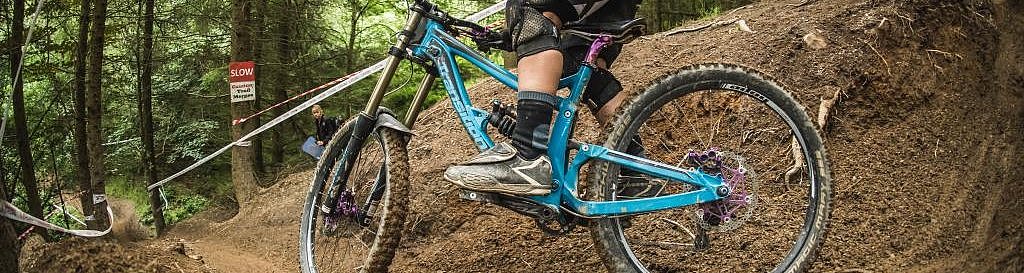
HOPE TECHNOLOGY get their compressed air system into gear with help from BEKO TECHNOLOGIES
Hope Technology is one of the world leaders in engineering bicycle components. Since 1989, owners Ian Weatherill and Simon Sharp have been pushing the industry forward through designing, testing and manufacturing virtually all products in-house at the factory in Barnoldswick, United Kingdom. They employ over 150 employees. BEKO TECHNOLOGIES have installed equipment at their factory which has increased their compressed air quality from ISO standard 2.5.4 to class 2.4.1. This has helped improve product quality and protect the production equipment saving energy and costs.
Hope Technology began life in the late 1980’s as a subcontract machining business making tools and fixtures for the many local aerospace companies. In 1989 they began making disc brakes for the newly developed mountain bikes. Initially for the personal use of the owners Ian Weatherill and Simon Sharp but they quickly realised these brakes could be sold as a product in their own right.
Since disc brakes were such a novel idea on a bicycle they decided to begin manufacturing other more common bicycle products, the first of these being a front hub. These began selling through retailers in the UK and interest was also shown in many countries around the world.
Over the subsequent years many more products were added to the range and in 2000 the decision was made to stop all subcontract work and concentrate purely on bicycle products.
Hope now manufactures almost every part for a bicycle including hubs, brakes, headset, stems, bottom brackets and lights. The only major part left to develop is the actual frame, which may be happening in the not too distant future. All parts are proudly manufactured in Hope’s Barnoldswick factory which is a true state of the art facility. They have almost 150 staff operating the factory 24-7, running the 55 CNC machines, anodising the individual components and hand assembling the finished parts. Manufacturing all products on site gives Hope total control on quality and delivery schedules.
Hope exports around 50% of its production to over 40 countries. They deal directly with retailers in the UK, France, Germany, Austria, Belgium and The Netherlands (employing French and German speaking staff), then have distributors in many other countries. Their components have an excellent international reputation for both quality and reliability. They are generally fitted by enthusiasts looking to upgrade their bikes to the highest levels and are supplied through specialist retailers.
Hope Technologies had poor compressed air quality on site which was affecting product quality at their factory. BEKO TECHNOLOGIES recommended and installed a refrigeration dryer, oil water separators and condensate drains together with a carbon tower and membrane dryer for their compressed air system.
The refrigeration dryer and carbon tower with filters clean the compressed air which is used to manufacture and spray the carbon fibre cycle parts, frames, handlebars and seat stems in the production area. The air quality is critical as the compressed air comes in to direct contact with the carbon fibre as the parts are bonded together.
The membrane dryer is used for the CMM equipment where a -20 degree C dew point is required to protect the air bearings, any water contamination could cause surface rust and require a very expensive refurbishment.
Since installing the refrigeration dryer and carbon tower the compressed air quality has increased from ISO standard 2.5.4 to class 2.4.1. There has been an increase in product quality with no product spoilage in the carbon frame production area and the spray shop. The CMM machine bearings have been kept dry thanks to the membrane dryer and has increased life of the bearings.
Co-owner Ian Weatherill says “We are very happy with the results since installing the BEKO equipment, our compressed air quality has increased and we no spoilage of products saving us money. We found BEKO TECHNOLOGIES to be both professional and knowledgeable”.
If you would like more information or to find out how BEKO TECHNOLOGIES can help you, please contact us on 01527 575778 or email info@beko-technologies.co.uk. All our plants are unique as your application. Thanks to our comprehensive range we are able to meet any requirements.