Technika kondensatu dla turbosprężarek
Branża: | metal, stal |
Klient/miejscowość/rok: | ThyssenKrupp Steel Europe, Duisburg (Niemcy), 2011 |
Zastosowanie sprężonego powietrza: | w produkcji, technika kondensatu |
Zainstalowane produkty: | BEKOMAT |
Ponad dziesięć kilometrów długości ma sieć sprężonego powietrza w najważniejszym zakładzie ThyssenKrupp Steel Europe AG w Duisburgu. Niezwykle rozgałęziony system, wymagający skutecznej i niezawodnej wentylacji. Zapewniają to bardzo wydajne turbosprężarki, które są dokładnie monitorowane.
Nic nie jest tu małe. Osoby, które zagłębią się w rozległy obszar duisburskich hut firmy ThyssenKrupp Steel Europe AG, muszą nastawić się na wyjątkowe wrażenia pod każdym względem. Tradycyjna lokalizacja producenta stali miała 120 lat czasu, aby osiągnąć swoją obecną wielkość i znaczenie. Aktualnie pracuje tu najwięcej osób wśród wszystkich spółek koncernu w Niemczech.
ThyssenKrupp Steel Europe skupia się na intensywnie rozwijającym się segmencie wysokiej jakości płaskowników stalowych. Spektrum działalności sięga od rozwiązań materiałowych przez obróbkę specyficzną dla produktów, usługi i kompleksowy serwis, aż po gotowe komponenty i podzespoły ze stali. Dzięki koncentracji metalurgii i przeważającej części produkcji taśm walcowanych na gorąco w Duisburgu stworzono nad Renem koncepcję lokalizacji wyjątkową na skalę europejską. Dopełnia ją efektywna działalność związana z walcowaniem na zimno i powlekaniem.
Podobnie jak w niemal wszystkich procesach przemysłowych, także tu sprężone powietrze należy do ważnych nośników energii. Jednocześnie jest ono centralnym elementem bezpieczeństwa procesów w firmie ThyssenKrupp Steel Europe AG. Poświęca się mu oraz jego uzdatnianiu odpowiednio dużą uwagę.
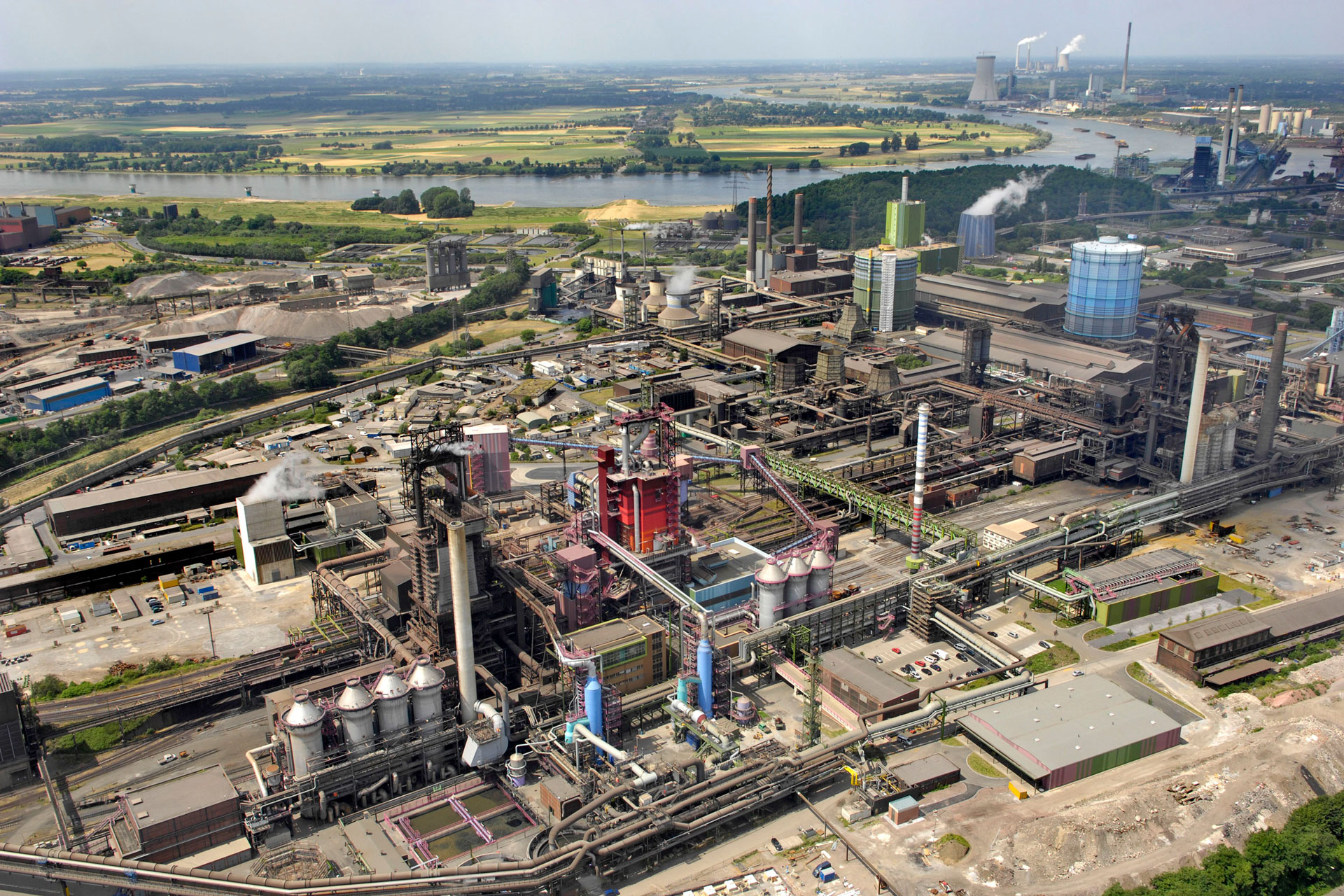
