Optimisation du système d'air comprimé chez Umbria Filler
Secteur d'activité : | Industrie chimique |
Client / lieu / année : | Umbria Filler, Nocera Umbra (Italie), 2017 |
Utilisation de l'air comprimé : | Air de processus |
Produits installés : | BEKOSPLIT 13, METPOINT BDL, CLEARPOINT 3eco |
Les entreprises de l'industrie chimique sont aujourd'hui sous pression non seulement pour produire de manière efficace, mais elles doivent en plus répondre aux exigences de qualité et de durabilité. L'obtention de sceaux et de certificats volontaires permet aux entreprises de marquer des points non seulement auprès de leurs clients et de leurs partenaires, elles profitent aussi souvent d'économies directes. C'est également le cas de l'entreprise italienne Umbria Filler S.r.l., une société du groupe Moccia, qui produit des matières de remplissage à partir de carbonate de calcium naturel ou revêtu pour le carrelage, le caoutchouc, les plastiques, mais aussi pour les secteurs du BTP et de l'automobile.
Umbria Filler s'est fixée l'optimisation de "la qualité, la santé, l'environnement et de la consommation d'énergie" comme principe directeur, et elle a pris quelques mesures au cours des dernières années pour une production plus écologique et énergétiquement plus efficace. Le partenaire et conseiller était la filiale italienne de l'expert en air comprimé de Neuss BEKO TECHNOLOGIES
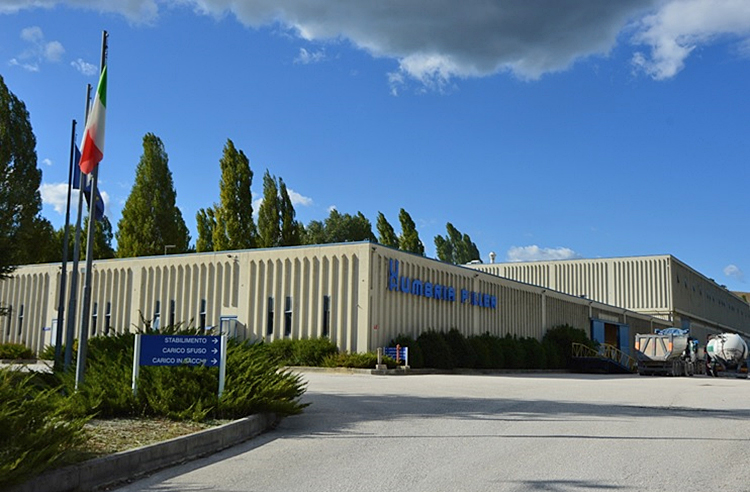
Le condensat propre augmente le caractère écologique de la production
Umbria Filler a commencé à s'intéresser à BEKO TECHNOLOGIES il y a cinq ans, alors que le département des compresseurs était confronté au problème de l'élimination de l'eau de condensation dans le système d'air comprimé. L'air comprimé et le condensat étaient contaminés par les compresseurs lubrifiés par huile. Les émulsions aqueuses avec des huiles dispersées dans l'eau devaient jusque là être éliminés avec les déchets spéciaux à des coûts considérables. BEKO TECHNOLOGIES apporta la solution avec la mise en place de l'unité de fractionnement d'émulsions BEKOSPLIT 13. Dans cette installation, les polluants organiques non solubles dans l'eau comme les huiles et les impuretés solides, qui ne peuvent être éliminées par la seule séparation gravimétrique, le sont par l'ajout d'un agent de floculation spécial. Les particules d'impuretés et d'huile sont encapsulées par le produit hautement efficace, puis filtrées hors du condensat, sous forme de macro-flocons. L'eau qui s'en écoule peut ensuite être dirigée dans le réseau des eaux usées, sans aucun risque de pollution.
"Aujourd'hui, la quantité de particules d'huile et d'hydrocarbures dans l'eau de condensation des compresseurs reste en deçà des valeurs limites nécessaires, comme l'indiquent les certifications ISO 14001, auxquelles nous nous soumettons régulièrement", dit Luca Frezzini, directeur-exécutif de Umbria Filler.
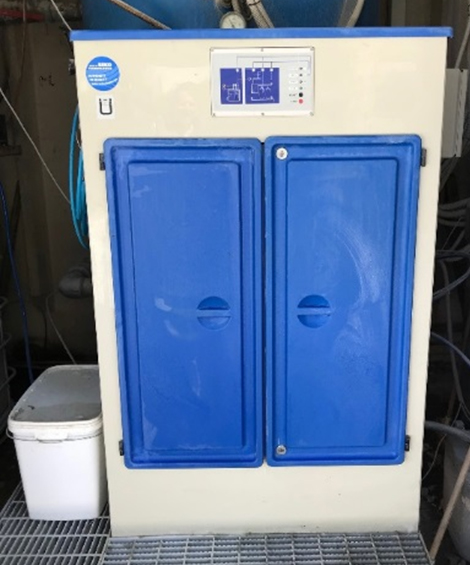
Augmentation de l'efficacité énergétique
Quand Umbria Filler se décida en 2017 à demander la certification énergétique selon l'ISO 50001, qui analyse la consommation d'énergie dans chaque service de l'entreprise, l'entreprise se trouva à nouveau devant un défi : la zone des compresseurs présentait une consommation d'énergie disproportionnée par rapport à la réalité de la production. Les quatre compresseurs utilisés, dont l'un avec la technologie Inverter (à variateur) et les trois autres d'une génération plus ancienne, représentaient ensemble 12 % de la consommation totale d'énergie de Umbria Filler. "Une telle consommation n'était plus acceptable pour nous. En raison des précédents positifs, nous nous sommes tournés vers BEKO TECHNOLOGIES pour résoudre le problème", rapporte Frezzini.
