of compressed air: | Measuring, control, process air |
Installed products: | METPOINT OCV |
When a new think-tank and research centre is built for medical science, visions become reality. As is the case with the new Garching research campus near Munich: this is where work started in 2008 on planning, building and equipping the laser research centre CALA (Centre for Advanced Laser Applications). After ten years of planning and construction work, it is finally scheduled to go into operation in 2018. Permanent measurement of the compressed air quality ensures supply to highly complex laser systems in the CALA research centre.
Biomedical imaging, tumour therapy and risk-free screening: in this new research centre, physicists, doctors and biologists from the Ludwig-Maximilians-University (LMU) and the Technical University Munich (TUM) will investigate the potential of light for the early diagnosis and therapy of serious diseases such as cancer. Only when research and possible therapies are made as cost-effective as possible can the maximum number of cancer patients profit from this work in future. Compressed air, and in particular its purity, plays an important role in the use of intense laser light. It is therefore crucial for the researchers that the compressed air quality is monitored at all times – a sensitive process that is simplified and rendered suitably reliable through the use of an online measuring system.
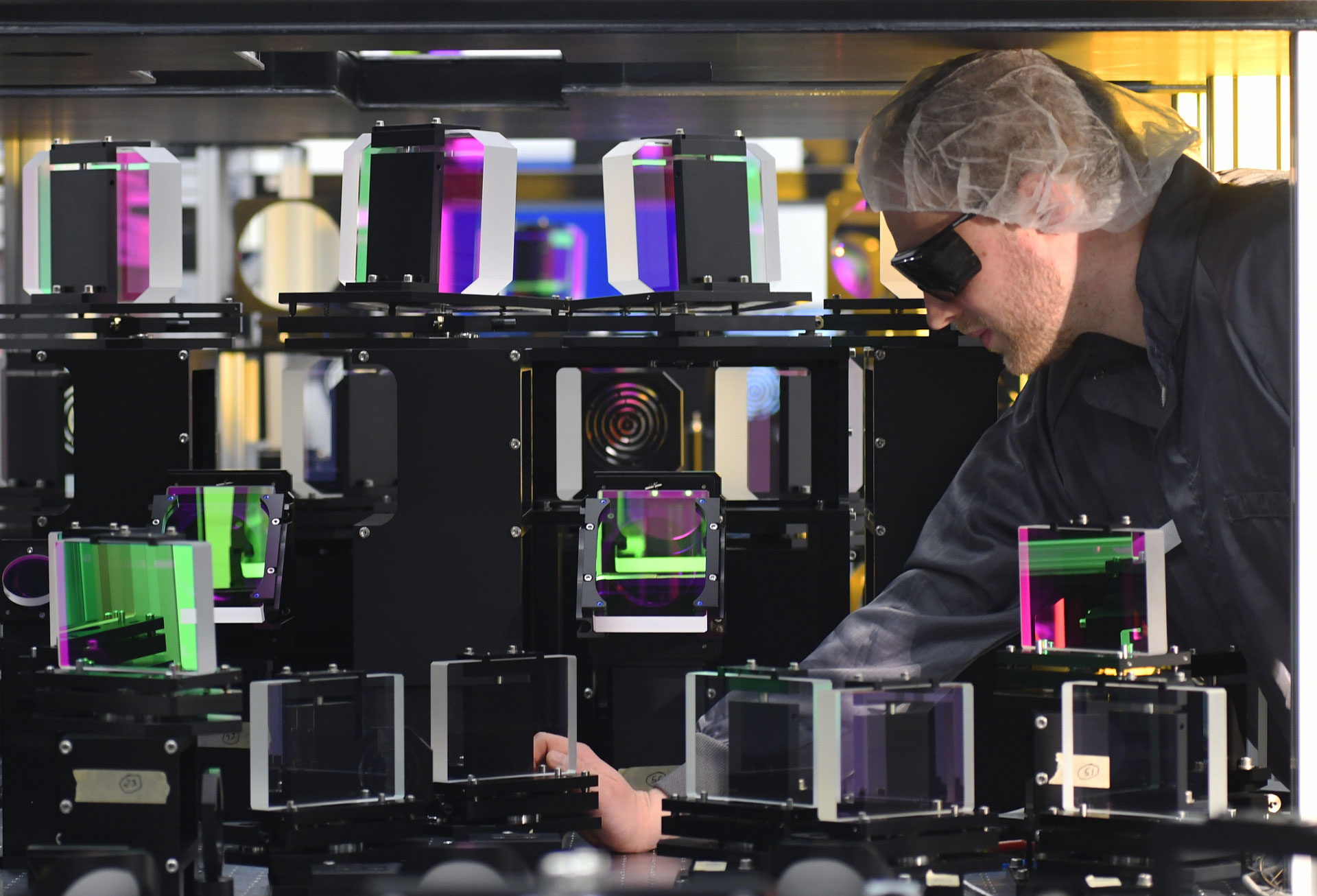
The researchers in Munich generate laser light with the latest laser systems. The laser beam is guided through the beamline – a system of tubes in an ultra-high vacuum that runs beneath the floor panels of the research centre: from the light source to the various applications and test laboratories in the building - for over 50 metres. Only the cleanest, purest compressed air may be used to ventilate the beamline. Gate valves operated by compressed air separate the sections of the beamline from the experimental chambers. Even the slightest contamination of the compressed air could tarnish the deflection mirrors and thus have a tangible influence over the quality of the overall system. il or moisture residues would make the laser light more diffuse, solid particles could even damage the deflection mirrors. The very clean compressed air is also used to clean the deflection mirrors with the help of a plasma gun.
Complete monitoring of the compressed air quality
So as to permanently monitor the quality of the compressed air and to be able to react immediately in the event of any contamination, the persons responsible for the CALA project decided on checks by the METPOINT OCV measuring device from BEKO TECHNOLOGIES. The measurement method used by the compressed air specialists from Neuss is TÜV-certified according to the requirements of ISO 8573-1, class 1-4, and therefore offers maximum security when recording and analysing data on the compressed air quality. The measuring device permits analyses in the range of thousandths of a milligram of residual oil mist per cubic metre. The online system monitors the compressed air around the clock during normal operation. It does away with sampling and time-consuming laboratory analyses.
Automated control of the compressed-air valves
The measuring device automates the handling of the measurement and control of compressed air. Hence, it also simplifies the control of connected systems. This reduces the risk of contamination to the entire laser system as well as the time and effort needed for such a highly complex technology and ramified laser infrastructure as that in CALA. Apart from the sophisticated technology, an extensive cooling water and ventilation system, whose pipes run throughout the entire building, guarantee safe and reliable operation of the plant.
The beamline, also referred to a the “laser motorway”, runs beneath the floor panels in a false floor that is around one metre high. In the event of any contamination through oil, the compressed air lines and the beamline would have to be cleaned. The measuring device, however, allows an overriding control of the gate valves and compressed air valves. The technology sounds an alarm as soon as the recorded data exceeds an individually adjustable limit. The compressed air main valve is closed to prevent any contamination of the overall laser system.
High process reliability through quality control of the compressed air
Compressed air plays an important role for the efficiency and smooth operation of the laser centre. Which is why the permanent measurement and control of its quality is crucial for process reliability, and the measuring device an indispensable indicator. This lays the technical foundations for successful research in the laser centre.
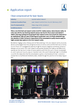