Trattamento dell’aria compressa sulle locomotive ibride
Settore: | trasporto, locomotive |
Cliente/luogo/anno: | ALSTOM, Stendal (Germania), 2013 |
Uso dell’aria compressa: | aria di pilotaggio, aria di processo |
Prodotti installati: | CLEARPOINT, DRYPOINT M, BEKOMAT, ÖWAMAT |
Un concetto di tendenza nel settore automobilistico, una tecnologia già collaudata su rotaia: la trazione ibrida. Fino al 50 per cento di risparmio di carburante sulle moderne locomotive grazie alla combinazione tra generatore diesel e batteria. Sempre a bordo, un sistema di trattamento dell’aria compressa complesso e “mobile” per il funzionamento dei freni idraulici.
Se i ferrovieri potessero scegliere il loro posto del cuore, Stendal, vicino Magdeburgo, avrebbe ottime possibilità di essere scelta come tale. Infatti, su questo territorio ricco di tradizione, in padiglioni altrettanto storici, nascono da decenni quei giganti in ferro che mettono in moto il traffico su rotaia: le locomotive di ALSTOM. Qui viene costruita anche la locomotiva di manovra più intelligente e dai consumi parsimoniosi: un ibrido con generatore diesel combinato e batteria.
Il Gruppo francese ALSTOM, presente a livello internazionale, è leader nel mondo per la costruzione di impianti e prodotti destinati alla generazione di corrente, alla trasmissione di energia e all’infrastruttura ferroviaria. Il Gruppo è costruttore di un treno velocissimo, della metropolitana automatizzata più potente al mondo e, nella cittadina tedesca di Stendal, della pionieristica locomotiva ibrida.
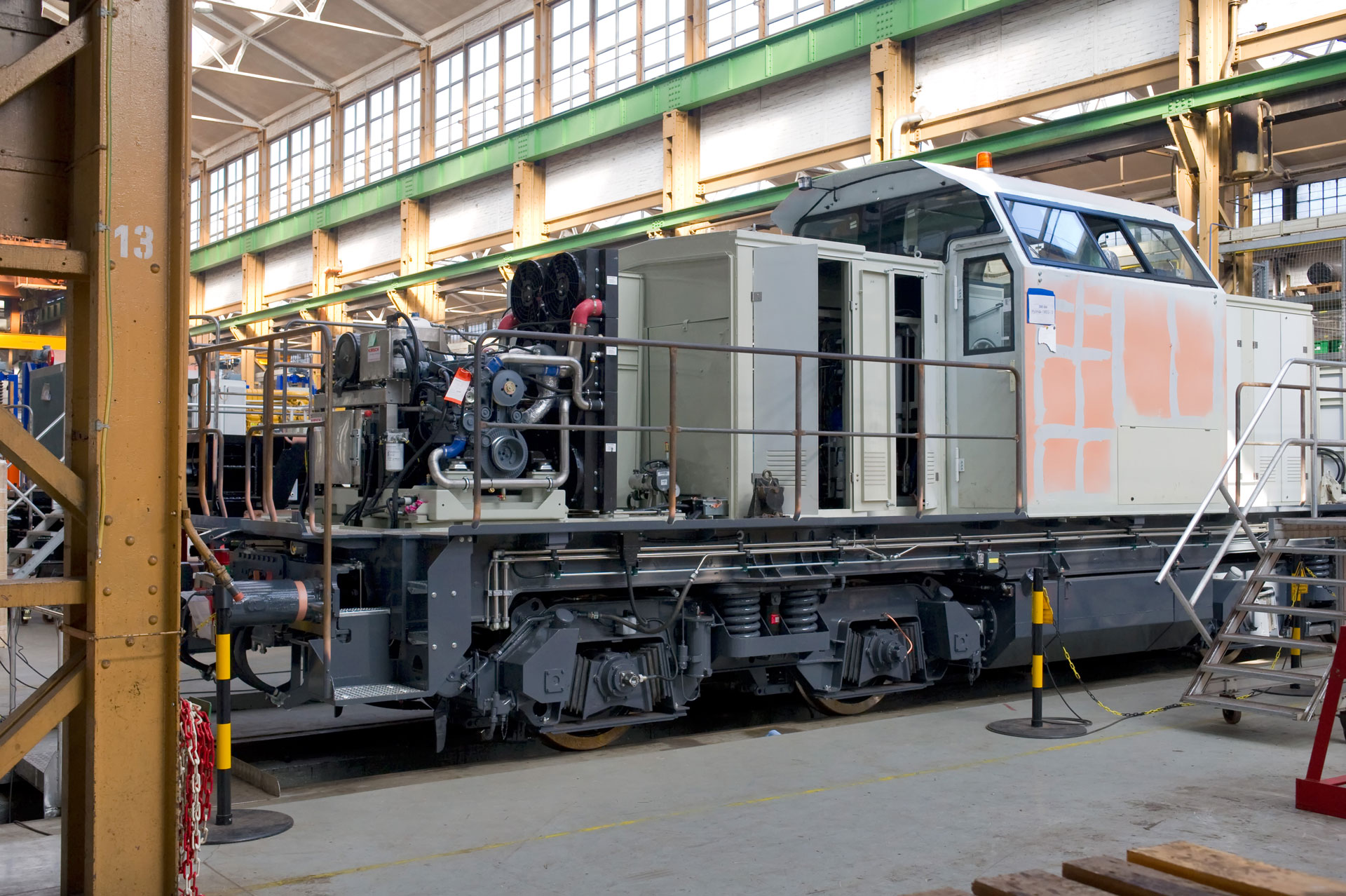
Proprio qui, nella sede dell’ALSTOM Lokomotiven Service – un’impresa comune in collaborazione con Deutsche Bahn AG, già nel 2006 prese forma il concept di una trazione combinata. Quell’anno, gli ingegneri ALSTOM misero su rotaie i primi prototipi pronti alla guida della locomotiva di manovra ibrida, creata sul telaio della comprovata locomotiva V100 con i suoi due carrelli snodati. Oltre al tipico generatore elettrico a diesel, a bordo venne aggiunta una grande batteria che serviva a immagazzinare energia - nonché un impianto sviluppato da zero per gli impianti frenanti di locomotiva e vagoni agganciati.
Dai prototipi alla produzione di serie
