Pressure monitoring
Continuous pressure monitoring Early detection of faults Optimized use of energy
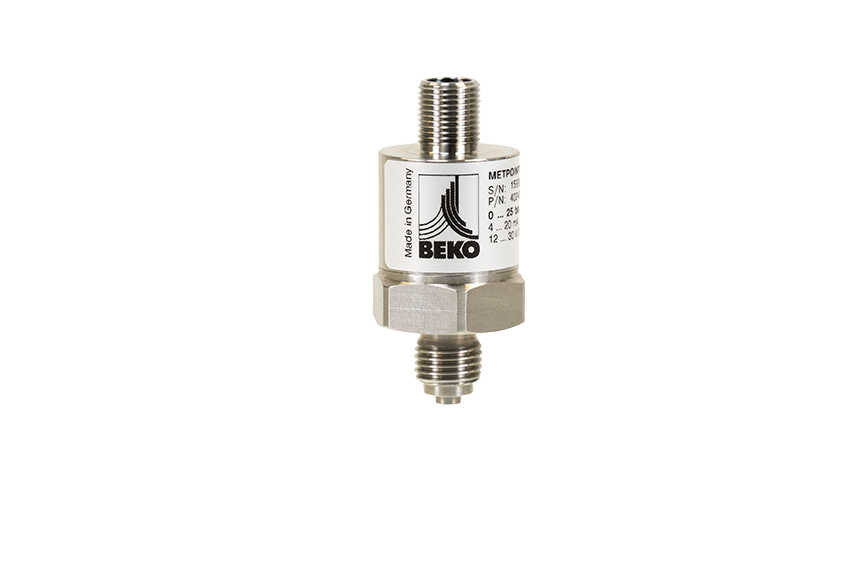
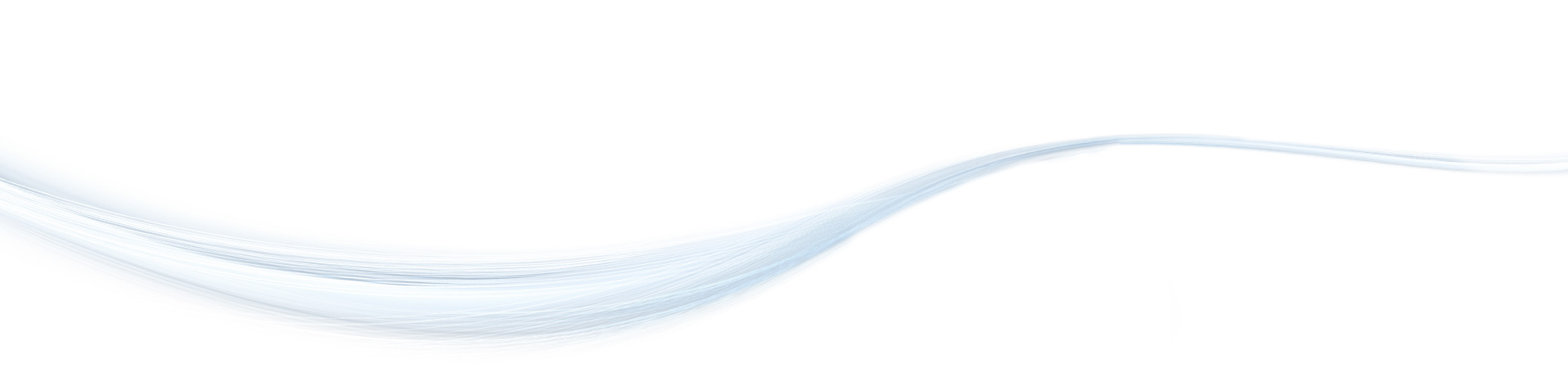
Precise control and monitoring
Accurate pressure measurement is crucial for the safe operation and efficiency of your compressed air systems:
Constant pressure control: Stable pressure is essential for the smooth operation of machines and systems. Deviations from the setpoint can impair performance and lead to malfunctions.
Preventing damage: Overpressure or underpressure can damage system components or shorten their service life. Accurate pressure measurement enables timely corrective measures and protects your systems.
Early fault detection: Pressure sensors help to detect irregularities at an early stage. They inform you immediately of potential problems before they lead to costly failures.
Reliable pressure monitoring therefore makes a significant contribution to the operational safety of your compressed air systems and ensures the continuity of your processes.
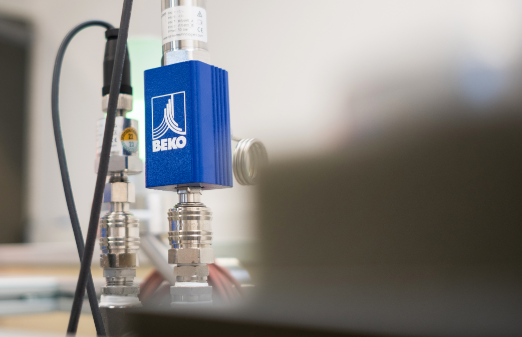
Measuring the pressure in a compressed air system, particularly in air treatment, is crucial for energy savings for several reasons:
Avoiding excessive pressure
- Operating at a higher-than-necessary pressure increases energy consumption. Every 1 bar increase in pressure can raise energy consumption by approximately 6-8%.
- Continuous pressure monitoring ensures that the system operates at the optimal pressure level, preventing unnecessary energy waste.
Detecting pressure losses and leaks
- Leaks are a major source of energy loss in compressed air systems, with up to 30% of generated air potentially being lost due to leaks.
- Regular pressure measurement helps identify unexpected pressure drops, allowing for targeted leak detection and repair.
Optimizing air treatment components
- Air dryers, filters, and separators can cause pressure drops within the system.
- Monitoring the pressure difference across these components helps determine when maintenance or filter replacement is needed, preventing unnecessary pressure losses.
Preventing unnecessary compressor operation
- Fluctuating pressure levels and uneven distribution can lead to additional compressors being activated unnecessarily.
- Proper pressure control ensures that only the required amount of compressed air is generated, improving overall system efficiency.
Extending equipment lifespan
- High pressures and excessive loads increase wear and tear on pipes, seals, and air-powered tools.
- A well-regulated pressure system reduces maintenance costs and extends the lifespan of the entire installation.
Overview of pressure sensors
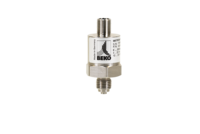
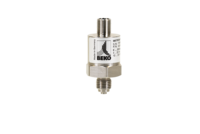
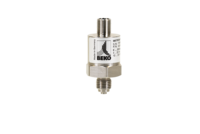
Downloads METPOINT® PRM
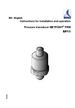
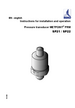
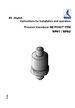
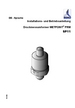
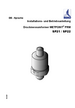
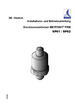
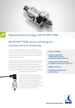
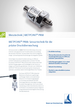