Refroidissement par air comprimé de machines de découpe au laser
Secteur d'activité : | Technologie laser |
Client / lieu / année : | Horstmann, Verl (Allemagne), 2008 |
Utilisation de l'air comprimé : | Air de processus |
Produits installés : | BEKOKAT |
La découpe au laser fait partie des procédés de séparation thermiques. Ceci n'est pas manifeste seulement au point de focalisation, où le rayon laser rencontre le matériau à découper. Déjà sur le trajet du rayon laser, il fait vite chaud. Il faut un refroidissement. Le meilleur et le plus économique est effectué avec de l'air comprimé. Celui-ci doit être absolument exempt d'huile.
Dans l'entreprise Horstmann GmbH & Co. KG, dont le siège est à Verl près de Gütersloh, on se consacre à la transformation exigeante et de haute qualité du métal pour des clients renommés dans de nombreux secteurs économiques, dont l'industrie automobile et la construction navale, ainsi que la construction de machines, d'installations et d'outils.
Les machines de découpe au laser qui travaillent infatigablement chez Horstmann réagiraient de manière très fortement allergique à la moindre contamination par de l'huile dans l'air comprimé. Et ce par une nette baisse des performances et de la qualité. Parce que leur rayon laser coupant comme un couteau serait dégradé littéralement en une "lampe à huile" vacillant mollement. Contrairement à ce que l'on pourrait penser, l'air comprimé sur les machines de découpe au laser chez Horstmann n'est pas utilisé pour les systèmes pneumatiques, mais exclusivement pour le refroidissement du trajet du rayon laser.
En principe, une installation de découpe au laser CO2 comporte un source de rayon laser et une optique de focalisation mobile, souvent un miroir concave ou une lentille convergente. À partir de la source, le rayon laser est dirigé vers l'optique de traitement par des miroirs de renvoi. Là, le rayon laser est focalisé pour atteindre la densité de puissance nécessaire à la découpe. Chez Horstmann, où l'on découpe surtout des tôles d'acier inoxydable, il est question d'une puissance de rayon jusqu'à six kW. Suffisante d'ailleurs pour traverser un corps humain sans efforts.
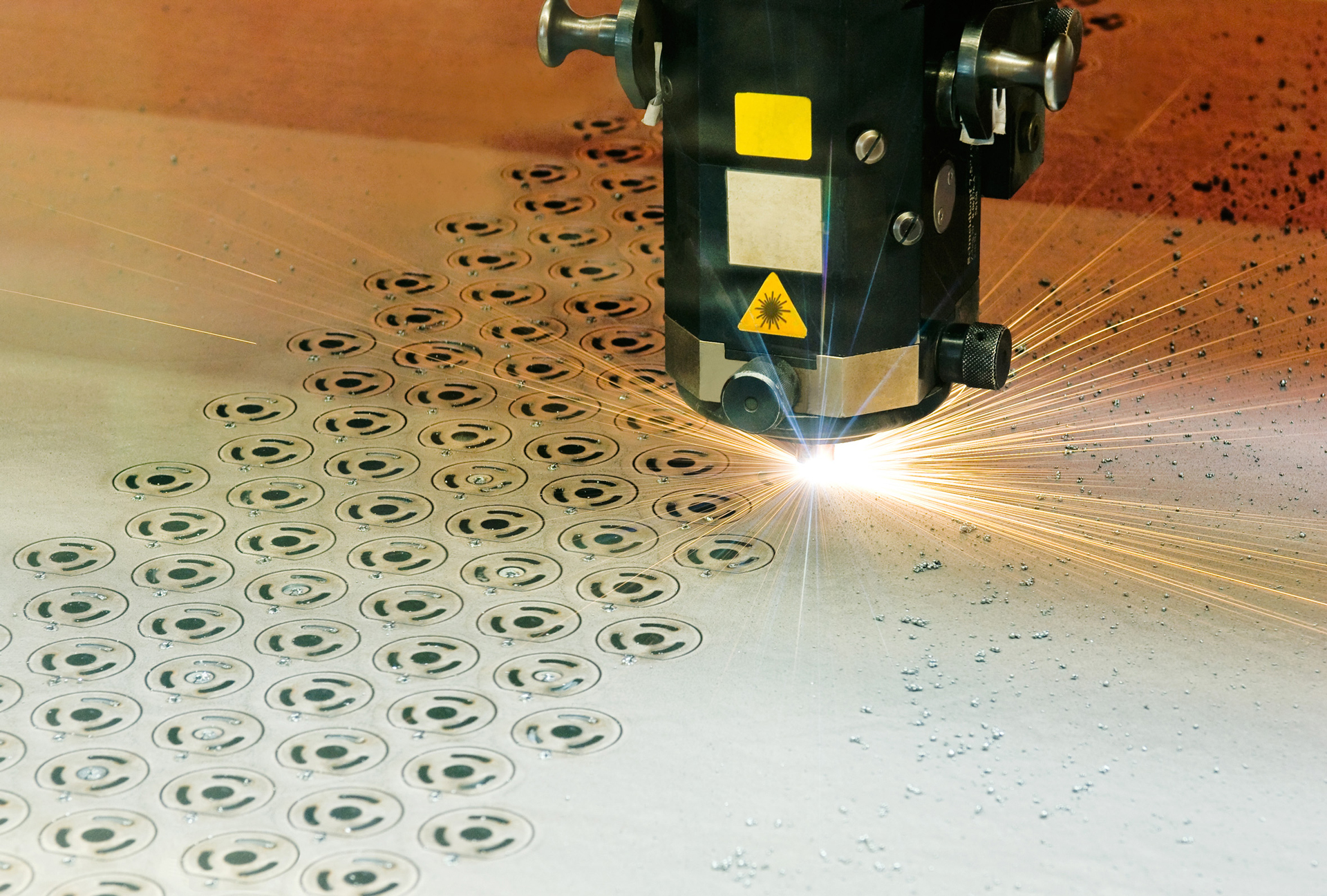
