Refrigeración de cortadoras láser con aire comprimido
Sector: | Tecnología láser |
Cliente/lugar/año: | Horstmann, Verl (Alemania), 2008 |
Aplicación del aire comprimido: | Aire de proceso |
Productos instalados: | BEKOKAT |
El corte por láser es un proceso de separación térmica. No es algo perceptible hasta que el punto focal, donde el rayo láser incide sobre el material que se va a cortar. Ya en la trayectoria previa del rayo se genera calor, por eso es necesaria la refrigeración. El aire comprimido es el medio más usado para refrigerar este proceso y este aire debe estar totalmente libre de aceite.
En Horstmann GmbH & Co. KG, con sede en Verl junto a Gütersloh, se dedican al procesamiento complejo y de gran calidad de metales para clientes de renombres de numerosos sectores económicos, entre los que se encuentran la industria automovilística y la naval, así como la construcción de máquinas, instalaciones y herramientas.
Las cortadoras láser que funcionan incansablemente en Horstmann reaccionarían muy negativamente incluso a la mínima entrada de aceite a través del aire comprimido, pues se produciría una clara reducción de la potencia y la calidad ya que el cortante rayo láser se degradaría. Al contrario de lo que podría presumirse, el aire comprimido en las cortadoras láser de Horstmann no se usa para el sistema neumático, sino exclusivamente para refrigerar la trayectoria del rayo láser.
En principio, una cortadora con láser de CO2 se compone de una fuente de radiación láser y una óptica de enfoque móvil, generalmente un espejo hueco o una lente convexa. Desde la fuente, el rayo láser es llevado por espejos de desvío hasta la óptica de procesamiento. Allí, el rayo láser se enfoca y se genera la densidad de potencia necesaria para cortar. En Horstmann, donde se corta preferentemente chapa de acero inoxidable, se requiere una potencia de rayo de hasta 6 kW. Por lo demás, es suficiente para atravesar por completo y sin esfuerzo el cuerpo humano.
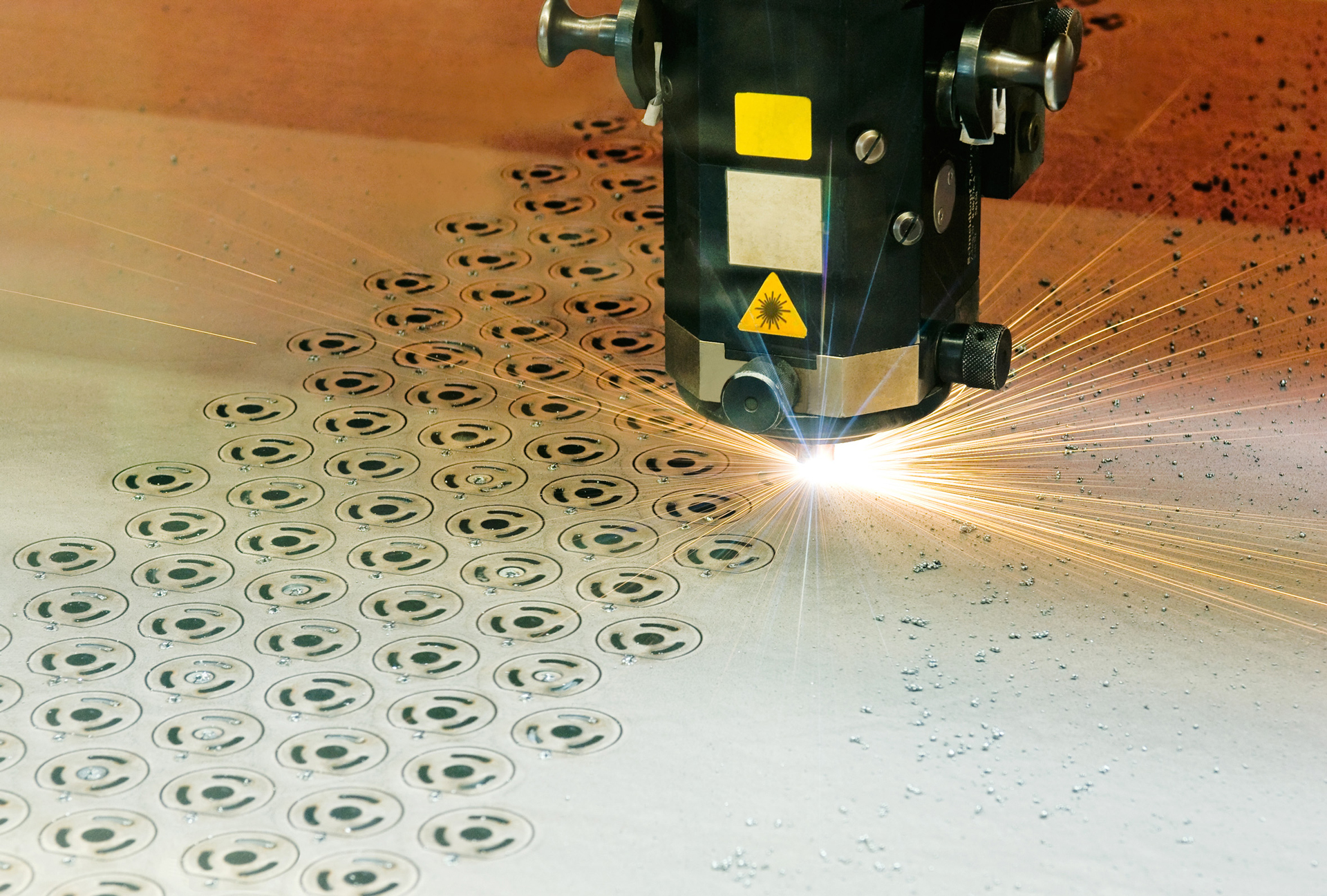
Al moverse el elemento óptico flotante sobre la chapa que se desea mecanizar, cambia constantemente su distancia respecto a la fuente de láser fija. En cualquier caso, el rayo láser generado no está suficientemente paralelo para transferirlo a través de las grandes distancias cambiantes. Por eso, y para reducir la carga térmica del espejo reflector, en parte se amplía con un espejo telescópico.
