Koeling van lasersnijmachines met perslucht
Branche: | lasertechnologie |
Klant/Plaats/Jaar: | Horstmann, Verl (Duitsland), 2008 |
Toepassing van de perslucht: | proceslucht |
Geïnstalleerde producten: | BEKOKAT |
Het lasersnijden is een thermisch procedé. Dat is niet pas op het focuspunt herkenbaar, daar waar de laserstraal op het te snijden materiaal valt. Al in de stralenbundel daarvoor gaat het er heet aan toe. Hier is afkoeling gewenst. Het best en meest economisch door perslucht. Die moet echter wel absoluut olievrij zijn.
Bij Horstmann GmbH & Co. KG met zetel in Verl bij Gütersloh wijdt men zich aan de hoogkwalitatieve en veeleisende metaalbewerking voor gerenommeerde klanten uit tal van nijverheidstakken, waaronder de automobiel- en scheepsbouwindustrie en de machine-, installatie-en gereedschapsbouw.
De bij Horstmann onvermoeibaar werkende lasersnijmachines zouden uiterst allergisch reageren op zelfs maar een minimale olievervuiling door perslucht. En wel met een duidelijke afname van prestaties en kwaliteit. Omdat hun vlijmscherpe laserstraal letterlijk tot een flauw flakkerend ‘olielichtje’ zou worden gedegradeerd. In tegenstelling tot wat men misschien denkt wordt de perslucht aan de lasersnijmachines bij Horstmann namelijk niet gebruikt voor de pneumatiek, maar uitsluitend voor de koeling van het traject van de laserstralen.
In principe bestaat een snijmachine met CO2-laser uit een stralenbron met een beweeglijke focusseeroptiek, meestal een holle spiegel of een verzamellens. Vanuit de bron wordt de laserstraal via omkeerspiegels naar de bewerkingsoptiek geleid. Daar wordt de laserstraal gefocusseerd en zo de voor het snijden vereiste vermogensdichtheid gegenereerd. Bij Horstmann, waar voornamelijk roestvrij stalen platen worden gesneden, is dat tot wel zes kW straalvermogen. Genoeg overigens om een menselijk lichaam moeiteloos compleet te doordringen.
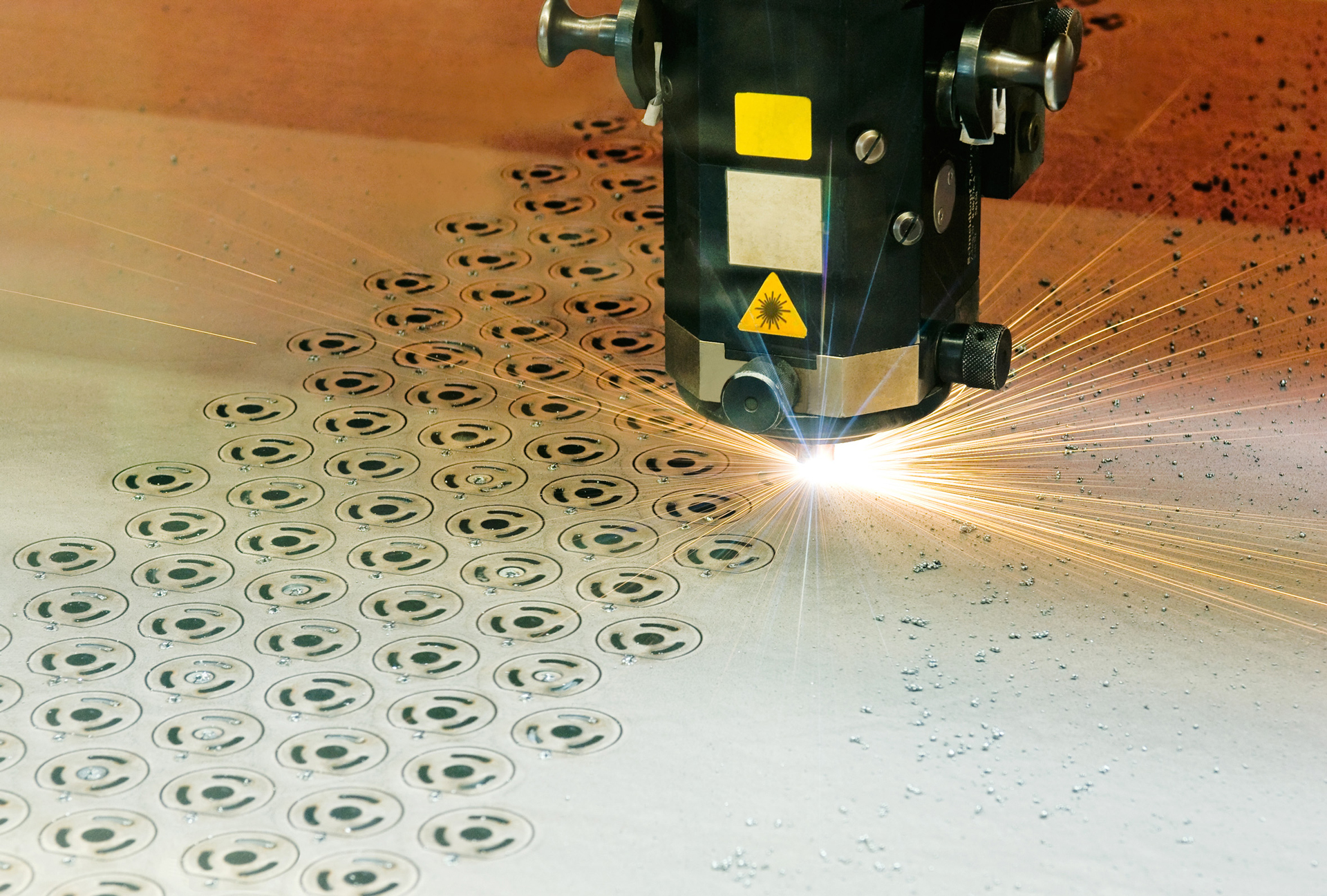
