Technologia sprężonego powietrza w przemyśle opakowaniowym
Branża: | pakowanie, papier |
Klient/miejscowość/rok: | Delkeskamp, Nortrup (Niemcy), 2008 |
Zastosowanie sprężonego powietrza: | powietrze sterujące, powietrze procesowe, technika kondensatu |
Zainstalowane produkty: | EVERDRY, BEKOSPLIT |
Tej gałęzi przemysłu nie można bagatelizować: ponad 100 wyspecjalizowanych w tej dziedzinie fabryk zatrudniających około 19 000 pracowników produkuje i przetwarza w Niemczech tekturę falistą. Sprężone powietrze i jego uzdatnianie odgrywają kluczową rolę w procesie produkcyjnym. Fatalne skutki dla urządzeń, surowców i gotowych produktów miałaby przede wszystkim wilgoć w sprężonym powietrzu.
Produkcja roczna, wynosząca w przybliżeniu dziewięć miliardów metrów kwadratowych tektury falistej, plasuje Niemcy na pierwszym miejscu w Europie, natomiast na rynku międzynarodowym na miejscu 4 za USA, Chinami i Japonią. Niemal trzy czwarte wszystkich transportowanych towarów w Niemczech opakowanych jest obecnie w tekturę falistą – i prawie 30 procent wszystkich napełnionych opakowań z tektury falistej przekracza granice kraju w drodze do konsumenta. Jest to zatem potężny biznes zataczający koła i mający duże znacznie dla całej niemieckiej gospodarki narodowej.
Jednym z pionierów, inicjatorów i usługodawców w tym sektorze przemysłu jest firma Delkeskamp Verpackungswerke GmbH w dolnosaksońskiej miejscowości Nortrup. Przedsiębiorstwo zostało założone już w 1896 r. jako fabryka kartonów. Obecnie, oprócz głównego zakładu w Nortrup, firma posiada kolejne zakłady produkcyjne w Hanowerze oraz czeskim mieście Odry. Przedmiotem działalności jest produkcja papieru, tektury falistej i pianki do opakowań w różnych kolorach.
Zamknięty obieg produkcji
Materiałem wyjściowym do produkcji tektury falistej jest surowa tektura falista. Dużą część potrzebnego papieru surowcowego firma Delkeskamp GmbH produkuje samodzielnie w zakładzie w Nortrup. W związku z tym lokalizacja ta jest pierwszym członem zamkniętego obiegu produkcyjnego – i tym samym ma decydujące znaczenie dla sprawności i ekonomiczności całej struktury produkcji firmy Delkeskamp. Oprócz zalet istotnych z punktu widzenia technologii produkcji samodzielne wytwarzanie surowej tektury falistej zapewnia firmie także maksymalną niezależność od rynku zaopatrzeniowego.
Firma Delkeskamp ceni sobie tę autonomiczność także w szerszym kontekście. W związku z tym w Nortrup we własnej elektrowni za pomocą nowoczesnych turbin gazowych wytwarzana jest nawet para potrzebna do produkcji papieru. W tym procesie powstaje elektryczność w ilości znacznie przewyższającej własne zapotrzebowanie – i jest doprowadzana do sieci publicznej. Tym samym firma zaopatruje nie tylko własne zakłady. Dodatkowo jest cenionym dostawcą energii w Dolnej Saksonii.
Obok bezwarunkowego bezpieczeństwa procesów we własnej działalności produkcyjnej przedsiębiorstwo ponosi także w pewnym stopniu odpowiedzialność za mieszkańców regionu. Są to oczekiwania, którym należy sprostać. Jednym z filarów jest stabilne i doskonałe jakościowo zaopatrywanie zakładu w sprężone powietrze – jeden z decydujących pod różnymi względami nośników energii do produkcji.
Sprężone powietrze jest decydującym nośnikiem energii
W Nortrup sprężonym powietrzem zasilane są trzy – właściwie cztery – obszary zakładu. W pierwszej kolejności należy tu fabryka papieru, dział produkcji tektury falistej i zakład produkujący piankę. Kolejnym obszarem – o znacznie mniejszym zapotrzebowaniu – jest należąca do firmy elektrownia.
