Trattamento della condensa per turbocompressori
Settore: | Metallo, acciaio |
Cliente/luogo/anno: | ThyssenKrupp Steel Europe, Duisburg, (Germania), 2011 |
Uso dell’aria compressa: | In produzione, tecnica di condensazione |
Prodotti installati: | BEKOMAT |
L'impianto per aria compressa nella sede centrale di Duisburg di ThyssenKrupp Steel Europe AG è lungo oltre dieci chilometri. Un sistema ampiamente ramificato, che viene alimentato in modo potente e affidabile. A farlo ci pensano degli eccezionali turbocompressori, che vengono accuratamente monitorati.
Qui, nulla è piccolo. Chi si immerge nell’enorme stabilimento di Duisburg di ThyssenKrupp Steel Europe AG, viene inondato in ogni punto da visioni immense. Dimensione e importanza odierna, questa tradizionale sede di produttori di acciaio le deve a ben 120 anni di storia. Attualmente, si tratta anche dello stabilimento con più personale in tutta la Germania.
ThyssenKrupp Steel Europe si concentra sul segmento in enorme crescita del pregiato acciaio piatto di qualità. La gamma di prestazioni va da soluzioni per materiali fino a trattamenti specifici per prodotti, servizi e manutenzione onnicomprensiva fino a componenti pronti e gruppi in acciaio. Grazie alla concentrazione della metallurgia e della parte prevalente della generazione di nastri laminati a caldo a Duisburg, nella regione della Rheinschiene si è creato un concept esclusivo in Europa. Che viene completato con efficienti attività di laminazione a freddo e rivestimento.
Come in quasi tutti i cicli industriali, anche l’aria compressa rientra le principali fonti energetiche. Al contempo, si tratta di un elemento centrale per la sicurezza del processo presso ThyssenKrupp Steel Europe AG. Ecco perché vi viene conferita un'attenzione particolarmente grande, così come al suo trattamento.
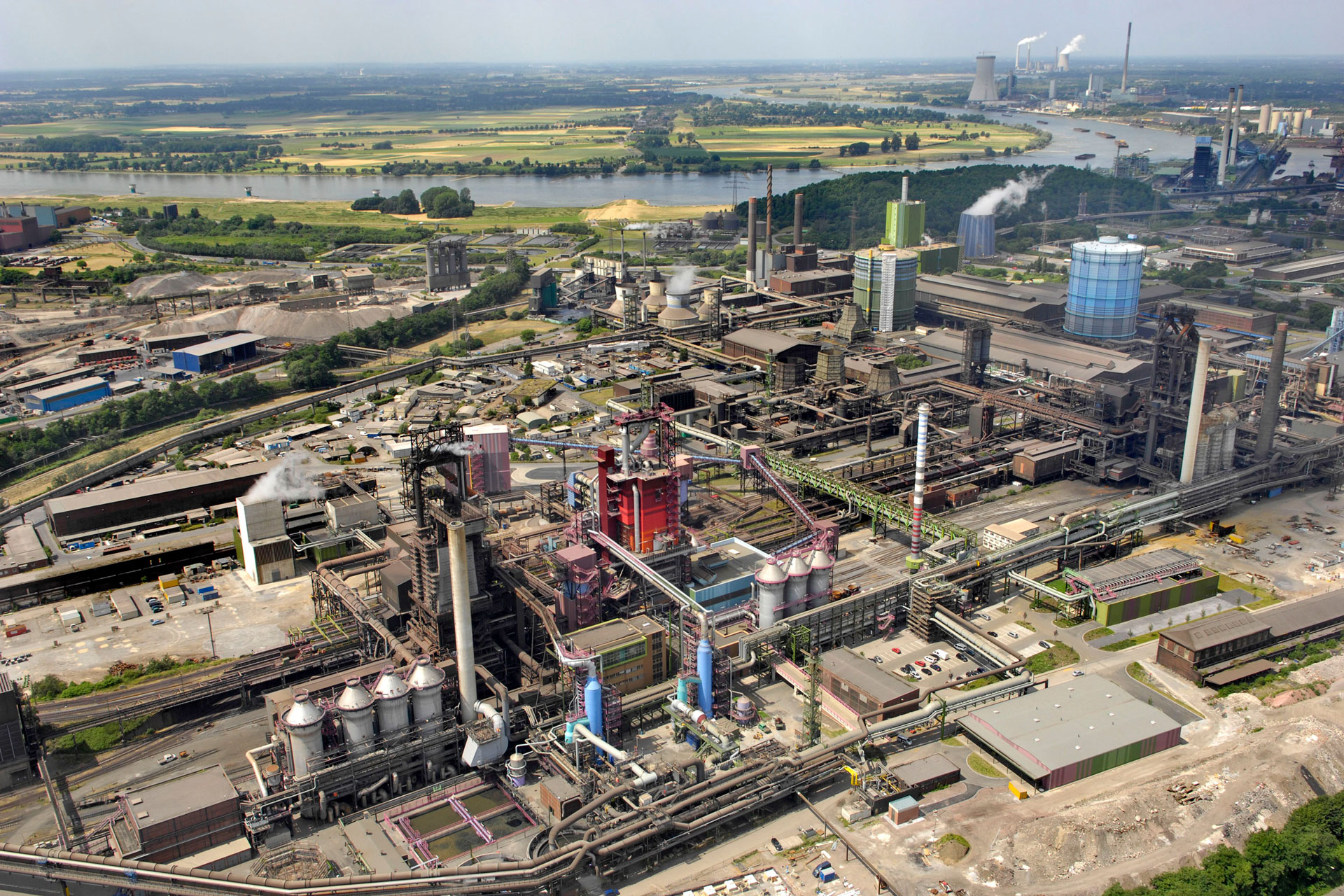
Non sono bazzecole
