Uzdatnianie sprężonego powietrza jako koncepcja łańcucha procesowego
Branża: | technika napędowa |
Klient/miejscowość/rok: | Flender, Mussum (Niemcy), 2009 |
Zastosowanie sprężonego powietrza: | powietrze procesowe, powietrze zamykające, technika kondensatu |
Zainstalowane produkty: | BEKOSPLIT, CLEARPOINT, DRYPOINT RA |
Tam, gdzie konieczne jest spełnienie rozmaitych wymagań, pojedyncze rozwiązania rzadko dają zadowalające efekty. Dlatego firma A. Friedr. Flender AG, jeden ze światowych liderów w zakresie produkcji mechanicznych i elektrycznych urządzeń napędowych, stawia na kompleksową koncepcję w łańcuchu procesowym – między innymi w odniesieniu do uzdatniania sprężonego powietrza, które wymaga spełnienia technicznych i jakościowych wymagań, jak również wymogów ochrony środowiska.
W zakładzie produkcyjnym firmy Flender w Mussum, największej na świecie wytwórni sprzęgieł przemysłowych w zakresie momentu obrotowego do 10 do 10 000 000 Nm, w trzyzmianowym trybie pracy przez 365 dni w roku powstają sprzęgła elastyczne i bardzo elastyczne, sprzęgła sztywno-obrotowe – czyli sprzęgła zębate i całkowicie stalowe sprzęgła wielopłytkowe – oraz sprzęgła specjalne do turbin wiatrowych i napędów kolejowych. Niezwykle imponujące portfolio, które tworzy tu około 350 pracowników – spośród 6300 osób pracujących w całej grupie firm Flender.
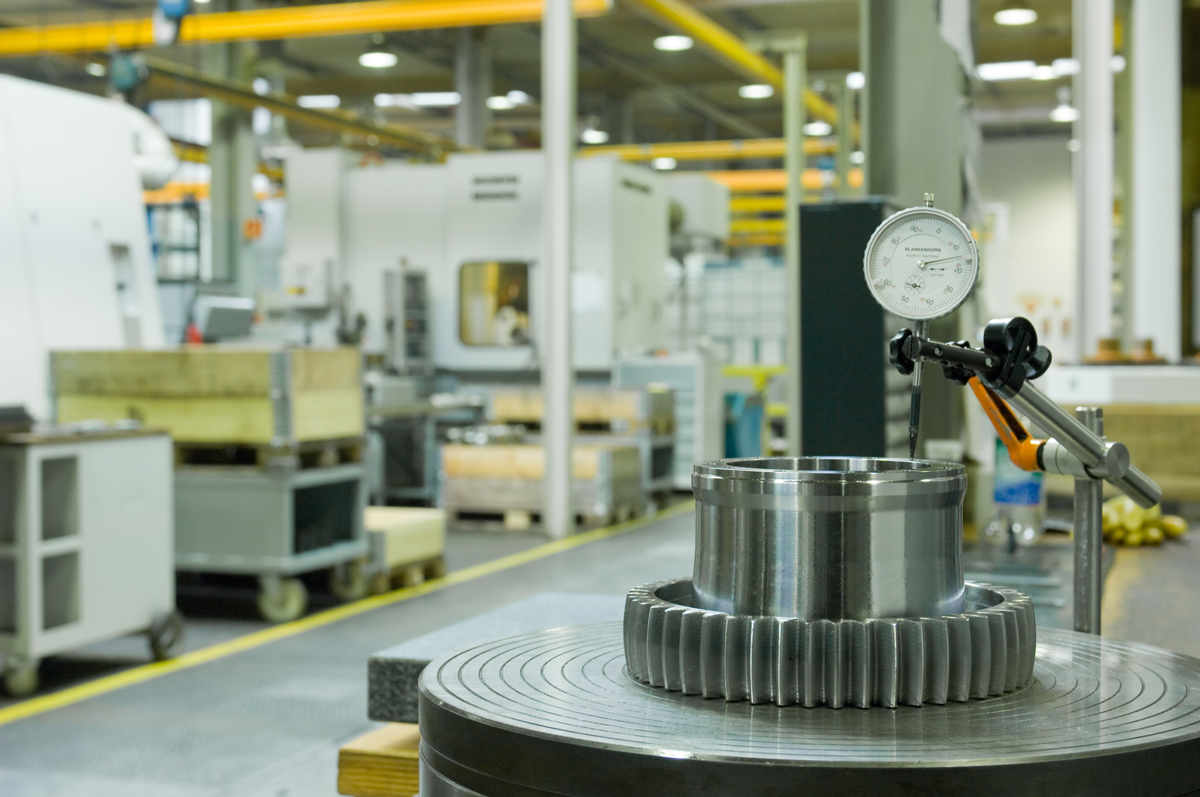
Podział zadań i ogólna odpowiedzialność
Mussum, jako zakład produkujący sprzęgła, reprezentuje praktycznie moduł kompleksowego układu przeniesienia napędu firmy Flender. Czynności precyzyjnie zazębiają się z operacjami zakładu macierzystego w Bocholt oraz zakładu zajmującego się montażem przekładni w Voerde-Friedrichsfeld. Zakłady pracują według logicznej koncepcji ogólnej, która uwzględnia wszystkie obszary i działalności koncernu oraz łączy je w określonym celu. I – jak potwierdza długa historia przedsiębiorstwa – robi to bardzo dobrze. Nieprzypadkowo w 2005 r. spółka Siemens AG przejęła spółkę Flender Holding AG, uzupełniając w ten sposób swoją działalność w obszarze przemysłowej techniki napędowej.
