MONIN produces premium syrup with premium compressed air
Industry: | Food & Beverage |
Customer/Location/Year: | MONIN, Bourges (France), 2018 |
Use of compressed air: | Process Air |
Installed products: | METPOINT OCV, EVERDRY FRA-V |
The food industry wants safe products. An important influencing factor is the quality of the compressed air used at many points in the production process. The French syrup producer MONIN installed a new compressed air treatment unit from BEKO TECHNOLOGIES at its Bourges site. The system meets the highest demands, which go far beyond the usual requirements in the food & beverage sector.
MONIN is specialized in the production and marketing of syrups, liqueurs and fruit purees. Growing demand prompted the company to replace the historic production facility in Bourges with a new 20,000 m² building. There, six production lines now fill 150,000 bottles a day, which corresponds to an output of around 25 million units per year. The production facilities were largely taken over from the old plant. The compressed air station, however, only completed the relocation in order to serve as a back-up for a new plant in case of an emergency. "Their performance no longer met our requirements," explains Camille Moreau, Head of Maintenance at MONIN.
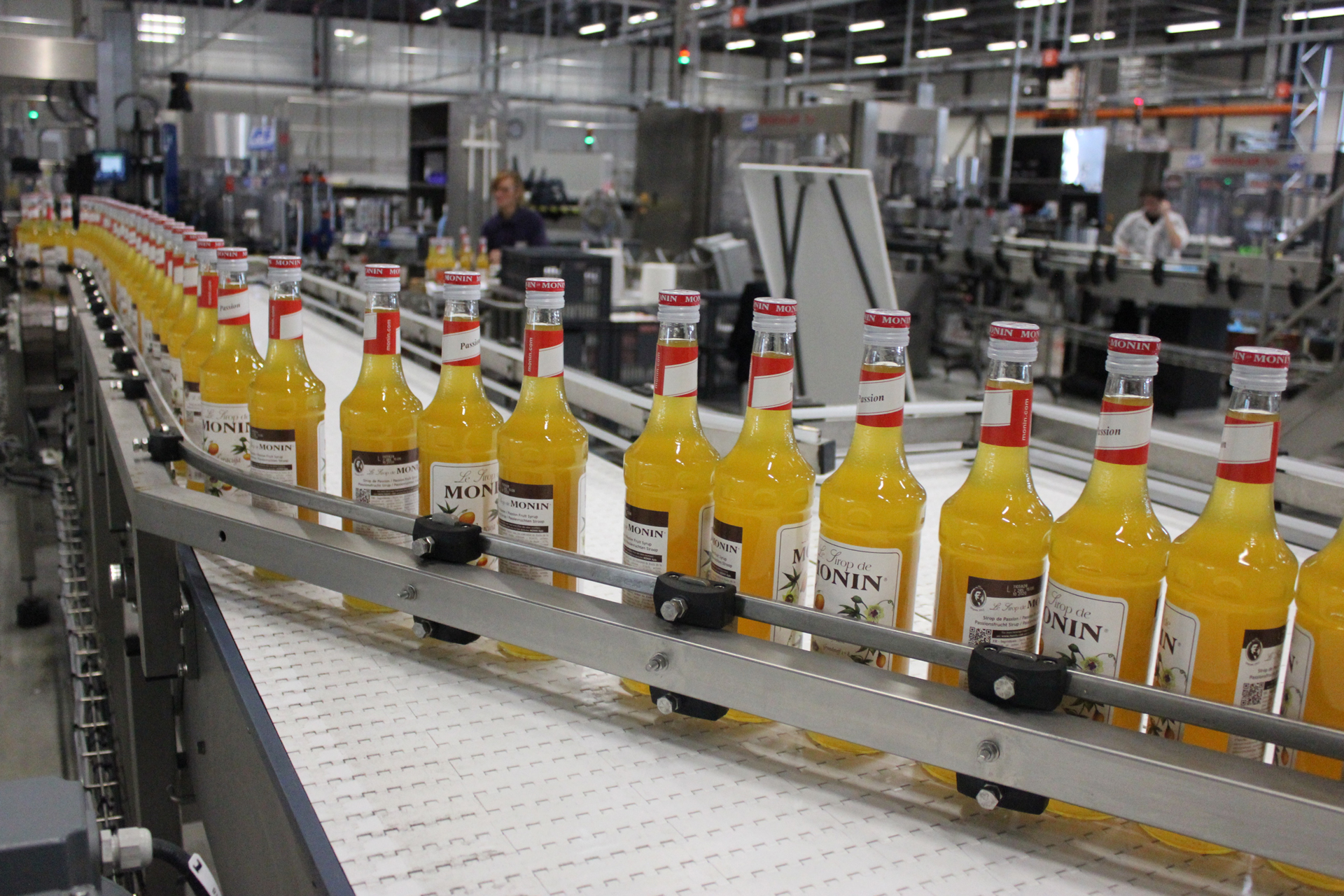
A comprehensive catalogue of requirements
MONIN commissions MIB (Maintenance Industrielle du Berry), a BEKO TECHNOLOGIES' French distributor, to design a new solution for compressed air treatment. A complete system including dryer was required for the treatment of a maximum volume flow of 1,160 m³/h at a minimum operating pressure of 8 bar effective and a maximum inlet temperature of +38 °C in order to achieve a pressure dew point (DTP) of -40 °C. The requirement criteria in comparison with the disused plant also included lower operating and energy costs.
In terms of food safety, compressed air of the highest quality was required, which was to be monitored and made traceable by measuring technology. In the food industry, compressed air comes into direct or indirect contact with products at various points in the process chain and should therefore be free of solids, oil, moisture and germs.
Clean compressed air made to measure
Following a thorough analysis on site, MIB and BEKO TECHNOLOGIES installed a tailor-made compressed air treatment system in 2018. The new station is composed of standard elements that are optimally matched to each other. An oil-free 110 kW compressor with variable speed and dry screw produces the compressed air. The heart of the BEKO TECHNOLOGIES treatment system is the heat regenerating adsorption dryer EVERDRY FRA-Vplus ZERO PURGE. In this model, desorption takes place in countercurrent to the adsorption direction with heated blower air and cooling in cocurrent flow. This ensures that there is no loss of compressed air for regeneration (ZERO PURGE).