Doordat de beweeglijke ‘vliegende’ optiek over de te bewerken plaat beweegt, verandert voortdurend de afstand tot de vaststaande laserbron. De gegenereerde laserstraal bezit echter niet de vereiste parallelliteit om hem over te dragen over de deels grote en veranderlijke afstanden. Daarom, en ook om de thermische belasting van de omkeerspiegels te verlagen, wordt hij deels met een spiegeltelescoop wijder gemaakt.
De eigenlijke geleiding van de stralen tussen de laserbron en de focusseeroptiek gebeurt via met goud of molybdeen gecoate spiegels, die meestal ofwel van zuiver koper of van monokristallijn silicium zijn gemaakt. En die bovendien uiterst gevoelig reageren op olie respectievelijk aerosolen, die zich daarop afzetten en een vroegtijdige, erg dure vervanging noodzakelijk maken.
In de hele stralengang van de laser treden natuurlijk erg hoge temperaturen op. Zonder koeling zouden de hier ingezette materialen, bijvoorbeeld de omkeerspiegels en nog sneller de vouwbalg van de beweeglijke optische eenheid, aanzienlijke schade oplopen.
Voor deze cruciale koelfunctie zorgt in de stralengang ingeblazen perslucht. Deze moet absoluut vrij van stofdeeltjes en olie en droog zijn, om noch de laserstraal door zwevende deeltjes te ‘verstrooien’ noch de omkeerspiegels door afzettingen te vervuilen. Ook maar de geringste aandelen olie of aerosolen in de perslucht zouden snel fatale gevolgen voor de proceszekerheid en rentabiliteit van de snij-installatie hebben.
Beide factoren zijn echter – samen met absolute productkwaliteit – voor Heinrich Horstmann GmbH & Co. KG wezenlijke factoren voor het aanhoudende zakelijk succes. Daarom wijdt men aan het thema persluchtbehandeling daar ook enorm veel aandacht.
Tot op heden probeerde men bij Horstmann – zoals overigens bij nagenoeg alle gebruikers van perslucht met gelijkaardige eisen – olievrije perslucht te produceren door relatief kostbare, vaak zelfs met elkaar gekoppelde op verdichters, filters en drogers gebaseerde technieken. Vaak lukt dat echter slechts met meer of minder grote betrouwbaarheid.