Étant donné que l'optique mobile „volante“ se déplace au-dessus de la tôle à traiter, la distance entre elle et la source laser fixe change constamment. Il est vrai que le rayon laser produit n'a pas le parallélisme nécessaire pour le transmettre à des distances parfois importantes et changeantes. C'est pour cela, et aussi pour réduire la charge thermique sur les miroirs de renvoi, qu'il est parfois complété par un télescope à miroir.
Le guidage du rayon proprement dit entre la source laser et l'optique de focalisation est effectué via des miroirs recouverts d'or et de molybdène, fabriqués soit en cuivre pur soit en silicium mono-cristallin. Et ces miroirs réagissent en plus de manière très sensible à l'huile et aux aérosols qui se déposent sur eux et rendent nécessaire un remplacement précoce et extrêmement couteux.
Sur tout le trajet du rayon du laser, des températures considérables se développent naturellement. Sans refroidissement, les matières utilisées ici, comme par exemple le miroir de renvoi et plus rapidement le soufflet de l'unité optique mobile, seraient fortement endommagées.
L'air comprimé soufflé dans le trajet du rayon prend en charge cette fonction vitale de refroidissement. Il doit être absolument exempt de particules et d'huile et sec pour éviter de "disperser" le rayon laser avec des particules en suspension et de salir les miroirs de renvoi avec des dépôts. Même les plus infimes parties d'huile ou d'aérosol dans l'air comprimé auraient des conséquences fatales pour la sécurité du processus et la rentabilité de l'installation de découpe.
Cependant les deux facteurs, liés à une qualité de produit absolue, sont des éléments essentiels pour le succès commercial durable de l'entreprise Heinrich Horstmann GmbH & Co. KG. C'est pourquoi on accorde une attention considérable au sujet du traitement de l'air comprimé.
Jusqu'ici, on essayait chez Horstmann (comme d'ailleurs chez presque tous les utilisateurs d'air comprimé avec des exigences similaires) de produire de l'air comprimé sans huile avec des techniques relativement complexes basées sur des compresseurs, des filtres et des sécheurs, souvent même reliées ensemble. Cela fonctionne souvent, toutefois avec une fiabilité plus ou moins grande.
