With compressed air to effective sealing foam
Industry: | Mechanical engineering |
Customer/Location/Year: | CeraCon, Würzburg (Germany), 2019 |
Use of compressed air: | Control air, process air |
Installed products: | DRYPOINT M plus |
When manufacturing sealing foams, a supply of high-quality compressed air is indispensable. A machine manufacturer from southern Germany shows how to set up efficient production.
Polyurethane foams (or PUR foams) have become indispensable in today's industry. They are used, for example, when sealing car door locks, headlights or fuse boxes. The engineering and mechanical engineering company CeraCon from Weikersheim, 40 km south of Würzburg, is a specialist in sealing technology. Its product portfolio includes foam metering systems (Sealing Systems) as well as automated industrial ovens (Thermal Systems), which are needed to cure the sealing foam.
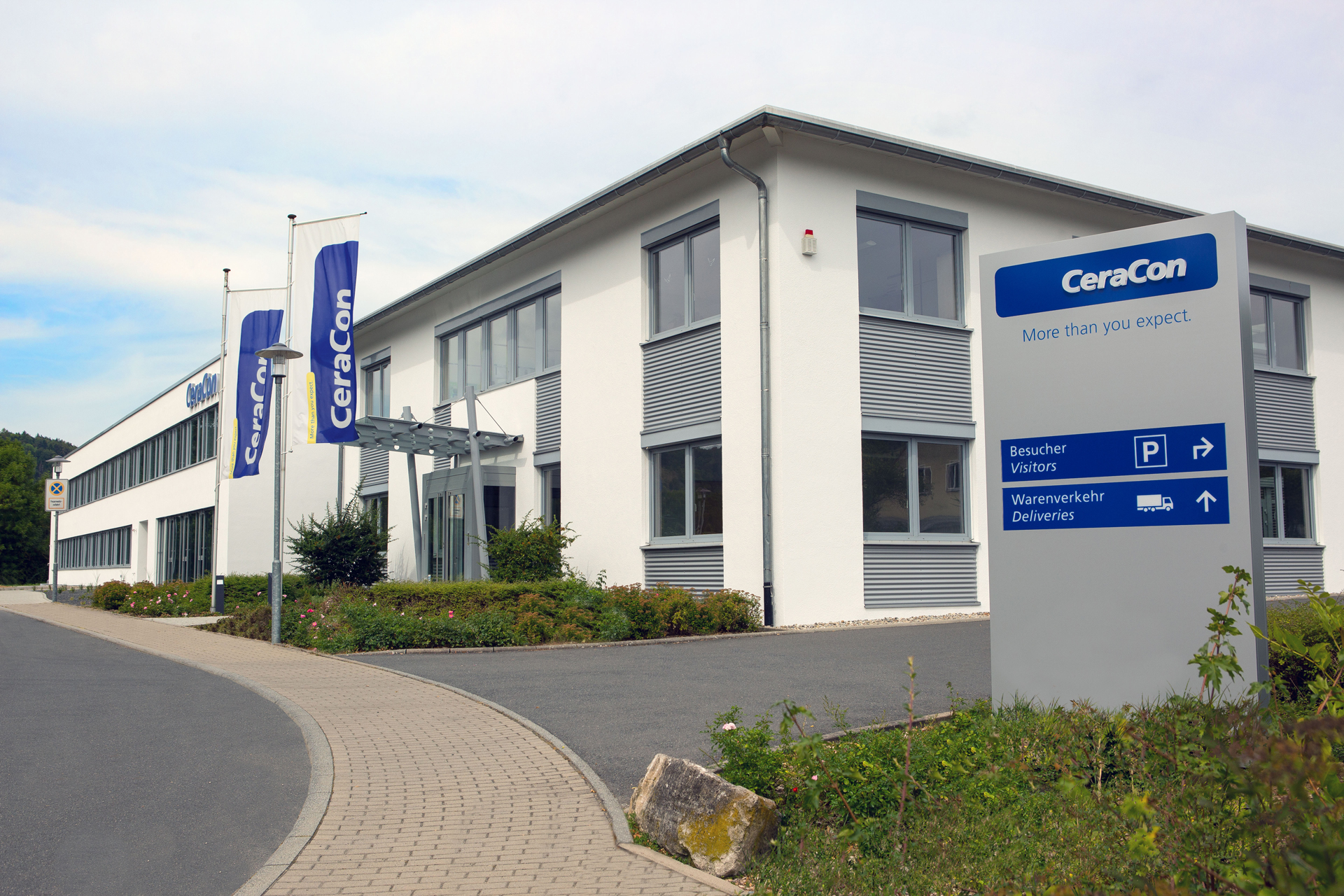
Reliable sealing technology due to single-component foam
CeraCon is particularly well known for its one-component PUR foams. To produce them, the fast-curing one-component elastomers are foamed purely mechanically with compressed air in the foam metering unit. This ensures a homogeneous and predominantly closed-cell foam structure. The sealing material is then precisely metered by a freely programmable robot arm and applied to the component as a foam bead (continuous line of sealing material). To cure the foam, the component then needs to be heat treated for a few minutes in a thermal system.
The foam bead gets its special impermeability from its predominantly closed-cell structure. "This is achieved by the physical foaming process using compressed air, which creates gas pores in the raw material," explains Dr. Frank Kukla, one of the three managing directors at CeraCon. He continues: "This structure makes the foam particularly tear-resistant and highly impermeable. Even if the outer skin of the foam bead is damaged during the installation of a component, reliable sealing performance continues to be provided."
