Tecnologia ad aria compressa nel settore degli imballaggi
Settore: | imballaggio, carta |
Cliente/luogo/anno: | Delkeskamp, Nortrup (Germania), 2008 |
Uso dell’aria compressa: | aria di pilotaggio, aria di processo, trattamento della condensa |
Prodotti installati: | EVERDRY, BEKOSPLIT |
Un settore da non sottovalutare: oltre 100 fabbriche specializzate con circa 19000 dipendenti creano ed elaborano in Germania il cartone ondulato. L'aria compressa e il suo trattamento giocano un ruolo centrale nel processo di produzione. Infatti, è soprattutto l’umidità nell'aria compressa ad avere conseguenze fatali per impianti, materie prime e prodotti finiti.
Con una produzione annuale di circa nove miliardi di metri quadrati di cartone ondulato, la Germania è il paese europeo al primo posto tra i produttori, e il quarto a livello mondiale dopo USA, Cina e Giappone. Praticamente tre quarti di tutte le merci trasportate in Germania vengono avvolte nel cartone ondulato - e quasi il 30 percento di tutti gli imballaggi così rivestiti attraversano i confini nazionali alla volta dei consumatori. Un’attività gigantesca, in continua crescita e quindi di grande rilevanza per tutta l’economia nazionale tedesca.
Uno dei pionieri, apripista e player fondamentale di questo ramo industriale è l’azienda Delkeskamp Verpackungswerke GmbH a Nortrup, in Bassa Sassonia. Fondata già nel 1896 come fabbrica di cartone, oltre che presso lo stabilimento principale di Nortrup, produce anche negli altri siti di Hannover e ad Odry, in Repubblica Ceca. Si producono carta, cartone ondulato e schiuma per imballaggi in molteplici colori.
Ciclo produttivo chiuso
Il materiale di partenza per la produzione di cartone ondulato è il cartone ondulato grezzo. La Delkeskamp GmbH produce la gran parte di questa materia prima in autonomia, presso lo stabilimento di Nortrup. In tal senso, questa sede è il primo anello di un ciclo di produzione chiuso e quindi di importanza fondamentale per la funzionalità e la redditività dell’intera struttura produttiva della Delkeskamp. Infatti, oltre ai vantaggi di natura puramente tecnico-produttiva, la generazione in proprio del cartone ondulato grezzo garantisce all’azienda anche un’indipendenza massima dal mercato degli appalti.
Da Delkeskamp si preferisce dunque camminare con le proprie gambe. Infatti, a Nortrup, persino il vapore necessario alla produzione di carta viene creato presso una propria centrale elettrica mediante moderne turbine. In questo processo si origina l’elettricità che supera anche il proprio fabbisogno - e che viene fornito alla rete pubblica. In questo modo non si copre solamente la necessità interna, bensì anche quella di altre famose aziende della Bassa Sassonia.
Oltre alla necessaria sicurezza di processo nella produzione, l’azienda ha anche una certa responsabilità per le persone che vivono nella regione. Attese, che vanno soddisfatte. In tal senso, uno dei pilastri è l’alimentazione stabile e qualitativamente elevata dello stabilimento con aria compressa - una fonte di energia decisiva da molti punti di vista per la produzione.
L’aria compressa come importante fonte di energia
A Nortrup vengono alimentati tre, anzi quattro, settori di attività. Essi sono principalmente la fabbrica di carta, la produzione del cartone ondulato e lo stabilimento della schiuma. Un altro, seppur con ridotto fabbisogno, spetta alla centrale elettrica propria.
Senza aria compressa, in pratica la Delkeskamp non potrebbe muoversi. Per capire questo passaggio, basta immaginare a grandi linee i cicli di produzione nelle tre aree di produzione: il cartone ondulato grezzo viene prodotto dalla carta da macero in una prima fase, all’interno di impianti produttivi giganti, altamente moderni, e, all’inizio, della realizzazione viene scaldata e inumidita. In questo modo raggiunge l’elasticità necessaria per essere conformata. Nella fase successiva, la carta viene condotta sotto la pressione e l'effetto del calore tra due rulli scanalati concatenati e dentati. Quindi, la carta ondulata viene innanzitutto incollata con il nastro di carta interno, dall’alto, e poi con quello esterno, dal basso - in questo modo il cartone ondulato dispiega tutto il suo ottimale effetto protettivo.
