Chłodzenie sprężonym powietrzem maszyn do cięcia laserowego
Branża: | technologia laserowa |
Klient/miejscowość/rok: | Horstmann, Verl (Niemcy), 2008 |
Zastosowanie sprężonego powietrza: | powietrze procesowe |
Zainstalowane produkty: | BEKOKAT |
Cięcie laserowe należy do metod termicznych. Jest to zauważalne zanim promień lasera trafia na cięty materiał. Wysoka temperatura powstaje już we wcześniejszym biegu promienia. Potrzebne jest tu chłodzenie. Najlepszym i najbardziej opłacalnym medium do zastosowania jest sprężone powietrze. Bezwzględnie jednak nie może ono zawierać oleju.
Firma Horstmann GmbH & Co. KG, której siedziba znajduje się w miejscowości Verl niedaleko Gütersloh, zajmuje się wysokogatunkową i wymagającą obróbką metali dla renomowanych klientów licznych gałęzi przemysłu, do których należy m.in. przemysł motoryzacyjny i stoczniowy oraz produkcja maszyn, urządzeń i narzędzi.
Maszyny do cięcia laserowego pracujące niestrudzenie w firmie Horstmann są niezwykle czułe nawet na minimalne wprowadzenie oleju przez sprężone powietrze. Reagują wyraźnym spadkiem wydajności i jakości, ponieważ ostry jak nóż promień lasera zostaje zdegradowany dosłownie do słabo migoczącej „kiepskiej lampy naftowej”. Inaczej niż być może przypuszczano, sprężone powietrze wykorzystywane jest przy maszynach do cięcia laserowego w firmie Horstmann nie do instalacji pneumatycznej, lecz wyłącznie do schładzania biegu promienia lasera.
Zasadniczo urządzenie do cięcia laserem CO2 składa się ze źródła promienia lasera i ruchomego ogniskującego układu optycznego, zazwyczaj zwierciadła wklęsłego lub soczewki skupiającej. Ze źródła promień lasera prowadzony jest przez reflektory ultraktrótkofalowe do optycznego układu obróbki. Tam promień lasera zostaje zogniskowany i w ten sposób powstaje wymagana do cięcia gęstość mocy. W firmie Horstmann, zajmującej się w pierwszej kolejności cięciem blach ze stali nierdzewnej, moc promienia wynosi do 6 kW. Wystarczająco dużo, aby bez problemu w całości przeniknąć przez ludzkie ciało.
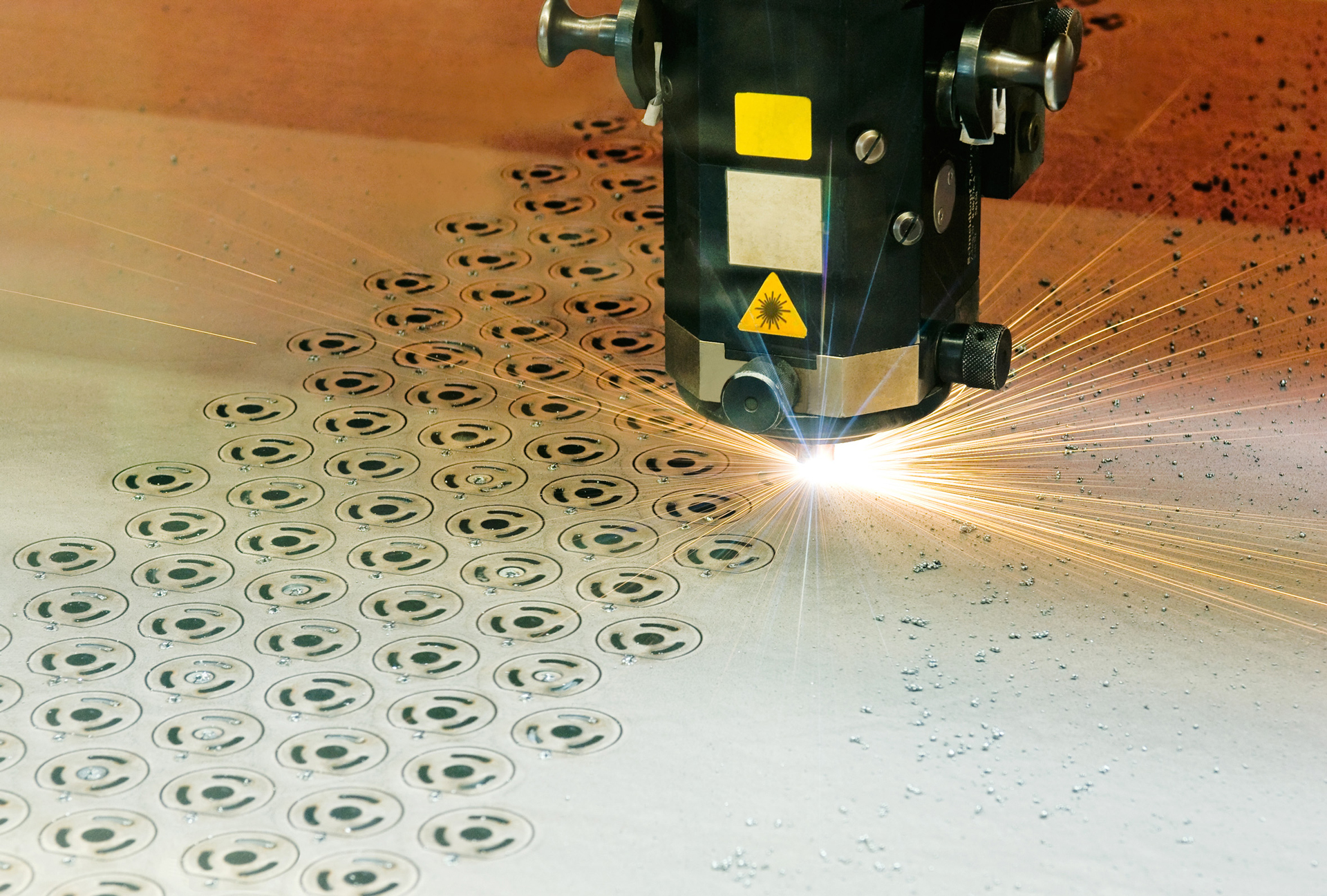
