Raffreddamento di macchine da taglio a laser mediante aria compressa
Settore: | tecnologia laser |
Cliente/luogo/anno: | Horstmann, Verl (Germania), 2008 |
Uso dell’aria compressa: | Aria di processo |
Prodotti installati: | BEKOKAT |
Il taglio laser rientra tra le procedure di separazione termiche. Il calore non è percettibile al punto focale, ovvero dove il fascio laser tocca il materiale da tagliare; bensì, nel percorso della luce precedente. Proprio qui è necessario il raffreddamento. Ancora meglio se realizzato in modo economico con aria compressa. Che, tuttavia, deve essere assolutamente priva di olio.
A Horstmann GmbH & Co. KG con sede a Verl, nelle vicinanze di Gütersloh, ci si dedica alla lavorazione del metallo altamente qualitativa e sofisticata per clienti famosi di numerosi rami aziendali, tra cui del settore automobilistico e navale, nonché dell’ingegneria meccanica, impiantistica e costruzione di utensili.
Le instancabili macchine di taglio laser in uso a Horstmann reagirebbero malissimo anche alla minima penetrazione di olio dovuta all’aria compressa. Inoltre, ciò comporterebbe anche una riduzione di prestazione e qualità.
Infatti, il loro affilatissimo fascio laser diventerebbe letteralmente una tremolante “lampada a olio”. Diversamente da quanto si potrebbe immaginare, l’aria compressa nelle macchine di taglio laser di Horstmann non viene usata per l’impianto pneumatico, bensì esclusivamente per il raffreddamento del percorso della luce laser. Infatti, fondamentalmente un impianto di taglio è costituito da un laser CO2 da una fonte di fascio laser e una focalizzazione mobile, di norma uno specchio concavo oppure una lente convessa. A partire dalla fonte, il raggio laser viene guidato mediante specchio di rinvio alla lavorazione. Qui, il fascio laser viene focalizzato e quindi viene emessa la densità di potenza necessaria al taglio. Da Horstmann, dove in precedenza venivano tagliate lamiere d’acciaio inossidabile, si tratta di una potenza irradiata fino a sei kW. Tanto da penetrare completamente un corpo umano senza alcun problema.
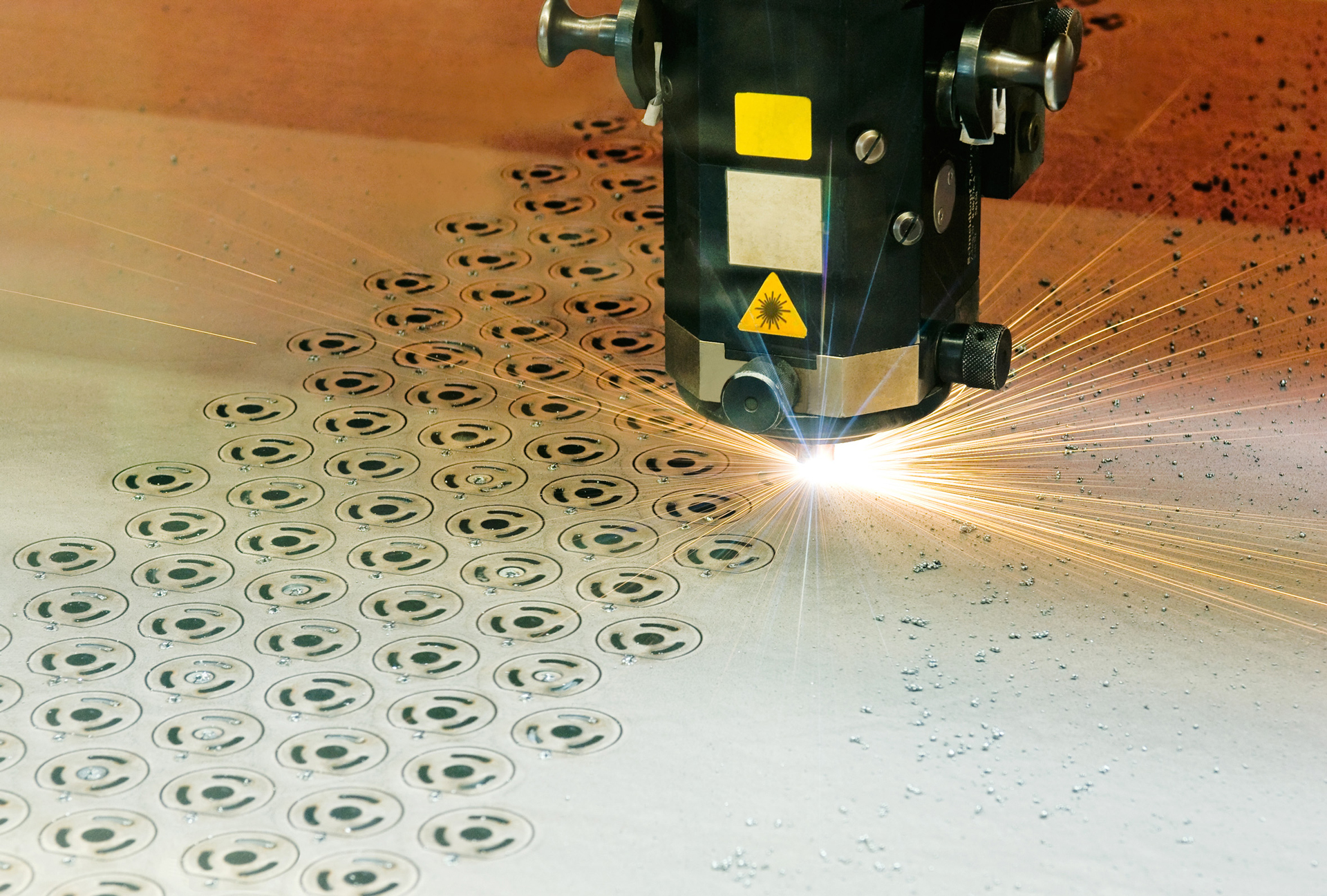