Ook bij Horstmann vond men nooit een oplossing die echt tot tevredenheid stemde, vooral niet na de aanschaf van nieuwe, nog krachtigere snij-installaties. Begin 2008 stuitte men op een door de Duitse persluchtspecialist BEKO TECHNOLOGIES GmbH ontwikkeld katalyse procedé voor het genereren van absoluut olievrije perslucht. Het BEKOKAT gedoopte procedé ontsloot de weg naar absoluut olievrije perslucht met een compleet ander technologisch uitgangspunt dan alle oplossingen tot dan toe: met de katalyse.
Totale oxidatie van koolwaterstoffen
In principe realiseert het BEKOKAT systeem een totale oxidatie van koolwaterstoffen en daarmee een absoluut olievrije perslucht. En wel in één geconcentreerde, omvattende processtap na de verdichting. Zo gebeurt het complete ontoliën van de perslucht in nog maar één enkele component van de installatie. Deze werkt onafhankelijk van de omgevingsvoorwaarden, de olie-ingangsconcentratie en de relatieve vochtigheid van de perslucht.
BEKOKAT bekommert zich om alle verontreinigingen in de door de verdichter toegevoerde perslucht. Dat zijn doorgaans smeermiddelen, olies, zwaveldioxide, koolmonoxide, nitrogene gassen enz. Deze zijn aanwezig in de vorm van zowel gas als damp en aerosol. Door het BEKOKAT procedé worden zulke bestanddelen in de lucht volledig omgezet in kooldioxide en water.
Dit laatste kan zonder bezwaren en zonder verdere maatregelen ter bescherming van het milieu worden afgevoerd in het rioleringsnet. Zelfs het bij de afkoeling van de perslucht gevormde condensaat is dankzij het katalyse procedé absoluut olievrij, en kan zonder behandeling eveneens in de riolering stromen. Deze totale oxidatie en absoluut restloze werkwijze realiseert momenteel geen ander procedé.
Als katalysator dient een granulaat in de BEKOKAT, dat via verwarmingselementen wordt opgewarmd tot een bedrijfstemperatuur van ongeveer 150 graden Celsius. In de katalysator worden de oliemoleculen zo lang gebroken, tot er nog maar één koolstofatoom overblijft. In de eindfase van de katalyse zijn de oliemoleculen geoxideerd tot H2O en CO2.
Wezenlijk is dat de koolwaterstofketens, dus de oliemoleculen, op elk willekeurig punt kunnen worden ‘geknakt’. Ze worden steeds zo lang opgebroken, tot alleen nog kooldioxide en waterstof overblijven. De koolwaterstofketens van verschillende lengte uit olievrije en oliegesmeerde compressoren vormen dus voor BEKOKAT geen enkel probleem.
Evenmin altijd geweten is dat de anders vaak ingezette actieve koolfilters geen polaire verbindingen, zoals olefines, alcohol, glycol of keton kunnen adsorberen. Het BEKOKAT systeem verwijdert daarentegen ook deze stoffen volledig uit de perslucht. In het verdere BEKOKAT procesverloop wordt de gezuiverde perslucht in een warmtewisselaar tot circa 10 tot 15 graden Celsius boven inlaat afgekoeld en staat dan voor de betreffende toepassing ter beschikking.
Met het BEKOKAT procedé is het voor het eerst mogelijk om constant absoluut olievrije perslucht met een maximaal restoliegehalte van een nauwelijks nog meetbare 0,003 milligram per kubieke meter verdichte lucht te bereiden. Een kwaliteit dus zoals deze op de uiterst veeleisende gebieden van de geneeskunde en farmacie en bij de verwerking en verpakking van levensmiddelen nodig is.
Economisch uiterst voordelig is ten slotte ook de enorme standtijd van het speciale BEKOKAT granulaat, dat pas na goed 20.000 bedrijfsuren hoeft te worden vervangen. In vergelijking daarmee is de levensduur van een actieve koolfilter zelfs onder perfecte operationele voorwaarden al na ongeveer 500 bedrijfsuren uitgeput.