Żadnych drobiazgów
Część agregatów do wytwarzania i uzdatniania sprężonego powietrza znajduje się w dużej hali sprężarek w centrum zakładu. Wśród nich są trzy turbosprężarki, każda o wydajności sprężania 25 000 m³ na godzinę. Objętość ta, wynosząca łącznie 75 000 m³, przyczynia się do zapewnienia działania niezliczonych systemów w całym łańcuchu produkcyjnym. Jednym z takich obszarów jest chociażby sterowanie zaworami w walcowni. Łatwo zrozumieć, jakie daleko idące konsekwencje dla całego przebiegu produkcji mogą mieć usterki lub nawet awarie w takich częściach zakładu. Niesprawność jednej sprężarki mogłaby doprowadzić do problemów.
Do połowy 2010 r. utrudnienie, czy nawet problem z tego powodu wystąpiłby szczególnie przy odprowadzaniu kondensatu. Szczególne wymagania mają tu niezwykle wydajne turbosprężarki: każdy z czterech stopni sprężania agregatu wymaga własnego odprowadzania kondensatu. Do tej pory kondensat odprowadzany był ręcznie. Proces ten podlegał kontroli ręcznej i wzrokowej.
Mechanicznych spustów kondensatu stosowanych przy turbosprężarkach nie można było zintegrować w elektronicznym systemie monitorowania uzdatniania sprężonego powietrza. Wykluczało to zatem także możliwość włączenia ich na centralnym stanowisku dyspozytorskim. W obliczu wymagającej koncepcji zapewnienia jakości w firmie ThyssenKrupp Steel Europe AG sytuacja ta była dłużej nieakceptowalna. Ponieważ usterka nawet jednego spustu na tylko jednym z czterech stopni sprężania mogłaby spowodować tymczasową awarię sprężarki. Wydawało się, że żadna firma oferująca technikę sprężonego powietrza nie jest w stanie wyposażyć tak bardzo wydajnych sprężarek w pojemnościowe, monitorowane elektronicznie spusty kondensatu i zapewnić przy tym bezpieczeństwa procesu.