Per il fatto che l’ottica mobile, “volante”, si muove al di sopra della lamiera da lavorare, la distanza fino alla fonte di luce laser fissa cambia continuamente. Tuttavia, il raggio laser generato non possiede il parallelismo necessario a trasferirlo alle distanze in parte grandi e mutabili. Ecco perché, e anche per ridurre il carico termico dello specchio di rinvio, in parte esso viene ampliato con un telescopio a specchio.
La reale guida del raggio tra la fonte laser e l’ottica di focalizzazione avviene mediante uno specchio rivestito in oro o molibdeno, realizzato di norma in rame puro oppure in silicio monocristallino. E poiché reagiscono in modo assolutamente sensibile all’olio ovvero agli aerosoli, che vi si depositano sopra e rendono necessaria una sostituzione anticipata, estremamente costosa.
Nell'intero percorso di luce del laser, ovviamente si sviluppano temperatura elevate. Senza raffreddamento, i materiali qui impiegati, per esempio lo specchio di rinvio e ancora più rapidamente il soffietto dell’unità ottica amovibile, subirebbero danni ingenti.
Questa funzione di raffreddamento vitale è svolta dall'aria compressa soffiata nel percorso della luce. Essa deve essere assolutamente priva di particelle e olio, nonché asciutta, al fine di non “dissipare” il raggio laser per via delle particelle sospese, né sporcare lo specchio di rinvio con dei residui. Persino le più piccole percentuali di olio e aerosoli nell’aria compressa avrebbero conseguenze fatali per la sicurezza del processo e per l’economicità dell’impianto di taglio.
Tuttavia, entrambi i fattori - insieme all’assoluta qualità del prodotto - sono componenti essenziali del continuo successo aziendale di Heinrich Horstmann GmbH & Co. KG. Ecco perché al tema del trattamento dell’aria compressa l’azienda dedica enorme attenzione.
Sinora, da Horstmann, come anche presso utenti di aria compressa con simili necessità, si è cercato di produrre aria compressa priva di olio con tecniche di compressione, filtraggio e basate su essiccatori, relativamente costose, spesso persino accoppiate. Spesso, il tutto è possibile con un’affidabilità variabile, da elevata a bassa.