W związku z tym, że przesuwny „latający” układ optyczny przemieszcza się po obrabianej blasze, nieustannie zmienia się jego odległość od stałego źródła laserowego. Wytworzony promień lasera nie wykazuje natomiast wymaganej równoległości, aby przenosić go na dużych i zmiennych dystansach. Z tego względu, a także celem zmniejszenia termicznego obciążenia reflektorów ultrakrótkofalowych, zostaje on częściowo rozszerzony za pomocą teleskopu zwierciadlanego.
Właściwe prowadzenie promienia między źródłem laserowym a ogniskującym układem optycznym odbywa się za pośrednictwem zwierciadeł z powłoką złotą lub molibdenową, które wykonane są zazwyczaj z czystej miedzi lub monokrystalicznego krzemu. Zwierciadła te reagują bardzo wrażliwie na gromadzący się na nich olej lub aerozole, przyspieszające termin niezwykle kosztownej wymiany.
W całym biegu promienia lasera powstają oczywiście bardzo wysokie temperatury. Bez chłodzenia stosowane tu materiały, na przykład reflektory ultrakrótkofalowe i jeszcze szybciej mieszek ruchomej jednostki optycznej, zostałyby poważnie uszkodzone.
Tę niezwykle ważną funkcję chłodzenia przejmuje wdmuchiwane sprężone powietrze. Nie może ono zawierać żadnych cząstek stałych ani oleju oraz musi być suche, aby nie „rozproszyć” promienia lasera unoszącymi się cząstkami oraz nie zabrudzić osadami reflektorów ultrakrótofalowych. Nawet najmniejsza zawartość oleju lub aerozolu w sprężonym powietrzu miałaby w krótkim czasie fatalne skutki dla bezpieczeństwa procesu i zyskowności urządzenia tnącego.
Oba czynniki– razem z bezwzględną jakością produktu – są istotnymi elementami nieustającego sukcesu biznesowego firmy Heinrich Horstmann GmbH & Co. KG. Dlatego szczególną uwagę poświęca się tam także zagadnieniu uzdatniania sprężonego powietrza.
Dotychczas w firmie Horstmann próbowano – tak jak u niemal wszystkich użytkowników sprężonego powietrza o podobnych wymaganiach – produkować bezolejowe sprężone powietrze za pomocą względnie kosztownych, często nawet połączonych ze sobą technik opartych na sprężarce, filtrze i osuszaczu. Niejednokrotnie udawało się to zrealizować z lepszym lub gorszym stopniem niezawodności.