Même chez Horstmann, on n'a jamais trouvé de solution vraiment satisfaisante, surtout après l'acquisition de nouvelles machines de découpe encore plus performantes. Au début de 2008, un processus de catalyse développé par le spécialiste allemand de l'air comprimé BEKO TECHNOLOGIES GmbH pour la production d'air comprimé totalement exempt d'huile a été découvert. Le processus appelé BEKOKAT ouvre la voie vers l'air comprimé totalement exempt d'huile avec une approche technologique totalement différente des solutions existantes : avec la catalyse.
Oxydation totale des hydrocarbures
Dans le principe, le système BEKOKAT réalise une oxydation totale d'hydrocarbures et ainsi un air comprimé totalement exempt d'huile. Et ce dans une étape de processus complète et concentrée après la compression. De cette manière, le déshuilage complet de l'air comprimé est effectué dans un seul composant de l'installation. Celui-ci fonctionne indépendamment des conditions environnementales, de la concentration d'huile à l'entrée et de l'humidité relative de l'air comprimé.
BEKOKAT traite toutes les impuretés dans l'air comprimé acheminé par le compresseur. Ce sont communément les huiles de lubrification, le dioxyde de soufre, le monoxyde de carbone, les gaz d'azote etc. Ils sont présent aussi bien sous forme gazeuse que sous forme de vapeurs et d'aérosols. Le processus BEKOKAT transforme de telles particules en suspension dans l'air entièrement en dioxyde de carbone et en eau.
Cette dernière peut être dirigée sans hésitations et sans autres mesures de protection de l'environnement dans le réseau des eaux usées. Même le condensat formé par le refroidissement de l'air comprimé est totalement exempt d'huile grâce au processus de catalyse, et il peut également être évacué sans traitement dans la canalisation. Actuellement, aucun autre processus ne réalise cette oxydation totale et absolument sans résidus.
Le BEKOKAT utilise comme catalyseur un granulé chauffé à une température d'exploitation d'environ 150 °C par des éléments chauffants. Dans le catalyseur, les molécules d'huiles sont brisées jusqu'à ce qu'il ne reste qu'un atome de carbone. Dans la phase finale de la catalyse, les molécules d'huile sont oxydées jusqu'à obtenir de l'H2O et du CO2.
Il est essentiel que les chaînes hydrocarbonées, donc les molécules d'huile, puissent être "cassées" à n'importe quel endroit. Elles sont brisées jusqu'à ce qu'il ne reste que du dioxyde de carbone et de l'hydrogène. Les chaînes hydrocarbonées de longueurs différentes sortant des compresseurs sans huile et lubrifiés par huile ne présentent donc aucun problème pour le BEKOKAT.
On ne sait pas toujours non plus que les filtres à charbon actif, souvent utilisés en alternative, ne peuvent pas adsorber les liaisons polaires comme l'oléfine, les alcools, glycols ou cétones. Le système BEKOKAT élimine par contre intégralement toutes les substances de l'air comprimé. Dans la suite du processus BEKOKAT, l'air comprimé épuré est refroidi dans un échangeur de chaleur à 10 à 15 °C à l'admission et il reste disponible pour l'application respective.