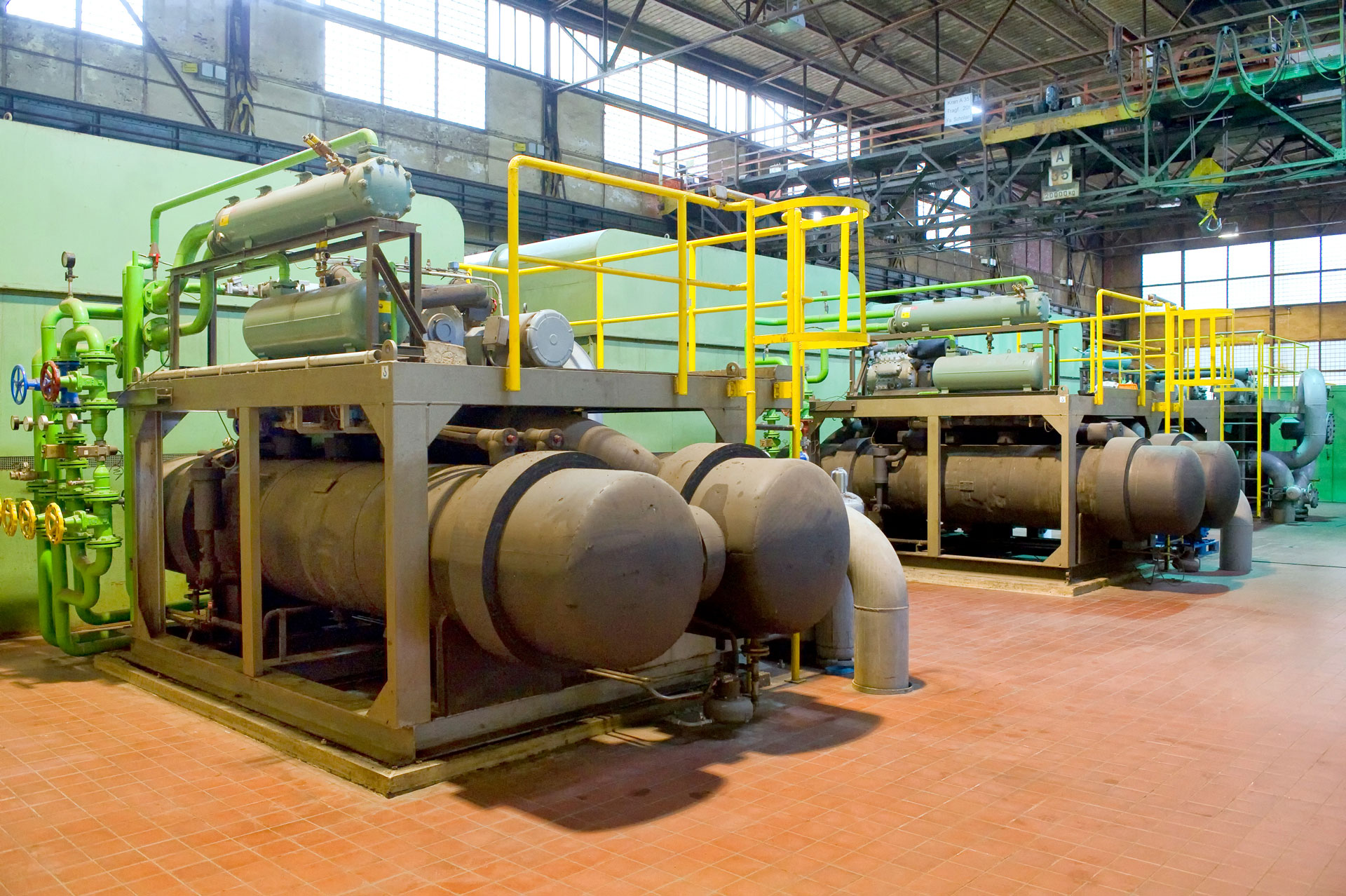
Odprowadzanie regulowane elektronicznie w zależności od poziomu
Ulgę w tej napiętej sytuacji przyniosła w końcu rozmowa z dostawcą systemów sprężonego powietrza, który w 1982 r. wprowadził na rynek spust kondensatu z elektroniczną regulacją w zależności od poziomu: niemiecka spółka BEKO TECHNOLOGIES GmbH z siedzibą w Neuss nad Renem. Przez wiele lat koncentrowano się tam początkowo tylko na tym produkcie – BEKOMAT – i odpowiednio doskonalono go także pod kątem trudnych zastosowań.
W komorze wychwytywania kondensatu w urządzeniu BEKOMAT sterowanym w zależności od poziomu nie znajduje się – inaczej niż w przypadku stosowania pływaka – żaden podatny na zakłócenia ruchomy element. Zadanie to przejmuje czujnik pojemnościowy. Reaguje on na każdy rodzaj kondensatu i jest zupełnie niewrażliwy na zanieczyszczenia.
