Traitement de l'air comprimé sur les locomotives hybrides
Secteur d'activité : | Transport, locomotives |
Client/Lieu/Année : | ALSTOM, Stendal (Allemagne), 2013 |
Utilisation de l'air comprimé : | Air de commande, air de processus |
Produits installés : | CLEARPOINT, DRYPOINT M, BEKOMAT, ÖWAMAT |
Un concept très tendance dans la construction automobile, une technique déjà éprouvée dans le monde ferroviaire : L'entraînement hybride. La combinaison d'un générateur diesel et d'une batterie sur les locomotives modernes permet des économies de carburant pouvant atteindre 50 %. Un système sophistiqué « mobile » de traitement d'air comprimé pour commander les freins hydrauliques est toujours embarqué.
Si les modélistes ferroviaires pouvaient rêver de se trouver dans un endroit précis, Stendal près de Magdebourg aurait les meilleurs chances d'être celui-là. Car c'est sur ce sol riche en tradition et dans des halles similaires que naissent ici depuis des décennies les géants d'acier qui font rouler le trafic ferroviaire : Les locomotives de ALSTOM. Entre autres la locomotive de manœuvre la plus ingénieuse et la plus économique actuellement : une hybride avec une combinaison d'un générateur diesel et d'une batterie.
Le groupe français ALSTOM présent sur la scène internationale est le leader mondial de la construction d'installations et de produits pour la production d'électricité, de transmission d'énergie et d'infrastructures ferroviaires. Le groupe construit le train le plus rapide et le métro automatique ayant la plus forte capacité au monde, et dans la ville allemande de Stendal, la locomotive hybride novatrice.
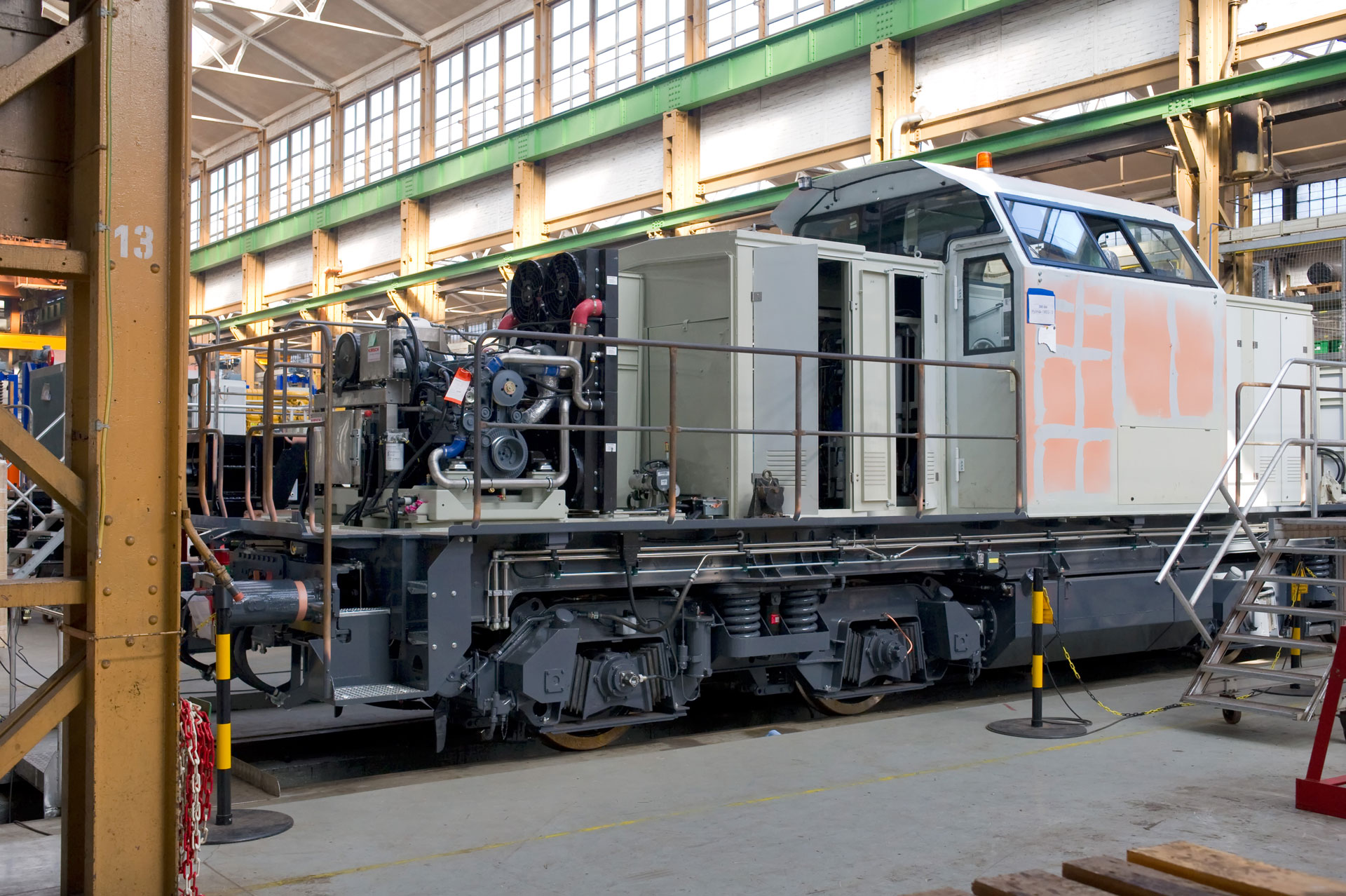
C'est ici, sur le site d'entretien des locomotives ALSTOM – une entreprise commune avec la Deutsche Bahn AG –, que le concept d'entraînement combiné a pris sa forme concrète dès 2006. Cette année-là, les ingénieurs ALSTOM ont mis les premiers prototypes opérationnels de la locomotive hybride de manœuvre sur les rails. Elle a été construite dans le cadre de la locomotive éprouvée V100 avec ses trois châssis rotatifs. En plus du générateur classique diesel-électrique, une grande batterie a été embarquée pour stocker l'énergie, ainsi qu'un tout nouveau système de traitement d'air comprimé pour le système de freins de la locomotive et des wagons accrochés.