Bez sprężonego powietrza firma Delkeskamp praktycznie nie mogłaby prowadzić działalności. Aby to zrozumieć, należy wyobrazić sobie jedynie ogólne szkice procesów produkcyjnych w trzech obszarach: w pierwszym etapie produkcji papieru następuje ogrzanie i nawilżenie surowej tektury falistej produkowanej w pierwszej fazie z makulatury w ogromnych, niezwykle nowoczesnych urządzeniach produkcyjnych. W ten sposób staje się ona elastyczna i podatna na dalsze formowanie. W kolejnym etapie papier przeprowadzany jest pod ciśnieniem i w wysokiej temperaturze między dwoma wałkami ryflowanymi zazębiającymi się analogicznie do kół zębatych. Następnie pofalowany papier sklejany jest najpierw z wewnętrzną wstęgą papieru od góry, a następnie z zewnętrzną wstęgą papieru od dołu – w ten sposób tektura falista może zachować swoją optymalną funkcję ochronną.
W pełni zautomatyzowanych operacjach roboczych z arkuszy tektury falistej powstają następnie składane pudełka, opakowania fasonowe, opakowania wewnętrzne z wypełnieniem i opakowania typu display. Do realizacji tych procesów bądź sterowania nimi wykorzystuje się liczne urządzenia pneumatyczne, jak również regulatory i zasuwy uruchamiane przy użyciu sprężonego powietrza. Jeśli którekolwiek ogniwo w tym niezwykle precyzyjnie zaprojektowanym łańcuchu produkcyjnym przestanie działać, od razu wpłynie to na kwotę produkcyjną, a przede wszystkim na jakość.
Najważniejsze: suche sprężone powietrze
Obok ciągłości zasilania, firma Delkeskamp potrzebuje przede wszystkim suchego sprężonego powietrza. Przedostanie się wilgotności do sprężonego powietrza działa na urządzenia pneumatyczne i produkty jak trucizna.
Wilgotne sprężone powietrze od dawna stanowi ryzyko nie tylko dla papieru i tektury falistej. Także w trzecim obszarze produkcji firmy Delkeskamp, wytwarzaniu pianki, zachowanie suchości jest obligatoryjne. Tu z polistyrenu piankowego (EPS) produkowane są kształtki zaprojektowane indywidualnie do różnych opakowań. Tworzywo, znane powszechnie jako styropian, określane jest w firmie Delkeskamp terminem Denopor, który uzupełnia płynną koncepcję opakowań producenta.
Sprężone powietrze znajduje zastosowanie w tej części zakładu między innymi do pracy automatów do kształtek, poruszania siłowników nastawczych oraz działania zaworów. Do tego dochodzi wydmuchiwanie z maszyn gotowych kształtek. Ponieważ gotowe elementy z Denoporu wydmuchane z maszyny formierskiej przy użyciu sprężonego powietrza są przechowywane w nieogrzewanej hali, muszą być absolutnie suche. Materiał ten charakteryzuje się wyjątkową wytrzymałością na różne obciążenia, jednak reaguje bardzo wrażliwie na ujemne temperatury. Wilgotność oczywiście jeszcze bardziej zwiększa tę wrażliwość.
Z tego względu suchość zajmuje wysoką pozycję w firmie Delkeskamp Verpackungswerke GmbH na liście priorytetów związanych z zasilaniem sprężonym powietrzem. Dotyczy to także koniecznej rozbudowy instalacji sprężonego powietrza w macierzystym zakładzie w Nortrup. Od 2007 r. firma rozwija się oraz inwestuje tu ogromne środki w powiększenie i modernizację produkcji.
Większe zapotrzebowanie na sprężone powietrze po powiększeniu zakładu
Dotychczasowa stacja sprężonego powietrza w tzw. „piwnicy sprężarek” nie mogła nadążyć za tym rozwojem. Pięć znajdujących się tam sprężarek plus dołączony osuszacz adsorpcyjny potrzebowało pilnego wsparcia. I istniejący już od dawna „niepewny kandydat” powinien zostać w końcu wysłany na emeryturę: statyczny separator oleju i wody, który już dawno nie zawsze działał tak, jak oczekiwano w firmie Delkeskamp.
Poszukiwania najnowocześniejszego rozwiązania tego problemu zaprowadziły firmę Delkeskamp po intensywnej analizie rynku do zupełnie nowego dla niej partnera do kontaktu: do niemieckiego dostawcy systemów sprężonego powietrza BEKO TECHNOLOGIES GmbH.
