Safe oil-free compressed air for the pharmaceutical production
Industry: | Pharmaceutical industry |
Customer/Location/Year: | Nycomed, Singen (Germnany), 2011 |
Use of compressed air: | Control air, process air |
Installed products: | CLEARPOINT, BEKOKAT, BEKOMAT, ÖWAMAT |
For the production of medicaments, the strictest hygienic standards apply to the production conditions. This of course also applies to the required compressed air. It must be absolutely free from oil in order not to contaminate the sensitive products. In its factory in Singen, Germany, drug manufacturer Nycomed relies on a comprehensive system solution provided by BEKO to treat the process air in a reliably oil-free manner.
Most of us know at least one of Nycomed's products from childhood on: Sanostol, as a nutritional supplement, is an advertising icon from the 1970s and 1980s to the same extent as Buerlecithin, also produced by Nycomed, is for the older generation. To ensure that nothing makes you feel sick with anger in your professional life between these two periods, the portfolio of the international pharmaceutical company also includes numerous medical products, for example for stomach discomfort and diarrhoea. Further focal points of activities are medicaments for respiratory and cardiovascular diseases, pain therapy and osteoporosis.
In Germany, Nycomed GmbH operates from four locations. In Constance, research and development, marketing and distribution are bundled. Another location for further research activities is Hamburg. Production takes place in Oranienburg and Singen. While all kinds of solid forms of medicaments - meaning tablets, film capsules and capsules - are manufactured in Oranienburg, the activities in Singen focus on the sterile and non-sterile production of medicaments in bottles, ampoules, syringes or tubes.
Strict international production standards
Nycomed supplies medicaments which are only available on prescription to more than 100 countries worldwide. Therefore Nycomed, as a matter of course, is geared to meeting even the strictest international standards for pharmaceutical production. This applies to the production processes themselves as well as to supporting processes and the media supply. The specification for air for medical use concretely refers to the Pharmacopoea Europaea or to the United States Pharmacopeia (USP) and the National Formulary (NF) of the American Food & Drugs Administration (FDA), in accordance with which the production in Singen is certified. Expressed in the better-known ISO-8573 classification of compressed air quality, Nycomed defines class 1 as a requirement for the residual oil content, class 1 for particles and class 4 for the residual moisture content.
The Nycomed factory in Singen has two separate compressed-air systems with an operating pressure of 6 and 10 bar. The 6-bar system, which is fed by two compressed-air stations, supplies compressed air to the pharmaceutical production, the chemical production and the chemical pilot plant stations. There, the air serves as control air and as an energy carrier for the operation of pneumatic devices. In pharmaceutical production, the compressed air is used as a cleaner and dehumidifier for primary means of packaging such as ampoules, for the aeration of the sterilizer chambers and for product superposition in manufacturing. And it is exactly these processes where the extremely high demands on safety that Nycomed makes on the compressed-air supply. For the production, they need compressed air guaranteed free from oil, and this must be ensured 24 hours a day, seven days a week."
Two ways to achieve oil-free compressed air
To be able to reliably provide oil-free compressed air, Nycomed has chosen a dual strategy. In one of the two 6-bar stations, there are three oil-free compressors with a compressed-air output of 17.25 m³/min. in total. In contrast, Nycomed, together an external service provider, has realised a completely different concept in the second station. Here, two oil-lubricated screw compressors with a capacity of 15.6 m³/min generate the compressed air. To subsequently process the compressed air to the quality level required for pharmaceutical production, a system solution from BEKO TECHNOLOGIES is employed. The justification for this constellation is very simple: The operation of this station is more profitable as regards the generation costs and also the maintenance costs than the oil-free compressedair generation.
For the high demands on the compressed-air quality of the pharmaceutical company, processing is decisive in this station. The first separation of condensate from the compressed air is realised by CLEARPOINT cyclone separators which are installed downstream of the compressors.
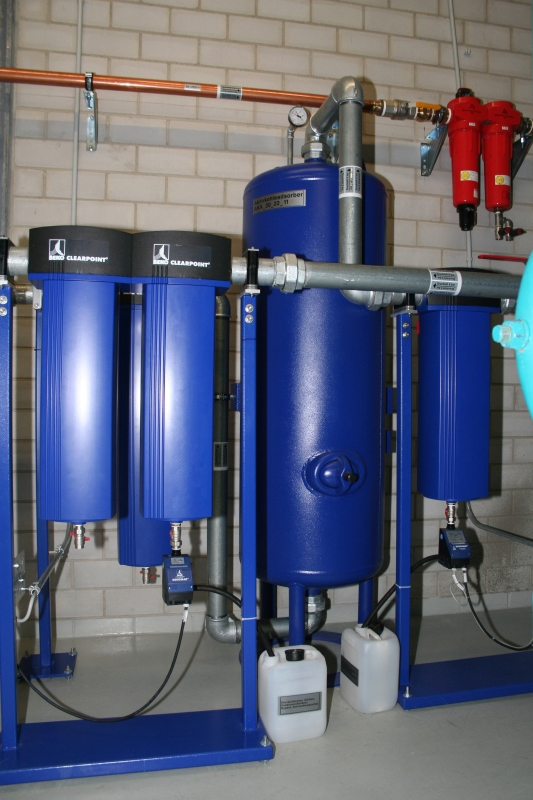
To be able to reliably guarantee the absence of oil in the generated compressed air, Nycomed in Singen relies on the BEKOKAT catalytic compressed-air processing from BEKO TECHNOLOGIES. Two systems, adjusted to the compressor performance for volume flows of 6 or 12 Nm³/h, are installed. Through the innovative catalysis method, the BEKOKAT systems fully split all hydrocarbons (these are, above all, the oil fractions in the condensate) contained in the compressed air into water and carbon dioxide. The result of the total oxidation in the BEKOKAT is oil-free compressed air with a quality better than ISO 8573-1 class 1, meaning a residual oil content of ≤ 0.01 mg/m³.
