EVERDRY® FRA-V
With EVERDRY® FRA the desorption takes place in counter flow direction to the adsorption process with heated blower air and the cooling in co-current flow direction to the adsorption process with blower air. Thus preventing compressed air loss for regeneration (ZERO Purge).
EVERDRY® FRA-Vplus
With EVERDRY® FRA the desorption takes place in counter flow direction to the adsorption process with heated blower air and the cooling in co-current flow direction to the adsorption process with blower air. Thus, preventing compressed air loss for regeneration (ZERO Purge). Additional customer advantage due to a central regeneration discharge.
EVERDRY® FRA-V with use of steam
With EVERDRY® FRA the desorption takes place in counter flow direction to the adsorption process with heated blower air and the cooling in co-current flow direction to the adsorption process with blower air. Thus, preventing compressed air loss for regeneration (ZERO Purge). Reduced energy costs due to vapour utilisation.
EVERDRY® with use of steam and electrical heater
With EVERDRY® FRA the desorption takes place in counter flow direction to the adsorption process with heated blower air and the cooling in co-current flow direction to the adsorption process with blower air. Thus, preventing compressed air loss for regeneration (ZERO Purge). Reduced energy costs due to vapour utilisation. Increased operational reliability due to redundant electrical heater.
EVERDRY® FRA-V with use of hot water and electrical heater
With EVERDRY® FRA the desorption takes place in counter flow direction to the adsorption process with heated blower air and the cooling in co-current flow direction to the adsorption process with blower air. Thus, preventing compressed air loss for regeneration (ZERO Purge). Reduced energy costs due to hot water utilisation. Increased operational reliability due to redundant electrical heater.
EVERDRY® FRA-V with integrated pre- and after filter
With EVERDRY® FRA the desorption takes place in counter flow direction to the adsorption process with heated blower air and the cooling in co-current flow direction to the adsorption process with blower air. Thus, preventing compressed air loss for regeneration (ZERO Purge). Reduced energy costs due to hot water utilisation. The integrated pre- and after-filters improve the energy balance and guarantee a consistency in the quality of compressed air.
EVERDRY® FRA-V 3400 with integrated pre- and after filter + by-pass
With EVERDRY® FRA the desorption takes place in counter flow direction to the adsorption process with heated blower air and the cooling in co-current flow direction to the adsorption process with blower air. Thus, preventing compressed air loss for regeneration (ZERO Purge). Reduced energy costs due to hot water utilisation. The integrated pre- and after-filters improve the energy balance and guarantee a consistency in the quality of compressed air. Due to the integrated Bypass, maintenance of EVERDRY is possible without any production downtime.
EVERDRY® FRA-V with pre-cooler unit
With EVERDRY® FRA the desorption takes place in counter flow direction to the adsorption process with heated blower air and the cooling in co-current flow direction to the adsorption process with blower air. Thus, preventing compressed air loss for regeneration (ZERO Purge). Reduced energy costs due to pre-cooling the compressed air. Thus, considerable prolongation in absorption time is achieved. The attached condensate separator guarantees a reliable condensate drainage.
EVERDRY® COMBITROC CT
The EVERDRY® COMBITROC CT ensures optimum processing by combining the best of refrigeration and adsorption dryers. The refrigeration dryer saves on energy by providing a pressure dew point of +3 °C. A lower pressure dew point is required during the colder season, to properly prevent condensation. The system then automatically switches to the heat-regenerated adsorption dryer, creating a pressure dew point of -40 °C. Another advantage of this combination: 100 % redundancy in case of a dryer failure.
EVERDRY® COMBITROC CT by-pass
The EVERDRY® COMBITROC CT ensures optimum processing by combining the best of refrigeration and adsorption dryers. The refrigeration dryer saves on energy by providing a pressure dew point of +3 °C. A lower pressure dew point is required during the colder season, to properly prevent condensation. The system then automatically switches to the heat-regenerated adsorption dryer, creating a pressure dew point of -40 °C. Another advantage of this combination: 100 % redundancy in case of a dryer failure. The bypass surrounding the refrigeration dryer allows maintenance without any production downtime.
