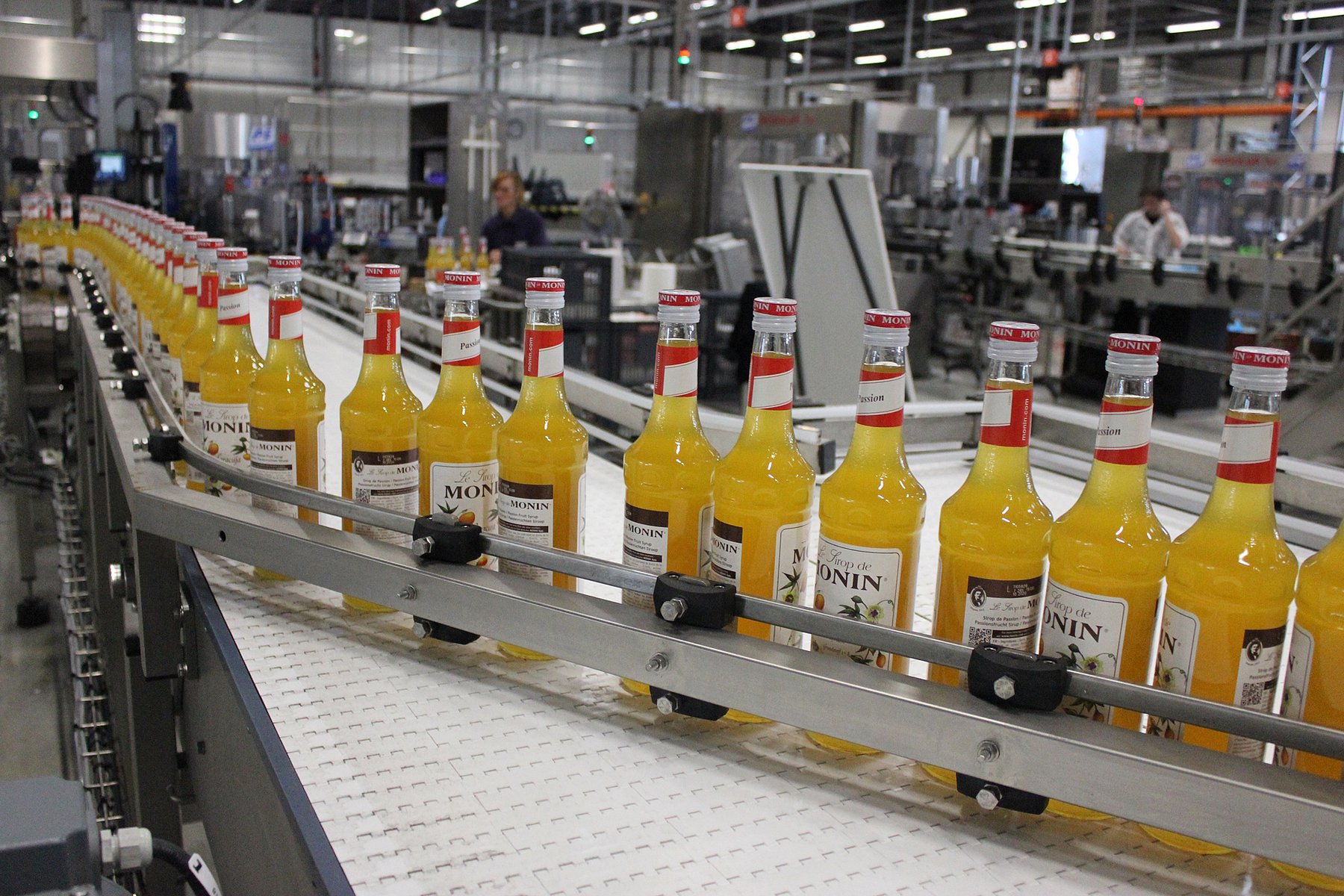
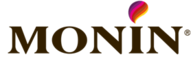
Industry:
Location:
Application:
Installed products:
Welcome to Monin
MONIN specializes in the production and marketing of syrups, liqueurs and fruit purees. Growing demand prompted the company to replace the historic production facility in Bourges with a new 20,000 m² building. There, 150,000 bottles are now filled every day on six production lines, which corresponds to an output of around 25 million units per year.
A comprehensive catalog of requirements
MONIN entrusted MIB (Maintenance Industrielle du Berry), BEKO TECHNOLOGIES' French distributor, with the design of a new solution for compressed air treatment. The requirement was for a complete system, including a dryer, to treat a maximum volume flow of 1,160 m³/h at a minimum operating pressure of 8 bar effective and a maximum inlet temperature of +38 °C to achieve a pressure dew point (DTP) of -40 °C. In addition, the requirement criteria in comparison with the disused plant included lower operating and energy costs.
In terms of food safety, compressed air of the highest quality was desired, which was to be monitored and made traceable by measurement technology. In the food industry, compressed air comes into direct or indirect contact with the products at various points in the process chain and should therefore be absolutely free of solids, oil, moisture and germs.
