Persluchttechniek in de verpakkingsindustrie
Branche: | verpakking, papier |
Klant/Plaats/Jaar: | Delkeskamp, Nortrup (Duitsland), 2008 |
Toepassing van de perslucht: | regellucht, proceslucht, condensaattechniek |
Geïnstalleerde producten: | EVERDRY, BEKOSPLIT |
Deze industrietak is niet van slap karton: meer dan 100 daarin gespecialiseerde fabrieken met zo’n 19.000 medewerkers fabriceren in Duitsland golfkarton en verwerken dit. Perslucht en de behandeling daarvan spelen een centrale rol in het productieproces. Vooral vocht in de perslucht zou fatale gevolgen hebben voor installaties, ruwe materialen en afgewerkte producten.
Met een jaarlijkse productie van bij benadering negen miljard vierkante meter golfkarton ligt Duitsland in Europa op de eerste plaats en komt in de internationale vergelijking achter de VS, China en Japan op plaats 4. Nagenoeg drie vierde van alle getransporteerde goederen in Duitsland zijn inmiddels onderweg in golfkarton – en bijna 30 procent van alle gevulde golfkarton verpakkingen steken de landsgrenzen over op hun weg naar de consument. Big business dus, die cirkels trekt en daarmee voor de hele Duitse economie van evenredig groot belang is.
Een van de pioniers, gangmaker en drijvende kracht van deze industrietak is Delkeskamp Verpackungswerke GmbH in het Neder-Saksische Nortrup. Al in 1896 opgericht als kartonfabriek produceert deze behalve in de moederfabriek Nortrup tegenwoordig in andere productievestigingen in Hannover en in het Tsjechische Odry. Gefabriceerd worden papier, golfkarton en schuimstof voor verpakkingen van veelvuldige couleur.
Gesloten productiekringloop
Het uitgangsmateriaal voor de fabricage van golfkarton is het ruw papier. Delkeskamp GmbH fabriceert het verreweg grootste deel van het ruw papier dat nodig is zelf in de fabriek Nortrup. In die zin is deze vestiging de eerste schakel in een gesloten productiekringloop – en voor het goede functioneren en de rentabiliteit van de hele Delkeskamp productiestructuur van cruciaal belang. Want naast louter productietechnische voordelen verzekert de eigen productie van ruw papier voor golfkarton de onderneming ook een maximale onafhankelijkheid van de markt.
Bij Delkeskamp staat men sowieso al graag op eigen benen. Zo wordt in Nortrup zelfs de voor de productie van papier benodigde stoom door middel van moderne gasturbines gegenereerd in een eigen krachtcentrale. In dit proces ontstaat elektriciteit in een hoeveelheid, die de eigen behoefte duidelijk overschrijdt – en het openbare net wordt toegevoerd. Zo voorziet men niet alleen in de eigen behoefte aan energie, maar is men bovendien erkend energieleverancier in Neder-Saksen.
Naast de absolute proceszekerheid in de eigen fabricage heeft de onderneming dus ook nog een zekere verantwoordelijkheid tegenover de mensen in de regio. Verwachtingen waaraan men moet voldoen. Een van de hoekstenen daarvoor is de stabiele en kwalitatief hoogwaardige voorziening van de fabriek met perslucht – een voor de productie in tal van opzichten doorslaggevende energiedrager.
Perslucht is doorslaggevende energiedrager
In Nortrup worden drie – eigenlijk vier – bedrijfstakken voorzien van perslucht. Dat zijn in hoofdzaak de papierfabriek, de productie van golfkarton en de schuimstof fabriek. Nog een andere, hoewel verreweg geringere vraag, valt ten deel aan de eigen krachtcentrale.