La auténtica guía del haz entre la fuente de láser y el elemento óptico de enfoque se realiza usando espejos revestidos de oro o molibdeno, que suenen estar hechos de cobre puro o de silicio monocristalino. Estos componentes reaccionan con la máxima sensibilidad al aceite o los aerosoles que se depositan sobre ellos.
En todo el recorrido del rayo láser se generan temperaturas considerables. Sin refrigeración, los materiales aquí empleados, como el espejo reflector o el fuelle del elemento óptico móvil, sufrirían daños considerables.
Esta función de refrigeración vital la realiza el aire comprimido insuflado en el recorrido del rayo. Debe estar seco y totalmente libre de aceite y partículas para no dispersar el rayo láser con partículas flotantes ni contaminar los espejos con depósitos. Incluso las mínimas proporciones de aceite o aerosol en el aire comprimido tendrían consecuencias fatales inmediatas para la seguridad del proceso y la rentabilidad de la instalación de corte. Por eso Heinrich Horstmann GmbH & Co. KG. dedica una enorme atención al tema del tratamiento del aire comprimido.
Hasta ahora, en Horstmann trataba de producir aire comprimido libre de aceite mediante técnicas relativamente costosas basadas en compresores, filtros y secadores acoplados entre sí. Sin embargo con este sistema se consigue una calidad poco fiable.
En Horstmann tampoco lograban encontrar una solución realmente satisfactoria, sobre todo tras la adquisición de nuevos equipos de corte aún más potentes. A comienzos de 2008 descubrieron un proceso de catálisis diseñado por el especialista alemán en aire comprimido BEKO TECHNOLOGIES GmbH para la producción de aire comprimido totalmente libre de aceite. El proceso, denominado BEKOKAT, abre el camino para el aire comprimido totalmente libre de aceite con un enfoque tecnológico completamente distinto a todas las soluciones anteriores: con catálisis.
Oxidación total de los hidrocarburos
En principio, el sistema BEKOKAT realiza una oxidación total de los hidrocarburos y consigue con ello un aire comprimido totalmente libre de aceite. Con ello, toda la eliminación del aceite del aire comprimido se realiza en un único componente de la instalación. Este funciona con independencia de las condiciones ambientales, de la concentración de entrada del aceite y de la humedad relativa del aire comprimido.
BEKOKAT elimina las impurezas en el aire comprimido provenientes de lubricantes sea que se presenten tanto en forma gaseosa como de vapor y aerosol. El proceso de BEKOKAT transforma totalmente estos componentes del aire en dióxido de carbono y agua.
El agua resultante se puede eliminar directamente por la red de aguas residuales, sin ninguna otra medida de protección ambiental. Incluso el condensado generado durante el enfriamiento del aire comprimido está libre de aceite, gracias al proceso de catálisis, y se puede introducir en la canalización sin tratamiento. Esta oxidación total y este procedimiento totalmente libre de residuos no son posibles actualmente con ningún otro proceso.
Como catalizador se usa un granulado en el BEKOKAT, que mediante elementos calefactores se calienta hasta una temperatura de funcionamiento de unos 150 grados centígrados. En el catalizador, las moléculas de aceite se rompen hasta que solo queda un átomo de carbono. En la fase final de la catálisis, las moléculas de aceite se oxidan formando H2O y CO2.
Lo esencial es que las cadenas de hidrocarburos, es decir, las moléculas de aceite, se puedan romper en cualquier punto que se desee. Se siguen rompiendo hasta que solo queda dióxido de carbono e hidrógeno. Por tanto, las cadenas de hidrocarburos, de distinta longitud, procedentes de compresores libres de aceite y lubricados por aceite no suponen ningún tipo de problema para BEKOKAT.