In procedimenti di lavoro completamente automatici, dai formati di cartone ondulato vengono creati scatole pieghevoli, imballaggi punzonati, imballaggi interni per imbottitura ed espositori. Il tutto viene spostato ovvero guidato mediante innumerevoli impianti pneumatici e anche mediante regolatori e barre azionati ad aria compressa. Se, in questa sequenza di produzione così ben coordinata, qualcosa resta imbrigliato, si possono avere effetti immediati sulla percentuale produttiva e soprattutto sulla relativa qualità.
Un aspetto fondamentale: aria compressa secca
Ciò di cui Delkeskamp ha maggiormente bisogno, oltre alla continuità dell’alimentazione, è l’aria compressa secca. La penetrazione di umidità nell’aria compressa è come veleno per gli impianti pneumatici e per i prodotti. Infatti, l’aria compressa umida non rappresenta un rischio solo per la carta e il cartone ondulato. Anche nella terza area di produzione di Delkeskamp, quella della schiuma, l’asciutto assoluto è d’obbligo.
Infatti, qui vengono prodotti singolarmente pezzi sagomanti progettati per i più disparati imballaggi, in polistirolo espanso (EPS). Ciò che comunemente è noto con il termine di “polistirene”, presso Delkeskamp si chiama “denopor” e completa il coerente concept di imballaggio del produttore.
In questa parte di attività, l’aria compressa viene usata tra le altre cose per l’esercizio dei macchinari che producono pezzi sagomati, per il movimento dei cilindri di posizionamento e il funzionamento delle valvole. A ciò si aggiunge la soffiatura di tali pezzi sagomati pronti dalle macchine. Poiché i pezzi pronti in denopor, soffiati via dalle macchine mediante aria compressa, vengono stivati in un padiglione non riscaldato, devono essere assolutamente asciutti. Infatti, con qualunque tipo di sollecitazione, questo materiale ha una reazione molto sensibile alle temperature gelide. Per natura poi, l’umidità aumenta ulteriormente questa sensibilità.
L’asciutto assoluto si trova quindi per la Delkeskamp Verpackungswerke GmbH in cima alla lista delle priorità quando si parla di fornitura di aria compressa. Lo stesso vale per l'ampliamento rivelatosi necessario dell’impianto di aria compressa presso la sede principale di Nortrup. Sin dal 2007, qui ci si espande e si investe abbondantemente nell’ingrandimento e nell’ammodernamento della produzione.
Elevato fabbisogno di aria compressa dopo l’ampliamento del sito
La postazione dell’aria compressa sinora esistente nella cosiddetta “cantina del compressore”, non poteva competere a livello di prestazione con questa crescita. I cinque compressori lì presenti più l’essiccatore ad adsorbimento a valle avevano infatti bisogno di maggiore potenza. Inoltre, un “componente vacillante” andava spedito finalmente alla rottamazione: il separatore olio-acqua statico, che da tempo non funzionava più come desiderava Delkeskamp.
La ricerca di una soluzione più moderna a questo problema ha portato Delkeskamp, dopo un’intesa analisi di mercato, a un interlocutore per loro del tutto nuovo: a BEKO TECHNOLOGIES GmbH, fornitore tedesco di sistemi per aria compressa.