Da ALSTOM, si è fieri delle “strutture in acciaio” - soprattutto della loro potenza e parsimonia. Il principio alla base: la versione ibrida della locomotiva di manovra è dotata di un generatore diesel da 230 kW e di una batteria. Con una tale progettazione, si adatta in modo particolare a smistamenti difficoltosi. Un generatore diesel molto economico ed ecologico carica la batteria e può azionare anche direttamente il motore elettrico in caso di carichi massimi. Con carico parziale, la locomotiva funzione a batteria, risparmiando così, in questa variante, dal 30 al 50 percento del diesel rispetto alle comuni locomotive di manovra da 700 kW. Questa forzuta locomotiva ibrida si muove grazie alla forza di trazione allo spunto da 220 kN e con una velocità massima di 60 km/h su quattro assi.
Durante lo smistamento, con i suoi cambiamenti di carico e direzione del caso, l’impianto frenante di una locomotiva è particolarmente sollecitato. Ecco perché, sin dalla primissima fase di sviluppo degli ibridi, alla potenza e alla stabilità del trattamento dell'aria compressa è stata riservata assoluta attenzione.
Trattamento dell'aria compressa direttamente a bordo
La produzione di aria compressa per l’impianto frenante della macchina e dei vagoni agganciati avviene completamente in modo autonomo a bordo di ciascuna locomotiva. Il tutto, presso una postazione dell'aria compressa “mobile” dietro la cabina del macchinista. Fino alla copertura, essa si trova praticamente “all’aperto”, quindi è costantemente esposta alle intemperie e alle condizioni climatiche; affronta le manovre di smistamento sia sotto zero che con la cocente calura estiva; nelle campagne nordiche oppure nelle terre caldo-umido dell’emisfero sud o in Asia. Quindi, la tecnica del trattamento dell'aria compressa è sottoposta a enormi sfide: nulla può essere lasciato al caso.
Proprio in questo contesto, presso la sede ALSTOM a Stendal, sin dalla fase di progettazione ci si è rivolti allo specialista di questa categoria di dispositivo a bordo: il fornitore tedesco di sistemi per aria compressa BEKO TECHNOLOGIES GmbH con sede a Neuss, che ha invitato i propri ingegneri dal Reno all’Elba, affinché anche i capitolati d’onere così disparati di questo incarico potessero entrare a far parte della storia dello sviluppo del progetto. Sin da subito fu chiaro che, oltre alla combinazione dei componenti di trattamento presenti, andavano sviluppati anche versioni di dispositivi completamente nuovi - soprattutto riguardo alla separazione olio-acqua.
