In our solutions for branches and applications we describe which typical compressed air quality standards are needed in different fields of application.
Compressed air quality according to ISO 8573-1
The DIN ISO 8573 series of standards deals with compressed air quality in nine parts. Parts two to nine include test methods. Part 8573-1 classifies compressed air by a maximum content of impurities (particles, water and oil) that may be contained. The DIN ISO 8573-1 standard defines the quality classes of compressed air with regard to:
Particle size and density
Determination of size and concentration of the solid particles which may still be contained in the compressed air.
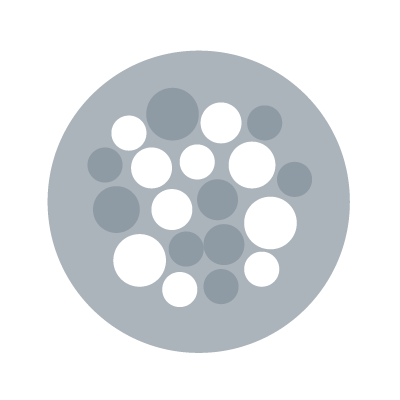
Pressure dew point / moisture
Determination of the temperature at which water vapour condenses to water at the current operating pressure
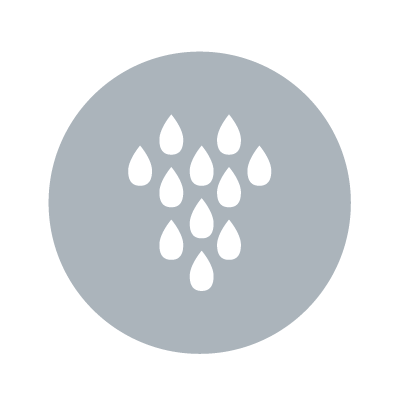
Oil content
Determination of the residual quantity of oil aerosols and hydrocarbons which may be contained in the compressed air.
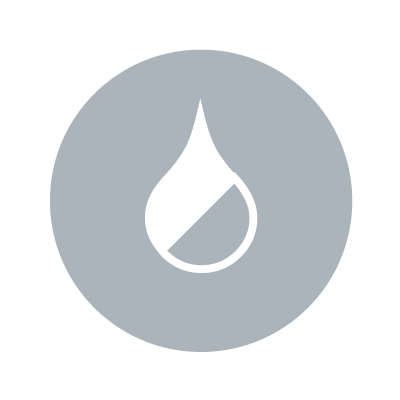
ISO8573-1 is the main publication of the ISO8573 series of standards, as it specifies the permissible amount of pollutant per cubic metre of compressed air. In ISO 8573-1, solid particles, water and oil are named as the 3 primary pollutants.
To express a specific quality, three digits are used, separated by a colon.
A Class of particles (solid and liquid impurities),
B Class of moisture (gaseous) and water (liquid) content; and
C Class of total oil content (liquid and gaseous).
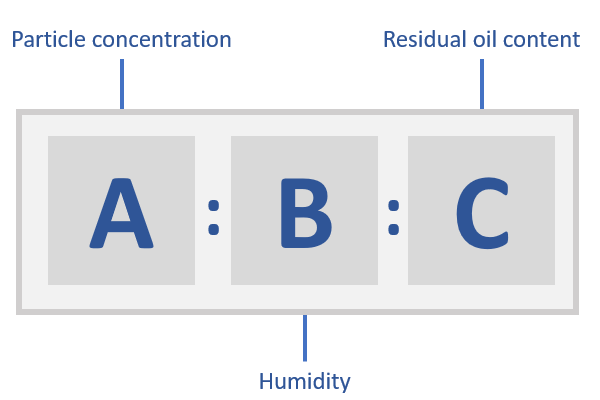
Filling tires, for example, requires quality class 2 for both particle and oil concentration, whereas spray gun and laser cutting requires class 1 particle and oil content. While Class 4 humidity is sufficient for general applications with factory or service air, more complex process engineering processes require Class 2 to Class 1 humidity.
