Ottimizzazione del sistema d’aria compressa presso Umbria Filler
Settore: | Industria chimica |
Cliente/luogo/anno: | Umbria Filler, Nocera Umbra, 2017 |
Uso dell’aria compressa: | Aria di processo |
Prodotti installati: | BEKOSPLIT 13, METPOINT BDL, CLEARPOINT 3eco |
Oggi, le aziende del settore chimico non sono sotto pressione poiché devono produrre in modo efficiente, bensì devono anche soddisfare requisiti di qualità e di sostenibilità. Acquisendo sigilli e certificati in modo volontario, le aziende non si distinguono solo tra i loro clienti e partner, bensì spesso traggono anche vantaggio dai risparmi diretti. Vale anche per l’italiana Umbria Filler S.r.l., un’impresa del Gruppo Moccia, che da oltre 40 anni produce riempitivi in carbonato di calcio naturale oppure rivestito per piastrelle, gomma, plastiche e il settore edile e automobilistico.
L’ottimizzazione di qualità, salute, ambiente e consumo energetico è uno standard presso Umbria Filler e, negli ultimi anni, ha richiesto alcune misure per la produzione ecologica ed energeticamente efficiente. Partner e consulente è stata la filiale italiana degli esperti dell’aria compressa BEKO TECHNOLOGIES di Neuss.
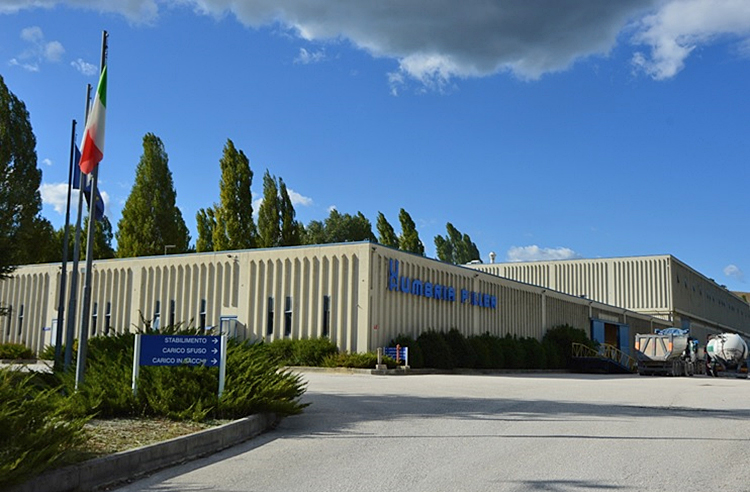
Una condensa pulita aumenta l’ecologicità della produzione
Umbria Filler ha conosciuto BEKO TECHNOLOGIES cinque anni fa, quando la sezione compressori si è trovata davanti al problema dello smaltimento dell’acqua di condensa dal sistema d’aria compressa. L’aria compressa e la condensa venivano contaminate dai compressori lubrificati a olio. Le emulsioni acquose con oli dispersi in acqua sino a quel momento dovevano essere smaltite come rifiuto speciale con costi elevati. BEKO TECHNOLOGIES propose la soluzione con l’installazione della sistema di scissione BEKOSPLIT 13. In questo, inquinamenti organici non idrosolubili come gli oli e lo sporco dovuto a particelle solide, che non era possibile rimuovere solamente mediante la separazione puramente fisica per gravità, vengono smaltiti con l’aggiunta di uno speciale materiale splittante. Le particelle di sporco e olio vengono incapsulate dal materiale altamente efficace e filtrati via dalla condensa come macrofiocchi. L’acqua in uscita può successivamente essere scaricata nella rete fognaria.
“Oggi, la quantità di acqua delle particelle di olio e di idrocarburi presente nell'acqua di condensa dei compressori resta al di sotto dei valori limite necessari, come dimostrano le certificazioni ecologiche secondo ISO 14001, a cui ci sottoponiamo regolarmente”, dice Luca Frezzini, amministratore delegato di Umbria Filler.
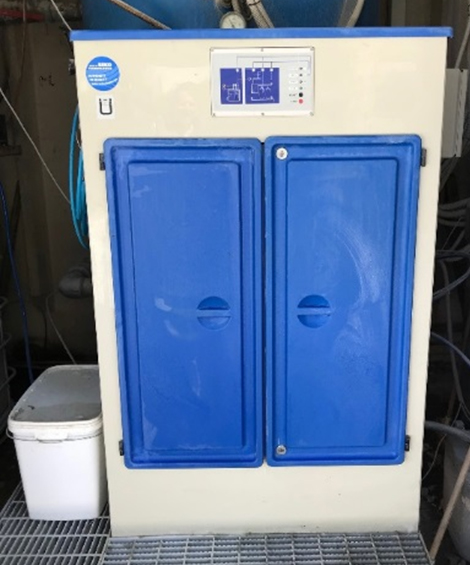
Aumento dell'efficienza energetica
Quando, nel 2017, Umbria Filler decise di richiedere la certificazione energetica secondo ISO 50001, che analizza il consumo energetico di ogni settore aziendale, l’impresa si trovava di nuovo davanti a una sfida: rispetto alla realtà di produzione, l’area dei compressori presentava un consumo energetico sproporzionatamente elevato. I quattro compressori impiegati, di cui uno con tecnologia inverter e tre di vecchia generazione, realizzavano insieme il dodici percento del consumo energetico di Umbria Filler. “Per noi un tale consumo non era più accettabile. Visti i positivi casi precedenti, ci siamo rivolti aBEKO TECHNOLOGIES, al fine di risolvere il problema” racconta Frezzini.