Process requires dry, oil- and particle-free compressed air
The medium compressed air plays an important role in CeraCon's sealing foam technology. The amount of air introduced into the PUR material allows its softness to be regulated. This is particularly important because each application places different demands on the foam's degree of hardness. Since the quality of the compressed air used in the foaming process has an impact on the quality of the sealing medium, CeraCon prepares it. "For our application, we need dry, oil- and particle-free compressed air," explains Thomas Dierolf, application engineer at CeraCon. "If the compressed air contains too much moisture, it reacts with the PUR material. This results in a viscous medium and clogged nozzles." For reliable drying of the compressed air with integrated filtration, the company has been installing the DRYPOINT M Plus membrane dryer from the Neuss-based compressed air specialist BEKO TECHNOLOGIES GmbH in its foam metering systems as standard since the beginning of 2019.
Compressed air drying through partially permeable membrane
For a safe process, the dew point of the compressed air used for foaming must be below -20 °C. This is clearly exceeded by the DRYPOINT M Plus, which achieves a pressure dew point of up to -40 °C. The membrane dryer with integrated nanofilter also offers drying in a small space, since the compressed air filter and membrane dryer are installed in a single housing. At the same time, it requires neither electrical energy nor environmentally harmful desiccants. By using the membrane dryer, CeraCon ensures that the plants are always supplied with reliably dry compressed air - regardless of the climate zone in which they are located.
According to Udo Mueller, Head of OEM Sales at BEKO TECHNOLOGIES, compressed air is still an "energy form anyway" for companies - in other words, "it's there anyway, we don't have to worry about it anymore." However, Mueller clarifies that this is a misconception. "Safe industrial manufacturing processes require constantly available compressed air of stable quality, just like at CeraCon."
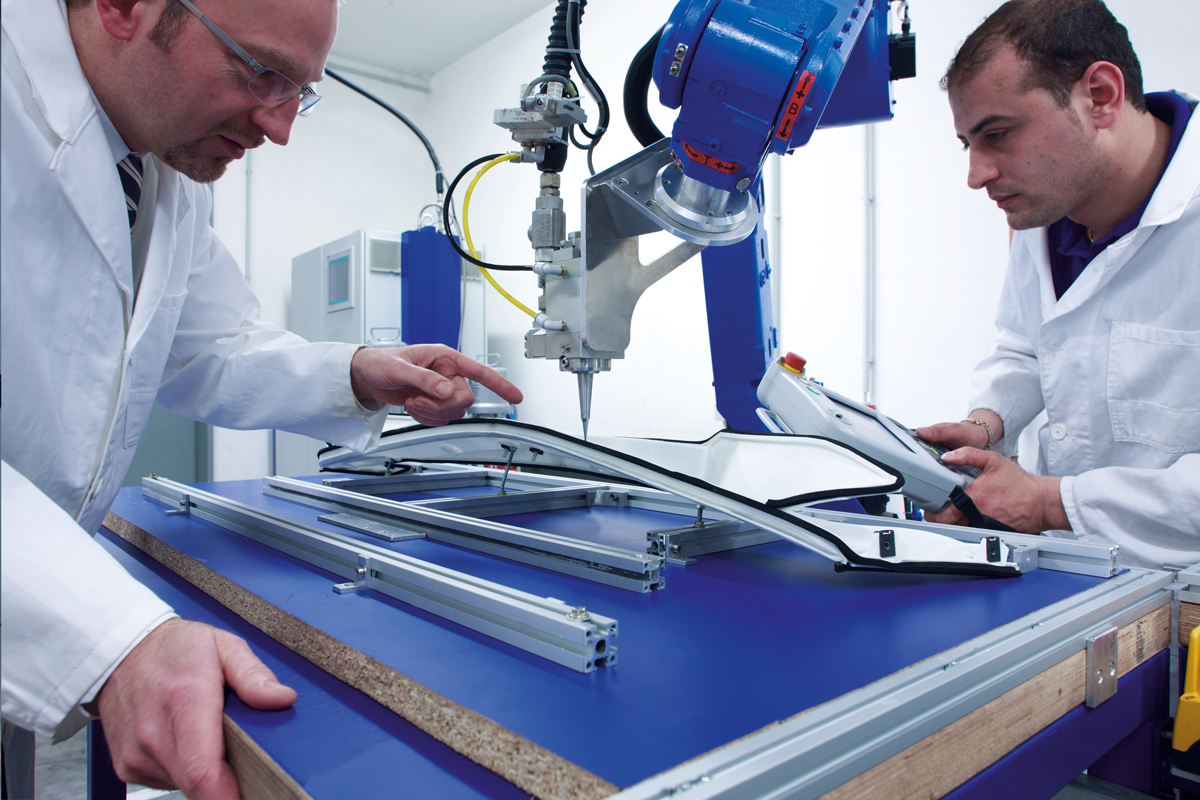
Membrane dryer in compact design
Even before the BEKO TECHNOLOGIES system, CeraCon used a membrane dryer in its foam proportioning systems. However, since the product required more maintenance and also had a much higher space requirement, the company decided to switch to the DRYPOINT M Plus in the middle of the start of the new series production. "The space requirement was a very important argument for us," says Dierolf. "Another advantage is that, unlike the dryer we used before, the DRYPOINT is one-piece and does not require an electrical connection. The compressed air filter and membrane dryer are installed in one housing. This makes maintenance easier, more convenient and less expensive for us." Mueller adds, "It also fits in better with the appearance of the CeraCon plant, which was recently redesigned by an industrial designer."
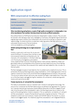