W firmie Siemens AG i w Flender Holding AG planowanie i realizacja działań odbywa się w powiązanych łańcuchach procesowych. Nie tylko ważne jest to, co było wcześniej, lecz duże znacznie ma także to, co wydarzy się później i w jaki sposób to się stanie. Czy to jest skuteczne, logiczne, prowadzi do celu? A przede wszystkim: czy należy brać za to odpowiedzialność? Brać odpowiedzialność w sensie aspektów związanych z jakością, rozważań ekonomicznych i oczywiście spraw prawno-etycznych – na przykład w kwestiach ochrony środowiska i ochrony zasobów naturalnych.
Dobre zamiary i konkretne wyniki
Jak pokazują konkretne przykłady w niemieckich zakładach produkcyjnych firmy Flender AG, rola tych haseł jest znacznie większa i nie ogranicza się tylko do umieszczenia ich na prospektach. Niezwykle obrazowym przykładem jest uzdatnianie sprężonego powietrza w zakładzie produkującym sprzęgła w Mussum.
Największa część sprężonego powietrza potrzebna jest tam do zasilania powietrzem zamykającym przyrządów do pomiaru współrzędnych przy maszynach produkcyjnych. Kolejne miejsce zajmuje zasilanie silników z napędem bezpośrednim w maszynach, które w ten sposób chronione są przed przedostawaniem się wilgoci. Następnymi istotnymi obszarami zastosowania sprężonego powietrza są maszyny okrawające, urządzenia czyszczące do przedmuchiwania detali oraz systemy natryskiwania farby w lakierni i automatyczne gwoździarki.
Nawet infrastruktura zakładu produkującego sprzęgła stawia na sprężone powietrze jako nośnik energii. Na przykład do ustawiania kopuł świetlnych i klap wentylacyjnych oraz do sterowania systemami wentylacyjnymi. Niektóre z tych zastosowań nie wymagają szczególnej jakości sprężonego powietrza, inne natomiast są bardzo wrażliwe – do tej grupy należą zwłaszcza urządzenia pomiarowe i wyposażenie lakiernicze. Pierwsza grupa zastosowań nie akceptuje przede wszystkim resztek oleju w sprężonym powietrzu, w lakierni z kolei powstają reakcje alergiczne na wprowadzoną wilgoć. Spowodowałaby ona tu powstanie niewielkich pęcherzyków w warstwie farby na obudowie sprzęgła. Jest to „zniekształcenie estetyczne” nieakceptowane przez klientów solidnej techniki przemysłowej.
Złożone wymagania względem jakości sprężonego powietrza
Potrzebne jest zatem zarówno w dużej mierze bezolejowe, jak również bezwzględnie suche sprężone powietrze, aby spełnić wysokie wymagania jakościowe w produkcji sprzęgieł. Ale to nie wszystko. Firma Flender stawia sobie dalsze „wewnętrzne” cele i sama nakłada na siebie dodatkowe obowiązki. Podstawę takiego działania stanowi macierzysty koncern Siemens, posiadający certyfikat zgodnie z nową normą zarządzania środowiskiem ISO 14001. Należy tu także możliwie najlepsza utylizacja kondensatu powstającego podczas uzdatniania sprężonego powietrza.