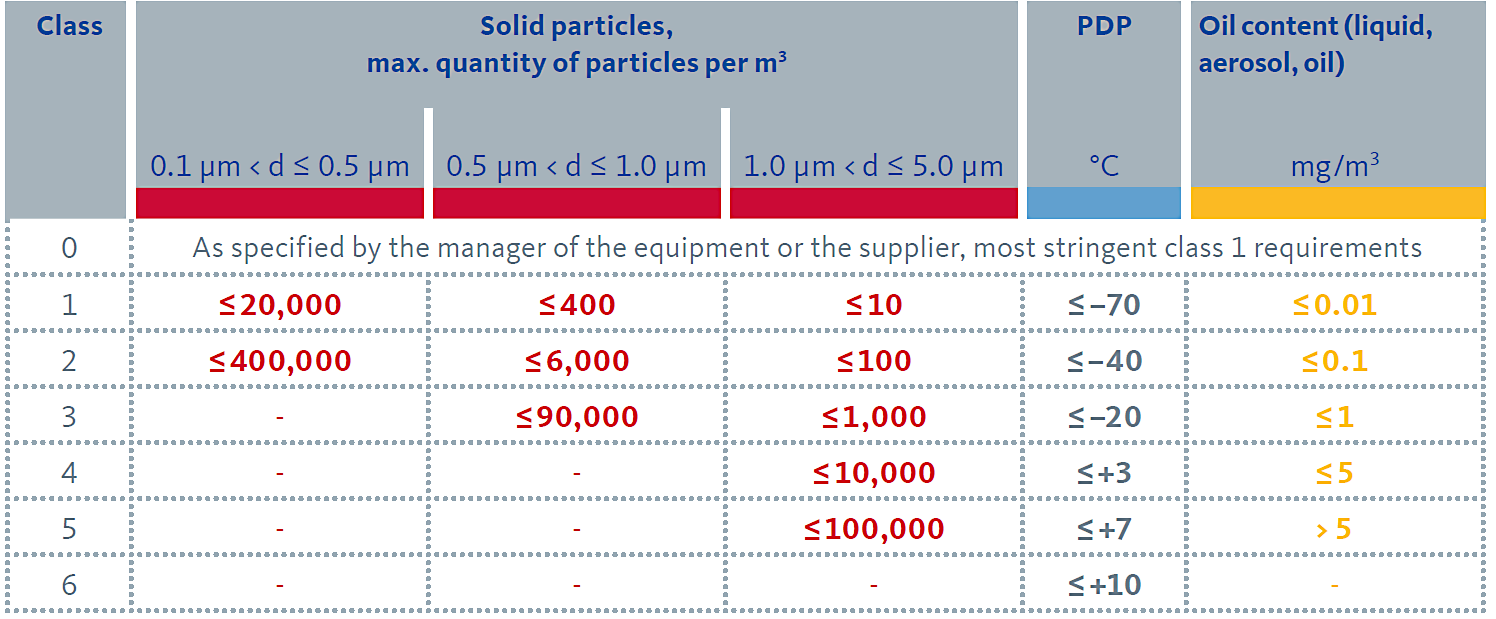
Compressed air treatment with a system
The compressed air schedule shows an overview with all possibilities. How to achieve a certain compressed air quality with which compressed air preparation products.
Compressed air is an important source of energy in almost all industries. The required quality varies from industry to industry and from application to application. However, the desire for optimal production processes, safe systems and cost-efficient operation remains the same. We fulfill these requirements on the way from the compressed air generator to the application with safe, reliable and globally proven treatment technology. And thus ensure your success!
Quality is not a coincidence
Companies face great challenges in production: if product and process safety depend on the quality of the compressed air, the treatment at the highest level must be ensured at all times. You can only win the trust of consumers if you take responsibility and unconditionally rely on quality assurance. At the same time, the profitability of the processes determines the future viability of the company. An intelligent energy management has the highest priority: In compressed air generation, energy costs often amount to more than three quarters of the total costs, the savings potential in this area is considerable. BEKO TECHNOLOGIES measurement technology helps to identify these potentials.