A water separator is installed upstream of the dryer, an oil filtration system and a dust filter behind it filter out solid impurities. Several BEKOMAT condensate drains remove condensate from the compressed air system.
Measurement technology for controlled processes
The basis for important analyses and documentation is sensor technology for recording the current volume flow and compressed air consumption. The METPOINT FLM flow meter offers precise point-of-use monitoring. The METPOINT OCV monitoring system permanently monitors the residual oil vapour content in the compressed air network and achieves an accuracy of approximately one thousandth of a mg/m³. This ensures that the entire compressed air treatment chain does not allow any migration of hydrocarbons into the process. MONIN can thus permanently ensure the quality and purity of its process compressed air.
More food safety and less expenses
In the meantime, the new compressed air treatment plant has been in operation for more than two years. Camille Moreau is very satisfied with what has been achieved: "Volume flow, compressed air consumption, air quality - everything is under control and traceable. As soon as a critical threshold is exceeded, an alarm message is triggered”.
The information reaches the maintenance department in real time and corrective measures can be taken. By replacing the old dryer with a heat regenerating adsorption dryer EVERDRY from BEKO TECHNOLOGIES, MONIN saves more than 1 million m³ of compressed air per year, which corresponds to a monetary value of approximately 15,000 Euro. The quality of the compressed air even exceeds the criteria of class 1/2/1 according to the ISO standard 8573-1 and meets the strict requirements of the manufacturer
About MONIN
GEORGES MONIN SAS was founded in 1912 and is today a world leader in syrups and liqueurs. The portfolio of the French family-owned company with headquarters in Bourges also includes fruit mix drinks, sauces, frappés and smoothies. The products are mainly used in the gastronomy sector in the production of cocktails. MONIN employs almost 700 people and operates a total of five production sites in Europe, the USA and Asia. It is estimated that 8 million drinks are prepared daily with MONIN products. (www.monin.com)
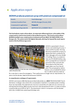