Dans une première étape BEKO TECHNOLOGIES a analysé le rapport entre l'air comprimé produit et la consommation d'électricité. L'analyse a révélé que l'exploitation du compresseur avec la technologie Inverter (à variateur) la plus récente serait suffisante pour couvrir 80 à 85 % du besoin de l'entreprise. L'installation a été modifiée en conséquence, de sorte qu'aujourd'hui un compresseur est exploité 24 h / 24, et en cas de besoin un deuxième compresseur est activé pour les 15 à 20 % restants. "Cela se passe un peu comme dans certains moteurs de voitures de la nouvelle génération : selon le besoin, ceux-ci utilisent seulement une partie des cylindres disponibles et réduisent ainsi la consommation et la pollution de l'environnement", explique Frezzini.
Surveillance sans failles du système d'air comprimé
Pour augmenter le contrôle des compresseurs, dans le cadre de la logique d'intervention, BEKO TECHNOLOGIES a installé dans une deuxième étape des sondes permettant l'enregistrement de la pression et du débit. Ainsi, l'activité des compresseurs et le besoin relatif en air comprimé sont mesurés simultanément. Les données collectées sont envoyées au terminal enregistreur de données METPOINT BDL qui mesure régulièrement les valeurs, les rend disponibles au sein du réseau de l'entreprise et les envoie à l'Automate Programmable Industriel (API). L'API pilote la mise en route et l'arrêt des compresseurs pour couvrir avec précision le besoin en air comprimé et maintenir la consommation d'énergie aussi basse que possible. Le logiciel supplémentaire METPOINT SW 201 permet de surveiller et de traiter les données de l'installation en continu. Ainsi les employés de Umbria Filler ont à tout moment une vue d'ensemble actuelle sur l'efficacité et l'utilisation du système d'air comprimé.
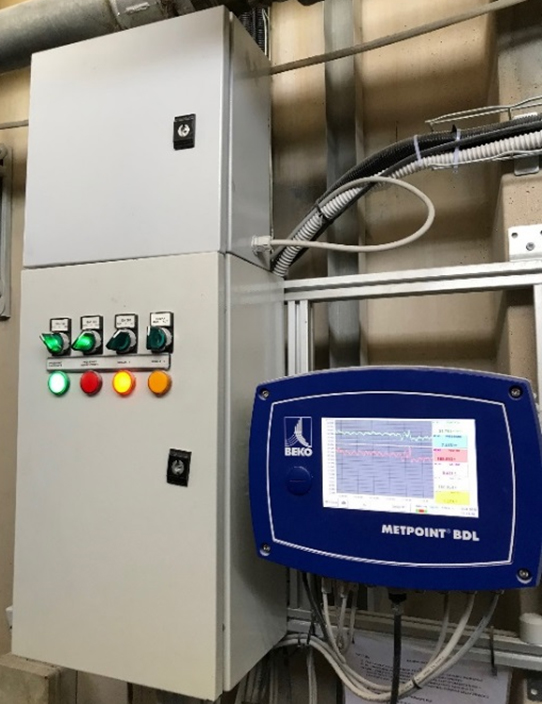
Réduction de la pression différentielle
Simultanément, la perte de charge au sein de l'installation a pu être réduite d'un bar environ, par l'installation des filtres CLEARPOINT 3eco. Grâce à l'utilisation d'un matériau de conception nouvelle (Mesh) et de technologies de fabrication qui se distinguent par l'association d'une vaste surface de filtration et d'une grande profondeur du lit de filtration, ainsi qu'une construction de corps optimisée pour une circulation sans entrave et résistant à la corrosion, le CLEARPOINT 3eco fournit un air comprimé de meilleure qualité, avec des coûts d'exploitation réduits. "La perte de charge nettement abaissée nous a permis de mieux gérer la problématique des seuils de pression de service pour les moteurs pneumatiques et de réduire considérablement la consommation d'énergie", selon Frezzeni
Vue d'ensemble du projet:
- Mesures préventives : analyse du système d'air comprimé par BEKO TECHNOLOGIES et installation d'un équipement de mesure de la gamme Instrumentation et de filtres d'air comprimé à haute efficacité énergétique
- Résultat : certification énergétique ISO 50001, réduction drastique de la consommation électrique
- Amortissement prévu des investissements par les économies considérables en seulement huit à dix mois.
Avec de nombreuses certifications à intervalles réguliers – l'ISO 9001, qui analyse les systèmes de gestion et de la qualité ; l'ISO 14001, qui concerne la certification environnementale et enfin l'ISO 50001 qui certifie une méthode correcte d'utilisation de l'énergie – Umbria Filler montre qu'elle poursuit ses objectifs du point de vue de la qualité du produit, de la santé dans l'environnement de travail, de la protection de l'environnement et des économies d'énergie avec cohérence.
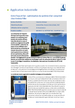