EVERDRY® FRA-V oil-free with METPOINT OCV
With EVERDRY® FRA the desorption takes place in counter flow direction to the adsorption process with heated blower air and the cooling in co-current flow direction to the adsorption process with blower air. Thus, preventing compressed air loss for regeneration (ZERO Purge). This unit guarantees the highest standard oil-free compressed air due to a two-stage preliminary filtration using CLEARPOINT activated carbon adsorber and a dust filter. The attached METPOINT OCV constantly monitors the residual oil content in the compressed air.
EVERDRY® FRA-V Sorbead® ECO
With EVERDRY® FRA the desorption takes place in counter flow direction to the adsorption process with heated blower air and the cooling in co-current flow direction to the adsorption process with blower air. Thus, preventing compressed air loss for regeneration (ZERO Purge). Regeneration of the unit requires less energy consumption due to the use of the special desiccant SORBEAD®. This is a significant contribution to lowering your energy costs!
Basic
- Adsorber container sandblasted, primed and painted in RAL 5002
- Base frame sandblasted, primed and painted in RAL 5002
- Pipelines galvanised inside and out for maximised corrosion protection
- Flow distributors made of stainless steel for even distribution of compressed air flow
Option without charge
- Adsorber container painted in preferred colour (RAL)
- Base frame painted in preferred colour (RAL)
Option
- Outdoor installation
Basic
- Streamlined single fitting to minimise differential pressure
- Two-piece flap housing for easy maintenance / repairs
- Reliable pneumatically powered pneumatic valves for pressure release / build-up
- Hand-operated fitting for manual pressure release
- Pneumatic piping in robust, corrosionproof pneumatic pipe
- Valve terminal, control air unit, pressure transmitter mounted in a stable pneumatic cabinet
- Cable routed in galvanised steel shell pipes or cable ducts
- All sensors connected with M12 connectors
- Cable numbering
Option
- Safety valves (2 pcs., G1/2)
- Preparation for mounting the safety valves
- Single conductor labelling
Basic
- Counter flow desorption
- Parallel mode to avoid temperature- and dew point fluctuations
- Insulation of the heater container
Option
- Thermal insulation for the adsorber body and -head
- Insulation for outdoor installation
- Insulation in special materials (stainless steel, aluminium, etc.)
Basic
- Monitoring of the operating pressure through analogue measurement recorders
- Adjustable alarm value for input temperature
- 1x 24 V power supply for BEKOMAT
- 1x BEKOMAT alarm contact
- S7-1200 control with KTP700 touch panel (in colour, multilingual, 7")
- Ambient control (only FRA-V / FRA)
- Measurement and display of ambient temperature
- Measurement and display of ambient humidity
- Calculation and display of ambient dew point
- Calculation and display of specific energy consumption [Wh/m³, Wh/Nm³, Wh/cft]
- Outlet volume flow measurement "ready to connect" (adjustable alarm value for volume flow)
- Maintenance package (flap operation registration / "flexible maintenance")
- Calculation and coloured visualisation of dryer capacity
- Measurement of operational time dew point sensor / heater / blower with adjustable maintenance intervals
- Stainless steel pressure gauge with shut-off valve on every adsorber container
Option without charge
- Special voltage (3 x 380 - 440 V, 50 Hz)
Option
- Change-over control for moist air entry flaps through inductive sensors incl. LED-display (green / red)