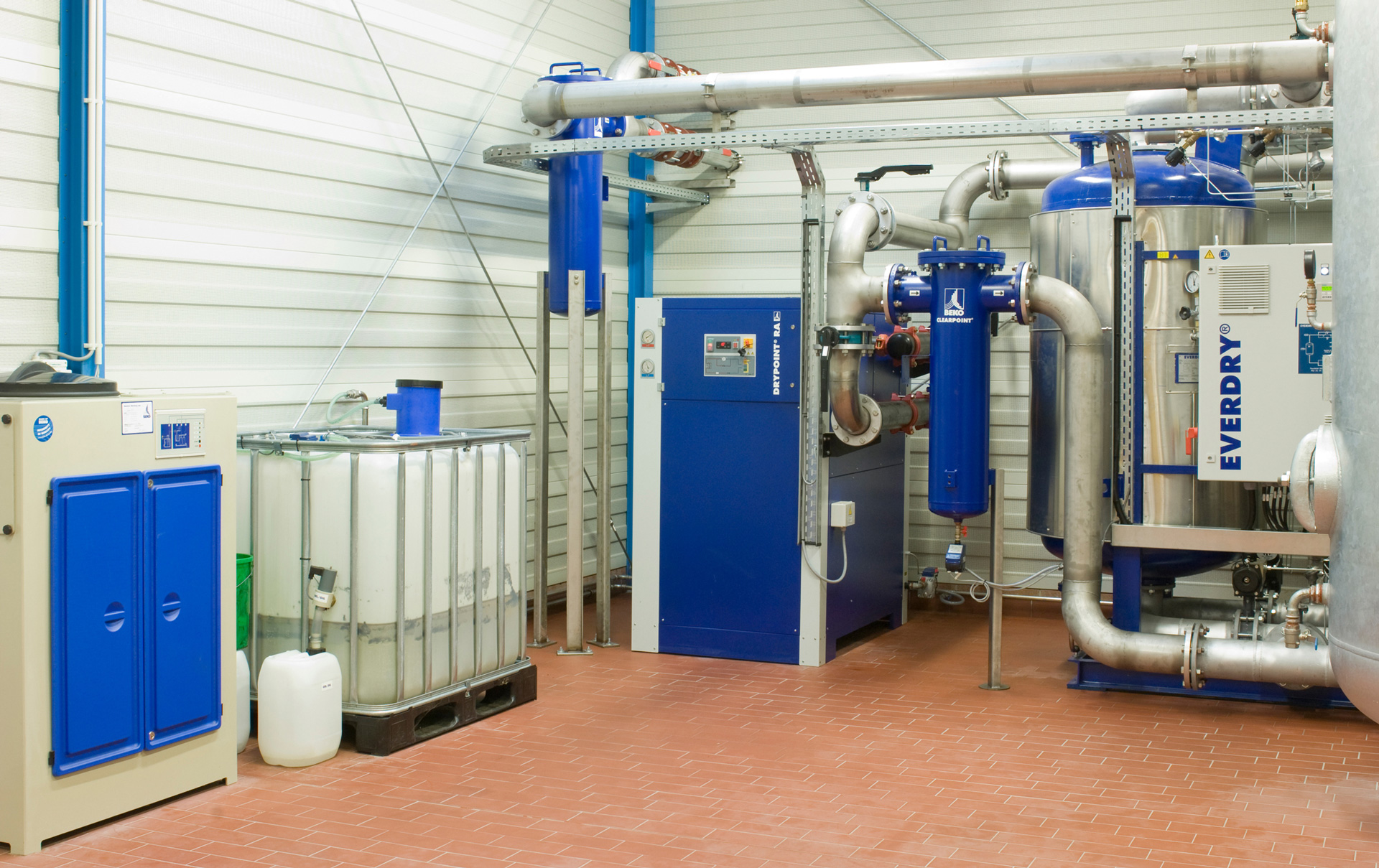
Przedsiębiorstwo prowadzące działalność na całym świecie, którego siedziba znajduje się w nadreńskiej miejscowości Neuss, posiada w ofercie technologię do separacji emulsji oleju i wody: BEKOSPLIT. Separatory te oczyszczają zemulgowane kondensaty powstające na skutek niekorzystnych warunków wyjściowych lub w wyniku określonych połączeń środków smarnych i sprężarek. Poza kondensatem sprężonego powietrza urządzenia te umożliwiają uzdatnianie także innych zaolejonych ścieków przemysłowych. Z wody usuwane są nierozpuszczalne w wodzie zanieczyszczenia organiczne – takie jak oleje, tłuszcze roślinne lub zwierzęce – oraz liczne zanieczyszczenia cząstkami stałymi. Ponadto niezawodnie pochłaniane są występujące ewentualnie metale ciężkie, brud i cząstki farb.
