Technologie des condensats pour les turbocompresseurs
Secteur d'activité : | Métal, acier |
Client/Lieu/Année : | ThyssenKrupp Steel Europe, Duisbourg (Allemagne), 2011 |
Utilisation de l'air comprimé : | Dans la production, technologie des condensats |
Produits installés : | BEKOMAT |
Le réseau d'air comprimé du pôle de ThyssenKrupp Steel Europe AG à Duisbourg s'étend sur plus de dix kilomètres. Un système fortement ramifié, qui doit être ventilé de façon puissante et fiable. C'est ce à quoi veillent des turbocompresseurs haute performance qui sont soigneusement surveillés.
Ici, rien n'est petit. Qui plonge dans l'immense complexe sidérurgique de ThyssenKrupp Steel Europe AG à Duisburg doit se préparer être impressionné. C'est sur une durée de 120 ans que le site historique de production d'acier a acquis sa taille et son importance. Actuellement, c'est en termes de personnel le premier site de tout le groupe en Allemagne.
ThyssenKrupp Steel Europe se concentre sur le segment en pleine croissance des aciers plats haute qualité. L'éventail des prestations va des solutions matériaux aux pièces et sous-ensembles finis en acier en passant par des traitements spécifiques pour des produits, des prestations de services ou des prestations complètes. Grâce à la spécialisation de la métallurgie et du poids prépondérant de la fabrication de feuillards à chaud à Duisburg, il a été possible de créer dans l'axe rhénan un concept de site industriel unique en Europe. Ce concept est complété par des activités performantes de laminage à froid et de revêtement.
Comme pour presque tous les procédés industriels, l'air comprimé fait ici également partie des vecteurs énergétiques clés. En même temps, chez ThyssenKrupp Steel Europe AG, c'est un élément central de la sécurité du process. En conséquence, on porte donc une grande attention à l'air comprimé et à sa production.
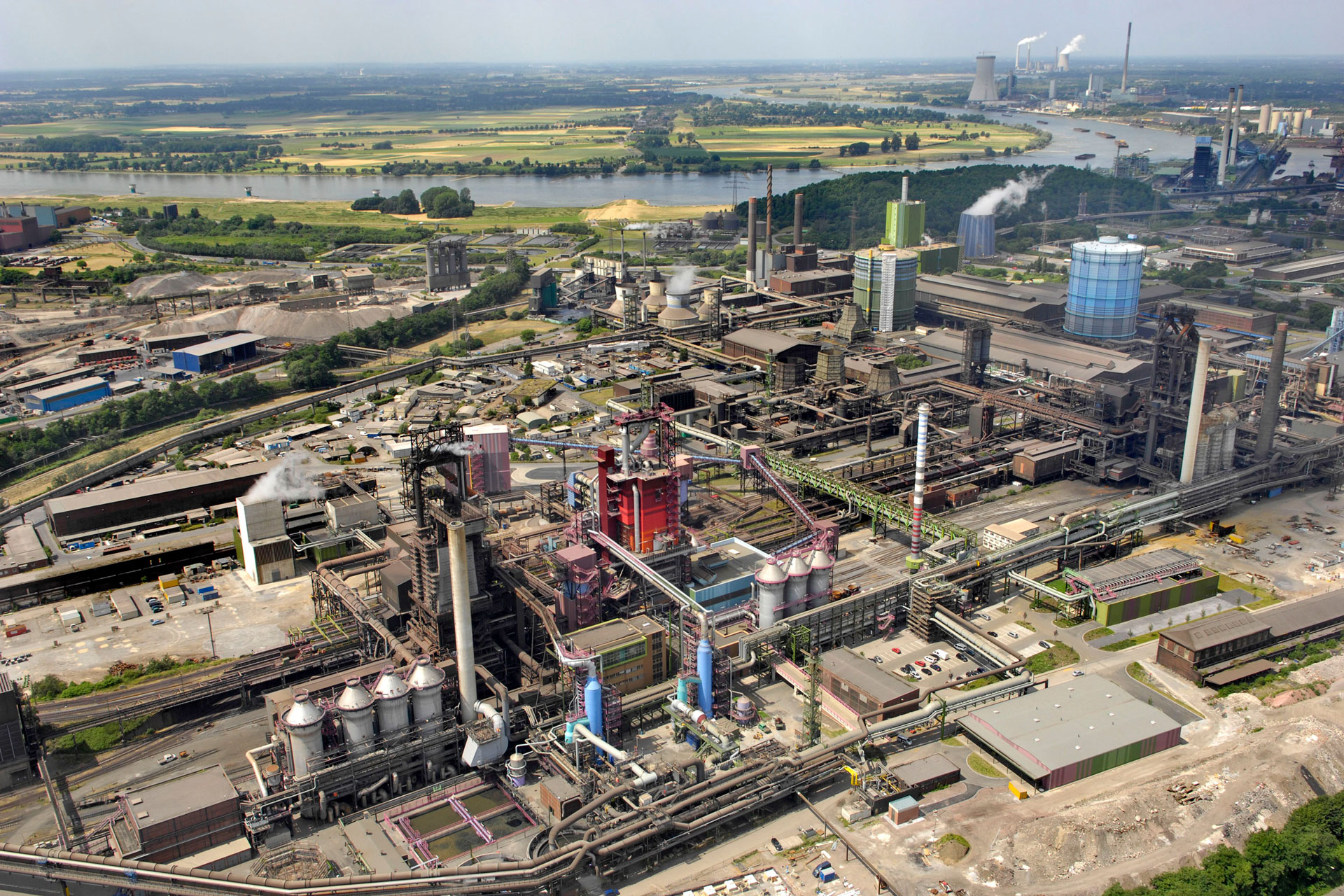
Des menus détails