Anche da Horstmann non si era ancora mai trovata una soluzione veramente soddisfacente, soprattutto non dopo l’acquisto di impianti di taglio nuovi, ancora più potenti. Nel 2008, l’azienda venne a conoscenza del processo catalitico dello specialista tedesco dell’aria compressa BEKO TECHNOLOGIES GmbH per la produzione di aria compressa assolutamente priva di olio. La procedura chiamata BEKOKAT apriva la strada a un’aria compressa assolutamente priva di olio con un approccio completamente diverso rispetto alla soluzioni del momento: con la catalisi.
Ossidazione totale degli idrocarburi
Fondamentalmente, il sistema BEKOKAT realizza un’ossidazione totale degli idrocarburi e quindi produce un'aria compressa assolutamente priva di olio. Il tutto, con una fase processuale concentrata, onnicomprensiva successiva alla compressione. In questo modo, la completa sgrassatura dell’aria compresa avviene in un unico componente dell’impianto. Questo funziona indipendentemente dalle condizioni ambientali, dalla concentrazione iniziale dell’olio e dall’umidità relativa dell’aria compressa.
La procedura BEKOKAT si dedica infatti a tutto lo sporco presente nell'aria compressa inviata al compressore. Si tratta insieme di lubrificanti, oli, anidride solforosa, monossido di carbonio, gas nitrosi ecc. Essi sono presenti sia in forma di gas, che di vapore e aerosol. La procedura BEKOKAT trasforma tali componenti dell'aria completamente in biossido di carbonio ed acqua.
Quest’ultima può essere quindi avviata alla rete fognaria direttamente e senza mettere in atto ulteriori misure di tutela ambientale. Persino la condensa prodotta dal raffreddamento dell’aria compressa è assolutamente priva di olio e si può scaricare nella rete fognaria senza alcun trattamento. Questa ossidazione totale e modalità di lavoro assolutamente priva di residui non è possibile con nessun’altra procedura.
Il catalizzatore è un granulato del BEKOKAT che, mediante elementi riscaldanti, viene riscaldato a una temperatura d’esercizio di circa 150 gradi Celsius. Nel catalizzatore, le molecole dell’olio vengono frazionate finché ne resta solamente un atomo di carbonio. Nella fase finale della catalisi, le molecole dell’olio vengono ossidate in H2O e CO2.
L’essenziale è che le catene di idrocarburi, ovvero le molecole d’olio, presso ogni punto necessario possano essere “decodificate”. Vengono sempre frazionate finché resta solamente biossido di carbonio e idrogeno. Le catene di idrocarburi dalle diverse lunghezze da compressori privi di olio e lubrificati a olio, per BEKOKAT non rappresentano quindi alcun problema,
Inoltre, spesso gli utenti non sanno che i filtri ai carboni attivi spesso usati non posso adsorbire composti polari, come olefine, alcoli, glicoli o chetoni. Il sistema BEKOKAT, al contrario, rimuove completamente anche queste sostanze dall'aria compressa. Nell’ulteriore svolgimento del processo BEKOKAT, l’aria compressa pulita viene raffreddata in uno scambiatore di calore a circa 10-15 gradi Celsius mediante ingresso, e resta a disposizione per l’intera applicazione.
Con la procedura BEKOKAT è possibile, per la prima volta, ottenere un’aria compressa assolutamente priva di olio sempre con un contenuto residuo di olio massimo che non supera i 0,003 milligrammi per metro cubi di aria compressa. Una qualità, quindi, necessaria nei settori più esigenti della medicina e della farmacia, nonché nell’elaborazione e nell’imballaggio di alimenti.
Dal punto di vista economico è assolutamente vantaggiosa anche l’enorme durata utile dello speciale granulato del BEKOKAT, che deve essere sostituito solo dopo 20.000 ore di esercizio. A confronto, la forza vitale di un filtro ai carboni attivi, anche in condizioni di lavoro perfette, va sostituito già dopo circa 500 ore di esercizio.
Sin dall’inizio dell'estate del 2008, il sistema BEKOKAT funziona ventiquattro ore al giorno e senza guasti presso l’azienda Horstmann, dedita al trattamento dei metalli. La Horstmann GmbH & Co. KG ha inoltre sviluppato un’ottima consapevolezza ambientale, poiché sin da quando impiega il BEKOKAT, l’acqua di condensazione dall’impianto ad aria compressa può essere avviata senza problemi e senza un costoso trattamento direttamente alla rete fognaria.