Du prototype à la série
Chez ALSTOM, on est très fier des « destriers d'acier », en particulier de leur puissance et de leur caractère économique. Le principe : la version hybride de la locomotive de manœuvre est équipée d'un générateur diesel de 230 kW et d'une batterie. Avec cette configuration, elle est particulièrement adaptée pour les manœuvres lourdes. Un générateur diesel économique et écologique charge la batterie et peut aussi entraîner directement le moteur électrique pour les pics de charge. Pour les charges partielles, la locomotive fonctionne sur batterie et économise ainsi dans cette version de 30 à 50 % de gazole par rapport aux locomotives de manœuvre classiques. La locomotive hybride musclée avec sa force de traction de 220 kN se déplace à une vitesse maximale de 60 km/h sur quatre essieux.
Le système de freins est particulièrement sollicité pendant le triage, avec les nombreux changements de charges et de direction. La capacité de performance et la stabilité du traitement de l'air comprimé ont donc reçu la plus grande attention dès les premières phases de développement de la version hybride.
Traitement de l'air comprimé directement à bord
La production et le traitement de l'air comprimé pour le système de freinage de la machine et des wagons accrochés sont effectués en complète autonomie à bord de chaque locomotive. Dans un poste d'air comprimé « mobile » propre derrière le poste de conduite. Hormis le carter, il est donc « à l'air libre », donc exposé en permanence aux intempéries et aux conditions climatiques. En mode de triage, à des températures négatives hivernales tout comme dans la chaleur brûlante de l'été. Il est utilisé sur les terres nord tout comme dans les pays chauds et humides de l'hémisphère sud ou en Asie. Donc des défis énormes surtout pour la technique de traitement de l'air comprimé, et aucune marge de manœuvre pour des concepts incertains.
C'est dans ce contexte que ALSTOM a fait monter à bord à Stendal un spécialiste de ce domaine dès la phase de projection : le fournisseur allemand de systèmes d'air comprimé BEKO TECHNOLOGIES GmbH de Neuss.
