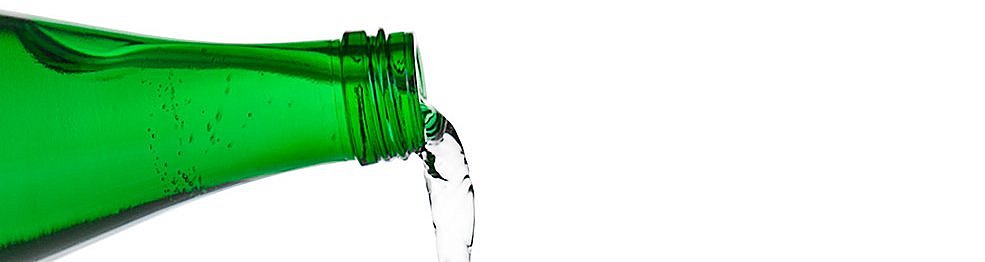
The key to perfect sparkling water: oil-free compressed air
Every hour, 150 cubic metres of purest mineral water is produced. Enough to fill 883 bathtubs every 60 minutes – or more than 207,000 bottles. To add sparkle to the water, there is only one solution: oil-free compressed air fed to state-of-the art bottling plants and peripheral systems. This company uses an innovative catalytic process for the total oxidation of hydrocarbons in the compressed air system.
The water is extracted from a huge natural reservoir located deep under a nature reserve.Of the 207,000 bottles, 72,000 are returnable glass bottles, 90,000 are returnable PET bottles and 45,000 are recyclable plastic bottles. In addition, the company sells its water in kegs to customers in the hospitality sector. The water is also used to produce fizzy drinks.They run a 24/6 plant and therefore need technology that guarantees 100% process safety. Oil-free compressed air is one of the key elements to ensure this.
Oil-free compressed air for sensitive applications
The bottling lines are supplied through two separate compressed air systems pressurised by two independent compressor stations. The conventional processing air system includes five screw compressors with capacities of between 90 and 120 kW. A frequency-controlled compressor provides the basic air flow, while the other units are automatically switched on and off as required.
The second, smaller system is pressurised by a 50kW oil-free compressor and supplies oil-free compressed air to dedicated consumption points. Compressed air of this high quality is required in sensitive sections of the bottling plant. Depending on the application, the oil-free compressed air needs to be sterile.
By running a single oil-free compressor, they have eliminated all unnecessary redundancy in this small compressed air system. In the event of a compressor failure the innovative catalysis technology provides them with a safety net.
In an emergency, the catalysis technology enables them to feed the oil-free compressed system from the five conventional screw compressors without any risk of oil contamination. This is achieved by means of a switchover unit installed between the two compressed air systems. This is made possible by the BEKOKAT solution. The BEKOKAT is a compact unit that removes hydrocarbons from the compressed air through total oxidation, breaking them up into carbon dioxide and water.
Turning hydrocarbons into water and air
BEKOKAT technology guarantees pure compressed air with a maximum residual oil content of 0.003 mg per cubic metre, which is close to the detection limit. The quality of compressed air treated in the BEKOKAT far exceeds that required for technical oil-free compressed air of purity class 1 according to DIN ISO 8573-1.
To achieve this, the hydrocarbons are eliminated through total oxidation in a separate process after compression. This means that the oil is removed from the compressed air in a single system component in a process that is not affected by the actual ambient conditions, the initial oil concentration or the relative humidity of the compressed air.
The BEKOKAT method removes all oil contained in the air – be it in gaseous, vapour or aerosol form – after compression. These substances contained in the air are converted in a catalytic process into carbon dioxide and water, which is drained from the system after condensation in the downstream cooling unit. The method is environmentally friendly, as the condensate does not contain any oil and can thus be safely disposed of through the sewerage system without any further treatment. The BEKOKAT system is the only one in the world that completely removes all oil from compressed air. The compressed air treated in the BEKOKAT thus meets the stringent requirements of the medical, pharmaceutical, food processing and packaging industries.
Another important issue are of course the running costs. There are huge differences regarding the efficiency of oil-free compressors on the one hand and conventional, oil-lubricated screw compressors with downstream BEKOKAT treatment on the other, which makes the latter a much more cost-efficient solution. When it comes to maintenance, the costs for systems that combine conventional compressors and BEKOKAT units are lower than those for oil-free converters.
Ideal for combination with refrigeration dryers
At the plant a system with oil-lubricated compressors and BEKOKAT units has been combined with DRYPOINT RA refrigeration dryers. These remove any residual moisture from the compressed air that has undergone total oxidation in the BEKOKAT. Given the relatively high temperature of compressed air produced in screw compressors, DRYPOINT RA refrigeration dryers are the perfect solution to cool down the air. The size and design of the heat exchangers promote effective cooling while minimising flow resistance.
"Every month, we produce around 1.3 million cubic metres of oil-free compressed air. By combining catalysis and dryer technology, we have achieved a process safety level that we could previously only dream of," explains the delighted customer, who follows this endorsement with a gulp from a freshly filled sparkling water bottle.