Także w firmie Horstmann nie znaleziono nigdy naprawdę zadowalającego rozwiązania; przede wszystkim nie udało się tego dokonać po nabyciu nowych, jeszcze wydajniejszych urządzeń do cięcia. Na początku 2008 r. trafiono na metodę katalityczną do wytwarzania całkowicie bezolejowego sprężonego powietrza, która została opracowana przez niemieckiego specjalistę w dziedzinie sprężonego powietrza – firmę BEKO TECHNOLOGIES Metoda o nazwie BEKOKAT otwiera drogę do całkowicie bezolejowego sprężonego powietrza poprzez zupełnie inne podejście technologiczne niż wszystkie dotychczasowe rozwiązania. Chodzi o metodę katalityczną.
Całkowite utlenianie węglowodorów
Podstawą systemu BEKOKAT jest całkowite utlenianie węglowodorów i tym samym całkowicie bezolejowe sprężone powietrze. I to wszystko odbywa się na etapie procesu po sprężeniu. W związku z tym sprężone powietrze zostaje całkowicie odolejone w zaledwie jednym jedynym komponencie systemu. Pracuje on niezależnie od warunków otoczenia, wejściowego stężenia oleju i wilgotności względnej sprężonego powietrza.
BEKOKAT przetwarza wszystkie zanieczyszczenia w sprężonym powietrzu podawane przez sprężarkę. Są to zazwyczaj smary, oleje, dwutlenek siarki, tlenek węgla, gazy azotowe itd. Występują one zarówno w postaci gazowej, jak również pary i aerozolu. Zastosowanie metody BEKOKAT powoduje całkowite przekształcenie takich składników powietrza w dwutlenek węgla i wodę, którą można bez obaw odprowadzać bezpośrednio do sieci kanalizacyjnej, nie podejmując żadnych innych działań na rzecz ochrony środowiska. Nawet kondensat gromadzący się podczas schładzania sprężonego powietrza jest dzięki metodzie katalitycznej całkowicie bezolejowy i bez uzdatniania może być odprowadzany do kanalizacji. Obecnie żadna inna metoda nie pozwala na całkowite utlenienie węglowodorów bez pozostawienia zawartości resztkowej.
Katalizatorem wykorzystywanym w urządzeniu BEKOKAT jest granulat, który zostaje nagrzany za pomocą elementów grzewczych do temperatury roboczej ok. 150°C. Cząsteczki oleju są „łamane” w katalizatorze tak długo, aż pozostanie tylko jeden atom węgla. W końcowym etapie katalizy cząsteczki oleju są utleniane do H2O i CO2.
Różnej długości łańcuchy węglowodorowe z bezolejowych i smarowanych olejem sprężarek nie stanowią dla metody BEKOKAT żadnego problemu.
Nie zawsze jest pełna świadomość, że często stosowane filtry z węglem aktywnym nie są w stanie pochłaniać związków polarnych, takich jak alkeny, alkohole, glikole czy ketony. System BEKOKAT natomiast całkowicie usuwa ze sprężonego powietrza także te substancje. W kolejnym etapie procesu BEKOKAT oczyszczone sprężone powietrze zostaje schłodzone w wymienniku ciepła do temperatury ok. 10-15°C powyżej wlotu i jest gotowe do stosowania.
BEKOKAT jest pierwszym urządzeniem umożliwiającym osiągnięcie niezmiennie całkowicie bezolejowego sprężonego powietrza z zawartością resztkową oleju na niemal niemożliwym do zmierzenia poziomie 0,003 miligrama na metr sześcienny sprężonego powietrza. Jest to jakość potrzebna w niezwykle wymagających obszarach medycyny i farmacji oraz przetwórstwa i pakowania żywności.
Pod względem opłacalności wyjątkową zaletą jest także doskonała trwałość specjalnego granulatu BEKOKAT, który należy wymienić dopiero po 20 000 godzin pracy. Dla porównania żywotność filtra z węglem aktywnym nawet w perfekcyjnych warunkach roboczych jest skończona już po 500 godzinach pracy.