Une grande salle des compresseurs au cœur de l'usine héberge une partie des composants servant à la production et à la préparation de l'air comprimé. Parmi ceux-ci, 3 turbocompresseurs avec chacun une capacité de compression de 25 000 m³/h. Ce volume d'en tout 75 000 m³ sert à sécuriser le fonctionnement d'un nombre incalculable de systèmes un peu partout dans le tissu productif. Par exemple, pour ce qui est du pilotage des vannes au niveau du laminoir, pour ne citer qu'une possibilité. Il est aisé d'imaginer quelles conséquences considérables des défaillances voire des arrêts dans de telles parties peuvent avoir pour l'ensemble de la production. Si un seul de ces compresseurs tombe en panne, cela peut entraîner de sérieuses difficultés.
Jusqu'à mi-2010, ça aurait pu devenir dans un cas particulier non seulement difficile mais même problématique : dans la purge des condensats. Ici, les puissants turbocompresseurs affichent des exigences particulières : chacun des quatre niveaux de compression d'une unité nécessite une purge des condensats à part entière. Jusque-là, la purge des condensats se faisait manuellement. Sa surveillance se faisait par contrôle manuel et visuel.
Les purgeurs de condensats mécaniques utilisés sur les turbocompresseurs ne pouvaient pas être intégrées au système électronique de surveillance de production de l'air comprimé. Toute désactivation depuis le poste de contrôle centralisé était ainsi impossible. Au regard de l'exigence de la politique d'assurance qualité en vigueur chez ThyssenKrupp Steel Europe AG, cette situation n'était plus acceptable. Car rien que la défaillance d'un purgeur sur un seul des quatre niveaux de compression pouvait entraîner une défaillance temporaire du compresseur. Aucun des fabricants d'équipement pneumatique ne paraissait à même de pouvoir équiper d'aussi grosses installations de compression avec des purgeurs de condensats capacitifs, à surveillance électronique et fiables.