- End position control for every additional flap through inductive sensors incl. LED-display (green / red)
- Dew point measurement and control unit
- Analogue measurement recorders monitor regeneration temperatures (heating / cooling)
- Additional temperature transmitter at inlet "ready to connect"
- Additional 24V power supply incl. alarm contact (potential free)
- Special voltage, other
- S7-1200 control with KTP1200 touch panel (in colour, multilingual, 12")
- ECO-Control (measurement of energy consumption current / average)
- Volume flow sensor at outlet
- Shiny Package (signalling systems current condition through coloured LED)
- Maintenance-PLUS package (flap runtime measurement / "flexible maintenance")
- Labelling of all measuring instruments, fittings and functional elements using durable signs
- User control with various password levels
- Individually change and expand user names
- Safety-Log (document all user entries)
Basic
- Profinet port for Modbus TCP or S7-communication (only for S7-1200 control)
- Remote ON/OFF through pot.-free contact or bus
- Analogue output for dew point signal
- 3 free analogue inputs (2x pre-programmed, 1x assign freely)
- 1x potential free alarm contact (collective fault notification)
- 1x potential free contact for operational notification
Option
- Profibus-Modul Slave (only with S7-1200 control)
- Modbus-RTU RS485 (only with S7-1200 control)
- 3 additional potential free contacts
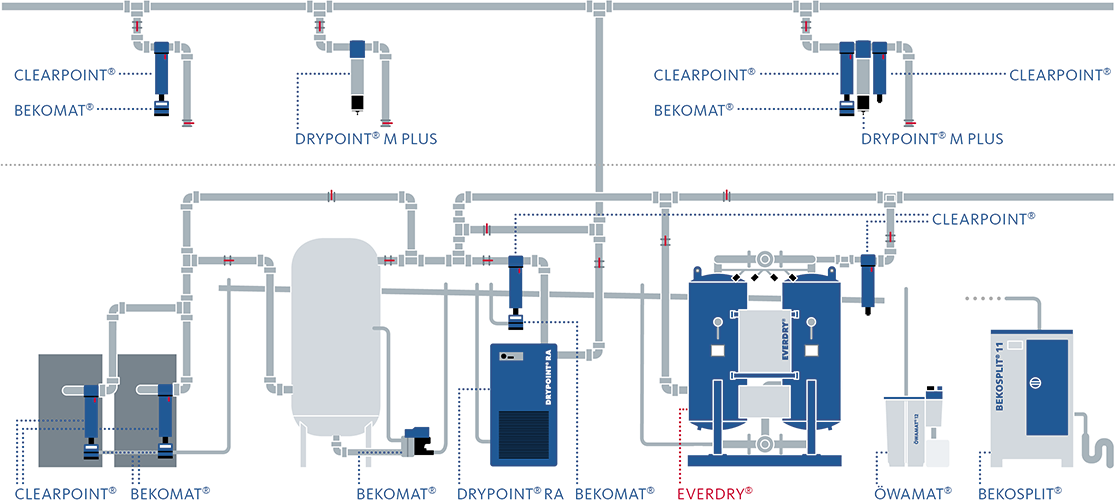
Bekomat®
Unnecessary costs and damage during the generation of compressed air can
only be avoided in an efficient way with amount-adjusted condensate
drainage.
Therefore, BEKOMAT® condensate drains operate with a capacitive
sensor. The intelligent electronics prevent compressed-air losses and
minimise the energy demand.
As a result, the BEKOMAT® often pays itself off within half a
year already, in contrast to devices with timed drain valves.
The comprehensive product portfolio offers the optimum device for every
compressor type and performance, for every system pressure, and for all
operating conditions.
Bekomat®
Unnecessary costs and damage during the generation of compressed air can only
be avoided in an efficient way with amount-adjusted condensate drainage.
Therefore, BEKOMAT® condensate drains operate with a capacitive
sensor. The intelligent electronics prevent compressed-air losses and
minimise the energy demand.
As a result, the BEKOMAT® often pays itself off within half a
year already, in contrast to devices with timed drain valves.
The comprehensive product portfolio offers the optimum device for every
compressor type and performance, for every system pressure, and for all
operating conditions.
Bekomat®
Unnecessary costs and damage during the generation of compressed air can only
be avoided in an efficient way with amount-adjusted condensate drainage.
Therefore, BEKOMAT® condensate drains operate with a capacitive
sensor. The intelligent electronics prevent compressed-air losses and
minimise the energy demand.
As a result, the BEKOMAT® often pays itself off within half a
year already, in contrast to devices with timed drain valves.
The comprehensive product portfolio offers the optimum device for every
compressor type and performance, for every system pressure, and for all
operating conditions.
Bekomat®
Unnecessary costs and damage during the generation of compressed air can only
be avoided in an efficient way with amount-adjusted condensate drainage.