Zasada działania urządzenia BEKOSPLIT jest przy tym skuteczniejsza niż ultrafiltracja: niepotrzebne są agresywne środki czyszczące oraz zużywa się mniej energii. Nakłady inwestycyjne są niezwykle przejrzyste, a wydłużone terminy konserwacji dodatkowo korzystnie wpływają na opłacalność.
System sprawdza się
Kontakt ze specjalistą z obszaru sprężonego powietrza – firmą BEKO TECHNOLOGIES – ma perspektywy na dalszą współpracę. W firmie Delkeskamp szybko zauważono, że spółka BEKO TECHNOLOGIES jest niezawodnym partnerem, posiadającym podobne priorytety jak Delkeskamp, myślącym kompleksowo i opracowującym konsekwentne koncepcje ogólne. Obrót sprawy zaczął być interesujący.
Przede wszystkim wówczas, gdy firma BEKO TECHNOLOGIES zaczęła jeszcze raz analizować niezwykle delikatne zagadnienie osuszania sprężonego powietrza, które ma bardzo duże znaczenie dla firmy Delkeskamp. Na przykład kwestie związane z opłacalnością. Jednak początkowo drzwi ponownie zatrzasnęły się, gdy postanowiono przenieść dużą część uzdatniania ze stosowanych dotychczas wyłącznie osuszaczy adsorpcyjnych na osuszacze ziębnicze.
Zdaniem firmy Delkeskamp propozycja ta przypominała początkowo przewrót pałacowy, pracownicy podczas projektowania urządzeń ufali jedynie koncepcji i bezpieczeństwu osuszania adsorpcyjnego. Dotychczas nie było żadnych problemów i nie chciano wprowadzać do firmy niepotrzebnego ryzyka. Z drugiej strony idea osuszaczy ziębniczych była niezwykle interesująca, biorąc pod uwagę znacznie korzystniejszy bilans energetyczny tej metody w porównaniu z osuszaczem adsorpcyjnym. Gdyby tak zatem można było połączyć oba te urządzenia...
Wyzwanie na miarę dostawcy systemowego BEKO TECHNOLOGIES. W ciągu kilku dni firma ta opracowała dla Delkeskamp kompleksową koncepcję skonstruowanego dodatkowo systemu łączącego osuszacz adsorpcyjny i ziębniczy. Od maja 2008 r. jest on rzeczywistością.
System ten pozwala producentowi opakowań, w zależności od wymagań i warunków otoczenia – na przykład sezonowo – wykorzystywać zarówno najbezpieczniejszą, jak również najbardziej optymalną pod względem kosztów konstelację osuszaczy. Albo jako elastyczne połączenie obu metod, albo wyłącznie osuszanie adsorpcyjne lub ziębnicze.
Ponieważ przewody rurowe instalacji sprężonego powietrza na terenie zakładu przebiegają przez mostki rurowe w dużej mierze na zewnątrz, są oczywiście narażone sezonowo na duże wahania temperatury. Na przykład w celu ochrony przed ponowną kondensacją i zamarzaniem zimą ciśnieniowy punkt rosy musi być lepszy niż -40°C. Celem osiągnięcia tu najwyższego bezpieczeństwa procesu zainstalowane osuszacze adsorpcyjne EVERDRY firmy BEKO TECHNOLOGIES wyposażone są w odpowiednie jednostki do pomiaru punktu rosy i sterowania. Jak dotąd funkcjonuje to perfekcyjnie. Wydajność osuszania jest bezwzględnie stabilna, a bilans energetyczny wyraźnie się poprawił.
Obecnie w dziedzinie nowoczesnego uzdatniania powietrza firma Delkeskamp wybiera wyłącznie urządzenia BEKO TECHNOLOGIES. Obok separatorów BEKOSPLIT, osuszaczy adsorpcyjnych EVERDRY oraz osuszacza ziębniczego DRYPOINT zastosowanie znajdują także filtry CLEARPOINT.
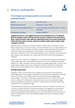