In una prima fase, BEKO TECHNOLOGIES ha analizzato il rapporto tra aria compressa generata e consumo di corrente. L’analisi diede come risultato che, per il fabbisogno produttivo, era sufficiente esclusivamente un compressore con l’aggiornata tecnologia a inverter, al fine di coprire il fabbisogno energetico aziendale dall’80 all’85 percento. L’impianto venne corrispondentemente modificato, tanto che oggi è in funzione h24 un solo compressore e, se necessario, per il restante 15-20 percento, viene coinvolto un secondo compressore. “È come per determinati motori d’auto dei nuova generazione: TECHNOLOGIESa seconda della necessità, questi utilizzano solamente una parte dei cilindri disponibili e riducono quindi il consumo e l’inquinamento ambientale,” spiega Frezzini.
Monitoraggio continuo del sistema d’aria compressa
Per aumentare il controllo sulla logica di intervento dei compressori, BEKO TECHNOLOGIES ha installato in una seconda fase delle sonde per il rilevamento di pressione e portata. Così, al contempo, vengono misurati l’attività dei compressori e il relativo fabbisogno di aria compressa. I dati raccolti vengono inviati al data logger METPOINT BDL che misura regolarmente i valori, li rende disponibili nella rete aziendale e li invia dal comando di memoria programmabile (PLC). Il PLC guida l’attivazione e lo spegnimento dei compressori, al fine di coprire esattamente il fabbisogno di aria compressa e quindi di tenere il consumo energetico più basso possibile. Con l’aggiuntivo software METPOINT SW 201, i dati dell’impianto vengono continuamente monitorati ed elaborati. Così, i collaboratori di Umbria Filler hanno sempre la panoramica attuale e il controllo dell’efficienza e dello sfruttamento del sistema d’aria compressa.
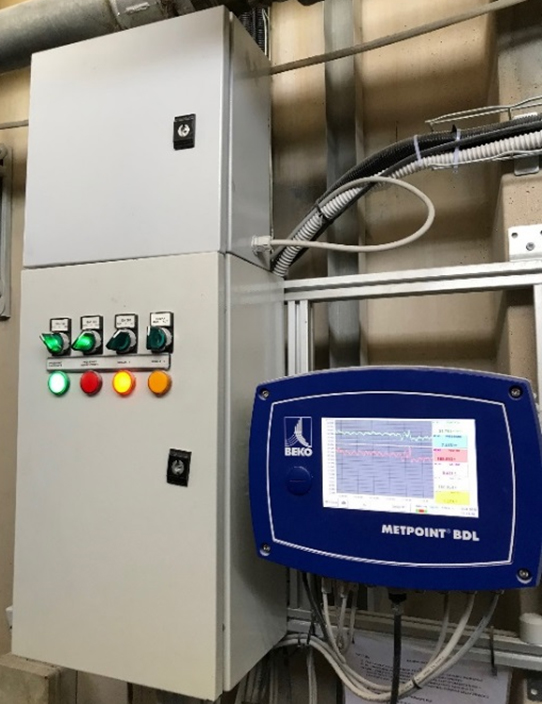
Riduzione della pressione differenziale
Al contempo, la perdita di pressione nell’impianto è stata ridotta di circa un bar mediante l’installazione di un filtro CLEARPOINT 3eco. Mediante l’uso di uno speciale materiale (mesh) e delle tecnologie di produzione, che si contraddistinguono grazie all’unione di un’ampia superficie filtrante ed elevato letto filtrante nonché una costruzione dell’alloggiamento ottimizzata al flusso e protetta dalla corrosione, il CLEARPOINT 3eco consente un’aria compressa migliore con costi operativi ridotti. “La caduta di pressione chiaramente ridotta garantisce una soglia di pressione di lavoro sostanzialmente più semplice e meno intensa dal punto di vista energetico per i motori”, così Frezzini.
Panoramica del progetto:
- Misure: Analisi del sistema d’aria compressa da parte di BEKO TECHNOLOGIES e installazione del sistema di misurazione e dei filtri d’aria compressa
- Risultato: certificazione energetica ISO 50001, drastica riduzione del consumo di corrente
- Ammortamento degli investimenti grazie al sostanziale risparmio prevedibilmente in soli otto o dieci mesi.
Con innumerevoli certificazioni a breve distanza - la ISO 9001 che analizza i sistemi di gestione e di qualità; la ISO 14001 che concerne la certificazione ambientale e infine la ISO 50001 che accelera la corretta procedura durante l’uso dell’energia - Umbria Filler dimostra di perseguire coerentemente la propria idea di ottenere gli obiettivi massimi in relazione a qualità di prodotto, salute nell’ambiente di lavoro, tutela dell’ecologia e risparmio energetico.
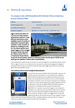