Il a envoyé ses ingénieurs du Rhin à l'Elbe pour prendre en charge l'un des cahiers des charges les plus diversifiés à ce jour dans l'histoire du développement de projets. Rapidement, le besoin est apparu de développer de nouvelles versions d'appareils, à côté de la combinaison de composants de traitement existants, pour la séparation huile-eau.
Cahier des charges épais pour les ingénieurs de l'air comprimé
BEKO TECHNOLOGIES a accompagné dès le départ le développement des systèmes pour les locomotives hybrides ALSTOM. Un autre défi : en mode de triage, les locomotives restent parfois naturellement pendant une longue durée dans la même position. En cas de températures négatives, le risque de gel de la condensation dans le système de traitement de l'air comprimé menace. C'est pourquoi tous les composants et conduites utiles ont été équipés d'un système de chauffage. Par ailleurs, toutes les évacuations de condensation montées sont reliées à la commande du compresseur. Ainsi, en cas de panne ou d'une coupure du système électrique de la locomotive, le condensat résiduel encore présent dans le système est évacué automatiquement avant de pouvoir geler.
Il est dirigé via l'évacuateur de condensat BEKOMAT directement dans un préparateur de condensat ÖWAMAT pour la séparation huile-eau. Ces appareils développés par BEKO TECHNOLOGIES prennent en compte la protection de l'environnement et des eaux et suivent une approche globale de la durabilité.
Sa technique de cartouche est particulièrement facile à utiliser. Elle permet un remplacement rapide du filtre et facilite l'élimination presque sans déchets. En plus, les durées de vie des filtres sont beaucoup plus longues que celles des filtres à charbon actif classiques. La haute qualité des produits génère en plus des intervalles d'entretien plus longs, une exigence majeure de ALSTON pour l'utilisation « mobile », plutôt dure sur les locomotives. BEKO TECHNOLOGIES prévoit spécialement pour cela le séparateur huile-eau ÖWAMAT avec un carter en acier inoxydable anti-corrosion particulièrement robuste.
Un système complet dans un espace très restreint
Le séparateur huile-eau n'est cependant que la dernière étape du système de traitement de l'air comprimé de la locomotive hybride conçu avec assemblage de formes. Le séparateur d'eau CLEARPOINT est installé juste derrière le compresseur à vis avec le premier évacuateur de condensat. Chaque millimètre compte dans l'espace limité de la locomotive. Le carénage étroit du système d'air comprimé occupe déjà la surface d'un petit abri de jardin sur seulement la moitié de sa hauteur.
Cependant il y a assez de place à côté du compresseur et du séparateur d'eau pour un filtre très fin avec évacuateur de condensat, ainsi que deux sécheurs à membrane DRYPOINT M de BEKO TECHNOLOGIES. L'un d'entre eux en version « Plus » avec un nanofiltre intégré.
Les sécheurs à membrane DRYPOINT M sont basés sur la technologie « Twist 60 » de BEKO TECHNOLOGIES : la membrane est composée de couches croisées de fibres creuses disposées autour d'un tuyau central. Cette structure représente une utilisation très efficace des principes actifs physiques et permet le séchage de l'air comprimé avec une faible consommation d'énergie. Pour le processus de séchage, une partie de l'air comprimé est déviée en continu dans la zone de sortie de l'élément à membrane et détendue à la pression atmosphérique comme air de régénération, ou utilisée comme air de rinçage.
Quand cela roule comme sur des rails
Ces atouts du sécheur à membrane DRYPOINT M sont précisément ceux indispensables pour une utilisation sur la locomotive hybride : une sécurité fonctionnelle absolue, la plus haute fiabilité et une disponibilité immédiate d'air comprimé sec même dans un mode de travail discontinu. De plus : la liberté par rapport à l'entretien et l'usure, car il n'y a aucune pièce mobile. Il est vrai qu'il n'est pas possible d'embarquer un monteur en plus pour le système d'air comprimé sur chaque locomotive. Le système doit fonctionner, être robuste et sans pannes. Jusqu'à présent c'est le cas de toutes les locomotives hybrides ALSTOM.
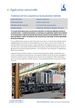