Técnica de aire comprimido en la industria de embalaje
Sector: | Embalaje, papel |
Cliente/lugar/año: | Delkeskamp, Nortrup (Alemania), 2008 |
Aplicación del aire comprimido: | Aire de control, aire de proceso, técnica de condensados |
Productos instalados: | EVERDRY, BEKOSPLIT |
Más de 100 fábricas especializadas en el sector con unos 19 000 trabajadores fabrican y procesan cartón ondulado en Alemania. El aire comprimido y especialmente su tratamiento tiene una importancia central en el proceso de producción ya que la humedad en el aire comprimido tendría consecuencias fatales para instalaciones, materiales en bruto y productos elaborados.
Con una producción anual de casi nueve mi millones de metros cuadrados de cartón ondulado, Alemania ocupa el primer puesto en Europa y el cuarto en la comparación internacional, por detrás de EE. UU., China y Japón. Casi tres cuartas partes de todas las mercancías transportadas en Alemania se embalan en cartón ondulado y casi el 30 % de todos los envases de cartón ondulado llenos cruzan las fronteras del país en su camino hacia el consumidor. Un gran negocio que es de especial importancia para toda la economía nacional alemana.
Uno de los pioneros, precursores y proveedor de servicios de este sector industrial es Delkeskamp Verpackungswerke GmbH en la localidad de Nortrup, en Baja Sajonia. Fundada en 1896 como fábrica de cajas de cartón, además de en la central de Nortrup, hoy fabrica en otros centros de producción en Hanóver y en la localidad checa de Odry. Fabrica papel, cartón ondulado y espuma para embalajes de muchos tipos.
Circuito de producción cerrado
El material preciso para la fabricación del cartón ondulado es el papel. Delkeskamp GmbH fabrica la amplia mayoría del soporte de papel que necesita en la planta de Nortrup. Esta sede es el primer eslabón de un circuito de producción cerrado y, por tanto, decisiva para la funcionalidad y rentabilidad de toda la estructura de producción de Delkeskamp. Además de las ventajas puramente técnicas de producción, la generación de energía del soporte de papel para el cartón ondulado de la empresa asegura una independencia total del mercado de abastecimiento.
En Delkeskamp disfrutan de su independencia. Así, en Nortrup se genera incluso el vapor necesario para la producción de papel, en una central eléctrica propia que usa modernas turbinas de gas. En este proceso se produce una cantidad de electricidad que supera claramente la demanda propia y se transfiere a la red pública. De este modo, no solo se autoabastece, sino que además es un proveedor de energía reconocido en Baja Sajonia.
El aire comprimido es un soporte de energía decisivo
En Nortrup se suministra aire comprimido a cuatro sectores: la fábrica de papel, la producción de cartón ondulado, la planta de espuma y, con una demanda muy inferior, a la central eléctrica propia.
Sin aire comprimido, en Delkeskap no se movería prácticamente nada. Para entenderlo, solo hay que imaginarse los procesos de producción esbozados en las tres áreas de producción: El soporte de papel para cartón ondulado producido en un primer paso a partir de papel usado en las enormes y modernas instalaciones de producción se calienta y humidifica en la primera fase de la producción del papel. Con ello alcanza la elasticidad necesaria para moldearlo. En el siguiente paso, el papel se pasa entre dos cilindros estriados que engranan entre sí como ruedas dentadas, aplicando presión y calor. Primero, el papel así ondulado se pega con la cinta interior del papel desde arriba y, después, con la cinta exterior desde abajo, con lo que el cartón ondulado puede desplegar su óptimo efecto protector.
En operaciones totalmente automatizadas, los formatos de cartón ondulado se transforman después en cajas plegadas, embalajes troquelados, embalajes interiores acolchados y expositores. Todo esto se mueve o controla mediante incontables equipos neumáticos y usando reguladores y válvulas correderas accionadas por aire comprimido. Si el proceso de detiene en algún lugar de esta secuencia de producción ajustada con precisión, la cuota de producción y, sobre todo, la calidad de la fabricación sufre las consecuencias inmediatamente.
Lo más importante: aire comprimido seco
Además de la continuidad del suministro, lo que Delkeskamp necesita ante todo es aire comprimido seco. La entrada de humedad en el aire comprimido es puro veneno para las instalaciones neumáticas y para los productos.