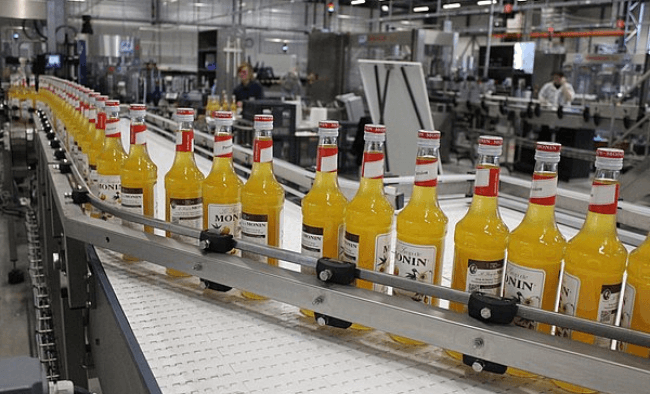
The food industry wants safe products. An important influencing factor is the quality of the compressed air, which is used at many points in the manufacturing process. The French syrup manufacturer MONIN installed a new compressed air treatment unit from BEKO TECHNOLOGIES at the Bourges site. The system meets the highest standards, which go far beyond the usual requirements in the food sector.
Berndt Sander, Head of Marketing, BEKO TECHNOLOGIES
Clean compressed air made to measure
After a thorough on-site analysis, MIB and BEKO TECHNOLOGIES installed a tailor-made compressed air treatment system in 2018. The new station consists of perfectly coordinated standard elements. A 110 kW oil-free, variable speed, dry screw compressor produces the compressed air. The heart of the processing plant from BEKO TECHNOLOGIES is the heat-regenerating adsorption dryer EVERDRY FRA-Vplus ZERO PURGE. In this model, desorption takes place countercurrently to the direction of adsorption with heated blast air and cooling takes place in parallel. This means that there is no loss of compressed air for regeneration (ZERO PURGE).
A water separator is installed in front of the dryer, an oil filter system and a dust filter behind it filter out solid impurities. Several BEKOMAT condensate drains remove condensate from the compressed air system.
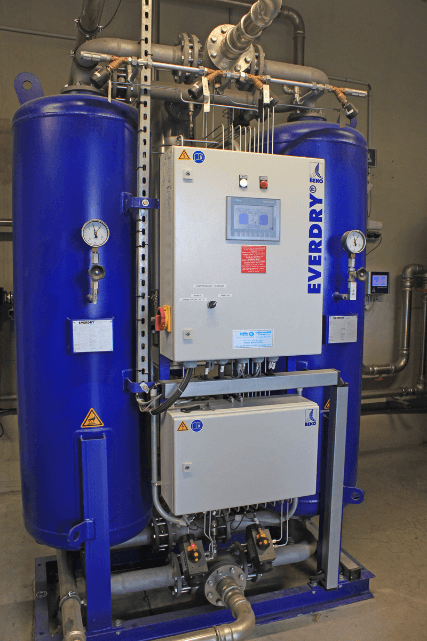
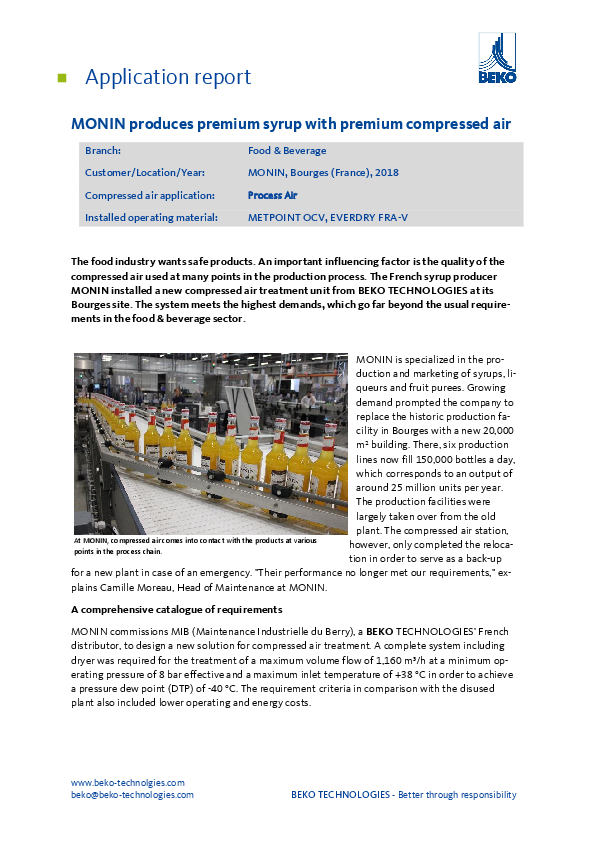
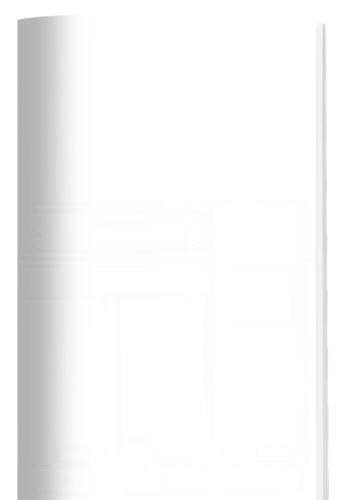