Un grande padiglione adibito ai compressori nel cuore dello stabilimento ospita una parte dei gruppi per la generazione e il trattamento dell’aria compressa. Tra questi ci sono tre turbocompressori con una potenza di compressione ciascuno di 25 000 m³ all’ora. Questo volume di complessivamente 75 000 m³ contribuisce a garantire il funzionamento di innumerevoli sistemi in tutto il tessuto produttivo. Come anche il comando delle valvole nel laminatoio - per menzionare solo un’area possibile. Basta quindi poco per immaginare quali enormi conseguenze potrebbero avere i guasti o fermi in queste aree aziendali per l’intero ciclo di produzione. Se un compressore si guasta, possono esserci gravi conseguenze.
Fino a metà 2010, tali difficoltà si sarebbero potute ripercuotere in modo particolarmente problematico sullo scarico della condensa. Qui, infatti, i potenti turbocompressori pongono speciali requisiti: ciascuno dei quattro livelli di compressione di un gruppo richiede uno proprio scarico della condensa. Sino a quel momento, lo scarico della condensa era stato manuale. Il suo monitoraggio avvenne mediante un controllo manuale e visivo.
Gli scaricatori di condensa meccanici usati presso i turbocompressori non potevano essere integrati al sistema di monitoraggio elettronico del trattamento dell'aria compressa. Era quindi impossibile un inserimento presso la sala di controllo centrale. Visto l’esigente concept di garanzia di qualità presso ThyssenKrupp Steel Europe AG questa situazione non era più accettabile da molto tempo. Infatti già in caso di guasto di uno scaricatore presso uno solo dei quattro livello di compressione, poteva comportare il guasto temporaneo del compressore. Nessun fornitore di tecnica d’aria compressa sembrava poter offrire impianti di compressione così potenti con scaricato di condensa capacitivi, elettronicamente monitorabili e a processo sicuro.