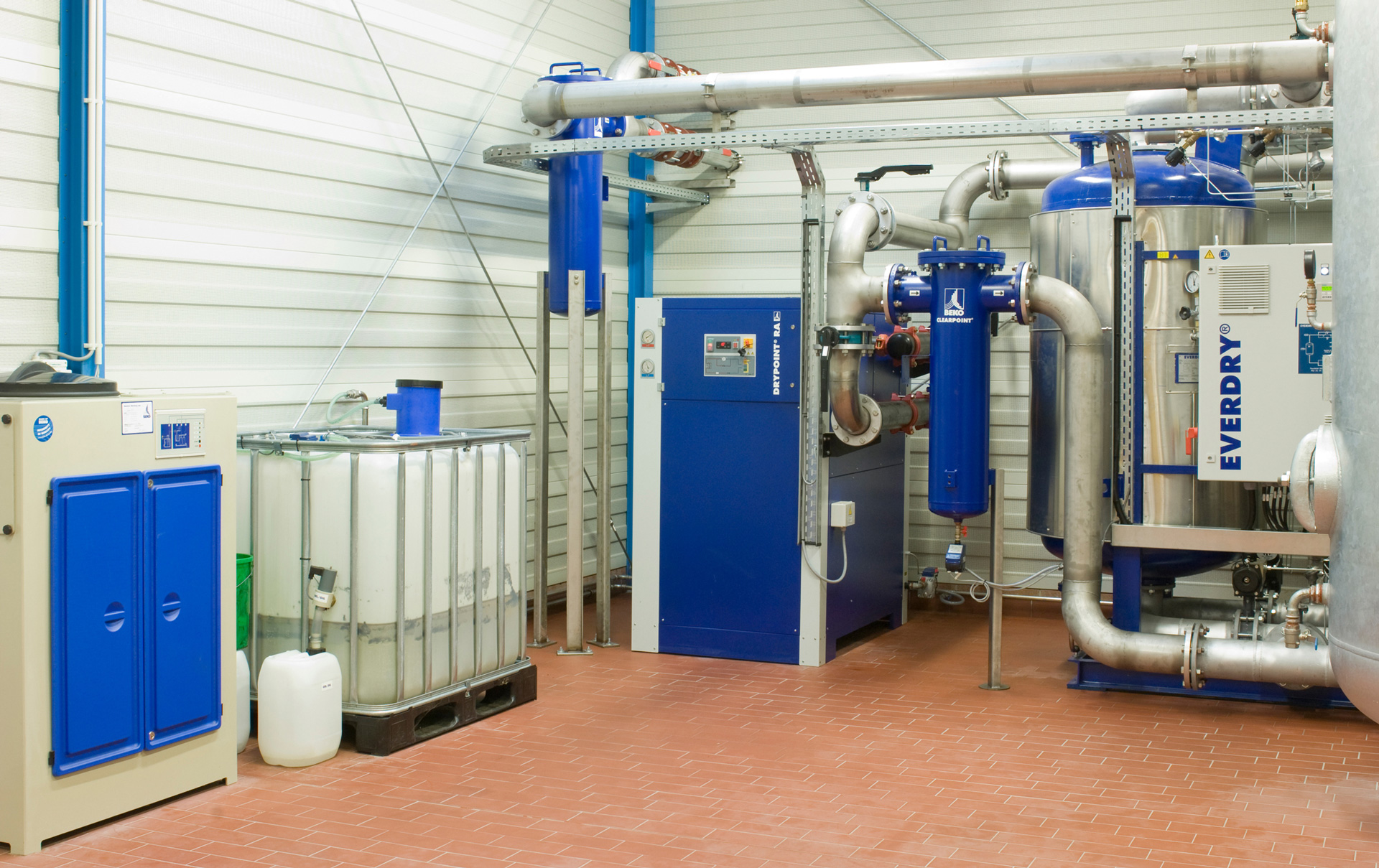
L’azienda con sede sul Reno, a Neuss, e attiva in tutto il mondo, aveva nel proprio programma una tecnologia per la separazione di emulsioni olio-acqua: BEKOSPLIT. Questi impianti di piroscissione ripuliscono condensati emulsionati, come si presentano nelle sfavorevoli condizioni di uscita oppure in determinate combinazioni di lubrificante-compressore. Oltre alla condensa dell’aria compressa, è possibile trattare anche altre acque reflue industriali contenenti olio. Inquinamenti organici non solubili in acqua - come oli, grassi vegetali oppure animali, nonché un gran numero di inquinamenti solidi, possono essere rimossi dall'acqua. Inoltre, metalli pesanti, sporco o particelle di colore eventualmente presenti vengono adsorbiti in modo affidabile.