Ta pojemnościowa rejestracja poziomu zapewnia odprowadzanie dostosowane do faktycznej ilości kondensatu bez strat sprężonego powietrza. Pozwala to na zaoszczędzenie energii i nie powoduje powstawania emulsji. Duże wymiary przekrojów spustów gwarantują bezpieczne odprowadzanie nawet w przypadku bardzo mocnego zanieczyszczenia kondensatu.
Inteligentna elektronika sterownicza zapewnia jednak nie tylko odprowadzanie kondensatu. Jednocześnie służy ona do całkowicie automatycznego monitorowania stanu urządzenia. Błędy wskazywane są za pomocą diody LED na spuście i mogą być ponadto przekazywane za pośrednictwem bezpotencjałowego styku jako komunikat o usterce także do centralnych punktów monitorowania.
Dzięki tym właściwościom spusty kondensatu BEKOMAT odpowiadały dokładnie profilowi wymagań firmy ThyssenKrupp Steel Europe AG w Duisburgu. Menadżerów przekonała przede wszystkim bezproblemowa integracja z istniejącym automatycznym systemem monitorowania i sterowania.
Tylko pięć tygodni
Wczesnym latem 2010 r. specjaliści z firmy BEKO TECHNOLOGIES, blisko współpracując z zespołem techników firmy ThyssenKrupp Steel Europe, zainstalowali przy jednej z turbosprężarek pierwsze cztery urządzenia BEKOMAT o różnej wielkości. Dopiero gdy konfiguracja ta zaczęła pracować płynnie pod każdym względem, uwagę poświęcono dwóm pozostałym agregatom.
Nie minęło jednak dużo czasu: w ciągu zaledwie pięciu tygodni między pierwszą konfiguracją wzorcową i całkowicie „nowym uruchomieniem” cały proces odprowadzania kondensatu był zmodernizowany w sposób zapewniający bezpieczeństwo. Kolejne urządzenia BEKOMAT posiadające elektroniczną regulację w zależności od poziomu znajdują się przy różnych osuszaczach ziębniczych systemu sprężonego powietrza.
Zwiększona w ten sposób niezawodność procesów jest kolejnym elementem dodanym do rygorystycznej koncepcji bezpieczeństwa w firmie ThyssenKrupp Steel Europe. Również przyszłe wydarzenia związane z systemem sprężonego powietrza nie powinny przyprawiać menadżerów o ból głowy. Ponieważ wszystkie warianty urządzenia BEKOMAT są nieustannie dostosowywane do parametrów tradycyjnych sprężarek i osuszaczy. Ulegają one ciągłym zmianom i są dopasowywane do wymagań wydajności przemysłowych systemów sprężonego powietrza.
Przyszłościowa technika
Prezentując niedawno piątą generację serii, czyli modele 31 i 32, firma BEKO TECHNOLOGIES osiągnęła obecnie optimum rentowności. Urządzenia te przedstawiają zupełnie nową zasadę konstrukcyjną wśród spustów kondensatu z elektroniczną regulacją w zależności od poziomu, co jest istotną zaletą podczas konserwacji.
Są one podzielone na zaledwie dwa moduły: jednostkę serwisową, łączącą w wyjątkowo odpornej na korozję aluminiowej obudowie wszystkie niezużywające się i bezobsługowe komponenty, oraz elektroniczną jednostkę sterującą i czujnikową wymagającą tylko jednorazowej instalacji. Oba podzespoły są połączone praktycznym szybkozłączem.
Taka konstrukcja umożliwia zupełnie nieskomplikowaną wymianę wszystkich części istotnych pod względem konserwacji i użytkowania poprzez szybką wymianę jednostki serwisowej. Do rozdzielania i łączenia obydwu modułów niepotrzebne są jakiekolwiek narzędzia – wystarczy zwykły chwyt ręką.
Nawet jeśli rozwiązanie to nie jest obecnie stosowane w urządzeniach z dużym przepływem sprężonego powietrza, tak jak w firmie ThyssenKrupp Steel Europe AG. Dla menadżerów w Duisburgu jest to dobry dowód możliwości rozwojowych ich systemowego dostawcy.
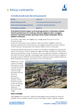