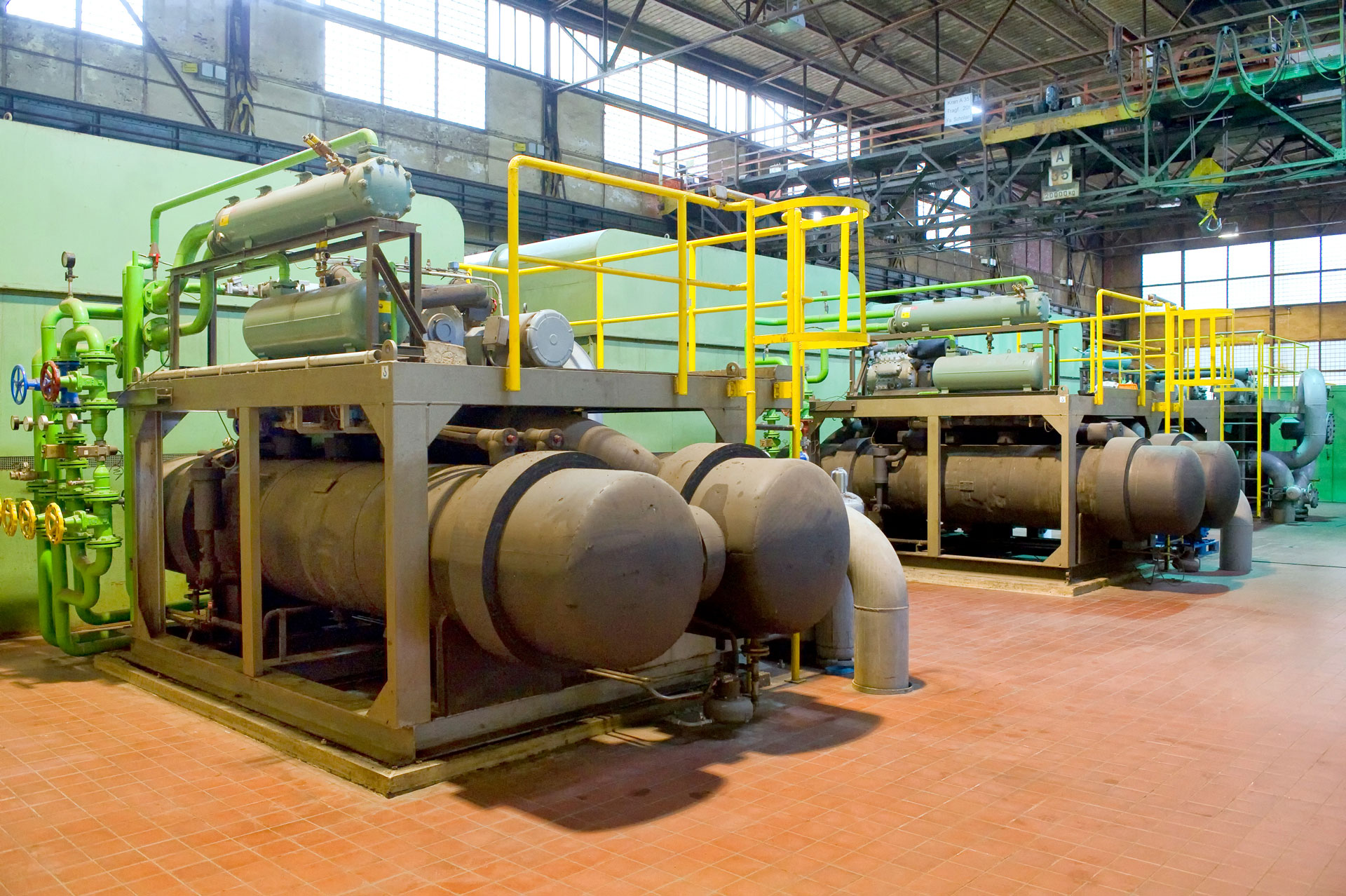
Scarico con livello elettronicamente regolato
Sollievo a questa pesante situazione si trovò finalmente in seguito al colloquio con il fornitore di sistemi d’aria compressa che nel 1982 aveva immesso sul mercato uno scaricatore di condensa con livello elettronicamente regolato: la tedesca BEKO TECHNOLOGIES GmbH con sede a Neuss am Rhein. Sin dall’inizio, e per molti anni, l’azienda si era concentrata su questo prodotto - il BEKOMAT - e lo stava anche corrispondentemente perfezionando per scopi d’uso più difficili.