In tale ambito, il principio alla base di BEKOSPLIT funziona in modo più efficace di un ultrafiltraggio: non sono necessari detergenti aggressivi e si consuma poca energia. L’investimento necessario è assolutamente gestibile e i lunghissimi intervalli di manutenzione stimolano ulteriormente la redditività.
Un sistema autoconservante
Da un semplice contatto con lo specialista dell’aria compressa BEKO TECHNOLOGIES, è nato ben altro. Infatti, da Delkeskamp, ci si è accorti subito che con BEKO TECHNOLOGIES si era trovato un partner che correva allo stesso ritmo del cliente. Che pensava in modo globale e che sviluppata concetti complessivi coerenti. La cosa iniziò a farsi interessante.
Soprattutto quando da BEKO TECHNOLOGIES si è iniziato a ripensare un tema così caro a Delkeskamp come l’essiccazione dell’aria compressa. Per esempio, riflettendo anche sulla redditività. Più si andava avanti col trasferire in gran parte il trattamento dagli essiccatori ad adsorbimento esclusivamente usati sino a quel momento a un essiccatore a freddo, più il tutto iniziava a prendere una giusta piega.
Nonostante per Delkeskamp, questo suggerimento poteva essere una vera rivoluzione di palazzo, l’azienda si è affidata al principio e alla sicurezza dell’essiccazione d’adsorbimento per la progettazione degli impianti. Se, da una parte, sino a quel momento non si erano avuti problemi e non si voleva andare incontro a rischi, dall’altra, l’idea di un essiccatore a freddo era enormemente allettante, guardando il bilancio energetico enormemente più vantaggioso grazie a questo processo rispetto all’essiccatore ad adsorbimento. Se allora, si potessero combinare entrambi...
Una sfida assolutamente fatta per il fornitore di sistemi BEKO TECHNOLOGIES. In pochi giorni, per Delkeskamp l’azienda ha sviluppato un concept coerente di sistema combinato ridondante tra essiccatore ad adsorbimento e a freddo. Da maggio 2008, tutto questo è realtà.
Questo sistema consente al produttore di imballaggi, a seconda di esigenze e condizione ambientale, per esempio stagionale, di mettere in moto una costellazione di essiccatori tanto sicura quanto conveniente. Come combinazione flessibile di entrambi i processi o esclusivamente come essiccazione d’asborbimento o a freddo.
Poiché le tubazioni dell’impianto ad aria compressa all’interno dell’area industriale scorrono ampiamente all'esterno mediante ponti di tubi, ovviamente a seconda delle stagione sono esposte a grandi oscillazioni di temperatura. Così, per esempio, per la protezione dalla ricondensa e dal congelamento in inverno, deve essere presente un punto di rugiada oltre i meno 40°. Affinché qui sia possibile ottenere la maggiore sicurezza di processo, gli essiccatori ad adsorbimento EVERDRY di BEKO TECHNOLOGIES sono dotati di corrispondenti unità per la misurazione dei punti di rugiada e di unità di controllo. Sinora, il tutto funziona perfettamente. La potenza di essiccazione è assolutamente stabile e il bilancio energetico è migliorato fortemente.
Nel frattempo, da Delkeskamp, nell’ormai moderno trattamento dell’aria compressa, si usano esclusivamente apparecchi di BEKO TECHNOLOGIES. Oltre agli impianti di piroscissione BEKOSPLIT, agli essiccatori ad adsorbimento EVERDRY nonché all'essiccatore a freddo DRYPOINT, anche i filtri CLEARPOINT offrono un servizio eccellente.
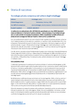