Therefore, BEKOMAT® condensate drains operate with a capacitive
sensor. The intelligent electronics prevent compressed-air losses and
minimise the energy demand.
As a result, the BEKOMAT® often pays itself off within half a
year already, in contrast to devices with timed drain valves.
The comprehensive product portfolio offers the optimum device for every
compressor type and performance, for every system pressure, and for all
operating conditions.
Bekomat®
Unnecessary costs and damage during the generation of compressed air can only
be avoided in an efficient way with amount-adjusted condensate drainage.
Therefore, BEKOMAT® condensate drains operate with a capacitive
sensor. The intelligent electronics prevent compressed-air losses and
minimise the energy demand.
As a result, the BEKOMAT® often pays itself off within half a
year already, in contrast to devices with timed drain valves.
The comprehensive product portfolio offers the optimum device for every
compressor type and performance, for every system pressure, and for all
operating conditions.
Drypoint® M Plus
DRYPOINT® M PLUS membrane dryer with an integrated
nanofilter is the innovative solution for efficient filtration and
drying in one housing. It offers reliable compressed-air drying
with low purge air demands, requires no electric energy and
contains no environmentally harmful desiccants.
The integrated nanofilter increases the quality of the dried compressed air
and
the reliability and long-term stability of the highly selective hollow-fibre
membranes. The high-capacity DRYPOINT® M PLUS is
even suitable for the processing of breathing air.
Drypoint® M Plus
DRYPOINT® M PLUS membrane dryer with an integrated
nanofilter is the innovative solution for efficient filtration and
drying in one housing. It offers reliable compressed-air drying
with low purge air demands, requires no electric energy and
contains no environmentally harmful desiccants.
The integrated nanofilter increases the quality of the dried compressed air
and
the reliability and long-term stability of the highly selective hollow-fibre
membranes. The high-capacity DRYPOINT® M PLUS is
even suitable for the processing of breathing air.
Drypoint® RA
The intelligent construction of the compressed air refrigeration
dryers not only allows highest functionality but also reliable and
cost-effective operation. In this respect, the fundamental elements
are the vertical design of the heat exchanger in accordance
with physical principles (top-down condensate flow), a stainless
steel demister for safe separation and a large settling chamber
preventing the re-entrainment of the condensate.
The DRYPOINT® RA is particularly energy-efficient because of the
avoidance of compressed air path deflections which are unfavourable
to the flow and of additional flow resistances. A constantly
low pressure dew point, droplet separation of nearly 99%, scarcely
any compressed air loss, low maintenance requirements and low
operating costs are further advantages.
BEKOSPLIT®
The BEKOSPLIT® splitting plant allows for reliable, economic,
and in-house processing of emulsified condensates that accumulated
as a result of unfavourable initial conditions, or due
to certain lubricant/compressor combinations.
Water-insoluble organic pollution, such as oils and solid impurities, is
removed
via the addition of a special alumina mineral. Subsequently, the
outflowing water, that is pollution-free, can directly be introduced
into the wastewater system.
ÖWAMAT®
ÖWAMAT® is an oil-water separation system for dispersed condensates. The purified water meets the legal requirements for the introduction into the sewer system.
CLEARPOINT®
With the CLEARPOINT® compressed-air filter series for volume
flows from 35 to 34,680 m3/h (at 7 bar), an economic concept for
efficient compressed-air filtration is now available.
Through innovative filter elements and a flow-optimised, corrosion-protected
housing construction, CLEARPOINT® offers safe and reliable
filtration,
and qualitatively better compressed air at significantly reduced
operating costs.
CLEARPOINT®
With the CLEARPOINT® compressed-air filter series for volume
flows from 35 to 34,680 m3/h (at 7 bar), an economic concept for
efficient compressed-air filtration is now available.
Through innovative filter elements and a flow-optimised, corrosion-protected
housing construction, CLEARPOINT® offers safe and reliable
filtration,
and qualitatively better compressed air at significantly reduced
operating costs.
CLEARPOINT®
With the CLEARPOINT® compressed-air filter series for volume
flows from 35 to 34,680 m3/h (at 7 bar), an economic concept for
efficient compressed-air filtration is now available.