Sinds de vroege zomer van 2008 wordt het BEKOKAT systeem bij de metaalverwerker Horstmann de klok rond zonder storingen ingezet. En een goed milieugeweten krijgt Horstmann GmbH & Co. KG op de koop toe: want sinds de inzet van de BEKOKAT kan het condenswater uit de persluchtinstallatie probleemloos en zonder dure zuivering rechtstreeks in de riolering worden afgevoerd.
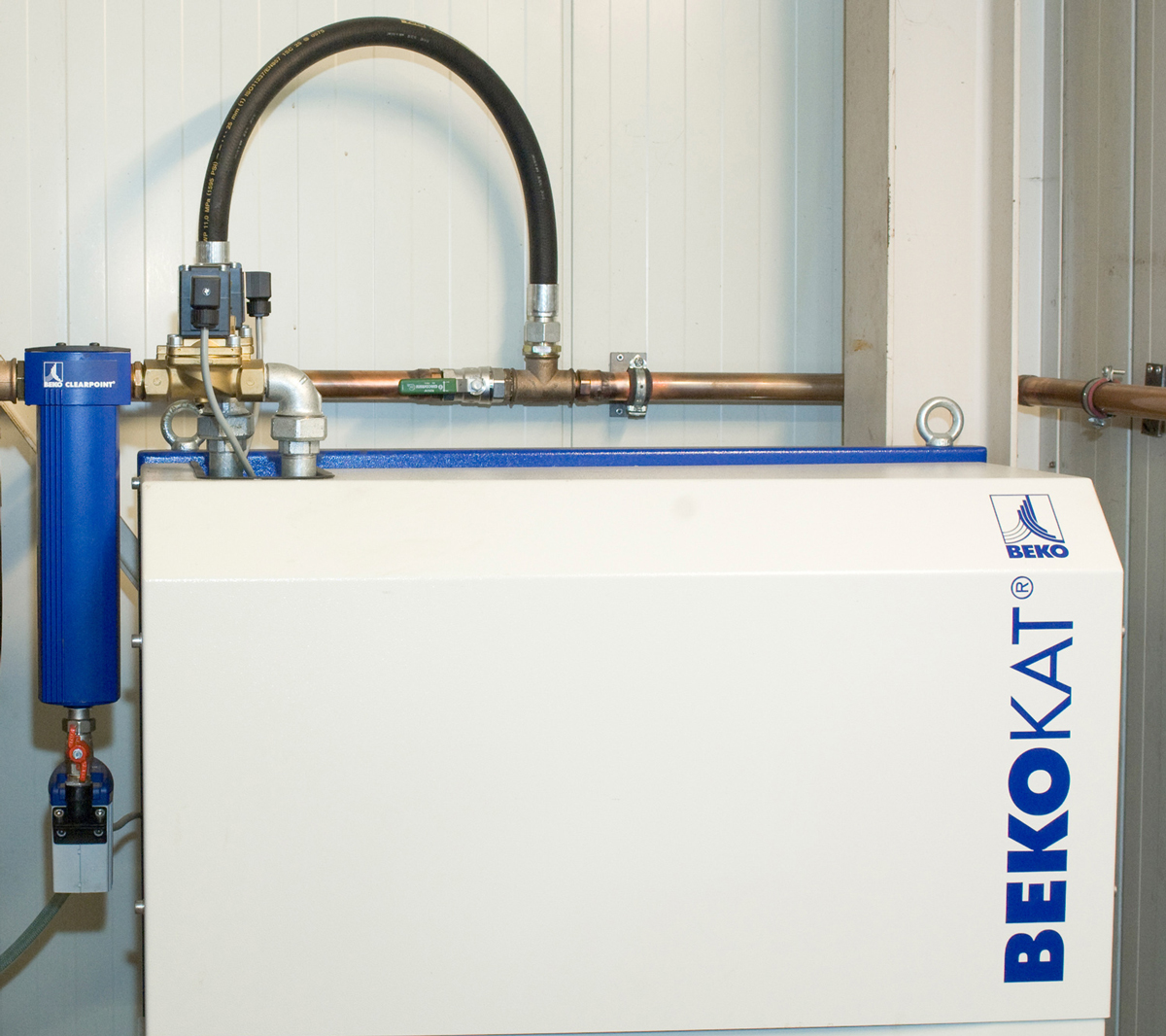
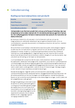