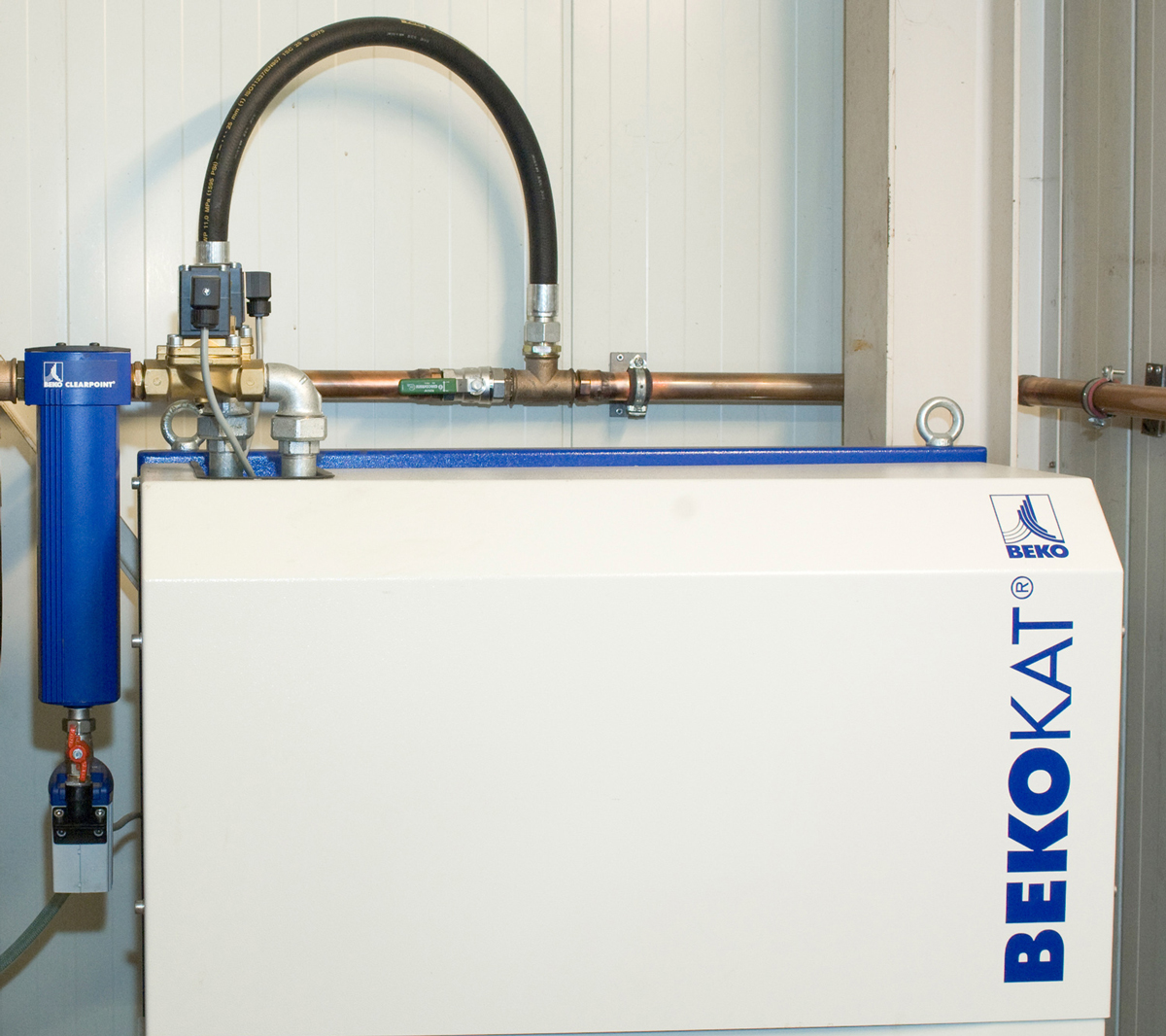
Avec le processus
BEKOKAT, il est possible pour la première fois d'obtenir de l'air comprimé absolument sans huile de manière constante, avec une teneur maximale résiduelle en huile à peine mesurable de 0,003 milligramme par mètre cube d'air compressé. Donc une qualité qui est nécessaire dans les domaines les plus exigeants de la médecine et la pharmacie, ainsi que la transformation et l'emballage des denrées alimentaires.
La durée de vie du granulat spécial BEKOKAT est enfin extrêmement avantageuse sur le plan économique, car il doit être remplacé seulement après au moins 20000 heures d'exploitation. Par comparaison, la durée de vie d'un filtre à charbon actif, même dans de parfaites conditions de travail, est déjà épuisée après 500 heures d'exploitation.
Depuis le printemps 2008 le système BEKOKAT est utilisé en continu dans l'entreprise de métallurgie Horstmann sans problèmes. Et la Horstmann GmbH & Co. KG a en plus une bonne conscience de l'environnement, car depuis l'utilisation du BEKOKAT, l'eau de condensation de l'installation d'air comprimé peut être évacuée sans problèmes ni traitement onéreux dans le réseau d'eaux usées.
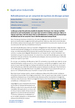