Through innovative filter elements and a flow-optimised, corrosion-protected
housing construction, CLEARPOINT® offers safe and reliable
filtration,
and qualitatively better compressed air at significantly reduced
operating costs.
CLEARPOINT®
With the CLEARPOINT® compressed-air filter series for volume
flows from 35 to 34,680 m3/h (at 7 bar), an economic concept for
efficient compressed-air filtration is now available.
Through innovative filter elements and a flow-optimised, corrosion-protected
housing construction, CLEARPOINT® offers safe and reliable
filtration,
and qualitatively better compressed air at significantly reduced
operating costs.
CLEARPOINT®
With the CLEARPOINT® compressed-air filter series for volume
flows from 35 to 34,680 m3/h (at 7 bar), an economic concept for
efficient compressed-air filtration is now available.
Through innovative filter elements and a flow-optimised, corrosion-protected
housing construction, CLEARPOINT® offers safe and reliable
filtration,
and qualitatively better compressed air at significantly reduced
operating costs.
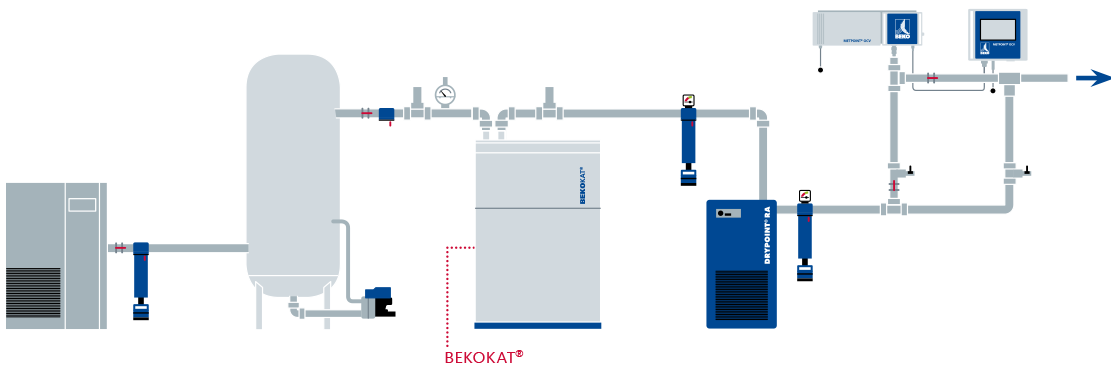
Bekokat®
During the compression of air, cleanliness of the air
becomes a
critical factor since compressed air always absorbs a certain amount
of hydrocarbons from the intake air, from compressor oil, and from
lubricated line-mounted valves in the compressed-air system. The
absence of oil needs to be systematically established in the course
of downstream processing since only through constant monitoring
of air quality can the contamination of processes and products be
prevented.
Here, the BEKOKAT® sets new standards with
its trendsetting
technology: with a residual oil content down to a barely
measurable 0.001mg/m³ - and an absolute absence of biological
contaminants – air cleanliness is taken to a new level.