Potrzebowano całościowej koncepcji ogólnej, która stawi czoła wszystkim wyzwaniom i kompleksowo im sprosta – dzięki kompetencji systemowej. Po wnikliwym procesie oceny i wyboru firma Flender zdecydowała się na dostawcę systemowego, którego produkty i rozwiązania już wcześniej zostały docenione w Mussum: niemieckiego specjalistę w dziedzinie sprężonego powietrza BEKO TECHNOLOGIES z miejscowości Neuss nad Renem.
We współpracy z lokalnym partnerem specjalizującym się w technologii sprężarek specjaliści z firmy BEKO TECHNOLOGIES przedstawili przekonującą koncepcję ogólną. Połączono logicznie wszystkie aspekty uzdatniania sprężonego powietrza, począwszy od sprężenia przez osuszenie, filtrację i uzdatnianie kondensatu, po monitorowanie oleju resztkowego i budowę przewodów rurowych.
Separator emulsji chroni środowisko
„Wisienką na torcie” konstelacji i jednocześnie potwierdzeniem poważnego podejścia firmy Flender AG do kwestii związanych z ochroną środowiska jest separator emulsji BEKOSPLIT. Dzięki temu urządzeniu bez trudu udaje się spełnić skrajnie wysokie wymagania nowej normy zarządzania środowiskiem ISO 14001.
Ten najczęściej sprzedawany w Niemczech separator do kondensatu sprężonego powietrza znajduje zastosowanie tam, gdzie w fazie wodnej rozłożone są najdrobniejsze cząstki oleju, w związku z czym zwykła fizyczna separacja grawitacyjna, np. za pomocą separatora cieczy lekkich lub separatora koalescencyjnego, jest niewystarczająca. System BEKOSPLIT oferuje natomiast w przypadku zemulgowanych ścieków przemysłowych zawierających olej niezawodną technikę uzdatniania, która polega na usunięciu ze ścieków nierozpuszczalnych w wodzie zanieczyszczeń organicznych, takich jak oleje i cząstki stałe, za pomocą dodatku naturalnego minerału glinu. Jednocześnie niezawodnie wchłaniane są występujące metale ciężkie i inne cząstki zanieczyszczeń. Pozostałe, oczyszczone ścieki można bez problemu odprowadzać do kanalizacji.
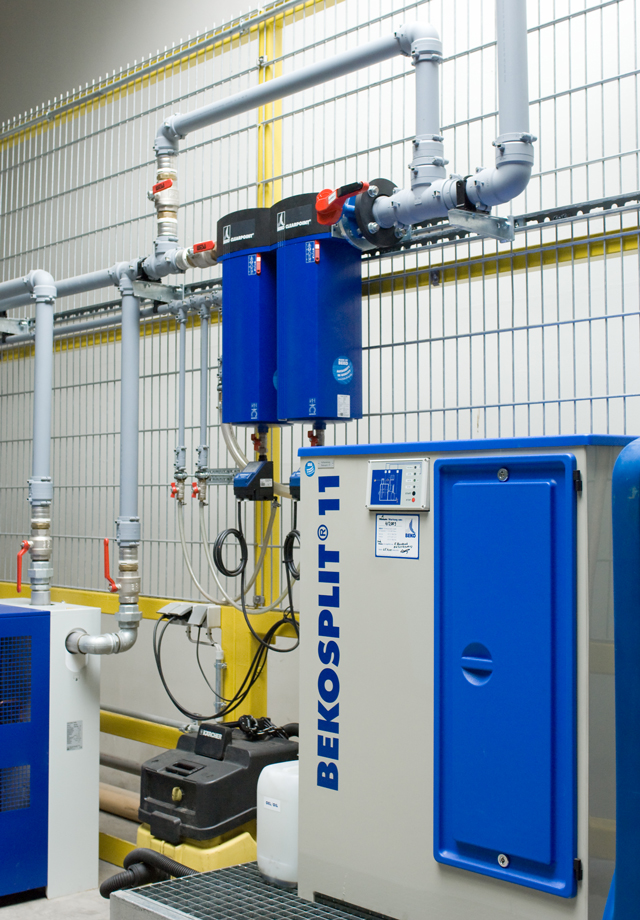
Połączenie z systemem od samego początku
Technologia BEKOSPLIT osiągająca techniczną szczytową wydajność w obszarze sprężonego powietrza znajduje się na „końcu utylizacji” w łańcuchu systemowym, natomiast na „początku zasilania” współgra ze sobą płynnie kilka komponentów. Sprężone powietrze jest najpierw kierowane przez zbiornik o pojemności 3000 litrów, w którym następuje już separacja części doprowadzonej wilgoci.