Od wczesnego lata 2008 r. system BEKOKAT jest wykorzystywany przez całą dobę w firmie Horstmann zajmującej się obróbką metali i nie występują żadne usterki. Firma Horstmann GmbH & Co. KG może spać spokojnie również jeśli chodzi o aspekt ekologiczny. Odkąd wykorzystywany jest system BEKOKAT kondensat z instalacji sprężonego powietrza można bez problemu i drogiego uzdatniania wprowadzać bezpośrednio do kanalizacji.
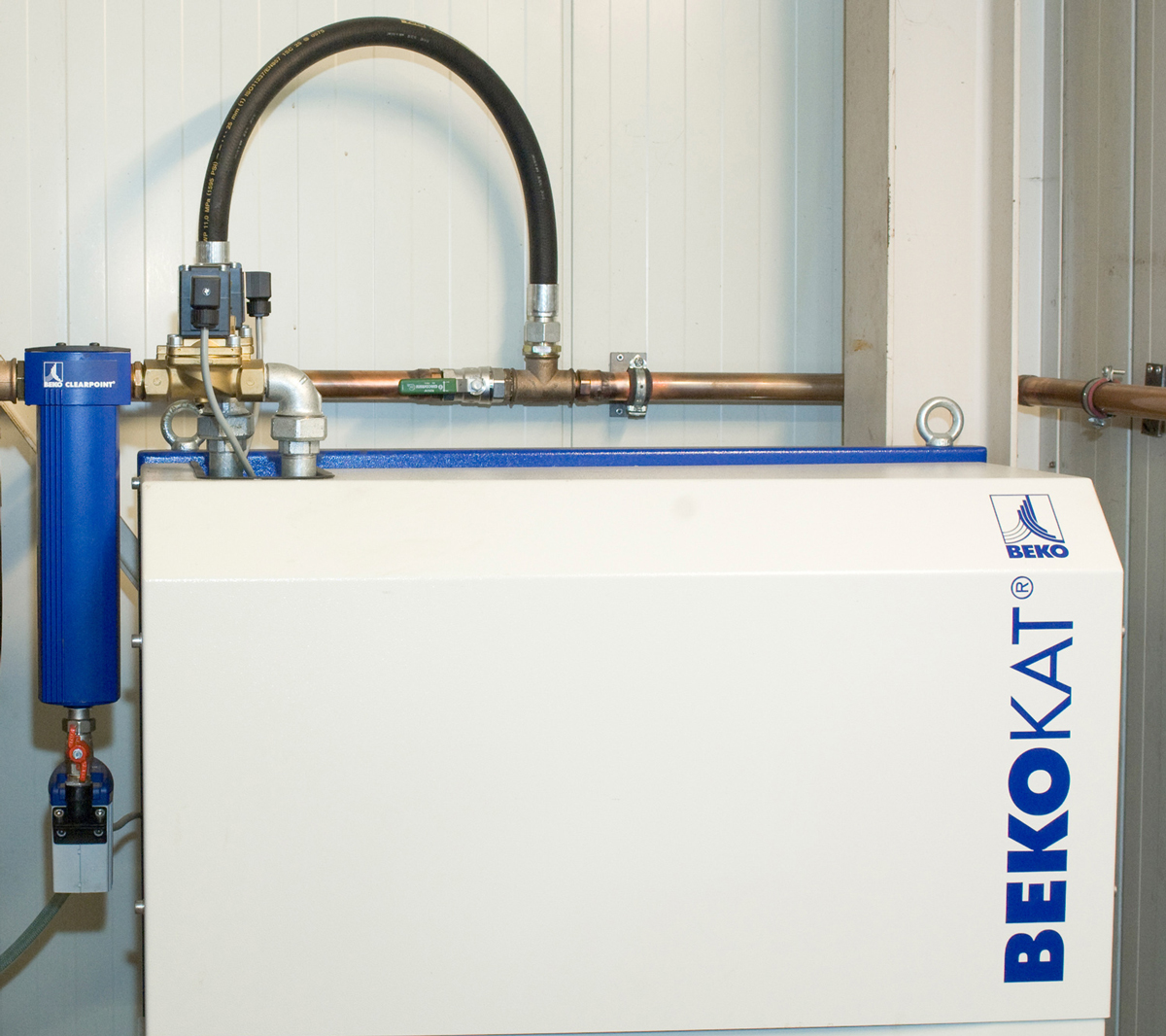
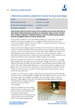