From the idea to the custom-made solution – on the basis of standardised system concepts
Profile
- Industry and application specific requirements (e.g. compressed air quality, volume flow, forms of energy for regeneration air heating)
- Investment and operating costs, individual amortisation period
- Local acceptance requirements
- Climate zone, local operating conditions, economic parameters
Concept
- Determination of system type
- Based on this: develop an individual solution
Presentation
- Introducing the solution concept
Realisation
- Implementation of the project
- Inhouse Engineering through our experienced and competent team of experts
Commissioning
- On-site system installation
- Optimised setting and adaption to local conditions
Continuous interaction between our experts and customers
Support / consultation / optimisation
Insight into our production
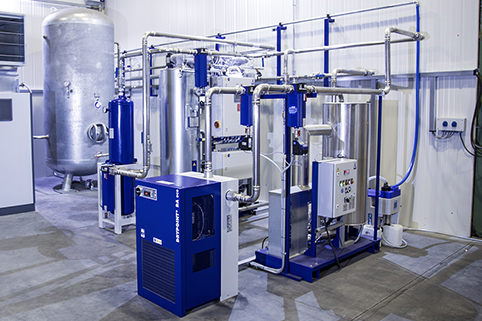
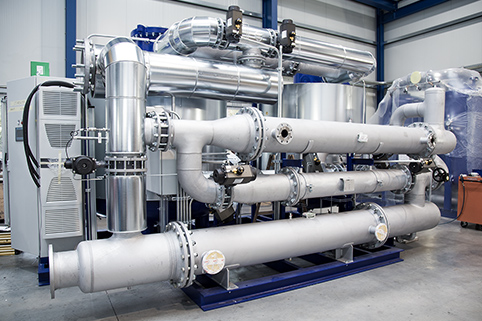
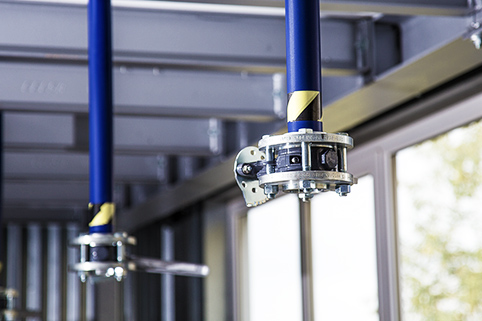
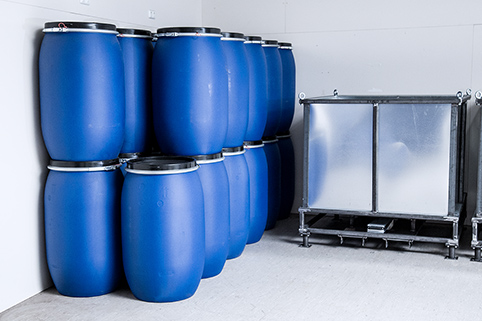

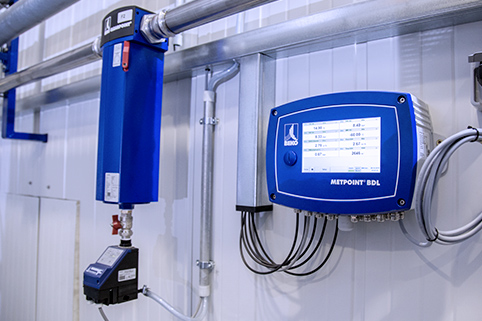
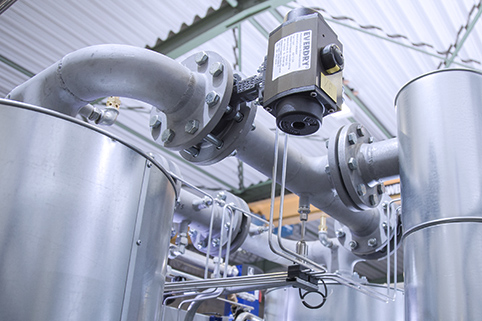
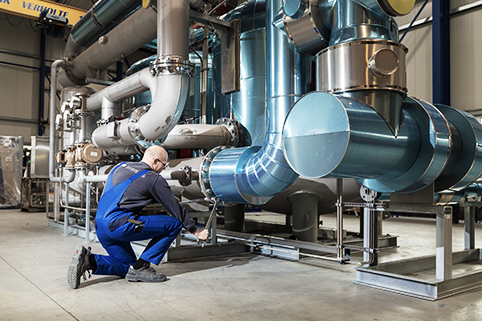
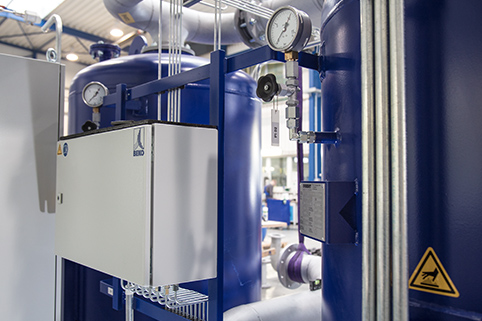