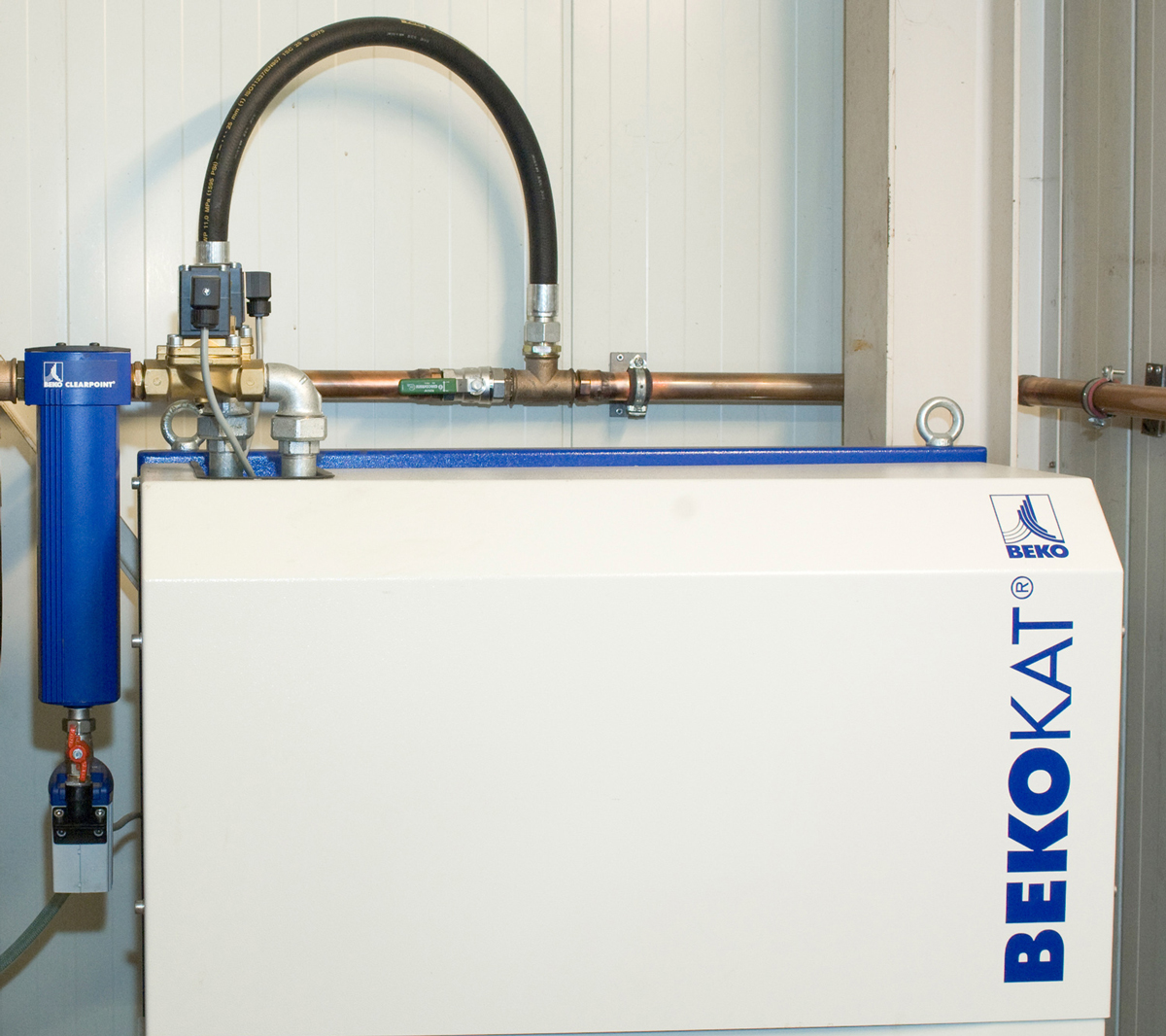
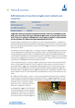