Dalej znajdują się trzy połączone równolegle osuszacze ziębnicze DRYPOINT RA firmy BEKO TECHNOLOGIES. Stanowią one w praktyce rozwiązanie 3 x 50%: każde spośród trzech urządzeń jest w stanie samodzielnie osiągnąć połowę wydajności osuszania wymaganej w instalacji firmy Flender. Dzięki równoległemu połączeniu wszystkich trzech osuszaczy ziębniczych generowana jest zatem wydajność na poziomie 150%. Zaletą tej koncepcji jest to, że w każdej chwili można usunąć z systemu – na przykład w celu konserwacji – całe urządzenie, nie wpływając negatywnie na wymaganą wydajność osuszania. Nawet całkowita awaria jednego osuszacza nie oddziałuje na jakość sprężonego powietrza.
Kondensat powstający w osuszaczach separowany jest bez strat sprężonego powietrza przez odwadniacze BEKOMAT posiadające regulację poziomu i doprowadzany do opisanego separatora emulsji BEKOSPLIT.
Osuszone sprężone powietrze jest następnie przepuszczane przez filtry CLEARPOINT o zoptymalizowanym przepływie. Dzięki nim firma BEKO TECHNOLOGIES zaimplementowała do systemu sprężonego powietrza niezwykle efektywną energetycznie i tym samym atrakcyjną pod względem kosztów produkcji technikę filtracyjną. Ostatnim punktem kontrolnym dla sprężonego powietrza przed opuszczeniem hali sprężarek jest opracowany również przez firmę BEKO TECHNOLOGIES system nadzorowania oleju resztkowego.
Ogólnie rzecz biorąc, firma Flender posiada w zakładzie produkcyjnym w Mussum płynny, perfekcyjnie dopasowany do siebie łańcuch procesowy w obszarze uzdatniania sprężonego powietrza.
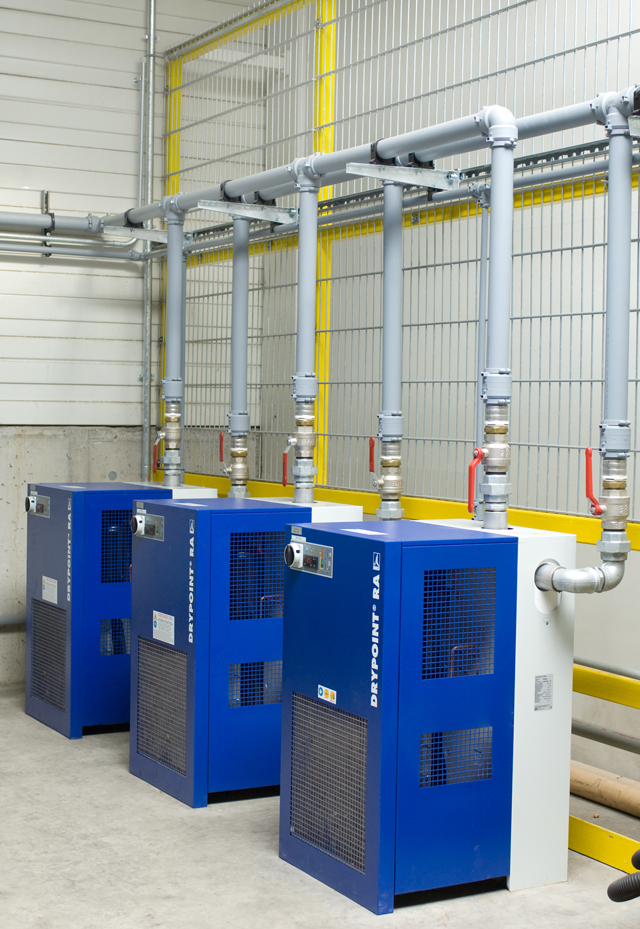
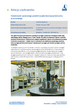