Zonder perslucht zou zich bij Delkeskamp praktisch niets bewegen. Om dat te begrijpen hoeft men zich alleen maar de grof geschetste productieprocessen in de drie domeinen voor te stellen: het in de eerste stap in reusachtige, ultramoderne productie-installaties uit oud papier gefabriceerde ruw papier voor golfkarton wordt in de eerste fase van de kartonproductie verwarmd en bevochtigd. Zo bereikt het de vereiste elasticiteit om gevormd te kunnen worden. In de volgende stap wordt het papier onder druk en inwerking van hitte door twee tandwielachtig in elkaar grijpende geribde walsen heen geleid. Dan wordt het gegolfde papier eerst met de binnenbaan van boven en dan met de buitenbaan van beneden vastgeplakt – daardoor kan het golfkarton zijn optimale beschermende werking ontplooien.
In volledig geautomatiseerde werkcycli worden uit de formaten golfkarton dan vouwdozen, stansverpakkingen, opvullende binnenverpakkingen en displays gefabriceerd. Dat alles wordt via talloze pneumatische installaties en ook door perslucht geactiveerde regelaars en schuiven bewogen respectievelijk aangestuurd. Wanneer ergens in deze fijn op elkaar afgestemde productiestappen iets geklemd blijft zitten, dan heeft dat onmiddellijke gevolgen voor de productiecijfers en vooral voor de kwaliteit van de fabricage.
Het belangrijkste: droge perslucht
Wat Delkeskamp vooral nodig heeft, naast de continuïteit van de toevoer, is droge perslucht. In de perslucht gedrongen vocht is puur vergif voor de pneumatische installaties en voor de producten.
Daarbij vormt vochtige perslucht lang niet alleen voor papier en golfkarton een risico. Ook in het derde productiedomein van Delkeskamp, de schuimstof productie, is droogheid een must. Hier worden individueel voor verschillende verpakkingen ontworpen vormdelen gefabriceerd uit expanderend polystyreen (EPS). Wat in de volksmond bekend staat onder het begrip piepschuim, heet bij Delkeskamp Denopor en rondt het naadloze verpakkingsconcept van de fabrikant af.
Perslucht is in dit bedrijfsonderdeel onder andere nodig voor het werk van de vormdeel automaten, het bewegen van stelcilinders en de werking van kleppen. Daarbij komt het uitblazen van de afgewerkte vormdelen uit de machine. Aangezien de afgewerkte, met perslucht uit de vormmachine geblazen Denopor delen moeten worden opgeslagen in een onverwarmde hal, moeten deze absoluut droog zijn. Want ondanks alle overige belastbaarheid reageert dit materiaal zeer gevoelig op ijzige temperaturen. Vochtigheid verhoogt deze gevoeligheid natuurlijk nog.
Droogheid staat voor Delkeskamp Verpackungswerke GmbH dus helemaal bovenaan de lijst van prioriteiten voor de persluchtvoorziening. Zo ook bij de noodzakelijk geworden uitbreiding van de persluchtinstallatie in de moederfabriek Nortrup. Sinds 2007 investeert men hier in aanzienlijke omvang in de uitbreiding en modernisering van de productie.
Hogere vraag naar perslucht na fabrieksuitbreiding
De capaciteit van het persluchtstation tot op heden in de zogenaamde ‘compressorenkelder’ kon met deze groei geen gelijke tred houden. De daar ondergebrachte vijf compressoren plus daarna geïnstalleerde adsorptiedroger waren dringend toe aan versterking. En een al langer bestaande ‘wankelende kandidaat’ zou eindelijk op pensioen moeten worden gestuurd: de statische olie-water scheider, die lang niet altijd zo functioneerde als men bij Delkeskamp zou wensen.
De zoektocht naar de modernste oplossing voor dit probleem leidde Delkeskamp na een intensieve marktanalyse tot een voor hen volledig nieuwe aanspreekpartner: naar de Duitse persluchtsysteemaanbieder BEKO TECHNOLOGIES GmbH.