Nel BEKOMAT a livello regolato non si trova - diversamente da quando si usa un galleggiante - alcun componente amovibile e in grado di subire guasti nel contenitore di raccolta della condensa. Questo incarico viene svolto infatti da un sensore capacitivo. Esso reagisce a qualunque tipologia di condensa ed è assolutamente insensibile allo sporco.
Questo rilevamento capacitivo del livello garantisce uno scarico adattato alla reale presenza di condensa, senza perdite di pressione. Si risparmia energia e non si genera alcuna emulsione. Le sezioni di scarico dalle grandi dimensioni garantiscono uno scarico sicuro anche in caso di condense molto sporche.
L’intelligente elettronica di controllo non garantisce solo lo scarico della condensa. Al contempo, serve al controllo completamente automatizzato dello stato dell’apparecchio. Gli errori vengono mostrati mediante LED direttamente sullo scaricatore e inoltre possono essere inoltrati, mediante un potenziale contatto, come messaggio di errore anche a punti di monitoraggio centrali.
Con queste caratteristiche, gli scaricatori di condensa BEKOMAT corrispondono esattamente al profilo di esigenza di ThyssenKrupp Steel Europe AG a Duisburg. A sorprendere fu soprattutto l’integrazione senza problemi nell'esistente sistema automatico di monitoraggio e guida.
Solo cinque settimane
All’inizio dell'estate 2010, gli specialisti di BEKO TECHNOLOGIES, in stretta collaborazione con il team tecnico di ThyssenKrupp Steel Europe installatore i primi quattro BEKOMAT di diverse dimensioni presso un turbocompressore. Solo quando si fu certi che la configurazione funzionasse bene sin nei dettagli, ci si dedicò agli altri due gruppi.
Tuttavia, non trascorse molto tempo: nell’arco di sole cinque settimane tra prima configurazione modello e “riavvio” completo, l’intero scarico della condensa era stato ammodernato con sicurezza.
Ulteriori BEKOMAT con livello elettronicamente regolato si trovano pressi i diversi essiccatori a freddo del sistema d’aria compressa.
Grazie all’affidabilità del processo così aumentata, al rigido concept di sicurezza presso ThyssenKrupp Steel Europe viene aggiunto un ulteriori pilastro. Anche i futuri sviluppi nel sistema d’aria compressa non avrebbero rappresentato alcun problema per i responsabili.
Infatti, tutte le varianti del BEKOMAT continuano a essere adattati ai parametri chiavi dei comuni compressori ed essiccatori. Questi cambiano continuamente e seguono i requisiti di potenza posti dal trattamento industriale di aria compressa.
Tecnica con futuro garantito
Così, presso BEKO TECHNOLOGIES, per esempio, con la quinta generazione della serie appena presentata, ovvero i modelli 31 e 32, si è raggiunta nel frattempo l’economicità attualmente ottimale. Questi apparecchi hanno in serbo un principio costruttivo completamente nuovo per quanto riguarda gli scaricatori di condensa a livello elettronicamente regolato, con elevati vantaggi in fase di manutenzione.
Sono infatti suddivisi in soli due moduli: la Service Unit che, nell’alloggiamento in alluminio estremamente resistente alla corrosione unisce tutti i componenti non sottoposti a usura e manutenzione, e nell’unità di comando e sensoriale elettronica che necessita esclusivamente di essere installata. Entrambi i gruppi costruttivi sono accoppiati mediante un pratico raccordo rapido.
Tale configurazione consente la sostituzione assolutamente semplice di tutti i componenti rilevanti per la manutenzione e il consumo, basta infatti un rapido cambio della Service Unit. Per separare e collegare entrambi i moduli non è necessario alcun utensile - basta un semplice tocco.
Anche se attualmente questa soluzione non viene ancora usata in impianti con volumi di aria compressa enormi come accade per ThyssenKrupp Steel Europe AG. Per la sede di Duisburg si tratta di un’ottima prova del piacere di sviluppo di suoi fornitori di sistema.
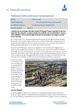