En el tercer área de producción de Delkeskamp, la producción de espuma, la sequedad también es imprescindible. Aquí se producen piezas moldeadas de poliestireno expandido (EPS) diseñadas individualmente para distintos embalajes. Lo que normalmente se conoce con el nombre de poliestireno, en Delkeskamp se denomina Denopor y completa el perfecto concepto de embalaje del fabricante.
El aire comprimido es necesario en esta parte de la empresa, entre otras cosas para el funcionamiento de las moldeadoras automáticas, el movimiento de los cilindros de ajuste y el funcionamiento de las válvulas. A esto hay que añadir la extracción por soplado de las piezas fabricadas de las máquinas. Las piezas de Denopor se extraen de la moldeadora usando aire comprimido y se almacenan en una sala sin calefacción, por lo que deben estar absolutamente secas ya que este material reacciona con gran sensibilidad a temperaturas bajo cero. Naturalmente, la humedad incrementa esta sensibilidad.
Por eso, para Delkeskamp Verpakungswerke GmbH, la sequedad es una de sus principales prioridades en el suministro de aire comprimido. También lo es en la necesaria ampliación de la instalación de aire comprimido en la central de Nortrup. Desde 2007, aquí se han producido considerables expansiones e inversiones en la ampliación y modernización de la producción.
Mayor demanda de aire comprimido tras la ampliación de la planta
La estación de aire comprimido anterior no lograba mantener el ritmo de rendimiento que requería el crecimiento de la empresa. Los cinco compresores allí instalados y el secador de adsorción urgentemente un refuerzo. Además, el separador estático de aceite-agua, llevaba tiempo sin funcionar como era deseable en Delkeskamp.
La búsqueda de la solución más moderna para este problema tras un intensivo análisis de mercado llevó a Delkeskamp a solicitar ayuda a un interlocutor totalmente nuevo para ellos: BEKO TECHNOLOGIES GmbH.
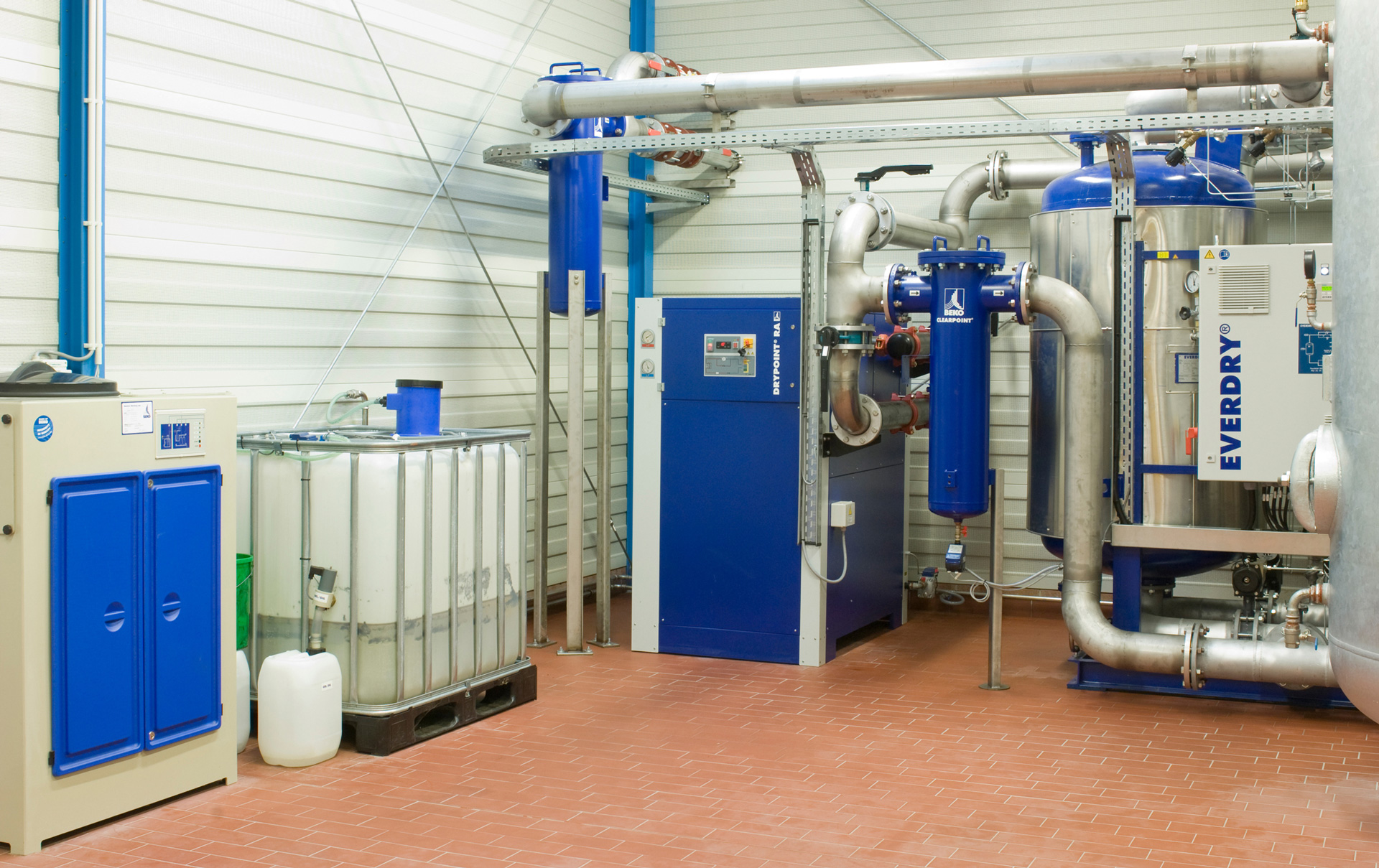