CLEARPOINT fine filters or ultrafilters made by BEKO with a separation degree of 0.1 µm and 0.01 µm respectively are installed downstream in the compressed-air line for the removal of particles. Air coolers by BEKO and downstream refrigeration dryers of the compressor manufacturer serve to cool down and dehumidify the compressed air, which is dehumidified to a pressure dew point of max. 5° C.
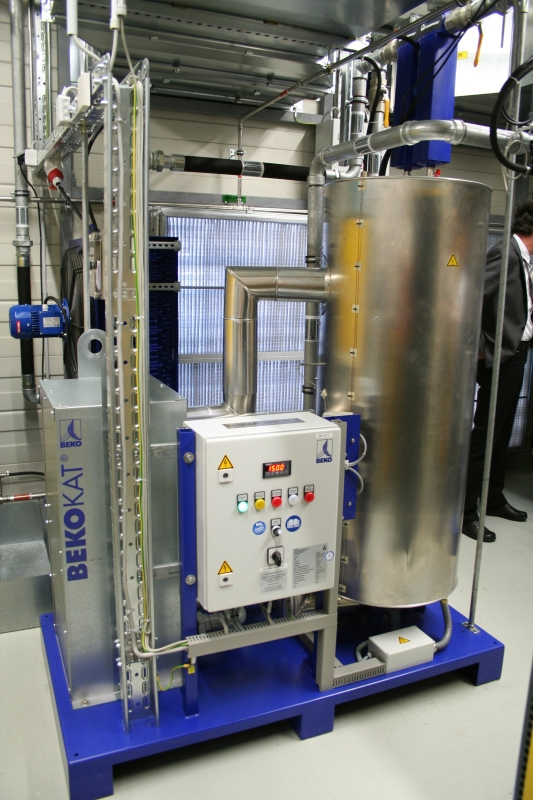
Additional firewall
An elaborated and stringently planned safety solution for the compressed-air processing, one could already say at this point, but for the safety requirements according to the specifications of the technical department this does not suffice: to be prepared for all contingencies and for maintenance periods, the station also accommodates an additional activated-carbon adsorber made by BEKO with a CLEARPOINT activated-carbon filter 0.01 µm in the bypass. This "police" filter represents an additional firewall to protect the production against oil introduction via the compressed air. A downstream calibrated pressure dew point and residual oil content measuring device in the compressed-air manifold continuously monitors the pressure dew point and the residual oil content. If limit values are exceeded, an alarm is signaled to the control room via the central building control systems. Only after this safety level is the compressed air supplied via pressure vessels to the distribution system for the compressed-air consumers.
Safety down to the last detail
But safety is not only observed with regard to the medium that comes out at the front side. Nycomed also relies on the technology made by BEKO, which has proven its worth many times in the field of condensate: BEKOMAT condensate drains are installed at all relevant points in the compressed-air processing and, via a manifold, supply the accumulated condensate to an oil-water separator of the ÖWAMAT 15 type. This way, Nycomed is on the safe side as far as the processing and disposal of compressor condensate is concerned because they reliably meet all environmental regulations. The planning and realization of the station was a joint project of Nycomed, an external service supplier and the BEKO TECHNOLOGIES project management team, which provided valuable support during the project planning. The on-site installation was implemented by Nycomed technicians, who not only joined the different components to form a system solution but who also scrupulously cleaned all pipes, fittings, valves etc. Because the best oil-free compressed-air supply is null and void when lubricated components re-contaminate the processed compressed air on its way. All things considered, the planning and realization effort was worth it because the plants function to Nycomed´s satisfaction and meet their high demands.
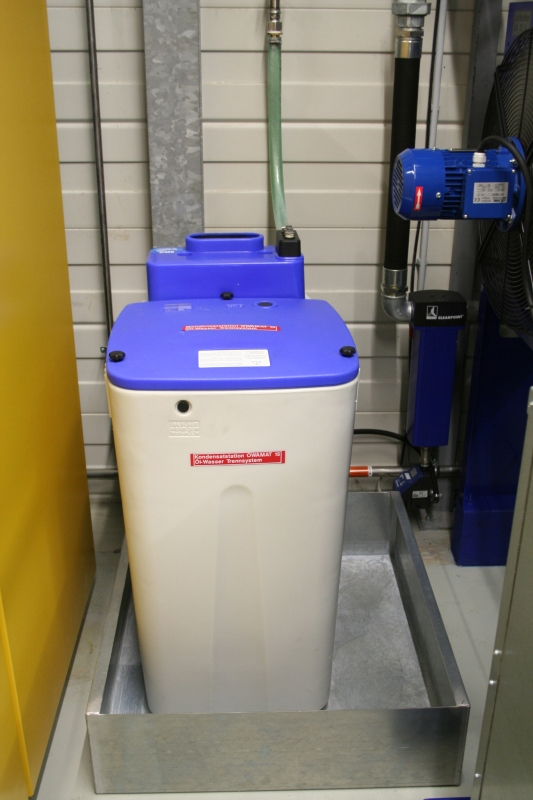
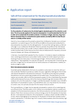