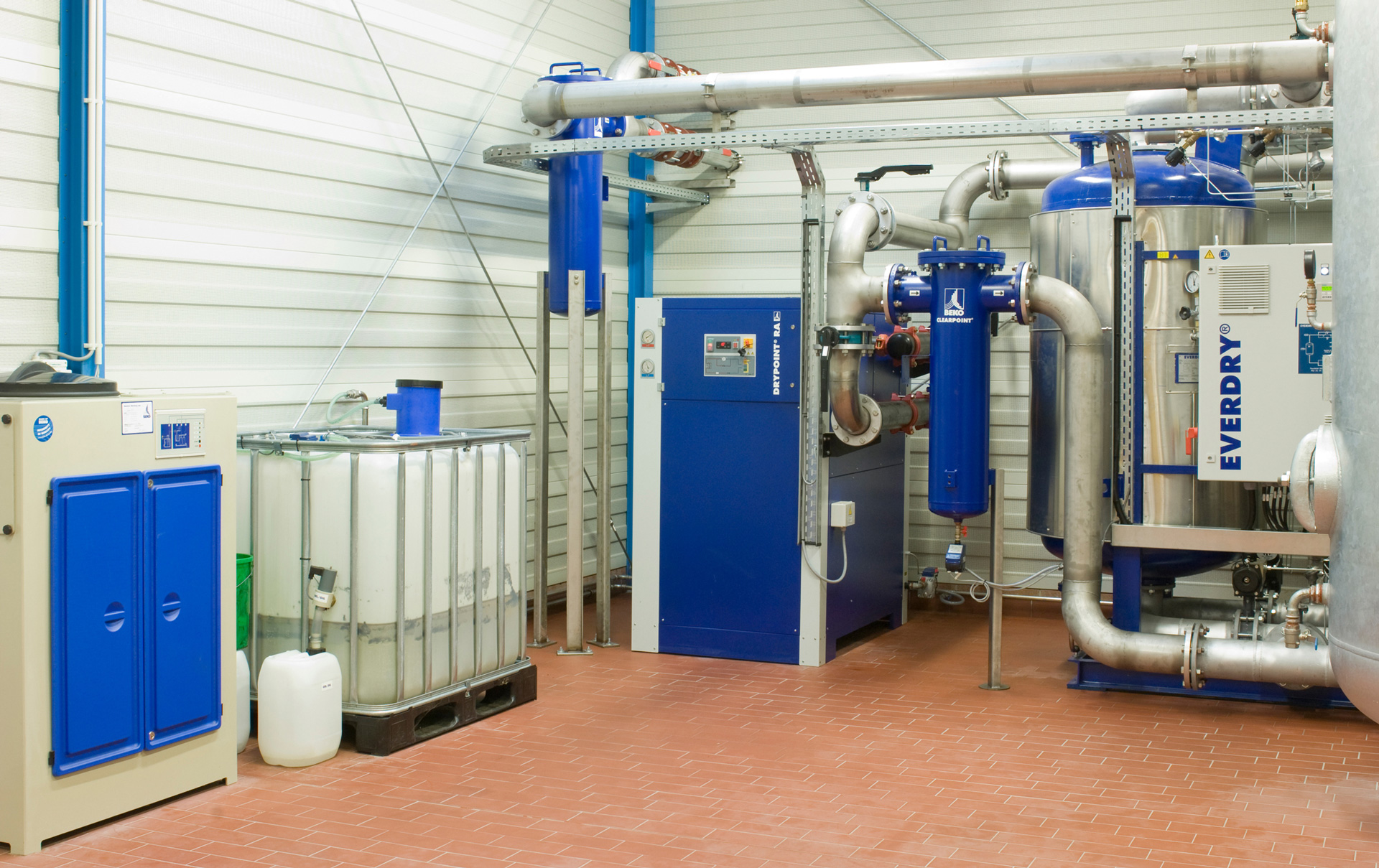
De in Neuss aan de Rijn gevestigde en wereldwijd actieve onderneming heeft een technologie voor de scheiding van olie-water emulsies in het programma: BEKOSPLIT. Deze scheidingsinstallaties zuiveren geëmulgeerde condensaten, zoals deze onder ongunstige uitgangsvoorwaarden of bepaalde smeermiddel-verdichter combinaties voorkomen. Naast persluchtcondensaat kan ook ander oliehoudend industrieel afvalwater worden gezuiverd. In water onoplosbare organische vervuilingen – bijvoorbeeld olies, plantaardige of dierlijke vetten – en een groot aantal vaste stofverontreinigingen worden verwijderd uit het water. Daarnaast worden eventueel aanwezige zware metalen, vuil en verfdeeltjes betrouwbaar geadsorbeerd.