Un capitolato d’oneri enorme per gli ingegneri dell’aria compressa
Sin dall’inizio, BEKO TECHNOLOGIES ha guidato lo sviluppo del sistema per la locomotiva ibrida di ALSTOM. Un’ulteriore sfida: durante lo smistamento, le locomotive, naturalmente, si trovano per lungo tempo in una sola posizione. Con temperature sotto lo zero, si nasconde il pericolo che la condensa possa congelare all’interno del sistema di trattamento dell'aria compressa. Quindi, tutti i componenti e i condotti rilevanti sono stati dotati di un sistema di riscaldamento. Inoltre, tutti gli scaricatori di condensa installati sono stai collegati al comando del compressore. In questo modo, nel caso di guasto o spegnimento del sistema elettrico della locomotiva, la condensa residua ancora presente nel sistema può essere telecomandata e scaricata automaticamente, prima che congeli.
Mediante lo scaricatore di condensa BEKOMAT, essa viene condotta alla separazione olio-acqua direttamente in un dispositivo di trattamento della condensa ÖWAMAT. Questi apparecchi sviluppati da BEKO TECHNOLOGIES tengono conto della tutela dell’ambiente e delle acque, rispettando un approccio del tutto sostenibile.
Il loro sistema a cartucce è inoltre facilissimo da usare. Consente infatti una sostituzione veloce del filtro e facilita lo smaltimento con pochi residui. Inoltre, la durata di questi filtri è di gran lunga maggiore rispetto a quella dei comuni filtri ai carboni attivi. Grazie all’elevata qualità produttiva, si originano inoltre intervalli di manutenzione prolungati, un’esigenza, questa, fondamentale di ALSTOM per l’impiego “mobile” e assiduo sulle locomotive. Appositamente per questo cliente, BEKO TECHNOLOGIES ha dotato i separatori olio di un alloggiamento in acciaio inossidabile e particolarmente robusto.
Sistema completo in uno spazio ridotto
Il separatore olio-acqua è tuttavia solamente l’ultimo passaggio del sistema di trattamento dell’aria compressa della locomotiva ibrida dalla realizzazione dinamica. Immediatamente dietro il compressore a vite si trova il separatore a ciclone CLEARPOINT installato con il primo scaricatore di condensa. Infatti, ogni millimetro conta nello spazio ridotto della locomotiva. Il piccolo alloggiamento dell’impianto frenante occupa quasi la superficie di una casetta da giardino per attrezzi, lo stesso in altezza.
Tuttavia, accanto al compressore e al separatore a ciclone c’è spazio a sufficienza per un microfiltro nel separatore di condensa nonché per ben due essiccatori a membrana DRYPOINT M di BEKO TECHNOLOGIES. Uno di questi nella versione “plus”, con nanofiltro integrato.
L’essiccatore a membrana DRYPOINT M si basa sulla tecnologia “Twist 60” sviluppata da BEKO TECHNOLOGIES. L’elemento a membrana è costituito da strati sovrapposti di fibre cave, disposte in un tubo carotiere interno. Questa configurazione rappresenta un utilizzo altamente efficiente dei principi fisici attivi e consente l'essiccazione dell'aria compressa con ridotto consumo energetico. Per il processo di essiccazione, viene continuamente separata una percentuale di aria compressa nell'area di uscita dell’elemento a membrana e rilasciata atmosfericamente, quindi usata come aria di rigenerazione oppure di lavaggio.
Quando si viaggia sui binari
Sono proprio questi punti di forza dell’essiccatore a membrana ad aria compressa DRYPOINT M a risultare irrinunciabili sulla locomotiva ibrida: assoluta sicurezza funzionale, maggiore affidabilità e disponibilità immediata di aria compressa secca anche in caso di lavoro discontinuo. Inoltre: non c’è bisogno di manutenzione, né di preoccuparsi dell’usura, poiché non sono presenti componenti mobili. Ovviamente non è possibile ospitare un installatore di impianti frenanti su ogni locomotiva; ecco perché il sistema deve funzionare, essere resistente e privo di guasti. Ed è proprio quello che succede sinora sulle locomotive ibride ALSTOM.
![[Translate to Italia:] awb_alstom_it.pdf](/fileadmin/_processed_/5/6/csm_awb_alstom_it_42c8388347.png)