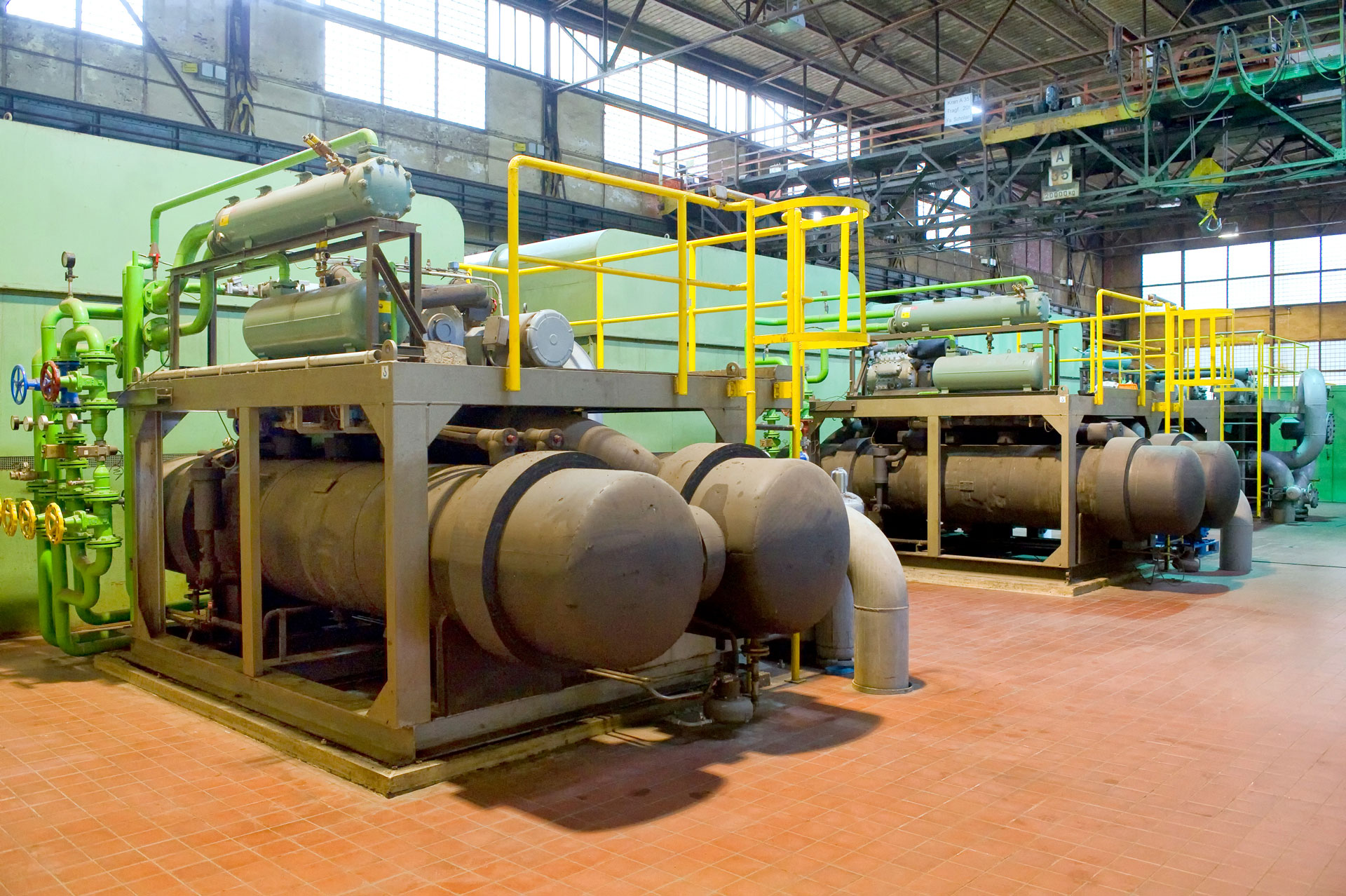
Purge à niveau régulé électroniquement
Un soulagement à cette situation sous pression est finalement venu après une conversation avec le fournisseur de systèmes d'air comprimé qui a accompagné en 1982 les purgeurs de condensats à régulation électronique du niveau jusqu'à la maturité : l'allemand BEKO TECHNOLOGIES GmbH dont le siège se trouve à Neuss au bord du Rhin. Au début, on s'y est concentré de nombreuses années uniquement sur ce produit, le BEKOMAT, et on l'a également perfectionné en correspondance pour des applications difficiles.