Daarbij werkt het BEKOSPLIT principe effectiever dan een ultrafiltratie: er zijn geen agressieve reinigingsmiddelen en er is minder energie nodig. De benodigde investering is uiterst overzichtelijk en langere onderhoudsintervallen bevorderen de rentabiliteit nog eens.
Een systeem bewijst zich
Maar er moest meer groeien uit dit contact met de persluchtspecialist BEKO TECHNOLOGIES. Al snel zag men bij Delkeskamp in dat ze in BEKO TECHNOLOGIES een partner hadden gevonden, die op dezelfde lijn zat als zijzelf. Die dacht in totaaloplossingen en omvattende concepten ontwikkelde. De zaak begon spannend te worden.
Vooral toen men bij BEKO TECHNOLOGIES begon het voor Delkeskamp zo gevoelige thema persluchtdroging toch nog eens te overdenken. Bijvoorbeeld wat de rentabiliteit aanging. Toen men zelfs zo ver ging de behandeling van de tot nu toe uitsluitend ingezette adsorptiedrogers voor een goed deel ook over te dragen naar koeldrogers, deed dat aanvankelijk echter weer de deur dicht.
Voor Delkeskamp stond dit voorstel in eerste instantie nu eenmaal gelijk aan een paleisrevolutie: zij vertrouwden toch alleen op het principe en de zekerheid van de adsorptiedroging voor het ontwerp van de installatie. Men had daarmee tot op heden geen enkel probleem gekend en ze wilden geen onnodige risico’s in huis halen. Anderzijds was de gedachte aan koeldrogers enorm verleidelijk, wanneer men kijkt naar de verreweg gunstigere energiebalans van dit procedé in vergelijking met de adsorptiedroger. Wanneer men beide dus zou kunnen combineren…
Precies de juiste uitdaging voor de systeemaanbieder BEKO TECHNOLOGIES. Binnen enkele dagen ontwikkelde deze voor Delkeskamp een sluitend concept voor een redundant opgebouwd combinatiesysteem van adsorptie- en koeldroger. Dat is sinds mei 2008 realiteit.
Dit systeem stelt de verpakkingsfabrikant in staat om, al naargelang eisen en omgevingsvoorwaarden – bijvoorbeeld seizoensafhankelijk – de telkens zowel meest betrouwbare als ook voordeligste drogercombinatie in te zetten. Ofwel als flexibele combinatie van beide procedé’s of uitsluitend via adsorptie- respectievelijk koeldroging.
Aangezien de buisleidingen van de persluchtinstallatie binnen het fabrieksterrein over buisbruggen zo veel mogelijk in de openlucht lopen, zijn ze natuurlijk seizoensafhankelijk blootgesteld aan grote temperatuurschommelingen. Zo moet bijvoorbeeld ter bescherming tegen nacondensatie en bevriezing in de winter een drukdauwpunt beter dan min 40 °C zijn gegarandeerd. Om hier maximale proceszekerheid te bereiken zijn de geïnstalleerde EVERDRY adsorptiedrogers van BEKO TECHNOLOGIES uitgerust met meet- en regeleenheden voor het drukdauwpunt. Tot op heden werkt dat perfect. De drogercapaciteit is absoluut stabiel en de energiebalans is merkbaar verbeterd.
Inmiddels kiest men bij Delkeskamp in de gemoderniseerde persluchtbehandeling uitsluitend voor BEKO TECHNOLOGIES apparaten. Naast de BEKOSPLIT scheidingsinstallaties, EVERDRY adsorptiedrogers en de DRYPOINT koeldroger verrichten ook CLEARPOINT filters hun werk.
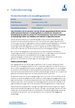