En el siguiente proceso de BEKOKAT, el aire comprimido limpio se enfría en un intercambiador de calor a unos 10 a 15 grados centígrados en la entrada y está disponible para la aplicación correspondiente.
Con el proceso BEKOKAT, por primera vez es posible conseguir un aire comprimido totalmente libre de aceite con un contenido de aceite residual máximo de apenas 0,003 miligramos por metro cúbico de aire comprimido. Una calidad necesaria en los muy exigentes sectores de la medicina y la farmacia, así como en el procesamiento y envasado de alimentos.
En definitiva, la enorme vida útil del granulado especial de BEKOKAT también es extremadamente rentable, dado que solo es necesario cambiarlo después de 20 000 horas de servicio.
Desde el principio del verano de 2008, el sistema BEKOKAT está funcionando permanentemente sin incidentes en la empresa metalúrgica Horstmann. Y Horstmann GmbH & Col. KG, además, tiene una gran conciencia ambiental porque desde que usa BEKOKAT, el agua condensada procedente de la instalación de aire comprimido se puede verter sin problemas y sin costosos tratamientos, directamente al alcantarillado.
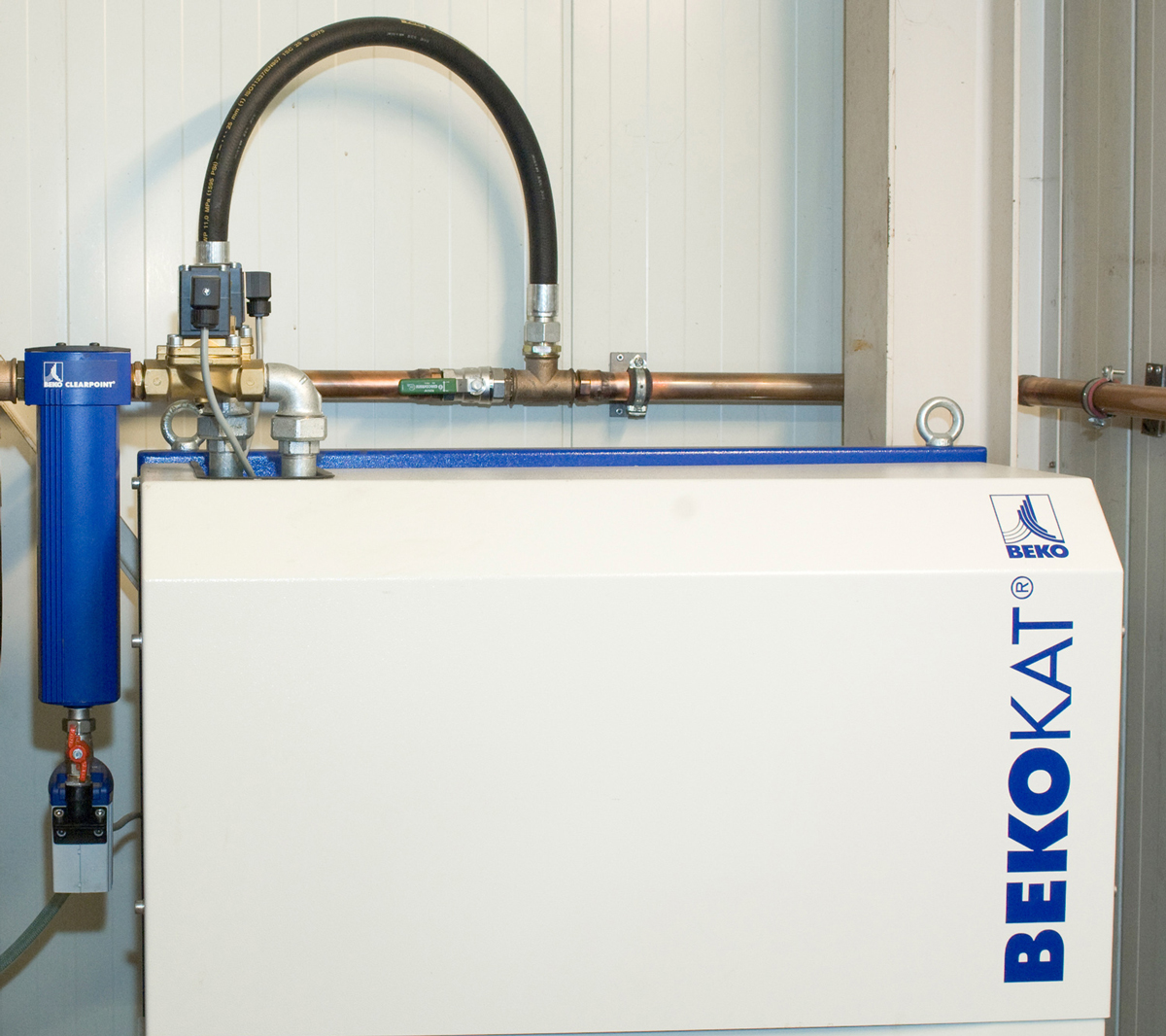
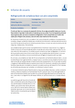