Esta empresa con sede en la localidad renana de Neuss y con actividad en todo el mundo, cuenta con una tecnología para separar emulsiones de agua y aceite: BEKOSPLIT. Estos separadores limpian condensados emulsionados como los que aparecen en condiciones de partida adversas o con determinadas combinaciones de lubricante-compresor. Además de condensado de aire comprimido, también se pueden tratar aguas residuales industriales que contengan aceite. Las impurezas orgánicas no solubles en agua, como aceites, grasas vegetales o animales y una gran cantidad de impurezas sólidas, se eliminan del agua. Además, se adsorben de manera fiable los posibles metales pesados, suciedad y partículas de pintura.
En este sentido, el principio BEKOSPLIT funciona con más efectividad que una ultrafiltración: No se necesitan limpiadores agresivos y se consume menos energía. La necesidad de inversión es extremadamente manejable y, además, los intervalos de mantenimiento más largos aumentan su rentabilidad.
Un sistema que merece la pena
En Delkeskamp pronto descubrieron que habían encontrado en BEKO TECHNOLOGIES que podía ayudarles a mejorar su instalación en muchos otros aspectos.
En BEKO TECHNOLOGIES empezaron a reflexionar sobre el tema del secado de aire comprimido, tan delicado para Delkeskamp. En pocos días desarrolló para Delkeskamp un concepto convincente para un sistema combinado de estructura redundante compuesto por secador de adsorción y frigorífico. Este sistema se hizo realidad en mayo de 2008.
Permite al fabricante de embalajes operar con la opción de secadores más segura y económica en función de la demanda y las condiciones ambientales, por ejemplo, estacionales. Tanto en forma de combinación flexible de ambos procesos como exclusivamente mediante un secado de adsorción o frigorífico.
Dado que las tuberías del sistema de aire comprimido dentro del recinto de la planta discurren sobre puentes de tuberías, principalmente por el exterior, están sometidas a grandes oscilaciones estacionales de temperatura. De modo que como protección contra la condensación en invierno debe haber un punto de rocío a presión mejor de - 40 °C.
Para conseguir la máxima seguridad de procesos, los secadores de adsorción EVERDRY instalados por BEKO TECHNOLOGIES están equipados con unidades adecuadas de control y medición del punto de rocío. Hasta la fecha, funciona a la perfección. La potencia del secador es totalmente estable y el balance energético ha mejorado sensiblemente.
Ahora, la nueva estación de aire comprimido de Delkeskamp emplea exclusivamente equipos de BEKO TECHNOLOGIES.
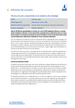