Le BEKOMAT à régulation de niveau ne contient aucune pièce mobile faillible au niveau de la zone de collecte du condensat, par exemple aucun flotteur. Cette fonction est assurée par un capteur capacitif. Il réagit à tout type de condensat et est absolument insensible à tout encrassement.
Cette lecture capacitive du niveau assure une purge adaptée à la production réelle de condensat sans perte d'air comprimé. Aucune émulsion n'est produite et de l'énergie est économisée. Des sections d'évacuation généreusement dimensionnées garantissent une purge sécurisée même en cas de condensats fortement pollués.
Mais l'électronique de commande intelligente n'assure pas que la purge des condensats. Elle gère en même temps la surveillance entièrement automatique de l'état de l'appareil. Toutes les défaillances sont affichées avec des LED au niveau du purgeur et peuvent également être signalées sous forme de message d'erreur aux postes de surveillance centraux via un contact hors potentiel.
Avec ces caractéristiques, les purgeurs de condensats BEKOMAT correspondaient exactement au profil d'exigence de ThyssenKrupp Steel Europe AG à Duisburg. C'est en particulier l'intégration sans aucun problème dans le système de surveillance et de commande automatique déjà existant qui a remporté les suffrages.
Cinq semaines seulement
Au début de l'été 2010, les spécialistes de BEKO TECHNOLOGIES ont installé en étroite collaboration avec les équipes techniques de ThyssenKrupp Steel Europe les quatre premiers BEKOMAT de différentes tailles sur l'un des turbocompresseurs. Ce n'est que quand cette configuration fonctionnait correctement jusque dans le moindre détail que l'on s'est tourné vers les autres éléments. Mais il n'y a pas eu beaucoup de temps de perdu : En à peine cinq semaines, entre le premier modèle de configuration et le « redémarrage » complet, l'ensemble de la purge des condensats était modernisé de manière fiable. D'autres BEKOMAT à régulation électronique du niveau se trouvent sur divers sécheurs frigorifiques du système pneumatique.
Le gain en fiabilité du process ainsi obtenu constitue un élément important de la politique de sécurité stricte de ThyssenKrupp Steel Europe. Les futurs développements au niveau du système d'air comprimé ne devraient pas non plus provoquer de sueurs froides chez les responsables.
Car toutes les variantes des BEKOMAT sont continuellement adaptées aux caractéristiques des compresseurs et sécheurs les plus courants. Celle-ci évolue continuellement et suivent ainsi les exigences de performance de la production industrielle d'air comprimé.
Une technique d'avenir fiable
Ainsi, chez BEKO TECHNOLOGIES, on a par exemple récemment présenté la cinquième génération de la gamme, les modèles 31 et 32, qui représentent actuellement un optimum en termes de rentabilité. Avec un principe de conception entièrement novateur avec des purgeurs de condensats à régulation électronique de niveau, ces appareils proposent des avantages significatifs au niveau de la maintenance.
Ils sont tout simplement scindés en deux modules : l'unité de maintenance, qui regroupe dans son corps en aluminium insensible à la corrosion l'ensemble des pièces d'usure et composants sans maintenance et l'unité de sondes et de commande électronique, à n'installer qu'une seule fois. Les deux sous-ensembles sont reliés par un raccord rapide, très pratique à manipuler.
Ce concept novateur permet de remplacer en un tour de main l'ensemble des consommables et éléments requérant un entretien : il suffit de remplacer le module appelé « unité de maintenance ». La séparation et le raccordement des deux modules s'effectuent en toute simplicité, sans aucun outillage.
Même si cette solution n'est actuellement pas encore mise en œuvre dans les installations avec des volumes d'air comprimé énormes, comme chez ThyssenKrupp Steel Europe AG. Pour l'entreprise de Duisburg, c'est une excellente démonstration de l'enthousiasme de développement de son fournisseur d'équipements.
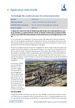