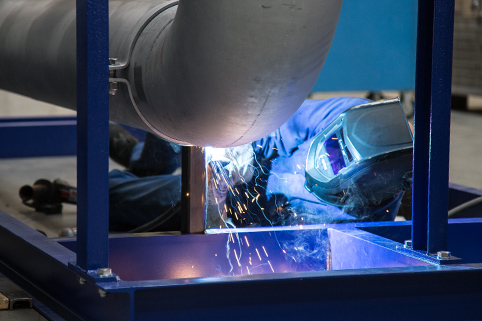
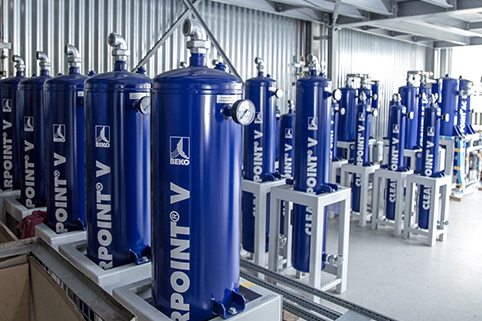
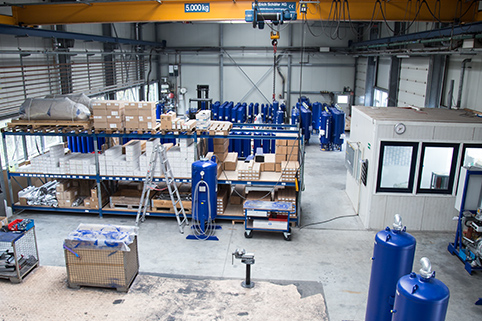
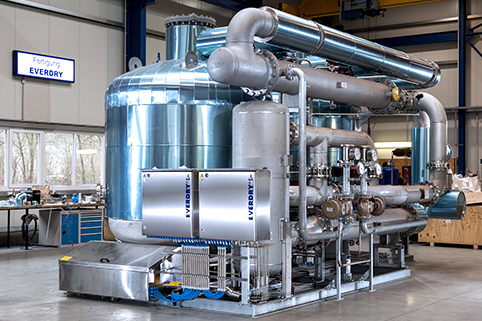
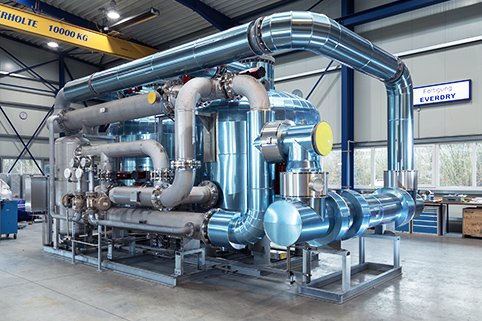
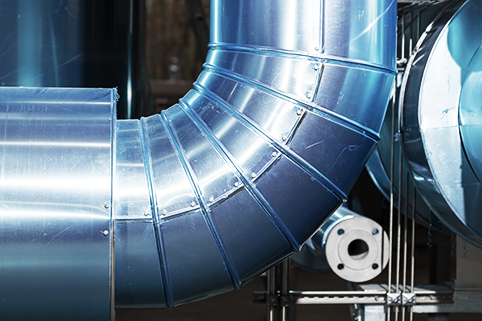
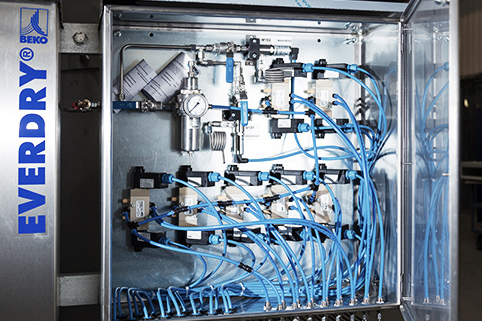
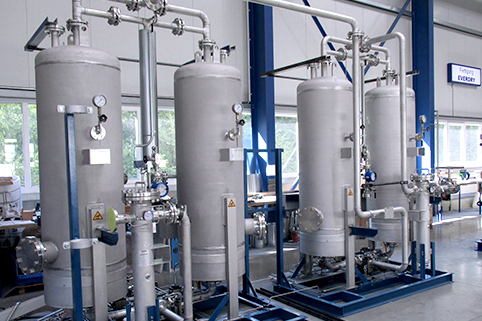
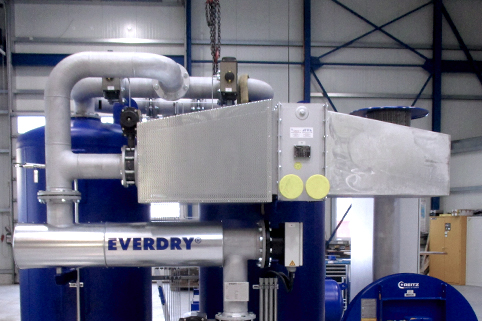
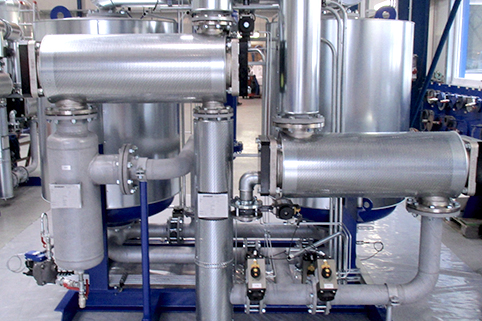
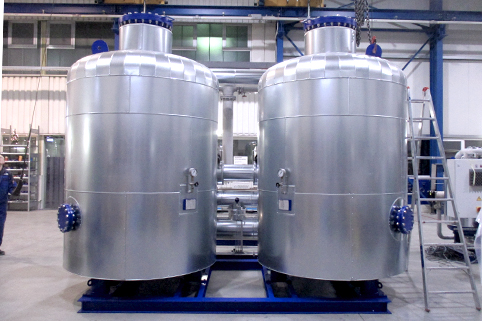
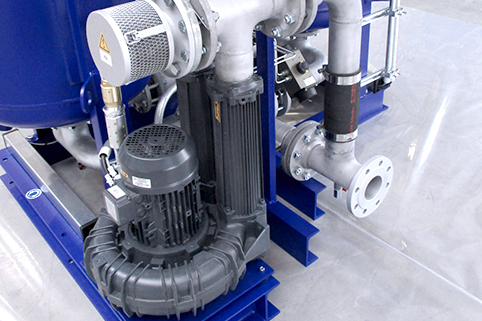
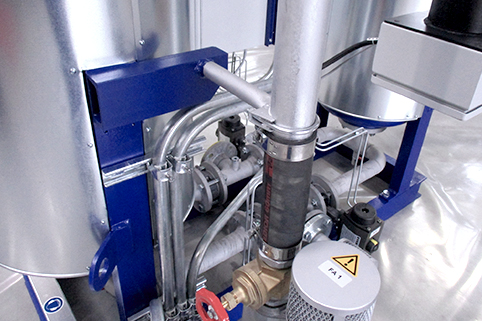
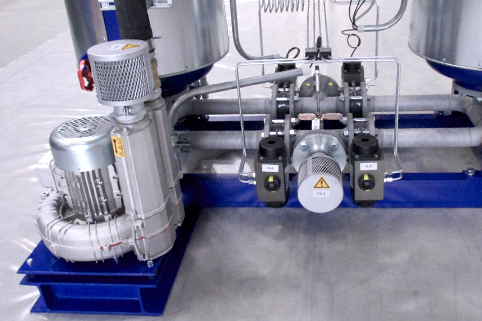
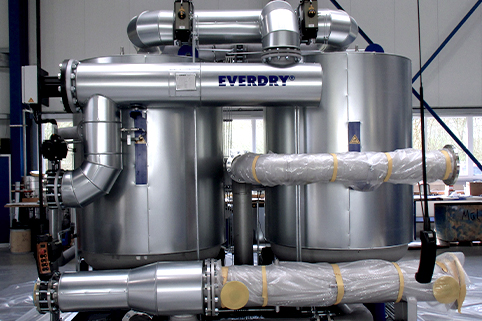